Tungsten carbide buttons are an extremely hard and durable material used in demanding applications where high wear resistance is required. Often referred to as simply “carbide”, this advanced material allows parts, components, and products to withstand harsh operating environments.
Carbide buttons feature unique properties that make them versatile for use across various industries including manufacturing, oil and gas, mining, construction, transportation, and more. They outlast other materials significantly in abrasive settings, delivering long service life to keep operations running optimally.
This article provides a comprehensive guide to tungsten carbide buttons. We’ll explore carbide button composition, types, key properties, manufacturing processes, applications, popular sizes and grades, design considerations, global standards, top suppliers, pricing, and more. Whether you’re an engineer exploring carbide options or a procurement manager sourcing wear-resistant parts, this guide offers vital details to inform your decisions.
Composition of Tungsten Carbide Buttons
Tungsten carbide (WC) is a ceramic material containing tungsten (W) carbide particles in a binder matrix of cobalt (Co). It is produced by mixing tungsten powder and carbon at high temperature in a process called carburization.
Most carbide buttons consist of closely controlled particles of tungsten carbide embedded in 6% to 25% cobalt binder. The cobalt acts to cement the hard WC grains together so they can be formed into a usable product.
The relative percentage of cobalt binder determines hardness and toughness. Lower cobalt grades are harder and more wear resistant but tend to be brittle. Higher cobalt grades are tougher but slightly softer.
Typical Composition Range of Carbide Buttons
Constituent | Composition by Weight % |
---|---|
Tungsten (W) | 72.0 – 97.5% |
Carbon (C) | 0.6 – 6.0% |
Cobalt (Co) Binder | 3.0 – 25% |
The extensive range of possible carbide grades and cobalt percentages allows manufacturers to tailor buttons for specific operating conditions.
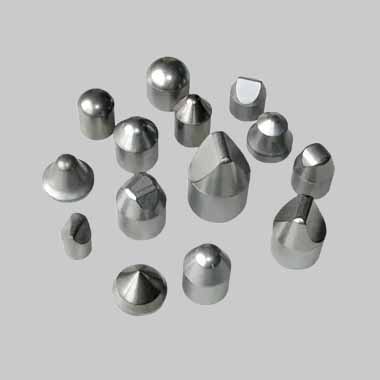
Types of Carbide Buttons by Manufacturing Method
Carbide buttons are produced using various methods that result in different material qualities suited to particular applications:
Cast Carbide Buttons
- Produced by liquid phase sintering tungsten powder and binder
- Large button sizes up to 3 inches diameter
- Higher porosity than other grades
Sintered Carbide Buttons
- Made from tungsten carbide particles pressed and solid phase sintered
- Low porosity for excellent hardness
- Up to 1 inch diameter buttons
Pelletized Carbide Buttons
- Compacted from tungsten carbide granules not powders
- Medium density and hardness
- Cost-effective grade
Cemented Carbide Buttons
- Carburized tungsten powders cemented by cobalt binder
- Very uniform hardness and dense structure
- Higher cost than pellet carbide
Tungsten Carbide Rods
- Drawn into rods then cut into plugs
- Very tight tolerances
- Uniform hardness and wear resistance
Carbide Button Inserts
- Pressed into various common insert shapes
- Reversible indexable inserts with multiple edges
- Cylindrical, conical, radius, trigon, diamond, etc.
Key Properties and Characteristics
The exceptional hardness and wear properties of carbide buttons over a wide temperature range lead to significant advantages that make them ideal upgrades from other materials across industry applications.
Tungsten Carbide Button Properties
Property | Description |
---|---|
Hardness | 89 to 93 HRA at room temperature |
Compressive strength | Higher than tool steels |
Tensile strength | Two times higher than tool steels |
Operating temp range | Up to 600°C for cobalt grades |
Coefficient of friction | 0.2 dynamic, 0.6 static |
Density | Triple that of steel |
Corrosion resistance | Resists corrosion except in presence of HCl and H2SO4 |
Thermal conductivity | Lower than tool steel so heat dissipation slower |
Key characteristics that lead to performance benefits:
- Extreme hardness delivers abrasion and erosion resistance
- Strength retains form and function under heavy loads
- Dense structure resists impacts without cracking
- Cobalt binder gives fracture toughness
- Chemically inert in most environments
- Dimensional stability across a wide temperature range
How Carbide Button Grades Differ
- Hardness directly linked to cobalt content
- Lower cobalt is harder but more brittle
- Higher cobalt is tougher but slightly softer
- Must balance wear resistance and toughness needed
Tungsten Carbide Button Manufacturing Process
Carbide buttons pass through a series of complex manufacturing steps leveraging extreme heat and pressure to achieve unique metallurgical properties.
Four Key Stages:
1. Milling
- Pure tungsten metal powder is milled to precise average particle sizes optimized for the grade of carbide required
2. Mixing
- Measured amounts of tungsten powder and carbon are mixed and milled into an evenly dispersed compound
3. Pressing
- The powder mix is pressed into a “green” compact form reflecting final dimensions
4. Sintering
- Green compacts are resistance sintered in a vacuum furnace at 2,500°F to produce a virtually pore-free product
Advanced technology combines carbon and tungsten through diffusion to create an extremely hard material able to withstand extreme pressure and heat.
Key Applications and Uses
With excellent wear characteristics and physical properties, carbide buttons deliver value across industries and applications including:
Typical Applications of Carbide Buttons
Industry | Common Applications |
---|---|
Manufacturing | Bushings, seals, nozzles, guides, valves, tooling, molds |
Construction | Road planing, piling, drivage tools, rock drilling buttons |
Mining | Crushing, grinding media, excavating teeth and hooks |
Transportation | Grader and snowplow blades, truck bed liners |
Forestry | Saw teeth, debarking heads, wood flails, chipper knives |
Oil and Gas | Downhole tools, wireline tools, logging instruments |
Steel Production | Continuous casting dies, furnace hot top cones |
Rail Transport | Brake pads and linings, rail inspection gauges |
Key reasons tungsten carbide is selected over steel alternatives:
- Wear life exceeds similar steel parts by 8X to 30X+
- Withstands high sliding speeds without seizing or heat damage
- Handles abrasive or corrosive environments that quickly degrade steel
- Provides cost efficiencies via longer replacement cycles
Carbide grades and binder ratios can be optimized to match operating demands whether for repetitive impact, constant abrasion, or cyclic erosion mechanisms degrading components.
Popular Carbide Button Sizes
Tungsten carbide buttons are produced in standardized sizes from stock or custom dimensions to suit particular equipment designs.
Most Common Button Diameters
- 3/8 inch
- 1/2 inch
- 5/8 inch
- 3/4 inch
- 7/8 inch
- 1 inch
Larger diameter plugs up to 3 inch are also produced though less commonly specified.
Smaller buttons and inserts down to 1/8 inch diameter made from sintered or cemented carbide are used in light duty applications.
Standard Height-to-Diameter Ratios
- 1:1 ratio buttons
- 1:2 ratio buttons
- 2:1 ratio buttons
- 3:1 ratio buttons
1:1 is the most frequently used carbide button ratio for versatility across mounting configurations. Custom length-to-diameter proportions made to order.
Grades, Quality Standards, and Specifications
Carbide Button Grading System
Tungsten carbide buttons are classified by a unified grading structure developed by the International Organization for Standardization (ISO).
This system categorizes carbide grades by grain size and cobalt content using an alphanumeric code.
Typical Carbide Grades for Buttons
Grade | Description |
---|---|
K10 / K01 | Ultra-fine 0.2 to 0.4 micron grain size with low cobalt content for maximum wear resistance where high toughness is not required |
K20 / K02 | Extra-fine 0.5 to 1 micron grain size with medium cobalt content for excellent toughness and strength |
K30 / K03 | Fine 1 to 2 micron grain size with higher cobalt content for increased fracture resistance under impact |
K40 / K04 | Medium 1 to 5 micron grain size with high cobalt content for strength rather than extreme wear performance |
The lower the ISO grade number, the smaller the tungsten carbide particle size and hence generally the better the wear resistance. Finer grain carbide is more costly to manufacture.
Quality and Consistency Standards
Reputable carbide button manufacturers control production using statistical process control and ISO quality standards:
- ISO 9001 – Quality Management
- ISO 14001 – Environmental Management
- ISO 45001 – Occupational Health and Safety
Compliance ensures consistency and reliability of carbide grade performance. Validation testing can be conducted on samples per customer requirements.
Design and Specification Best Practices
Considerations when specifying carbide button requirements:
- Operating conditions – moderate, heavy or extreme abrasion
- Base material being abraded – stone, concrete, soil, steel, wood etc.
- Hardness of embedded abrasives if applicable
- Loads, rotational speeds, temperature, chemical exposure
- Method of retention – brazed or clamped
Get expert guidance selecting optimum carbide grade, binder percentage, and retention method unless prior button models have proven successful in same application.
Supply ISO grade, dimensions, dimensional tolerances, surface finish, cobalt percentage, manufacturing method, and any custom requirements.
Global Supply and Manufacturers
China, Europe, and the United States are leading producers of cemented tungsten carbide products. Many major suppliers have facilities strategically located across these regions.
Notable Carbide Button Manufacturers
Company | Headquarters |
---|---|
Kennametal | United States |
Sandvik | Sweden |
Ceratizit | Luxembourg |
Mitsubishi Materials | Japan |
Guangdong Xianglu Tungsten | China |
Federal Carbide | USA |
TaeguTec | South Korea |
When selecting a preferred carbide button vendor, ensure:
- Technically qualified sales engineers to assist product selection
- Capability to deliver both standard and custom options
- Stringent quality control standards adherence
- Competitive pricing with prompt delivery at scale
- Strong reputation gleaned from customer testimonials
Carbide Button Pricing
Carbide buttons command premium pricing relative to steel alternatives. However longer service life results in lower overall part cost per hour or per unit produced.
Cost Ranges for Carbide Grades
Carbide Grade | Relative Price Index |
---|---|
K10/K01 | highest cost due to extensive processing |
K20/K02 | mid range pricing |
K30/K03 | lower cost than ultrafine grades |
K40/K04 | least expensive tungsten grade |
Price Drivers:
- Raw tungsten market pricing
- Manufacturing method complexity
- Required dimensional tolerance tightness
- Order quantity – individual versus bulk
- Custom options like chamfering or hole drilling
Pricing also varies by supplier depending on:
- Country of manufacturing origin
- Production capacity and economies of scale
- Reseller margins and tariffs
Comparing Carbide and Steel Buttons
Tungsten carbide substantially outperforms steel across critical properties while also offering environmental stability.
Contrasting Steel Against Carbide
Property | Tungsten Carbide Button | Steel Button |
---|---|---|
Hardness | Up to 93 HRA | Max 60 HRC |
Strength | 2X that of steel | Moderate strength |
Toughness | Hard, brittle material | Less hard but more ductile |
Wear resistance | Excellent due to hardness | susceptible to wear mechanisms |
Corrosion resistance | Inert to most chemicals | Prone to oxidation |
Work temp range | Up to 600°C | Loses hardness above 250°C |
Friction coefficient | Low at ~0.2 | ~0.7 and galls or seizes |
Key Considerations | Carbide Buttons | **Steel Buttons ** |
Initial price | Many times higher | Very economical |
Wear life | 8X to 30X greater | Low durability and life |
Weight | Two times heavier | Lighter weight |
Thermal conduction | Low to retain heat | High heat dissipation |
Lead time | Longer manufacturing time | Readily available |
Carbide buttons provide value via reduced downtimes, consumables cost savings, and improved equipment effectiveness.
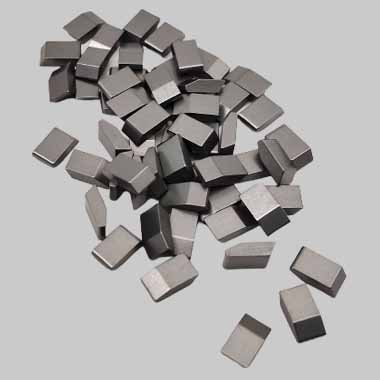
Carbide Button Design and Selection Best Practices
Proper design and controlled fabrication of carbide components enhance technical performance while avoiding common pitfalls.
Proven Design Principles
- Match carbide grade hardness to application wear mechanisms
- Ensure uniform cross-sectional thickness
- Eliminate stress concentration features
- Design to avoid brittle fracture inducing damage
- Optimize interface retention mechanisms for operating stresses
- Allow for thermal expansion differences from base metals
- Account for poor thermal conduction requiring cooling aids
Machineability Challenges
Being extremely hard, tungsten carbide can’t be machined using traditional methods. Outputs are ground to final dimensions.
- Requires diamond grinding wheels and processes
- Causes rapid tool wear requiring frequent wheel dressing
- Generates fine dusty swarf requiring filtration
- Risk of micro-cracking and tool pressure damage
Easier to manufacture carbide include:
- Softer grade K40/K04 carbide material
- Components with simpler geometries
- Large flat surface areas
Leverage manufacturer design expertise rather than attempting to machine finicky carbide pieces.
FAQ
Q: Why is tungsten carbide so popular over other hard materials like ceramics?
A: Tungsten carbide uniquely balances extreme hardness and abrasion resistance with improved fracture toughness. Ceramic alternatives tend to catastrophically crack under loads rather than gradually wearing over time.
Q: What causes carbide buttons and tooling to eventually fail and need replacement?
A: Given extremely hard structure, carbide does not deform gradually before failure like metals. Most damage results from small chipping leading to cracking. Impacts may cause macroscopic fractures as well. Fatigue wear also degrades front line surfaces through friction and abrasion mechanisms.
Q: Should tungsten carbide buttons be stored in any special manner?
A: Given their inert material properties, carbide buttons don’t require specialized storage as long as protected from physical damage. Ensure proper ventilation is available since cobalt binder dust from grinding may present respiratory hazards.
Q: What process connects carbide buttons into equipment and machinery?
A: The two most common methods for affixing carbide are brazing and clamping via bolts or threaded assemblies. Braze material selection depends on service temperatures and costs. Mechanical clamping allows simpler replacement but may suffer issues from differing thermal expansion rates between carbide and holder metals.
Q: How long should carbide button life expectancy be over steel?
A: Depending on operating conditions and counterparts abrading the buttons, properly designed carbide buttons generally last 8 to 30 times longer than alternative steel solutions. Payback economics justify 5X to 15X elevated price.