carbide indexable inserts represent replaceable cutting tips used across metalworking operations like turning, milling and boring. This guide serves as an in-depth reference on carbide indexable inserts – exploring materials, geometry formats, coatings, specifications, comparative performance, costs, applications and more.
Overview of Carbide Indexable Inserts
Indexable carbide inserts comprise small cutting pieces with specialized shapes/coatings brazed onto tool holders for machining applications. Key attributes:
- Composition: Tungsten or titanium carbide substrates (>85%)
- Geometry: ISO standardized shapes and size dimensions
- Coatings: Titanium nitride (TiN), titanium carbide (TiC) etc.
- Indexing: Rotated to expose fresh cutting edges
- Key traits: Hardness, wear resistance, heat tolerance
Offering extreme hardness and high hot hardness, indexable carbide inserts facilitate faster machining speeds, better finish quality and prolonged life versus high speed steel alternatives.
Grades of Carbide Indexable Inserts
The carbide composition determines thermal and mechanical behaviors:
Grade Type | Description | Key Properties |
---|---|---|
C2 & C6 | Straight tungsten carbides | Good impact strength |
C4 & C5 | Mixed/complex carbides | Enhanced hardness and heat resistance |
P Grades | Intrinsic PVD coatings | Oxidation protection at high cutting temps |
M Grades | CVD or MT-CVD coatings | Best all-around wear resistance |
Table 1: Primary grade categories of carbide indexable inserts based on composition/coatings
Selecting the right balance of hardness, built-in coating types and application temperatures dictates grade choice for optimal tool life.
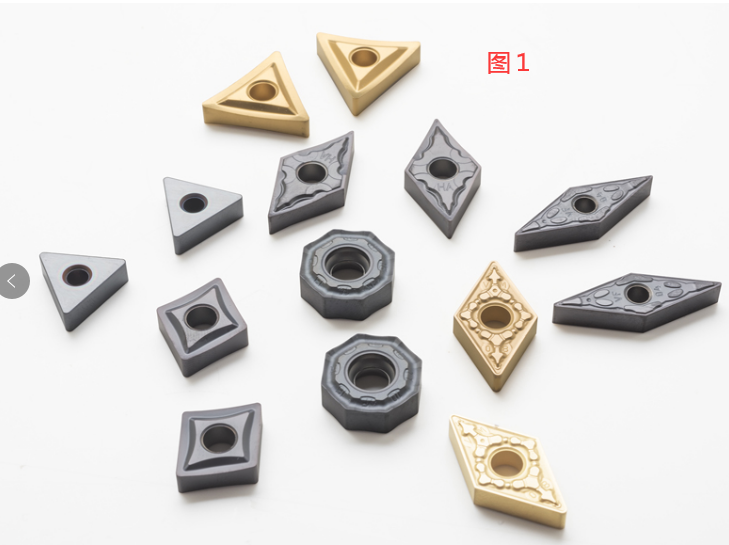
Insert Geometry Formats
Carbide inserts come in standardized ANSI and ISO dimensions and shapes:
Insert Style
Shape | Description | Key Applications |
---|---|---|
Triangle | General purpose turning, grooving, boring, parting | Most common insert style |
Rhombic | High feed milling, drilling, tapping | Used for milling cutters |
Square | Low speed finishing to precision turning | Fit a range of cutter sizes |
Round | Boring bars, grooving, parting | Multipurpose insert type |
Table 2A: Common indexable carbide insert geometries and applications
Size Parameters
Dimension | Specification |
---|---|
Inscribed Circle | ISO/ANSI defined sizes (e.g. IC328) |
Thickness | Available in fine, medium and heavy pitch sizes |
Angles | Determined by insert shape |
Edge Preps | Chamfer, hone radius options |
Table 2B: insert geometry dimensions, angles and edge specs
Standardized indexable insert dimensions, angles and edges enables interchangeable usage across various tool holders.
Insert Coatings
Protective coatings add lubricity and durability:
Coating | Key Attributes |
---|---|
Titanium carbide (TiC) | Heat resistance to 1000°C Excellent wear protection |
Titanium nitride (TiN) | High surface hardness Color identification aids |
Aluminum oxide (Al2O3) | Insulating properties for high electrical/thermal fatigue resistance |
Zirconium nitride (ZrN) | Good galling protection Suitable for high edge loads |
Table 3: Major types of specialty coatings applied to indexable carbide inserts
Coatings focus primarily on improving oxidation life, abrasion resistance and reducing coefficient of friction. Multiple layers combine strengths.
Specifications
Relevant quality metrics include:
Standard | Measure | Values |
---|---|---|
ISO 1832 | Hardness | 88 to 93 HRA (1600-2,000 HV) |
ISO 3685 | Transverse rupture strength | 2.5 GPA minimum |
ISO 8688-2 | Fracture toughness | 7 MPa√m |
ISO 13399 | Wear testing | 0.1mm flank wear in 25 minutes |
Table 4: Indexable carbide insert certification specifications
Adhering to published quality thresholds ensures insert integrity, lineup consistency and reliable producer comparisons.
Leading Carbide Insert Manufacturers
Top global suppliers include:
Company | Brand Names | Price Range |
---|---|---|
Kennametal | KC, MP | $4 – $15 per insert |
Sandvik Coromant | GC, LC | $5 – $20+ per insert |
Iscar | IC, Sumo | $3 – $18 per insert |
Kyocera Unimerco | STGCR, ALTUR | $2 – $12 per insert |
Tungaloy | TLN, TDN | $4 – $16 insert dependent |
Table 5: Major indexable carbide insert brands and price ranges
Prices vary based on insert geometries, grades, purchase volumes and tool types. Advanced coating and complex compositions command premiums.
Metal Cutting Applications
Indexable carbide facilitates world-class machining productivity:
Process | Benefits Over HSS |
---|---|
Turning | Higher surface speeds and feeds boost output 2-3x |
Milling | Improved finishes, complex geometries |
Drilling | Excellent burr and residual stress control |
Tapping | Prolong tap life, precision internal threads |
Industries
- Automotive: Engine blocks, driveshafts, valves
- Aerospace: Structural components, landing gear, hydraulics
- Medical: Orthopedic implants, devices, tooling
- Die/mold: Polished surfaces, reliable dimensions
Table 6: Broad usage of indexable carbide inserts across manufacturing
Indexable carbide enables holding tighter tolerances, extending production runs between tool changes and machining challenging superalloys over high speed or carbon tool steels.
Comparative Pros and Cons
Advantages vs Steel | Tradeoffs |
---|---|
2x – 5x tool life | Higher per insert cost |
Faster speeds/feeds possible | Advanced technical understanding required |
Pre-engineered geometries | Limited very large part rigidity currently |
Improved surface finishes | Higher initial toolholder investment |
Table 7: Primary benefits and challenges using indexable carbide inserts
The extreme hardness, built-in edge preps and standardized approach facilitates reliable scaling of moderate batch manufacturing. Coatings continue advancing wear protection at elevated temperatures.
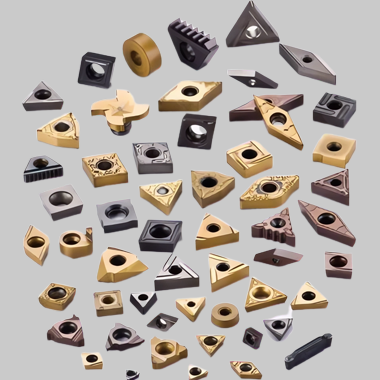
Indexable Carbide Insert FAQs
Q: What factors affect indexable carbide insert replacement cycles?
A: Speeds/feeds, workpiece material, cut depth, machine tool rigidity and coolant regimen primarily determine effective insert lifetime before rotating/replacing.
Q: What is the difference between indexable and solid carbide tools?
A: Indexable employs replaceable inserts brazed into toolholders saving re-grinding time. Solid carbide makes entire toolbody from carbide costing 2-4x more.
Q: Are ceramic inserts a replacement for carbide inserts?
A: Ceramics serve high speed niche applications given brittleness limitations. Carbide spans more general machining purpose with standardization around geometries, tooling and techniques.
Q: How do I measure and diagnose causes of insert wear or failure?
A: Inspection of flank/crater wear patterns, edge breakdowns, fracture surfaces and discoloration reveals predominant wear mechanisms guiding corrective action like speeds, feed tuning.
Conclusion
Carbide indexable inserts deliver enhanced machining productivity over high speed steel while minimizing tool regrinds through standardized geometries and replacement approaches – facilitating improved output across turned components to precision dies. Please reach out regarding any questions on insert grade selection, technical coaching or cost optimizations for your manufacturing lines.