Carbide plates are essential components in a variety of industries, including manufacturing, mining, and metalworking. Known for their exceptional hardness, wear resistance, and durability, carbide plates are the go-to solution for applications requiring strength and longevity. But what makes them so special? Let’s break down everything you need to know about carbide plates, from their composition to their applications and even how to select the right one for your needs.
What is a Carbide Plate?
Carbide plates, also known as tungsten carbide plates, are made from a composite material primarily consisting of tungsten carbide (WC) and a metallic binder, typically cobalt or nickel. These plates boast incredible properties, including extreme hardness and high wear resistance, making them ideal for heavy-duty applications.
Think of a carbide plate as a shield that stands up to the harshest conditions—whether it’s high heat, intense friction, or corrosive environments.
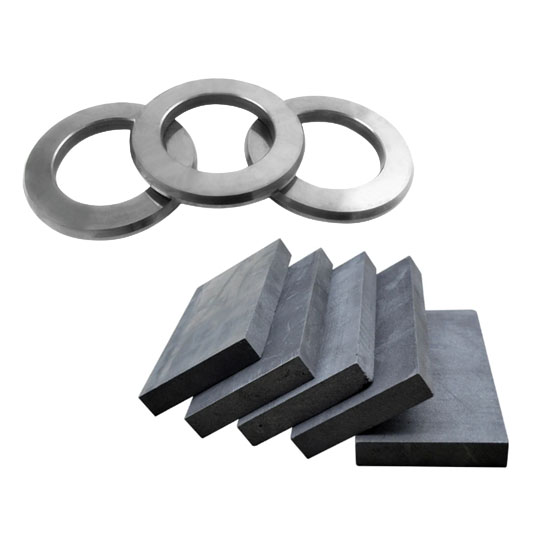
Types of Carbide Plates
Here’s a detailed table showcasing the different types of carbide plates based on their composition, intended application, and unique properties.
Type of Carbide Plate | Binder Material | Hardness (HRA) | Key Features | Applications |
---|---|---|---|---|
YG6 | Cobalt | 90 | Excellent wear resistance, moderate toughness | Cutting tools, wear parts |
YG8 | Cobalt | 89 | Higher toughness than YG6, good wear resistance | Mining tools, punches |
YG15 | Cobalt | 87 | High toughness, impact resistance | Drilling tools, heavy-duty dies |
YG20 | Cobalt | 85 | Superior strength, reduced wear resistance | Rock drilling, coal mining |
YT5 | Titanium | 91 | Outstanding heat resistance | High-speed machining |
YW1 | Nickel-Cobalt | 92 | Multi-purpose, corrosion resistance | Aerospace applications, cutting tools |
YG10X | Cobalt | 91.5 | High wear resistance, less toughness | Precision cutting, woodworking tools |
YS2T | Cobalt | 92.5 | Excellent toughness, anti-chipping | High-speed drills, carbide inserts |
ZP35 | Cobalt | 86 | Balanced hardness and toughness | Wear parts, stamping dies |
H10F | Nickel | 92 | Corrosion resistance, ultra-fine grain | Medical tools, chemical processing |
Raw Materials and Composition of Carbide Plates
Main Ingredients
- Tungsten Carbide (WC): This is the star ingredient. Known for its unparalleled hardness (second only to diamond), tungsten carbide forms the base of these plates.
- Binders: Common binders include:
- Cobalt: Offers toughness and impact resistance.
- Nickel: Adds corrosion resistance, especially for applications in chemical environments.
- Grain Size: The finer the grain, the harder and more wear-resistant the plate.
Detailed Composition
Material | Percentage (%) | Function |
---|---|---|
Tungsten Carbide | 85-95 | Provides hardness and wear resistance |
Cobalt/Nickel | 5-15 | Acts as a binder, offering toughness |
Additives | <1 | Enhances specific properties like corrosion resistance |
Applications of Carbide Plates
Carbide plates are incredibly versatile, finding use across industries. Here’s a breakdown of their applications:
Application | Industry | Details |
---|---|---|
Cutting Tools | Metalworking | Used for making saw blades, knives, and drills. |
Wear Parts | Mining | Ideal for rock crushing and drilling applications. |
Stamping Dies | Manufacturing | Ensure precision in heavy-duty stamping tasks. |
Heat-Resistant Components | Aerospace | Perform well under high temperatures. |
Corrosion-Resistant Tools | Chemical Processing | Withstand harsh chemical environments. |
Precision Machinery | Automotive | Used in machining high-precision components. |
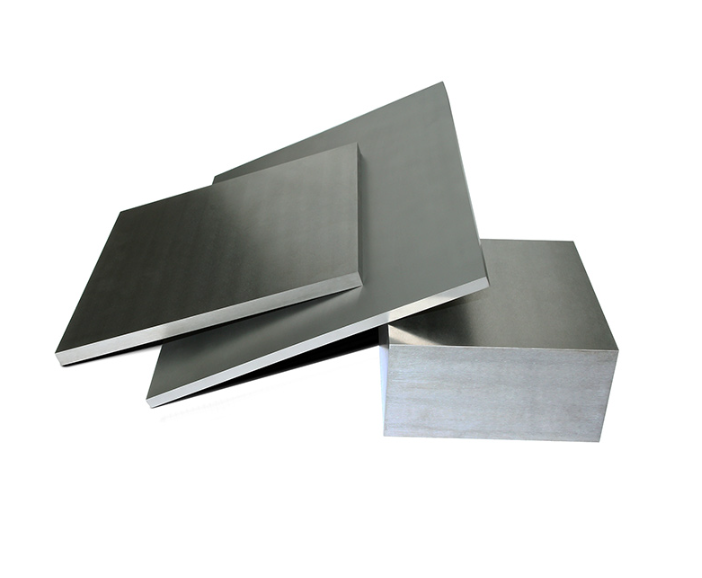
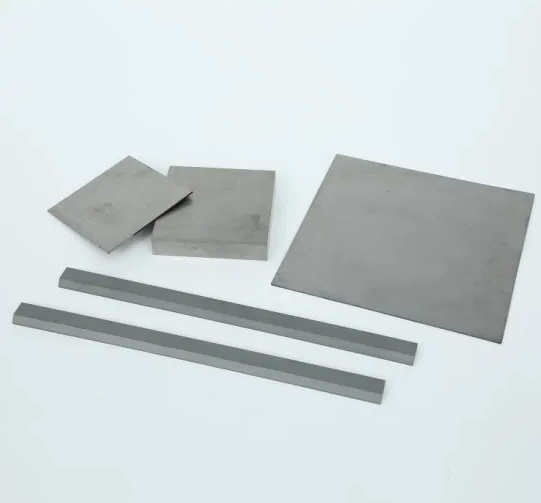
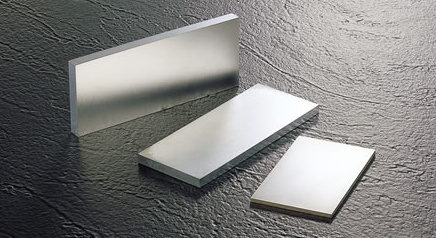
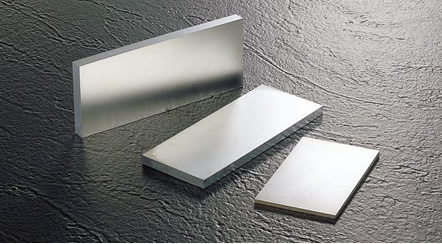
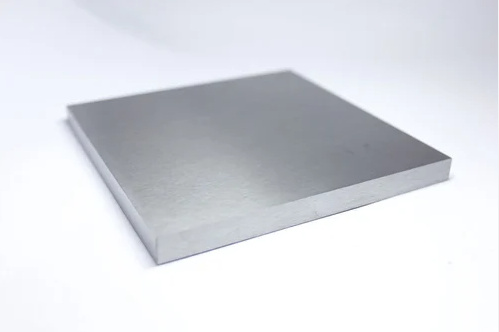
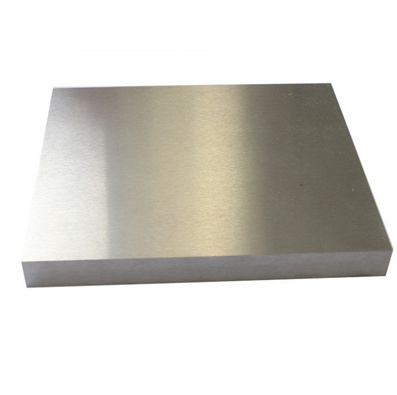
Production Process Flow of Carbide Plates
Ever wondered how carbide plates are made? Here’s the simplified production process:
- Powder Preparation:
Tungsten carbide powder is mixed with binders (like cobalt) to create a uniform mixture. - Pressing:
The mixture is pressed into the desired shape under high pressure. - Sintering:
The pressed plate is heated at extremely high temperatures in a sintering furnace. This fuses the particles and increases the material’s density. - Finishing:
The plate is ground and polished to meet precise specifications. - Quality Control:
Every plate undergoes rigorous testing to ensure it meets hardness, toughness, and wear-resistance standards.
Material Properties of Carbide Plates
Property | Range | Impact on Performance |
---|---|---|
Hardness (HRA) | 85-93 | Determines resistance to wear and abrasion. |
Density (g/cm³) | 14.5-15.5 | Higher density ensures better performance. |
Toughness (MPa) | 2000-3000 | Higher toughness prevents cracking. |
Thermal Conductivity (W/mK) | 50-120 | High thermal conductivity allows better heat dissipation. |
Specifications, Sizes, Shapes, and Standards
Carbide plates come in various sizes and shapes to cater to specific applications.
Specification | Size Range | Shape | Standards |
---|---|---|---|
Thin Plates | 1-5 mm | Rectangular, Square | ISO 9001, ANSI |
Medium Plates | 5-20 mm | Rectangular, Circular | DIN, ASTM |
Thick Plates | >20 mm | Customizable | JIS, GB |
Suppliers and Pricing Information
Supplier Name | Location | Price Range (USD) | Specialty |
---|---|---|---|
Kennametal | Global | 50-200 per plate | High-quality industrial plates |
Sandvik | Sweden | 70-250 per plate | Precision cutting tools |
Zhuzhou Cemented Carbide | China | 30-150 per plate | Cost-effective solutions |
Mitsubishi Materials | Japan | 100-300 per plate | Heat-resistant applications |
How to Select the Right Carbide Plate
Selecting the right carbide plate is like choosing the right armor for your application. Here’s a comparison table to help:
Criterion | Option A: YG6 | Option B: YG15 | Best For |
---|---|---|---|
Wear Resistance | High | Moderate | YG6 for cutting tools. |
Toughness | Moderate | High | YG15 for drilling applications. |
Corrosion Resistance | Low | Moderate | YG15 for corrosive environments. |
Price | Affordable | Premium | YG6 for budget-friendly options. |
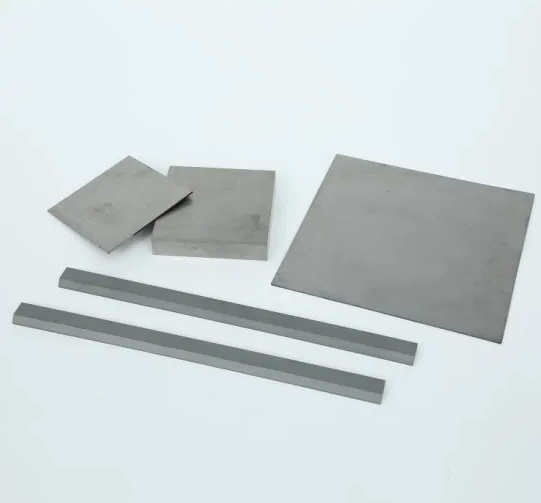
Advantages and Limitations of Carbide Plates
Advantages | Limitations |
---|---|
Exceptional hardness and wear resistance | Brittle under extreme impact |
High heat and corrosion resistance | Higher cost compared to steel alternatives |
Long lifespan reduces replacement frequency | Requires precision machining for customization |
FAQs
Question | Answer |
---|---|
What is the typical lifespan of a carbide plate? | Depending on use, carbide plates can last up to 5 times longer than steel alternatives. |
Can carbide plates be recycled? | Yes, carbide plates are 100% recyclable. |
Are carbide plates expensive? | While costlier upfront, their durability often makes them more economical in the long run. |
What industries benefit most from carbide plates? | Mining, manufacturing, and aerospace heavily rely on carbide plates for their performance. |