Imagine you’re a sculptor, meticulously shaping a piece of metal into a work of art. But instead of a chisel and hammer, you wield the incredible power and precision of a CNC lathe. Threading intricate features onto that metal is where carbide inserts come in, acting as the tiny, high-performance chisels that define those threads.
This guide delves into the world of threading carbide inserts, exploring their creation, selection, and application. By the end, you’ll be equipped to choose the perfect insert for your next threading project, ensuring clean, accurate results.
Introduction to Threading Carbide Inserts
Carbide inserts are like tiny, super-hard teeth on a rotating tool called a threading insert holder. These inserts are crafted from tungsten carbide, a phenomenal material known for its exceptional wear resistance and ability to handle high temperatures. This translates to sharp, long-lasting cutting edges that can tackle even the toughest materials.
But why use inserts instead of a solid tool? Here’s the beauty:
- Cost-effective: Inserts are replaceable, allowing you to swap out just the worn-out tip rather than discarding the entire tool. This translates to significant cost savings in the long run.
- Versatility: A wide variety of insert geometries are available, catering to different thread types, sizes, and materials. You can essentially have a dedicated “chisel” for each specific threading job.
- Precision: Carbide inserts hold their sharp edge exceptionally well, ensuring clean and accurate thread profiles. This is crucial for applications where tight tolerances are essential.
So, next time you see a CNC lathe churning out perfectly threaded components, remember the tiny carbide insert heroes working tirelessly behind the scenes.
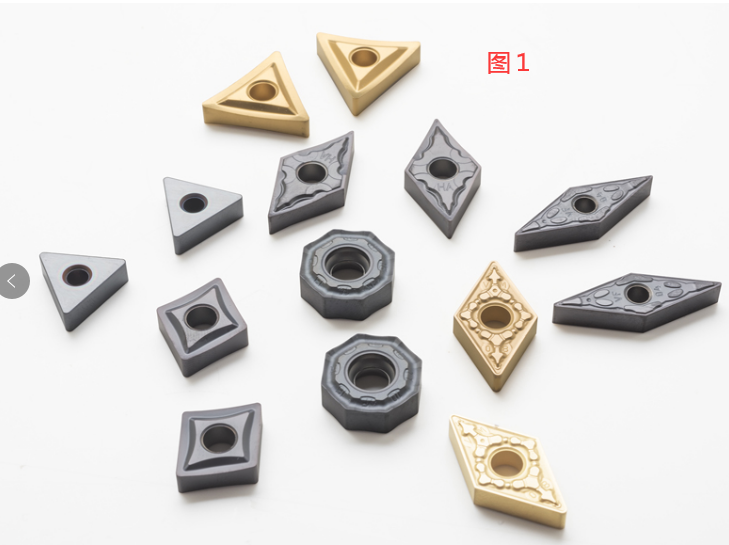
The Production Process of Threading Carbide Inserts
These little champions of metal shaping are born from a fascinating industrial process:
- Powder Preparation: The raw materials, primarily tungsten carbide powder, are meticulously blended with other elements like cobalt for binding.
- Pressing and Shaping: The mixture is compressed under immense pressure into the desired insert geometry using specialized molds.
- Sintering: The compacted shapes are subjected to high temperatures in a controlled atmosphere, causing the particles to fuse together and form a solid, yet highly porous, structure.
- Hipping (Hot Isostatic Pressing): The inserts undergo a high-pressure, high-temperature treatment in a sealed chamber. This eliminates internal voids and strengthens the carbide structure.
- Grinding: The insert’s cutting edges are precisely ground to the exact geometry required for the specific thread profile.
- Coating (Optional): A thin layer of a specialized coating, like titanium nitride (TiN), might be applied to further enhance wear resistance and improve chip flow.
- Quality Control: Finally, the finished inserts undergo rigorous inspections to ensure they meet strict dimensional and performance standards.
This meticulous process ensures that each carbide insert is a tiny masterpiece of engineering, ready to tackle demanding threading tasks.
Selection of Threading Carbide Inserts
With a vast array of threading carbide inserts available, selecting the right one can feel overwhelming. But fret not! Here’s a breakdown of key factors to consider:
- Thread Type: The most crucial factor. Are you creating internal or external threads? What thread profile (e.g., metric, UNC, UNF) is required?
- Material to be Threaded: Different materials have varying hardness and machinability characteristics. Choose inserts specifically designed for the material you’re working with (e. g., steel, aluminum, stainless steel).
- Insert Geometry: The insert’s geometry dictates the thread profile it can create. Consider factors like thread angle, flank angle, and chip formation characteristics. Common insert geometries include internal turning (ISO), external turning (NR), and threading (V or W).
- Insert Size: Select an insert size compatible with your threading insert holder and that offers sufficient cutting edge length for the desired thread depth.
- Coating (Optional): Coatings can enhance performance. For example, TiN coatings excel in high-speed machining applications.
- Cutting Grade: This refers to the carbide insert’s material composition and its suitability for various machining conditions. Higher cutting grades offer better wear resistance but might come at a slightly higher cost. Consider factors like workload, material hardness, and desired tool life.
- Expert Opinion: Machinist John Miller, with over 20 years of experience, emphasizes, “The right insert grade can make all the difference in terms of productivity and tool life. Don’t be afraid to consult with machining experts or refer to manufacturer recommendations to find the optimal grade for your application.”
- Manufacturer Reputation: Consider reputable brands known for their quality and consistency in insert production. While cost can be a factor, opting for reliable inserts ensures predictable performance and minimizes the risk of premature tool failure.
- Subjective Commentary: The visual aesthetics of threading carbide inserts might seem insignificant, but the clean, sharp lines and uniform coating on a high-quality insert can instill confidence in its capabilities. It’s a subtle indicator of precision engineering.
Additionally, consider these factors:
- Coolant Compatibility: Some inserts are designed for use with specific coolants to optimize chip removal and minimize heat generation.
- Environmental Regulations: In some cases, environmentally friendly coatings or insert materials might be preferred to comply with regulations.
By carefully evaluating these factors, you can select threading carbide inserts that perfectly match your project requirements. Remember, the right insert ensures:
- Clean and accurate threads: Precisely formed threads that meet dimensional specifications.
- Efficient machining: Faster cutting speeds and longer tool life, leading to increased productivity.
- Cost-effectiveness: Reduced insert replacements and improved overall machining efficiency translate to cost savings.
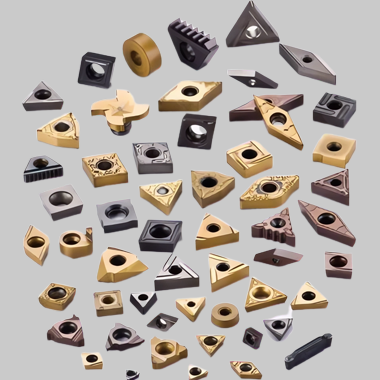
Applications of Threading Carbide Inserts
Threading carbide inserts are the go-to choice for various metalworking applications, but their potential extends beyond basic thread creation:
- High-Precision Threading: For critical applications demanding exceptional accuracy, carbide inserts shine. Their ability to hold a sharp edge translates to clean, precise threads that meet tight tolerances.
- Mass Production: The durability and wear resistance of carbide inserts make them ideal for high-volume production environments. They can withstand long hours of continuous operation without compromising thread quality.
- Difficult-to-Machining Materials: Certain materials, like stainless steel or high-temperature alloys, pose challenges for traditional cutting tools. Carbide inserts, with their exceptional hardness, can tackle these materials effectively.
- Specialized Threading: Need to create non-standard or exotic thread profiles? Carbide inserts can be custom-ground to meet specific requirements, offering unmatched versatility.
Customer Satisfaction in Action: Many machinists swear by the reliability and performance of threading carbide inserts. Online reviews consistently praise their ability to produce clean threads, extend tool life, and boost overall machining efficiency.
Maintaining Threading Carbide Inserts
Just like any cutting tool, proper care extends the lifespan and optimizes the performance of threading carbide inserts:
- Proper Storage: Store inserts in their designated holders or protective cases to prevent chipping or damage.
- Cleaning: Regularly clean the inserts to remove built-up chips and debris that can affect cutting performance.
- Inspection: Before each use, inspect the inserts for signs of wear or damage. Discard any chipped, cracked, or excessively worn inserts.
- Following Manufacturer Recommendations: Refer to the manufacturer’s guidelines for proper use, handling, and storage of the specific inserts you’re using.
By following these simple maintenance practices, you can ensure that your threading carbide inserts continue to deliver exceptional results for a longer period.
Common Challenges and Troubleshooting
Even with the best inserts, occasional challenges might arise during threading operations. Here are some common issues and troubleshooting tips:
- Poor Thread Finish: This could indicate dull inserts, improper cutting parameters (speed, feed), or inadequate coolant application. Sharpen or replace inserts, adjust cutting parameters, or optimize coolant flow.
- Dimensional Inaccuracy: Double-check your insert selection for compatibility with the desired thread profile. Verify that the toolholder is properly mounted and aligned on the lathe.
- Chipped Inserts: This signifies excessive cutting forces. Reduce cutting speed, feed rate, or depth of cut. Ensure proper insert selection for the material being machined.
Remember: If you encounter persistent issues, consult with a machining expert or the insert manufacturer for specific troubleshooting guidance.
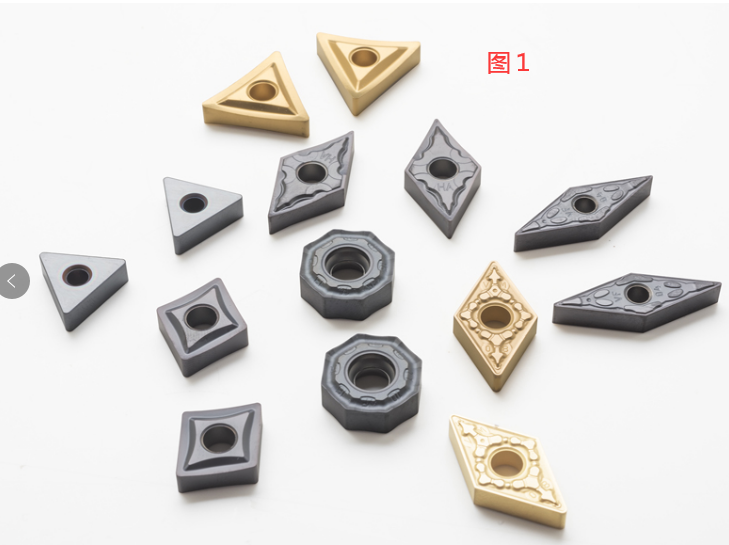
FAQ
Q: Are threading carbide inserts difficult to use?
A: Threading carbide inserts themselves are not inherently difficult to use. However, selecting the right insert for the specific application and ensuring proper setup on the CNC lathe require a basic understanding of threading parameters and insert characteristics. Consulting with a machining expert or referring to manufacturer recommendations can be helpful, especially for beginners.
Q: How long do threading carbide inserts last?
A: The lifespan of a threading carbide insert depends on various factors, including the insert grade, material being machined, cutting parameters employed, and maintenance practices. Generally, carbide inserts offer significantly longer tool life compared to traditional high-speed steel tools. With proper care, a single insert can create a substantial number of threads before requiring replacement.
Q: Can I re-sharpen threading carbide inserts?
A: In most cases, no. Threading carbide inserts are designed for single use and are typically discarded once they become dull or excessively worn. However, some manufacturers offer specialized re-grinding services for specific insert geometries. This is generally not recommended for everyday use due to the specialized equipment and expertise required.
Q: Are there any alternatives to threading carbide inserts?
A: Yes, a few alternatives exist:
- High-Speed Steel (HSS) Threading Tools: These are less expensive than carbide inserts but wear out quicker and might not be suitable for demanding applications or high-volume production.
- Solid Threaded Tools: These offer a simple solution but lack the versatility of inserts and require replacement for different thread sizes or profiles.
Ultimately, threading carbide inserts provide the best balance of performance, cost-effectiveness, and versatility for most thread machining applications.
Q: Where can I buy threading carbide inserts?
A: Threading carbide inserts are available from various sources, including:
- Industrial Tooling Suppliers: These companies offer a wide selection of inserts from different manufacturers and can provide expert advice on choosing the right inserts for your needs.
- Online Retailers: Several online retailers offer threading carbide inserts. However, it’s crucial to ensure you’re purchasing from a reputable source that provides accurate specifications and quality products.
- Machining Equipment Manufacturers: Many CNC lathe manufacturers also sell compatible threading carbide inserts specifically designed for their machines.