- Carbide endmill
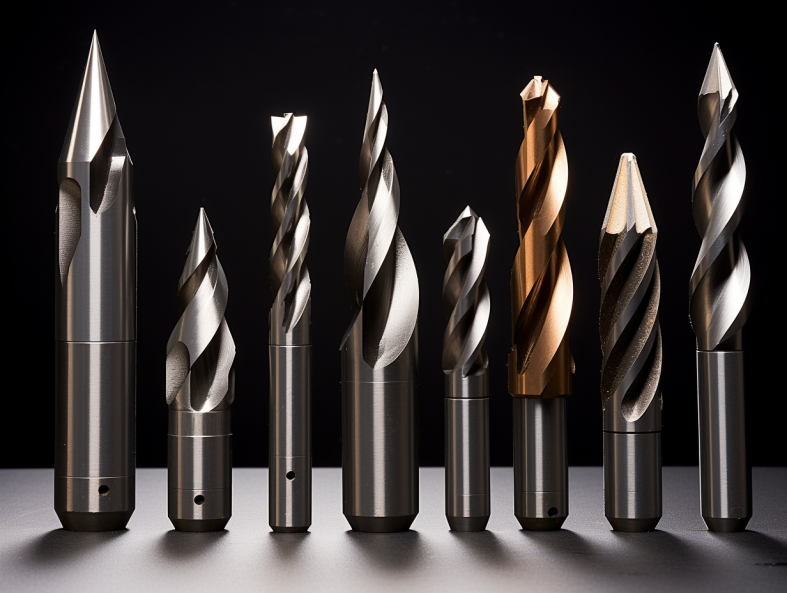
Carbide End mills
Carbide end mills are essential tools used in milling operations for cutting and shaping various materials. They are highly regarded for their hardness, heat resistance, and versatility. Made from a combination of tungsten carbide particles and a cobalt binder, carbide end mills offer superior durability and wear resistance compared to other types of end mills.
The exceptional hardness of carbide allows it to withstand high cutting forces and maintain its cutting edges for extended periods, resulting in longer tool life. Additionally, carbide’s excellent heat resistance allows these end mills to operate at high speeds and temperatures without compromising their cutting performance.
A wide range of carbide end mill options is available, including various sizes, geometries, and coatings. Different types of end mills, such as square end mills, ball end mills, and corner radius end mills, enable diverse milling operations, including slotting, profiling, and contouring. These tools are used across industries like machining, metalworking, and manufacturing to machine materials like steel, stainless steel, cast iron, aluminum, brass, and plastics.
Contact us if what you need is not shown here.
Introduction
Carbide end mills are cutting tools used in milling operations to remove material from a workpiece. They are widely used in various industries, including machining, metalworking, and manufacturing. Carbide end mills are preferred over other types of end mills due to their exceptional hardness, high heat resistance, and ability to cut through various materials efficiently.
Carbide is a composite material made primarily of tungsten carbide (WC) particles bonded together with a cobalt (Co) matrix. The combination of tungsten carbide’s hardness and cobalt’s toughness creates a durable and wear-resistant cutting tool. Carbide end mills typically have a cylindrical shank, with cutting edges at one end and a shank for holding in a milling machine at the other.
Composition and Structure
Carbide end mills consist of tungsten carbide particles mixed with a cobalt binder, forming a hard and durable cutting tool. The tungsten carbide provides hardness, while the cobalt binder offers toughness. The grain size and structure of the carbide particles determine the tool’s performance. Additionally, carbide end mills often feature coatings like titanium nitride or diamond-like carbon for improved wear resistance. The end mills have a cylindrical shank, cutting edges with various geometries, and can have different flute designs. Overall, carbide end mills are known for their hardness, heat resistance, and excellent cutting performance.
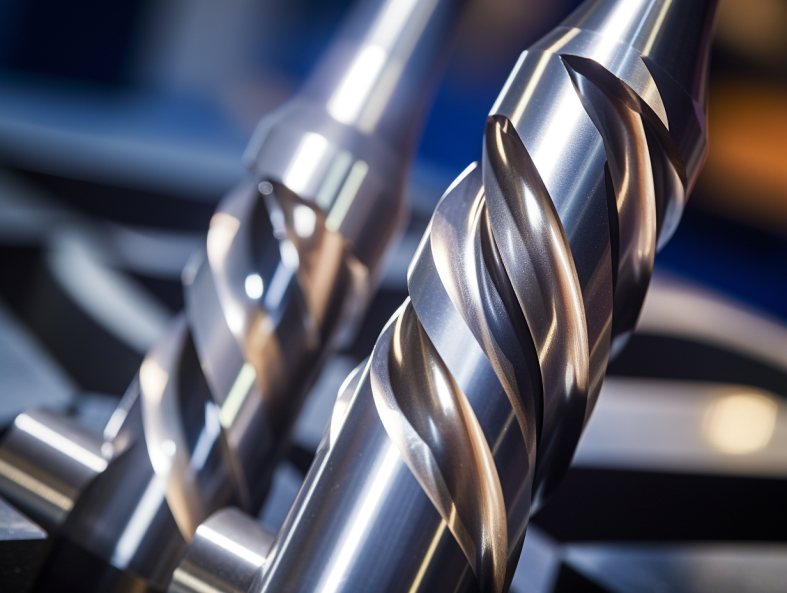
Hardness
Carbide end mills are extremely hard due to the presence of tungsten carbide particles. This hardness enables them to cut through tough materials like steel and iron with ease.
Wear Resistance
Wear Resistance: Carbide end mills are highly resistant to wear and abrasion. This property allows them to maintain their sharp cutting edges even after prolonged use, resulting in longer tool life.
Heat Resistance
Carbide end mills have excellent heat resistance, which allows them to withstand high cutting temperatures generated during machining operations.
Toughness
While carbide is known for its hardness, the addition of a cobalt binder enhances the toughness of carbide end mills.
Chemical Inertness
Carbide end mills are chemically inert, meaning they are resistant to chemical reactions with most workpiece materials.
Precision
Carbide end mills offer high precision and dimensional accuracy in machining operations. Their hardness allows for sharp cutting edges, resulting in clean and precise cuts.
Versatility
Carbide end mills are versatile tools suitable for a wide range of machining applications. They can effectively cut various materials.
Coatability
Carbide end mills can be coated with various materials. These coatings enhance the tool’s surface hardness, lubricity, and improving performance.
Carbide Material Preparation:
Tungsten carbide powder and cobalt powder are prepared in predetermined ratios and thoroughly mixed to create a homogeneous blend.
Compaction
The blended powders are placed in a hydraulic press and subjected to high pressures to compact them into a solid shape known as a green body.
Pre-Sintering
The green bodies are pre-sintered in a furnace at a specific temperature to remove binders, volatiles, and to strengthen the green body.
Shaping
The pre-sintered green bodies are shaped using various machining techniques such as grinding, cutting, and milling to achieve the desired dimensions and geometries of the end mill.
Sintering
The shaped green bodies are placed in a sintering furnace and subjected to temperatures close to the melting point of cobalt but below the melting point of tungsten carbide.
Tool Body Production
Once the carbide end mill is shaped, it can be coated with various coatings to enhance its performance. Coatings are applied through processes like physical vapor deposition (PVD) or chemical vapor deposition (CVD).
Finishing
After coating, the carbide end mills may require additional finishing processes, such as grinding or lapping, to achieve the desired surface finish and cutting edge sharpness.
QC and Packaging
The finished carbide end mills undergo rigorous quality control inspections. Once approved, they are properly packaged for distribution to customers.
Metal Cutting
Carbide end mills are highly effective in cutting and machining various metals. Due to their hardness and wear resistance, they can efficiently remove material from materials like steel, stainless steel, aluminum, brass, and cast iron. Whether it’s milling, profiling, slotting, or contouring, carbide end mills provide superior performance and long tool life in metal cutting operations.
Woodworking
Carbide end mills are also employed in woodworking applications. They can be used to shape, profile, and cut different types of wood, including hardwoods and softwoods. Carbide end mills offer high cutting speeds and exceptional precision, making them suitable for tasks such as routing, drilling, and carving in woodworking projects.
Aerospace Industry
The aerospace industry requires high-precision machining of aerospace-grade materials like titanium alloys, Inconel, and other heat-resistant alloys. Carbide end mills are capable of handling such demanding materials with their hardness, heat resistance, and edge retention. These tools are commonly used for machining complex components in aircraft structures, engine parts, and other aerospace applications.
Mold and Die Making
Carbide end mills are extensively used in mold and die making industries. The molds and dies are typically made from hardened materials like tool steel or hardened steels with high wear resistance. Carbide end mills can efficiently remove material from these tough materials, providing precise and intricate machining for creating mold cavities, die pockets, and intricate surface details.
Metal Cutting
Carbide end mills are highly effective in cutting and machining various metals. Due to their hardness and wear resistance, they can efficiently remove material from materials like steel, stainless steel, aluminum, brass, and cast iron. Whether it’s milling, profiling, slotting, or contouring, carbide end mills provide superior performance and long tool life in metal cutting operations.
Woodworking
Carbide end mills are also employed in woodworking applications. They can be used to shape, profile, and cut different types of wood, including hardwoods and softwoods. Carbide end mills offer high cutting speeds and exceptional precision, making them suitable for tasks such as routing, drilling, and carving in woodworking projects.
Aerospace Industry
The aerospace industry requires high-precision machining of aerospace-grade materials like titanium alloys, Inconel, and other heat-resistant alloys. Carbide end mills are capable of handling such demanding materials with their hardness, heat resistance, and edge retention. These tools are commonly used for machining complex components in aircraft structures, engine parts, and other aerospace applications.
Mold and Die Making
Carbide end mills are extensively used in mold and die making industries. The molds and dies are typically made from hardened materials like tool steel or hardened steels with high wear resistance. Carbide end mills can efficiently remove material from these tough materials, providing precise and intricate machining for creating mold cavities, die pockets, and intricate surface details.
A tungsten carbide insert is a cutting tool made from tungsten carbide, a material known for its incredible hardness and wear resistance. These inserts are used in machining processes to cut, shape, and finish various materials, including metals and composites. They are highly valued for their ability to maintain a sharp cutting edge even under extreme conditions.
Yes, tungsten carbide inserts can be resharpened, but the process requires specialized equipment and expertise. Resharpening can extend the tool’s life and maintain cutting performance, but it is often more cost-effective to replace the inserts.
Boring inserts can machine a wide range of materials, including steels, cast irons, non-ferrous metals, plastics, and composites. Their high hardness makes them particularly effective for cutting tough and abrasive materials.
- Increased Wear Resistance: Coatings like TiN or TiAlN extend tool life.
- Enhanced Performance: Better heat resistance and reduced friction.
- Higher Cutting Speeds: Allow for faster machining processes.
- Improved Surface Finish: Produces smoother and more precise cuts.
- Versatility: Suitable for a wide range of materials and applications.
Store inserts in a clean, dry environment, protected from impact, moisture, and extreme temperatures. Use appropriate chip brushes and cleaning methods to remove chips and debris after each use. Proper storage and maintenance can significantly extend the life of your inserts and ensure consistent performance.
Consider the material being machined (hardness, machinability), the type of turning operation (roughing, finishing), the desired tool life, and the cutting parameters (speed, feed, depth of cut). Consult supplier catalogs, online resources, or seek expert advice to determine the most suitable grade.
Threading inserts for turning are indexable cutting tools specifically engineered to machine external and internal threads on lathes or turning centers. Unlike their counterparts used for general turning operations, threading inserts feature precisely ground cutting edges that correspond to the desired thread form, pitch, and diameter. This specialized geometry allows for the efficient and accurate creation of threads in a single pass or multiple passes, depending on the thread specifications and material being machined.
- Turning Operations: For precise metal cutting and shaping.
- Milling: In both face and end milling tasks.
- Drilling: To enhance tool life and performance.
- Boring: For accurate hole enlarging.
- Grooving and Threading: In industrial machining.
Selecting the appropriate rake angle depends on the material being machined and the desired cutting conditions. Softer materials and finishing operations generally benefit from positive rake angles, while harder materials and roughing operations often require negative rake angles.
Lorem ipsum dolor sit amet, consectetur adipisicing elit. Optio, neque qui velit. Magni dolorum quidem ipsam eligendi, totam, facilis laudantium cum accusamus ullam voluptatibus commodi numquam, error, est. Ea, consequatur.
The number of flutes affects the cutting performance and material removal rate. Fewer flutes provide better chip evacuation, which is important for non-ferrous metals that tend to generate longer chips. However, more flutes can offer smoother cuts and better finishes. The choice depends on the specific material and the milling operation.
The optimal number of flutes depends on factors like material being machined, desired surface finish, and available spindle power. More flutes generally provide smoother finishes and higher material removal rates but require increased spindle speed and power.
Signs of wear include increased cutting forces, surface finish degradation, and chip welding. Optimize cutting parameters, ensure proper coolant application, and avoid excessive tool overhang to extend tool life.
- Milling: For contouring, slotting, and pocketing.
- Die and Mold Making: Precise shaping and finishing.
- Aerospace and Automotive: High-performance material removal.
- Medical Devices: Precision machining of complex parts.
- Prototyping: Creating detailed and intricate designs.
Cemented carbide end mills offer significantly greater hardness, wear resistance, and heat resistance compared to HSS end mills. This translates to extended tool life, higher cutting speeds, increased material removal rates, and the ability to machine harder materials.
Solid carbide end mills can cut a wide range of materials, including steel, stainless steel, aluminum, titanium, and composites. Their hardness and wear resistance make them suitable for both soft and hard materials.
3 flute end mills offer a better balance between chip evacuation and surface finish compared to 2 flute end mills. They generally produce a smoother surface finish while still providing efficient chip removal in many materials, making them versatile for various applications.
2 flute end mills excel in efficient chip evacuation, particularly in softer materials, and allow for higher cutting speeds and feed rates due to reduced cutting edge contact. This translates to faster machining times and increased productivity.
4 flute end mills offer increased stability, improved chip evacuation, and generally smoother surface finishes compared to 2 flute end mills. This makes them well-suited for a wider range of materials and machining operations, particularly when higher cutting forces are involved.
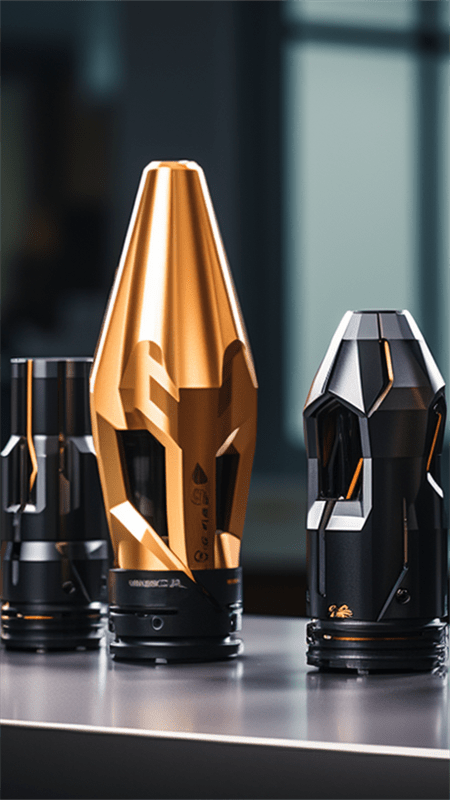
Data
2 Flute End Mills Description
2-flute end mills are versatile tools with two cutting edges. They are used for various machining tasks and can handle a wide range of materials. The flute design aids in efficient chip evacuation and provides a smooth surface finish. These end mills allow for higher feed rates, offer stability, and minimize tool deflection. Choosing the right end mill depends on the specific application and material being machined.
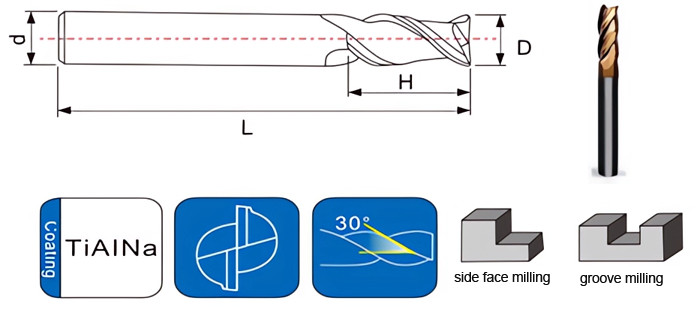
Type | Dimension (mm) | Number of teeth | ||||
---|---|---|---|---|---|---|
D | R | H | L | d | ||
TMC-2E-D1.0 | 1.0 | / | 3 | 50 | 4 | 2 |
TMC-2E-D1.5 | 1.5 | / | 4 | 50 | 4 | 2 |
TMC-2E-D2.0 | 2.0 | / | 6 | 50 | 4 | 2 |
TMC-2E-D2.5 | 2.5 | / | 8 | 50 | 4 | 2 |
TMC-2E-D3.0 | 3.0 | / | 8 | 50 | 4 | 2 |
TMC-2E-D3.5 | 3.5 | / | 10 | 50 | 6 | 2 |
TMC-2E-D4.0 | 4.0 | / | 11 | 50 | 4 | 2 |
TMC-2E-D4.5 | 4.5 | / | 11 | 50 | 6 | 2 |
TMC-2E-D5.0 | 5.0 | / | 13 | 50 | 6 | 2 |
TMC-2E-D5.5 | 5.5 | / | 16 | 50 | 6 | 2 |
TMC-2E-D6.0 | 6.0 | / | 16 | 50 | 6 | 2 |
TMC-2E-D7.0 | 7.0 | / | 20 | 60 | 8 | 2 |
TMC-2E-D8.0 | 8.0 | / | 20 | 60 | 8 | 2 |
TMC-2E-D9.0 | 9.0 | / | 22 | 75 | 10 | 2 |
TMC-2E-D10.0 | 10.0 | / | 25 | 75 | 10 | 2 |
TMC-2E-D11.0 | 11.0 | / | 26 | 75 | 12 | 2 |
TMC-2E-D12.0 | 12.0 | / | 30 | 75 | 12 | 2 |
TMC-2E-D14.0 | 14.0 | / | 32 | 75 | 14 | 2 |
TMC-2E-D16.0 | 16.0 | / | 45 | 100 | 16 | 2 |
TMC-2E-D18.0 | 18.0 | / | 45 | 100 | 18 | 2 |
TMC-2E-D20.0 | 20.0 | / | 45 | 100 | 20 | 2 |
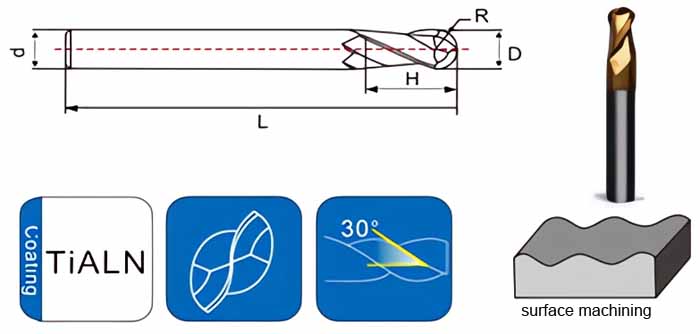
Type | Dimension (mm) | Number of teeth | ||||
---|---|---|---|---|---|---|
D | R | H | L | d | ||
TMC-2B-D1.0R0.5 | 1.0 | 0.50 | 6 | 50 | 4 | 2 |
TMC-2B-D1.5R0.75 | 1.5 | 0.75 | 6 | 50 | 4 | 2 |
TMC-2B-D2.0R1.0 | 2.0 | 1.00 | 6 | 50 | 4 | 2 |
TMC-2B-D2.5R1.25 | 2.5 | 1.25 | 6 | 50 | 4 | 2 |
TMC-2B-D3.0R1.5 | 3.0 | 1.50 | 6 | 50 | 4 | 2 |
TMC-2B-D3.5R1.75 | 3.5 | 1.75 | 6 | 50 | 6 | 2 |
TMC-2B-D4.0R2.0 | 4.0 | 2.00 | 6 | 50 | 4 | 2 |
TMC-2B-D5.0R2.5 | 5.0 | 2.50 | 6 | 50 | 6 | 2 |
TMC-2B-D5.5R2.75 | 5.5 | 2.75 | 6 | 50 | 6 | 2 |
TMC-2B-D6.0R3.0 | 6.0 | 3.00 | 6 | 50 | 6 | 2 |
TMC-2B-D7.0R3.5 | 7.0 | 3.50 | 8 | 60 | 8 | 2 |
TMC-2B-D8.0R4.0 | 8.0 | 4.00 | 8 | 60 | 10 | 2 |
TMC-2B-D9.0R4.5 | 9.0 | 4.50 | 10 | 75 | 10 | 2 |
TMC-2B-D10.0R5.0 | 10.0 | 5.00 | 10 | 75 | 12 | 2 |
TMC-2B-D12.0R6.0 | 12.0 | 6.00 | 12 | 75 | 12 | 2 |
TMC-2B-D14.0R7.0 | 14.0 | 7.00 | 14 | 75 | 14 | 2 |
TMC-2B-D16.0R8.0 | 16.0 | 8.00 | 16 | 100 | 16 | 2 |
TMC-2B-D20.0R10.0 | 20.0 | 10.00 | 20 | 100 | 18 | 2 |
3 Flute End Mills Description
3-flute end mills are cutting tools that are commonly used in milling operations. They are designed with three cutting edges or flutes, which offer several advantages. One of the key benefits of 3-flute end mills is their efficient chip evacuation. The three flutes provide ample space for the chips to evacuate from the cutting area during the machining process. This helps to prevent chip clogging, which can adversely affect cutting performance and result in poor surface finishes. With improved chip evacuation, 3-flute end mills can maintain their cutting efficiency and prolong tool life.
Additionally, 3-flute end mills offer enhanced stability during machining. The presence of three cutting edges provides more support to the tool, reducing deflection and vibration. This increased stability contributes to better dimensional accuracy and surface finish in the workpiece. It also allows for higher cutting speeds and feed rates, resulting in improved productivity. Another advantage of 3-flute end mills is their ability to achieve a smoother surface finish.
3 Flutes Straight Shank Endmills
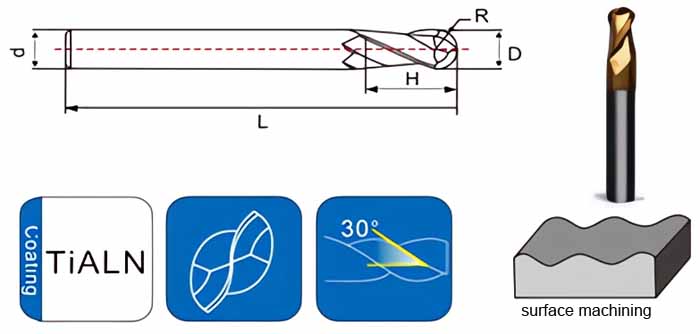
Type | Dimension (mm) | Number of teeth | ||||
---|---|---|---|---|---|---|
D | R | H | L | d | ||
TMC-3E-D1.0 | 1.0 | / | 3 | 50 | 4 | 3 |
TMC-3E-D1.5 | 1.5 | / | 4 | 50 | 4 | 3 |
TMC-3E-D2.0 | 2.0 | / | 6 | 50 | 4 | 3 |
TMC-3E-D2.5 | 2.5 | / | 7 | 50 | 4 | 3 |
TMC-3E-D3.0 | 3.0 | / | 9 | 50 | 4 | 3 |
TMC-3E-D4.0 | 4.0 | / | 12 | 50 | 6 | 3 |
TMC-3E-D5.0 | 5.0 | / | 15 | 50 | 4 | 3 |
TMC-3E-D6.0 | 6.0 | / | 18 | 60 | 6 | 3 |
TMC-3E-D8.0 | 8.0 | / | 20 | 60 | 6 | 3 |
4 Flute End Mills Description
4-flute end mills are cutting tools with four cutting edges or flutes. They are commonly used in milling operations to remove material from a workpiece. The flute design allows for efficient chip evacuation, reducing the chances of chip clogging and improving cutting performance. The main advantage of 4-flute end mills is their ability to provide a balance of cutting speed and tool rigidity. With four cutting edges, they can achieve higher feed rates compared to end mills with fewer flutes. This results in faster material removal rates and increased productivity.
The additional flutes also distribute the cutting forces across a larger surface area, reducing the tendency for the tool to chatter or deflect during machining. This improves the overall stability of the cutting process and allows for smoother surface finishes.
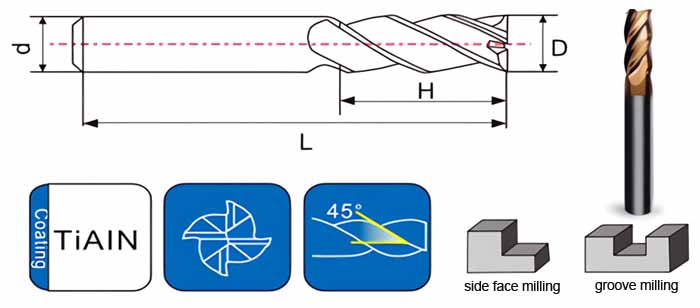
Type | Dimension (mm) | Number of teeth | ||||
---|---|---|---|---|---|---|
D | R | H | L | d | ||
TMC-2E-D1.0 | 1.0 | / | 3 | 50 | 4 | 2 |
TMC-2E-D1.5 | 1.5 | / | 4 | 50 | 4 | 2 |
TMC-2E-D2.0 | 2.0 | / | 6 | 50 | 4 | 2 |
TMC-2E-D2.5 | 2.5 | / | 8 | 50 | 4 | 2 |
TMC-2E-D3.0 | 3.0 | / | 8 | 50 | 4 | 2 |
TMC-2E-D3.5 | 3.5 | / | 10 | 50 | 6 | 2 |
TMC-2E-D4.0 | 4.0 | / | 11 | 50 | 4 | 2 |
TMC-2E-D4.5 | 4.5 | / | 11 | 50 | 6 | 2 |
TMC-2E-D5.0 | 5.0 | / | 13 | 50 | 6 | 2 |
TMC-2E-D5.5 | 5.5 | / | 16 | 50 | 6 | 2 |
TMC-2E-D6.0 | 6.0 | / | 16 | 50 | 6 | 2 |
TMC-2E-D7.0 | 7.0 | / | 20 | 60 | 8 | 2 |
TMC-2E-D8.0 | 8.0 | / | 20 | 60 | 8 | 2 |
TMC-2E-D9.0 | 9.0 | / | 22 | 75 | 10 | 2 |
TMC-2E-D10.0 | 10.0 | / | 25 | 75 | 10 | 2 |
TMC-2E-D11.0 | 11.0 | / | 26 | 75 | 12 | 2 |
TMC-2E-D12.0 | 12.0 | / | 30 | 75 | 12 | 2 |
TMC-2E-D14.0 | 14.0 | / | 32 | 75 | 14 | 2 |
TMC-2E-D16.0 | 16.0 | / | 45 | 100 | 16 | 2 |
TMC-2E-D18.0 | 18.0 | / | 45 | 100 | 18 | 2 |
TMC-2E-D20.0 | 20.0 | / | 45 | 100 | 20 | 2 |
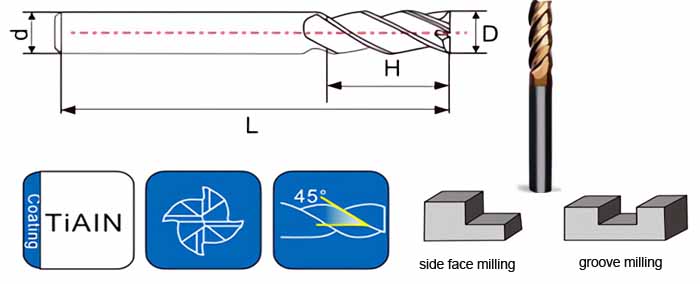
Type | Dimension (mm) | Number of teeth | ||||
---|---|---|---|---|---|---|
D | R | H | L | d | ||
TMC-4EL-D3.0 | 3.0 | / | 12 | 75 | 6 | 4 |
TMC-4EL-D4.0 | 4.0 | / | 15 | 75 | 6 | 4 |
TMC-4EL-D5.0 | 5.0 | / | 20 | 75 | 6 | 4 |
TMC-4EL-D6.0 | 6.0 | / | 20 | 75 | 6 | 4 |
TMC-4EL-D8.0 | 8.0 | / | 25 | 100 | 8 | 4 |
TMC-4EL-D10.0 | 10.0 | / | 30 | 100 | 10 | 4 |
TMC-4EL-D12.0 | 12.0 | / | 35 | 100 | 12 | 4 |
TMC-4EL-D14.0 | 14.0 | / | 40 | 100 | 14 | 4 |
TMC-4EL-D16.0 | 16.0 | / | 50 | 150 | 16 | 4 |
TMC-4EL-D20.0 | 20.0 | / | 55 | 150 | 20 | 4 |
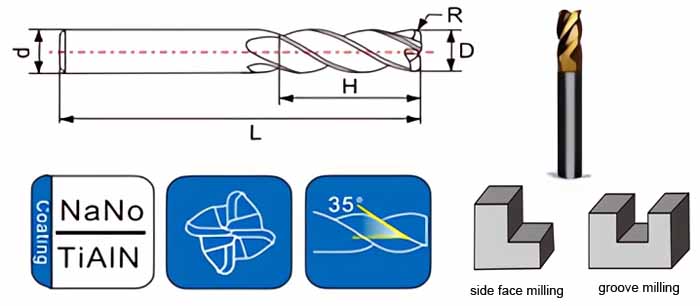
Type | Dimension (mm) | Number of teeth | ||||
---|---|---|---|---|---|---|
D | R | H | L | d | ||
TMC-4R-D3.0R0.2 | 3.0 | 0.2 | 8 | 50 | 6 | 4 |
TMC-4R-D4.0R0.3 | 4.0 | 0.3 | 10 | 50 | 6 | 4 |
TMC-4R-D4.0R0.5 | 4.0 | 0.5 | 10 | 50 | 6 | 4 |
TMC-4R-D5.0R0.5 | 5.0 | 0.5 | 13 | 50 | 6 | 4 |
TMC-4R-D5.0R1.0 | 5.0 | 1.0 | 13 | 50 | 6 | 4 |
TMC-4R-D6.0R0.5 | 6.0 | 0.5 | 16 | 50 | 6 | 4 |
TMC-4R-D6.0R1.0 | 6.0 | 1.0 | 16 | 50 | 6 | 4 |
TMC-4R-D8.0R0.5 | 8.0 | 0.5 | 20 | 60 | 8 | 4 |
TMC-4R-D8.0R1.0 | 8.0 | 1.0 | 20 | 60 | 8 | 4 |
TMC-4R-D10.0R0.5 | 10.0 | 0.5 | 25 | 75 | 10 | 4 |
TMC-4R-D10.0R1.0 | 10.0 | 1.0 | 25 | 75 | 10 | 4 |
TMC-4R-D10.0R2.0 | 10.0 | 2.0 | 25 | 75 | 10 | 4 |
TMC-4R-D10.0R3.0 | 10.0 | 3.0 | 25 | 75 | 10 | 4 |
TMC-4R-D12.0R0.5 | 12.0 | 0.5 | 30 | 75 | 12 | 4 |
TMC-4R-D12.0R1.0 | 12.0 | 1.0 | 30 | 75 | 12 | 4 |
TMC-4R-D12.0R2.0 | 12.0 | 2.0 | 30 | 75 | 12 | 4 |
TMC-4R-D12.0R3.0 | 12.0 | 3.0 | 30 | 75 | 12 | 4 |
Application Table of Machined Materials
(● perfect suitable ◐ suitable)
Workpiece | 2 flutes straight shank square endmills | 4 flutes straight shank square endmills | 4 flutes straight shank long flush endmills | 4 flutes straight shank round endmills | 2 flutes straight shank ball endmills | 3 flutes straight shank endmills |
---|---|---|---|---|---|---|
Carbon steel | ● | ● | ● | ● | ● | |
Alloy steel | ● | ● | ● | ● | ● | |
Hardened steel ∼ 40HRC | ● | ● | ● | ● | ● | |
Hardened steel ∼ 50HRC | ◐ | ◐ | ◐ | ◐ | ◐ | |
Hardened steel ∼ 55HRC | ||||||
Hardened steel ∼ 68HRC | ||||||
Stainless steel | ◐ | ◐ | ◐ | ◐ | ◐ | |
Cast iron | ● | ● | ● | ● | ● | |
Copper alloy | ||||||
Aluminium alloy | ● | |||||
Titanium alloy | ||||||
Heat-resisting alloy |
- Contact
Our team is ready to provide support
Truer Carbide is committed to providing efficient solutions to problems. Each team member has the expertise and experience to quickly understand and meet your needs.