The world of machining and manufacturing is filled with advanced tools and materials that boost productivity, precision, and durability. One such innovative product is the helical coolant holes carbide rod. These rods are essential for high-performance cutting tools, and their design ensures efficient cooling, prolonged tool life, and enhanced machining precision. But what exactly are these rods, and how do they differ from other carbide rods? Let’s dive deep into the details, breaking down everything from composition to applications, production process, and more.
Understanding Helical Coolant Holes Carbide Rods
Helical coolant holes carbide rods are tungsten carbide-based cylindrical rods with spiral (helical) coolant channels running through them. These coolant channels are engineered to optimize the flow of cooling fluids during machining, which prevents heat buildup and increases cutting efficiency.
Let’s look at the types of helical coolant holes carbide rods in the table below:
Type | Number of Coolant Holes | Helical Angle | Coating | Features |
---|---|---|---|---|
Single Helical Hole | 1 | 30° | None or TiAlN | Ideal for low-intensity operations, providing moderate cooling. |
Double Helical Holes | 2 | 40° | CVD or PVD Coating | Suitable for medium-duty machining, better cooling coverage. |
Triple Helical Holes | 3 | 45° | DLC or Nano-Coating | Optimized for high-speed machining, maximum cooling. |
Multi-Helical Holes | 4+ | 50° and above | Various Coatings | Designed for ultra-precision cutting in aerospace and automotive sectors. |
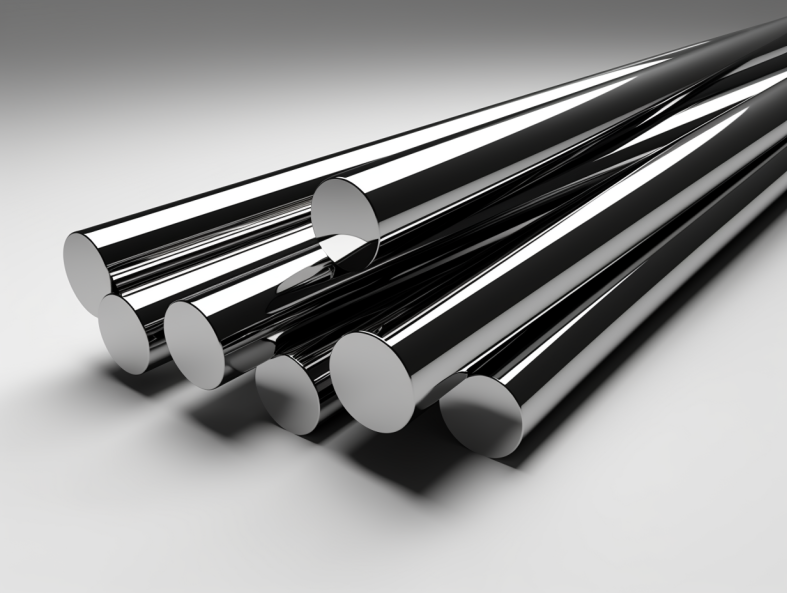
Raw Material and Composition Analysis
The base material for helical coolant holes carbide rods is tungsten carbide, a composite made of tungsten (W) and carbon (C), which is bonded with a metallic binder like cobalt (Co). Additional additives may enhance specific properties.
Key Composition Features:
- Tungsten Carbide (WC): Provides high hardness and wear resistance.
- Cobalt (Co): Enhances toughness and ductility.
- Additives (e.g., TaC, TiC): Improve heat resistance and grain refinement.
Material Component | Percentage (%) | Purpose |
---|---|---|
Tungsten Carbide (WC) | 85-95% | Primary hard material for cutting. |
Cobalt (Co) | 5-15% | Binder to improve toughness. |
Titanium Carbide (TiC) | 0-3% | Increases thermal stability. |
Tantalum Carbide (TaC) | 0-2% | Enhances grain strength. |
Applications of Helical Coolant Holes Carbide Rods
Thanks to their versatility, these rods are widely used across industries that demand precision and efficiency. Below is a comprehensive table summarizing their applications:
Industry | Application | Advantages |
---|---|---|
Aerospace | Milling, drilling of composites and alloys. | High precision and wear resistance. |
Automotive | Engine component manufacturing, gear cutting. | Prolonged tool life, reduced heat buildup. |
Medical | Surgical instrument production. | Superior finish and contamination control. |
Oil & Gas | Deep hole drilling, threading. | Exceptional performance in extreme conditions. |
General Machining | High-speed drilling and milling. | Cost-effective, efficient cooling. |
Production Process Flow of Helical Coolant Holes Carbide Rods
The manufacturing of these carbide rods involves multiple precise steps to ensure superior quality. Here’s a detailed flowchart-style breakdown:
- Powder Preparation:
Raw materials (WC, Co, additives) are mixed into fine powder. - Pressing:
The mixed powder is compressed into rod-shaped billets. - Drilling Coolant Holes:
CNC machines create helical coolant channels. - Sintering:
Billets undergo sintering at high temperatures to bond materials. - Grinding & Polishing:
Rods are ground to desired dimensions and polished for smooth surfaces. - Coating:
Optional coatings are applied for enhanced performance.
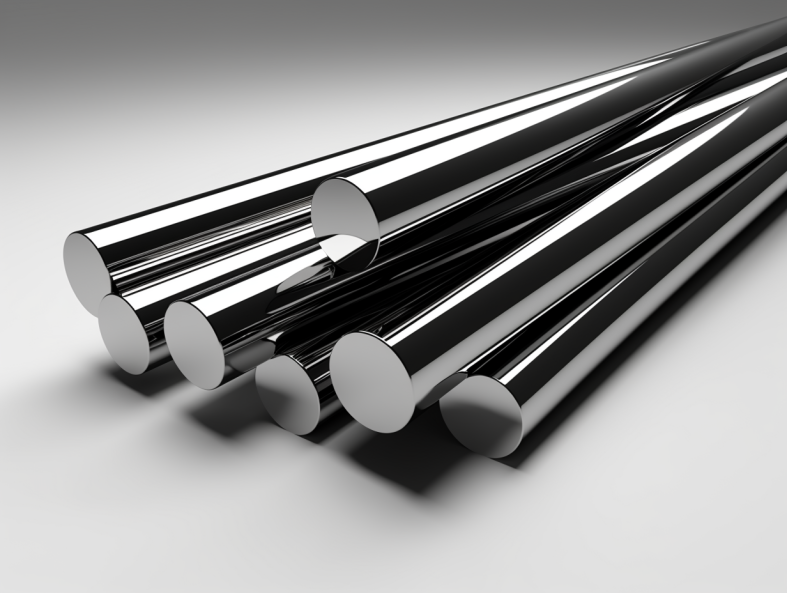
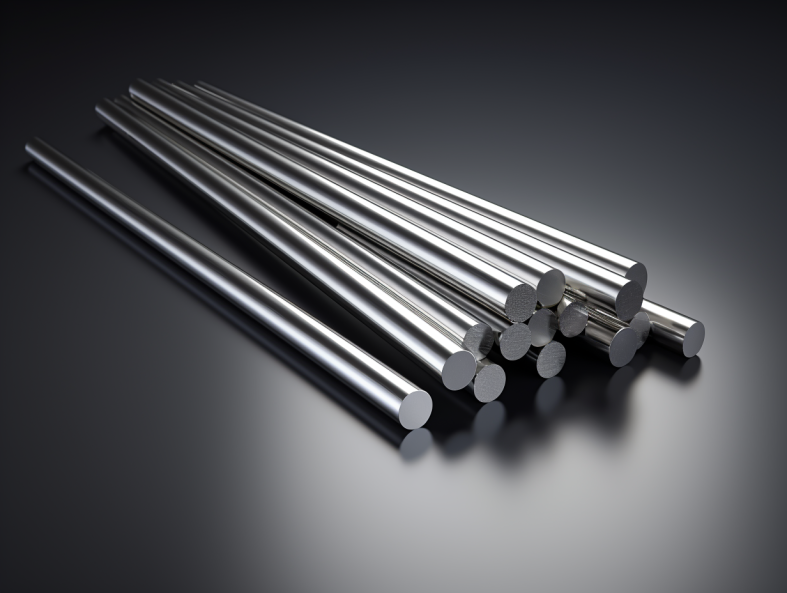
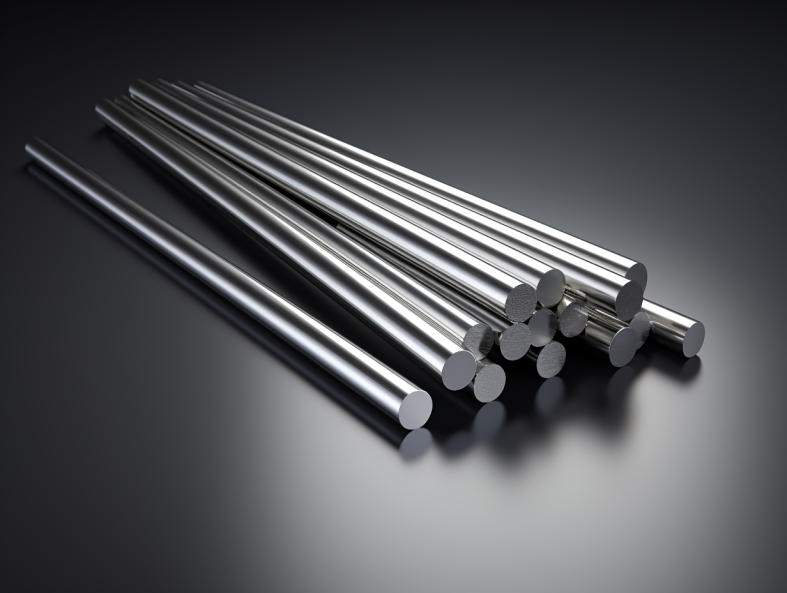
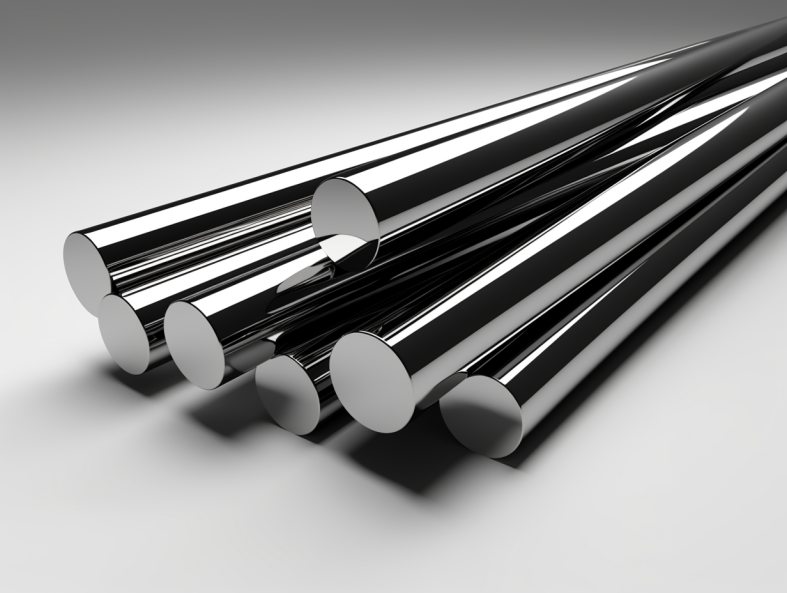
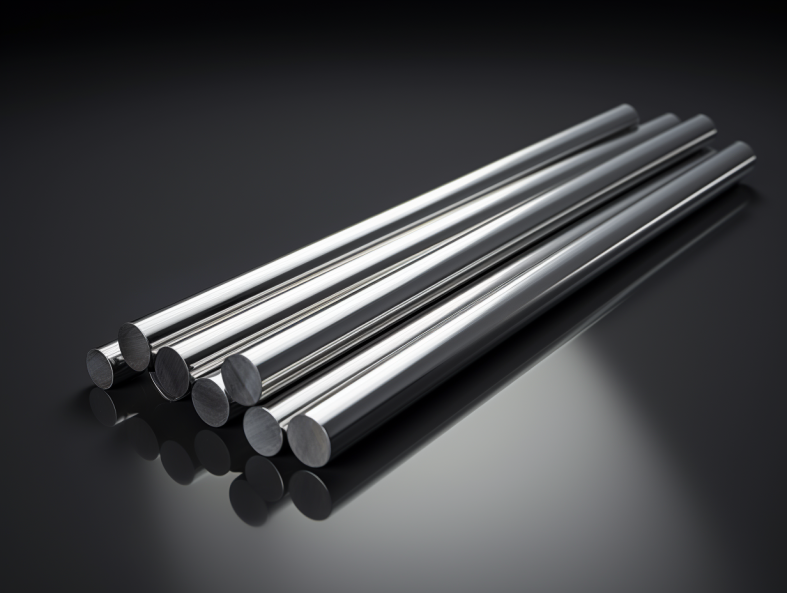
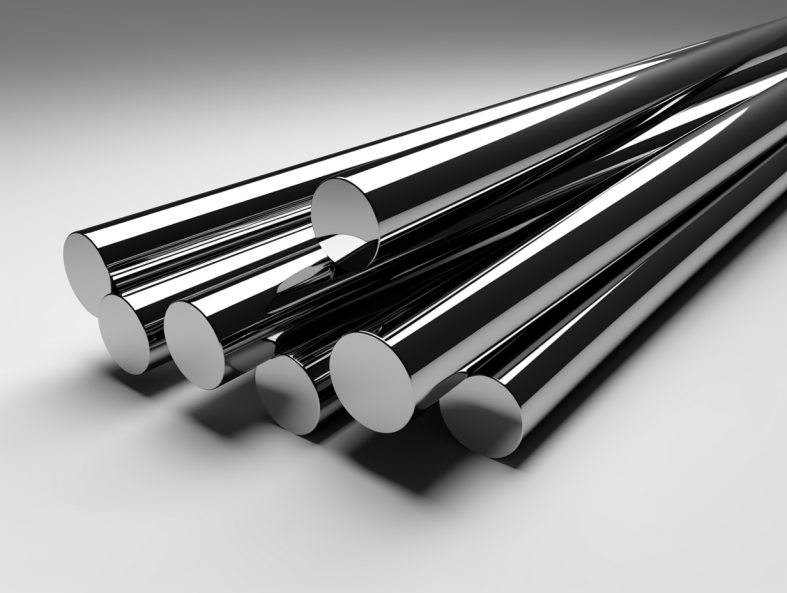
Material Properties of Helical Coolant Holes Carbide Rods
Property | Value | Benefit |
---|---|---|
Density | 14.5-15.5 g/cm³ | High mass ensures stability. |
Hardness | 88-94 HRA | Excellent resistance to wear. |
Transverse Strength | 3000-4000 MPa | Withstands heavy loads and impacts. |
Thermal Conductivity | 80-100 W/m·K | Effective heat dissipation. |
Specifications and Sizes
Helical coolant holes carbide rods come in various sizes and standards to meet specific application requirements.
Parameter | Range |
---|---|
Diameter | 3mm to 30mm |
Length | 50mm to 330mm |
Helical Angle | 30° to 60° |
Coolant Hole Diameter | 0.8mm to 5mm |
Suppliers and Pricing
Supplier Name | Location | Price Range (per unit) | Lead Time |
---|---|---|---|
XY Precision Tools | China | $30 – $50 | 2 weeks |
Global Carbide Inc. | USA | $35 – $60 | 3 weeks |
Innovative Machining | Germany | $40 – $70 | 1 month |
How to Select Helical Coolant Holes Carbide Rods
Choosing the right helical coolant holes carbide rod can be tricky. Consider the following:
Criteria | What to Look For |
---|---|
Application | Match the rod to your machining needs (e.g., drilling, milling). |
Number of Coolant Holes | More holes for higher-speed machining. |
Coating | Use coated rods for extreme wear conditions. |
Budget | Compare pricing across suppliers. |
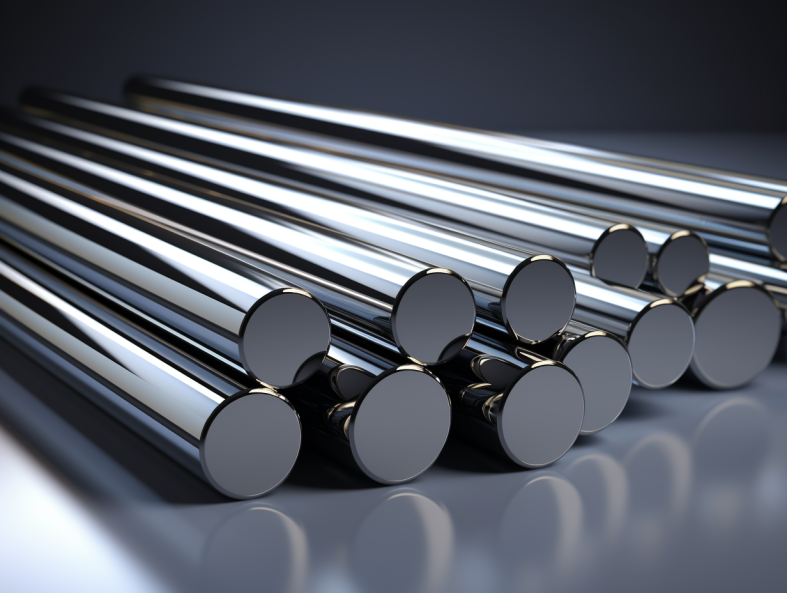
Advantages and Limitations
Advantages | Limitations |
---|---|
Excellent cooling and heat dissipation. | Higher cost compared to straight rods. |
Prolonged tool life. | Limited sizes for niche applications. |
High machining precision. | Requires specific coatings for some tasks. |
FAQs
Question | Answer |
---|---|
What are helical coolant holes for? | They ensure efficient cooling during machining, preventing heat buildup. |
Can these rods be coated? | Yes, with TiAlN, DLC, and other coatings for added durability. |
Are they reusable? | No, they are consumable cutting tools. |
Which industries use these rods most? | Aerospace, automotive, medical, and oil & gas industries. |