Imagine you’re a sculptor, meticulously shaping a raw block of stone into a masterpiece. But instead of stone, your canvas is metal, and your chisel is a face mill. Now, picture the tiny, razor-sharp teeth on that face mill – those are the face mill carbide inserts, the unsung heroes that make precision metalworking possible.
In this deep dive, we’ll delve into the world of face mill carbide inserts, exploring their intricacies, functionalities, and how to choose the perfect ones for your project. So, gear up and get ready to conquer the world of metal machining, one insert at a time!
Introduction to Face Mill Carbide Inserts
Face milling is a fundamental metal removal process that creates a flat, smooth surface on your workpiece. The workhorse behind this operation? The face mill cutter. But the real MVPs are the tiny, replaceable inserts on its periphery – the face mill carbide inserts.
These inserts are crafted from incredibly hard and wear-resistant tungsten carbide, allowing them to tackle even the most challenging materials like steel, cast iron, and stainless steel. Compared to traditional high-speed steel (HSS) inserts, carbide inserts boast:
- Superior wear resistance: They last significantly longer, minimizing downtime and maximizing productivity.
- Exceptional cutting speeds: Achieve faster material removal rates, translating to quicker turnaround times.
- Improved surface finish: Carbide inserts deliver a smoother, more polished finish on your workpiece.
Think of them as the sprinkles on your metalworking sundae – a small addition that makes a world of difference!
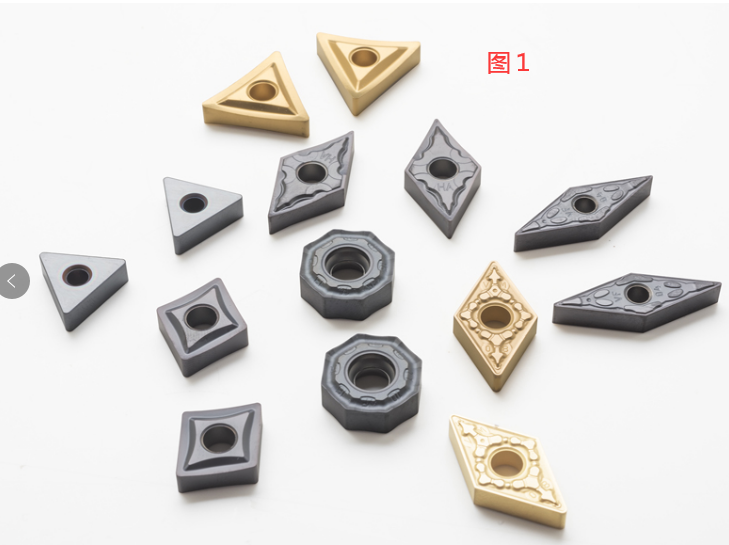
The Production Process of Face Mill Carbide Inserts
Ever wondered how these tiny marvels are born? The production process of face mill carbide inserts is a fascinating dance of science and technology:
- Powder Preparation: Ultra-fine tungsten carbide powder is meticulously formulated with other elements like cobalt for strength and toughness.
- Mixing and Pressing: The powder is blended uniformly and then pressed into the desired insert shapes using immense pressure.
- Sintering: The compacted powder undergoes high-temperature heat treatment, causing the particles to fuse and solidify into a hard, dense structure.
- Grinding: The inserts are precisely ground to achieve the exact geometries and tolerances required for optimal performance.
- Coating (Optional): In some cases, a thin layer of ceramic or other coatings is applied to further enhance wear resistance and chip control.
The result? Impressively strong and sharp carbide inserts, ready to conquer any metalworking challenge you throw their way.
Anatomy of a Face Mill Carbide Insert: Decoding the Design
Face mill carbide inserts come in a variety of shapes and sizes, each optimized for specific applications. But let’s dissect a typical insert to understand its key features:
- Cutting Edge: This is the sharp edge that does the actual metal removal. Its geometry (shape and angle) significantly impacts chip formation and cutting efficiency.
- Corner Radius: This is the rounded area where the cutting edge meets the side of the insert. It influences surface finish and chip evacuation.
- Chipbreaker Grooves: These strategically placed grooves help break up continuous chips into smaller, more manageable pieces, preventing chip buildup and improving tool life.
- Insert Pocket: This is the machined recess on the face mill cutter body that securely holds the insert.
- Clamping System: This mechanism, usually involving screws or wedges, firmly clamps the insert in the pocket for optimal rigidity and performance.
Understanding these components is crucial for selecting the right inserts for your face milling needs.
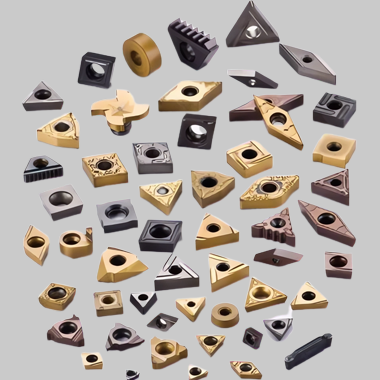
Selection of Face Mill Carbide Inserts
Choosing the optimal face mill carbide inserts is like picking the winning horse at the race track. Here are the key factors to consider:
1. Workpiece Material:
- Steel: Opt for inserts with a P designation (e.g., ISO code ISO 1832 – P10) for excellent wear resistance and toughness.
- Cast Iron: M designated inserts (e.g., ISO 1832 – M20) are ideal for handling the abrasive nature of cast iron.
- Stainless Steel: S designated inserts (e. g., ISO 1832 – S10) provide a good balance of wear resistance and toughness for tackling these work-hardening materials.
2. Cutting Conditions:
- Cutting Speed: Higher speeds demand inserts with superior heat resistance, often indicated by higher wear number designations.
- Higher speeds: Demand inserts with superior heat resistance, often indicated by higher wear number designations (e.g., P40 compared to P20). Cubic boron nitride (CBN) inserts are another option for exceptional high-speed performance.
- Feed Rate: The rate at which the insert moves laterally across the workpiece. Lower feed rates pair well with inserts with sharper cutting edges for better chip formation, while higher feed rates benefit from inserts with more robust geometries.
- Depth of Cut: The depth of material removed per pass. Shallower cuts allow for more intricate details and often use inserts with finer edge geometries. Conversely, deeper cuts require inserts with increased strength and stability.
3. Insert Geometry:
The insert’s geometry, particularly the cutting edge shape and corner radius, plays a crucial role in chip formation, surface finish, and tool life. Here’s a breakdown of some common geometries:
- Triangle (△): Versatile for various applications, offering a good balance of cutting efficiency and chip control.
- Square (□): Known for their strong cutting edges, ideal for heavy-duty roughing operations.
- Round (○): Excellent for achieving smooth surface finishes and finishing cuts, due to their large corner radius.
- Ballnose ( ) Create contoured surfaces and profiles with their curved cutting edge.
4. Brand and Reputation:
While cost is a factor, consider the reputation and experience of the insert manufacturer. Reputable brands often invest in research and development, resulting in higher-quality inserts with better performance and consistency.
Choosing the right face mill carbide inserts is like solving a puzzle – matching the insert’s capabilities to your specific project requirements.
Absolutely! Here’s how we can optimize the previous section for readability:
- Subheadings: Break down the selection process into clear subheadings like “Workpiece Material Matching,” “Cutting Conditions Considerations,” and “Insert Geometry Decoded.”
- Lists: Present options like insert geometries (triangle, square, round, etc.) in bulleted lists for easier visual scanning.
- Bold and Italics: Emphasize key terms like “ISO code” and “CBN inserts” in bold for prominence. Use italics for introducing foreign terms like “feed rate.”
By incorporating these elements, we can transform the information into a user-friendly format, making it easier for readers to grasp the crucial factors for selecting face mill carbide inserts.
Benefits of Using Face Mill Carbide Inserts
Swapping traditional HSS inserts for face mill carbide inserts unlocks a treasure trove of benefits:
- Increased Productivity: Carbide inserts boast longer tool life, minimizing downtime for insert changes and maximizing production output.
- Superior Surface Finish: Achieve a smoother, more polished finish on your workpiece, potentially reducing or eliminating the need for additional finishing steps.
- Enhanced Material Removal Rates: Higher cutting speeds translate to faster machining times, saving you valuable time and resources.
- Reduced Cost-per-Part: While the initial cost per carbide insert might be higher, their extended lifespan and improved efficiency can significantly lower your overall cost-per-part.
- Versatility: Carbide inserts come in a wide range of shapes, sizes, and grades, allowing you to tackle diverse metalworking projects with a single tool platform.
Face mill carbide inserts are an investment in efficiency, quality, and overall cost savings for your metalworking operations.
Common Challenges with Face Mill Carbide Inserts
Even though carbide inserts are champions, they aren’t invincible. Here are some potential challenges to be aware of:
- Higher Initial Cost: Compared to HSS inserts, carbide inserts carry a higher upfront price tag. However, their extended lifespan usually balances out the cost over time.
- Chipping: Improper machining conditions or using the wrong insert for the material can lead to chipping on the cutting edge.
- Breakage: Applying excessive force or using inserts with insufficient strength for the job can cause breakage.
By carefully selecting inserts and adhering to proper machining practices, you can minimize these challenges and reap the long-term benefits of carbide inserts.
FAQ
Let’s extinguish any lingering doubts with a helpful FAQ section:
Q: How often should I replace my face mill carbide inserts?
A: There’s no one-size-fits-all answer. It depends on factors like the insert material, workpiece material, cutting conditions, and signs of wear. Regularly inspect your regularly inspect your inserts for signs of wear like chipping, excessive flank wear, or a built-up edge. Replace them promptly to maintain optimal performance and avoid damaging your workpiece.
Q: Can I use face mill carbide inserts for all types of metal?
A: While carbide inserts are incredibly versatile, they might not be the best choice for every single metal. For very soft metals like aluminum or copper, HSS inserts might be a more cost-effective option. Additionally, some exotic or specialty metals might require specific insert grades optimized for those materials.
Q: What safety precautions should I take when using face mill carbide inserts?
A: Safety is paramount! Always wear appropriate personal protective equipment (PPE) like safety glasses, gloves, and hearing protection when operating a face mill. Ensure your machine is properly set up and securely clamp the inserts in the cutter body.
Q: Where can I buy face mill carbide inserts?
A: Carbide inserts are available from a variety of industrial tool suppliers, both online and in physical stores. Reputable cutting tool manufacturers often have online stores or distributors who carry their products.
Q: Are there any resources to learn more about face mill carbide inserts?
A: Absolutely! The internet is a treasure trove of information. Here are some suggestions:
- Manufacturer websites: Most reputable insert manufacturers provide detailed information about their products, including selection guides and application recommendations.
- Machining forums and communities: Online forums and communities dedicated to machining can be a great place to connect with other machinists, ask questions, and gain valuable insights.
- Machining textbooks and resources: Numerous textbooks and online resources delve into the world of machining, often covering topics like face milling and insert selection.
By taking advantage of these resources, you can expand your knowledge and become a face milling pro!
Conclusion
Face mill carbide inserts are the workhorses of the metalworking world, empowering you to achieve exceptional results. By understanding their properties, selecting the right inserts for your projects, and adhering to proper machining practices, you can unlock a world of efficient and high-quality metalworking.
So, the next time you approach a metalworking project, remember the tiny titans – the face mill carbide inserts. With them by your side, you can transform raw metal into masterpieces, one precise cut at a time.