Carbide brazed tips refer to cutting inserts or tips made of tungsten carbide that are brazed onto tools to impart hardness, durability and wear resistance. They are used across several industries like manufacturing, construction, mining etc. for machining, grinding, drilling, shaping and cutting applications.
This article provides a comprehensive guide on carbide tips brazed using silver alloy or nickel alloy to tools like drill bits, milling cutters, saw blades, broaches and cold hobs. We explore the composition, properties, sizes, standards and grades of these brazed carbide inserts. Their key characteristics, performance parameters and usage across materials and scenarios are compared to present the advantages and limitations. Supplier details with indicative pricing are also tabulated. An FAQ section addresses common queries on these wear parts.
Composition and Manufacturing Process
Carbide refers to cemented tungsten carbide which is a composite of tungsten carbide (WC) and cobalt (Co) that is produced via powder metallurgy. Cobalt acts as the cementing or binding agent in particles of WC to yield a solid carbide part. Based on cobalt percentage, WC-Co compositions are tailored for desired hardness, toughness and wear properties.
Brazed carbide tips have the following layers and constituents:
Table 1: Composition Stack-up in Carbide Brazed Tips
Layer | Composition | Role |
---|---|---|
Carbide Tip | 88-97% WC particles in Co matrix | Imparts hardness and wear resistance |
Silver Braze Alloy | Silver, Copper, Zinc, Cadmium, Nickel | Joins carbide insert to tool via brazing process |
Base Tool Material | Steel, Tungsten Carbide | Imparts strength and forms tool body |
The ingredients are combined using powder metallurgy process involving controlled pressing and sintering to produce the solid tungsten carbide insert. Braze alloy in powder form is applied on surface to be joined and heated over 1000 degree C in controlled atmosphere to melt the alloy which joins the carbide tip and tool via capillary action. This forms a strong metallurgical bond during subsequent controlled cooling. Nickel braze alloy is also coming into prominence due to environmental concerns over use of cadmium in silver braze.
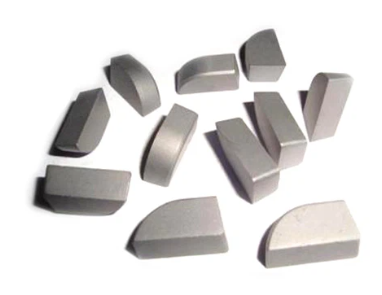
Types and Grades
Carbide tips brazed on variety of cutting, grinding, drilling, milling tools are classified based on properties and applications into types and grades:
Table 2: Major Carbide Brazed Insert Types and Grades
Type | Grade | Description |
---|---|---|
P | P10-P50 | General purpose positive carbide inserts across materials |
M | M10-M50 | Sharp inserts for high precision machining of steel, iron, alloys |
K | K10-K40 | Tougher carbide grades insert for hardened materials, interrupted cuts |
C | C1-C8 | High abrasion-resistant inserts for composite materials, graphite etc. |
S | S10-S50 | Inserts with chipbreakers designed specifically for steel materials |
H | H10-H15 | Hard tough inserts for high-temperature alloy steels |
D | D10-D50 | Grades optimized for cast iron turning and drilling operations |
CBN | B151-B198 | Cubic boron nitride composite ultrahard inserts |
Diamond | SD10 | Polycrystalline diamond or diamond-coated carbide inserts |
Carbide inserts are assigned an alphanumeric grade which indicates the binder percentage, grain properties of the carbide, and functionality in terms of application material and operation. Higher grade number indicates better resistance to wear from high temperatures or fracturing under loads. The letter prefix categorizes distinct utility across base materials groups. Advanced grades with nanostructure or coatings impart dramatically enhanced performance.
Mechanical Properties and Characteristics
Carbide tipped tools demonstrate a unique combination of hardness, strength and fracture toughness necessary for metal removal operations. Relative to high speed steel tools, they possess vastly superior hot hardness, chemical inertness under high machining temperatures and wear resistance due to the ultrahard carbide constituent supported in a tenacious cobalt matrix.
Table 3: Key Properties and Performance Metrics of Brazed Carbide Inserts
Property | Metric | Role |
---|---|---|
Hardness | 92-96 HRA | Resists abrasive wear on cutting edges |
Transverse Rupture Strength | 500-700 kgf/mm2 | Withstands high machining forces without breakage |
Fracture Toughness | 7-15 MPa√m | Sustains shocks during interrupted cuts |
Hot Hardness | Rockwell hardness retention 80% at 700°C | Maintains hardness at high temperatures near cutting interface |
Chemical Inertness | Stable tungsten oxide layer formation above 500°C | Resists diffusion wear and adhesion in hot zones |
Carbide Insert Strength relative to Titanium
- Carbide brazed tools have 2X higher transverse rupture strength than titanium for enhanced stability under loads
- 70% stronger in terms of modulus of rupture properties indicating superior resistance to fracturing
Carbide Tool Hardness against Ceramics
- Comparable hardness in the 92-94 Rockwell A range to silicon nitride and silicon carbide ceramics
- Generally harder than ceramics by up to 5% enhancing wear rate under high abrasion
Carbide grades versus HSS in thermal stability
- Exhibits over 50% higher red hardness indiciating effectiveness at elevated temperatures
- Retains hardness significantly more at over 600 deg Celsius temperature on cutting interface
Tougher by Design for Difficult Materials
- Improved binder amount, grain size distributions and protective coatings boost fracture toughness by up to 40% over some standard inserts
- Enables reliable machining of hardened, interrupted-cut steels by resisting crack initiation and propagation
Therefore carbide tipped brazed tools offer a prudent balance of hardness to stay sharp, strength to resist deformation and fracture toughness to absorb stresses – necessary virtues to outperform while removing material under rigors of machining.
Size Standards and Dimensions
Carbide inserts for brazing come in a range of international size standards, geometries and thicknesses to suit tooling and final application needs.
Table 4: Common Size Series and Dimensions for Brazed Carbide Tips
Size Series | Insert Dimensions (mm) | Max. Thickness Available |
---|---|---|
ISO RNGN | 9.5, 12.7, 16, 19.5, 25.4 | 3.18 |
ISO RNGX | 4.76, 9.5, 12.7, 16 | 4.76 |
ISO RNMN | 7.8, 9.5, 12 | 4.75 |
ISO SNGX | 6.35, 9.5, 12.7 | 3.97 |
ISO TNGX | 3.5, 4.5, 6 | 3 |
ISO TNGA | 16, 20, 25 | 6.35 |
ISO TNMA | 16, 20, 25 | 3.18 |
Custom tip geometries and fixations like shapes with chipbreakers, threaded studs or posts, anti-rotation lugs or clamps are also available based on tooling interface needs.
Graded RNMN inserts around 10mm size are extremely common across general purpose turning, drilling, milling applications for steel and difficult alloys. Larger diameter 25mm inserts withstand heavy loads in mining equipment, while micro sizes below 5mm enable precision boring and gearcutting operations.
Comparative Machining Performance
Brazed carbide inserts transform the output and economics of machining applications across sector, materials, parameters and scenarios as elaborated below:
Table 5: Advantages of Carbide Tips over HSS, Ceramics, PCD/CBN
Versus | Section | Advantages |
---|---|---|
High Speed Steel | Turning, Drilling | – 2-4X higher tool life – Higher productivity and lower cost per part – 40% increased cutting speeds and feeds |
Ceramics | Hard Turning, Cast Iron | – Stronger inserts avoid cracks under high loads – Thermal shock resistance enables deeper cuts |
PCD/CBN | Non-ferrous Alloys | – Operate at 50% hotter zones closer to interface – Cost effective option for aluminum, brass etc. |
Carbide Insert Grades for Materials
Material | Preferable Carbide Grade | Benefits |
---|---|---|
Normal Carbon Steels | M25, P25 | Universal sharp insert for steel turning |
Stainless Steels | M35, P35 | Smooth machined surface |
Hardened Steels 55-70 HRC | K25, S25-S40 | Avoids rapid wear out from hard phases |
Cast Iron | D25-D30 | Optimized chipbreakers; smooth graphite pockets |
Aluminum Alloys | M25-M30 Uncoated | Prevent aluminum build-up with sharp edges |
Titanium/Nickel Alloys | C2-C6, K15 Coated | High strength and temperature resistance inserts |
Advanced carbide grades for specific steel types, heat-resistant superalloys, interrupts cuts, High Efficiency Machining bring dramatic tool life enhancement over conventional options.
Application Areas
Carbide brazed inserts boost performance across vital metalcutting usages:
Table 6: Common Application Areas for Brazed Carbide Tipped Tooling
Industry | Applications | Benefits |
---|---|---|
Automotive | Engine block boring Driveshaft turning Transmission gear cutting | Higher machining productivity; Smooth surface finish |
Aerospace | Blisk milling Snagging titanium castings | Reduced tool costs on expensive alloys |
Die and Mold | Finishing Operations | High precision components; Fine surface finish |
Oil & Gas | Drilling Equipment | Reliable operation on offshore rigs |
Construction & Mining | Crushing, Drilling, Bits | Heavily loaded rock cutting equipment |
Brazed carbide inserts thus generate superior asset utilization across manufacturing, indirectly contributing to improved quality, lower prices and customer satisfaction.
Suppliers and Indicative Pricing
Leading manufacturers offering reliable quality carbide inserts globally are:
Table 7: Major Carbide Brazed Insert Suppliers and Grades
Supplier | Grades Available | Prices per Insert |
---|---|---|
Sandvik Coromant | GC4215 (~P35), GC3210 (~K25), GC1110 (~M25) | USD 24-144 |
Kennametal | BZ235 (~K35), BZ733 (~M30), BZ731 (~P30) | USD 15-62 |
Mitsubishi MC | VP15TF (~P20), XO35 (~M35), VF8 (~K20) | USD 14-98 |
Iscar | IC908 (~M30), DC915 (~K25), AC830 (~P30) | USD 19-124 |
Seco | TD100 (~P25), MD163 (~M35), PD626 (~K20) | USD 12-81 |
TaeguTec | T9325 (~P30), T9215 (~M30), T8325 (~K20) | USD 8-72 |
Carbide grade insert prices are based on size, grade, geometry, coatings etc. and typically range from USD 10 per piece for general purpose grades in standard sizes; upto USD 250 for advanced specialty inserts used in custom tooling. Given the dramatically improved tool life over other cutters like HSS, carbide brazed inserts generate much superior cost-per-cut economics. Private label carbide inserts are also available.
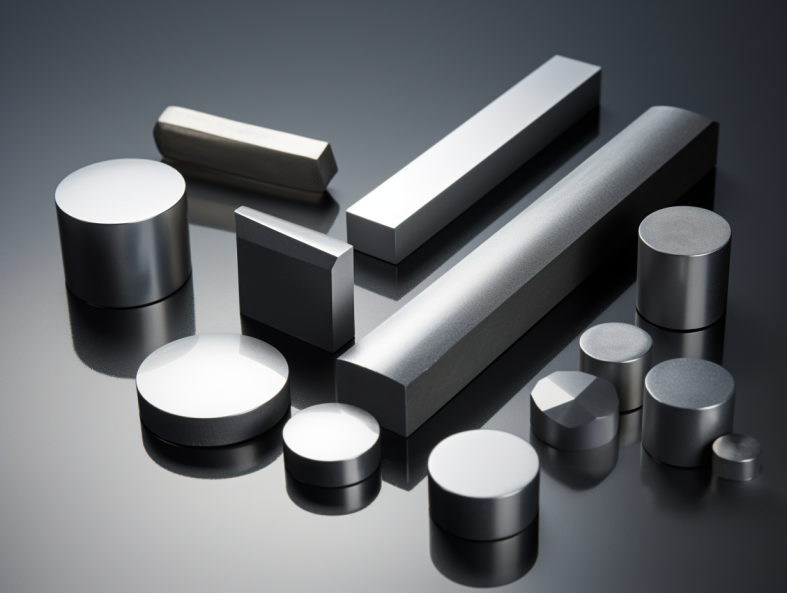
Advantages and Limitations of Carbide Brazed Tips
Parameter | Advantages | Limitations |
---|---|---|
Tool Life and Productivity | – Vastly outlasts HSS; At least 2-3X life – Increased cutting parameters – speeds, feeds by 30-50% – Generates higher metal removal rates | – Not recommended for very light finishing cuts – Cost per insert higher than solid carbide |
Machinability Range | – Hard materials upto 70 HRC like treated steels – Most metals – carbon steels, stainless steels, cast iron, titanium, aluminum etc. | – Very low rigidity machines may face vibration issues – Limited utility for wood, plastics, ceramics cutting |
Cost Implications | – Reduces overall tooling cost and cost per part – Enables unmanned automated production | – Higher insert prices versus HSS tools – Need for special indexable tool holders |
Ease of Use | – Quick insert indexes saves downtime – Easier to regrind/recoat inserts than HSS tools | – Need proper insert handling to avoid cracks – Insert seating needs to be precise to avoid failures |
Therefore carbide brazed inserts boost productivity and lower operating costs substantially despite higher prices over HSS, while easing usage by facilitating quick changeovers. They expand the scope of machinable materials despite limitations in rigidity or finishing requirements.
Frequently Asked Questions
Q: How is brazing used to fix carbide tips onto tools?
A: An intermediate braze alloy powder paste containing silver, copper, nickel is applied between carbide insert and tool surface. The assembly is heated above meting point of braze alloy, resulting in capillary flow which creates strong metallurgical bonding between tip and tool body.
Q: Why silver based braze alloys are more popular over nickel based?
A: Silver braze alloys containing some nickel flow at relatively lower temperatures between 650-800 deg C versus over 1000 deg C for nickel brazes. This prevents degradation of the carbide tip properties. However, nickel brazes are gaining acceptance to avoid environmental issues related to presence of cadmium in some silver brazes.
Q: How to select the right carbide grade insert?
A: Consider the hardness and abrasiveness of work material, whether continuous or interrupted cuts, parameter ranges contemplated, need for precision etc. Carbide inserts have differing proportions of cobalt binder, carbide grain sizes and grain distribution optimized for specific materials groupings. Consult manufacturers’ technical literature to select appropriate grade.
Q: What are the pros and cons of brazed versus solid carbide tools?
A: Brazed carbide inserts allow changing just the worn tip easily while retaining the tool body, yielding cost benefits. Minor uneven seating of the tip can however cause uneven wear. Solid carbide undergoes uniform wear but discarding the entire tool when worn out raises costs. Productivity levels are comparable.
This concludes the overview on carbide brazed inserts – their utility derives from markedly enhancing the production economics across vital metal removal processes through a prudent balance of hardness and strength. Continued innovation in compositions, coatings and fixations expands the scope of this integral technological pillar of the manufacturing sector.