Wood lathes utilize removable carbide cutting inserts to efficiently shape, turn and finish woodwork pieces. This article provides details on wood lathe carbide inserts geometries, grades, coatings and standards along with comparative analysis of brazed vs indexable options, suppliers listing, cutting parameters and insert optimization guidelines to boost wood lathe productivity.
Overview of wood lathe carbide inserts
Carbide inserts for wood turning feature specific cutting edge profiles and standardized shapes engineered for mounting on tool holders attached to the lathe. Sharpened through grinding or by CVD/PVD coatings, these remove material efficiently generating continuous wood chips rather than dust.
Benefits of Using Carbide Inserts
- Up to 10X longer tool life versus HSS turning tools
- Higher cutting speeds and lower temperatures
- Improved finish quality with reduced sanding needs
- Consistent profiles from indexable inserts vs manual sharpening
- Brazed tips add stiffness minimizing vibration/chatter
Proper insert grade, geometry, clearance angles and feed rates boost machining performance on varying wood species.
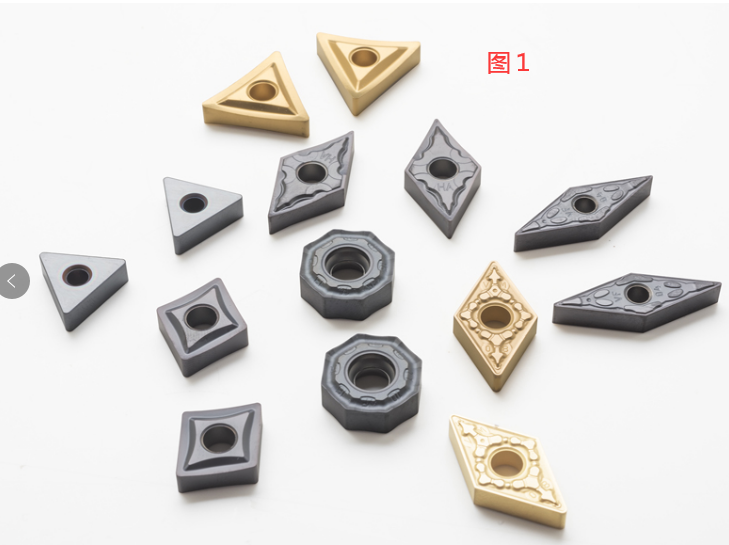
Insert Designs
Indexable Insert Styles
Indexable insert tooling relies on interchangeable carbide tips with defined cutting profiles mounted on standardized tool holders. Common options include:
Type | Shape Options | Features |
---|---|---|
SNMG | Square, neutral rake | General purpose roughing/finishing |
DNMG | 55° rhombus insert | Heavy roughing, mini profiler |
CNMG | 80° diamond shape | Finishing, profiling, bead cuts |
VNMG | 35° diamond shape | Beading, V-carving, grooving |
TNMG | Triangle insert, neutral rake | Deep hollowing on bowl gouges |
These cover varying edge preparations and chipbreakers to suit specific wood species and operations. Insert seats also impact approach angle, visibility and clearance.
Brazed Tip Designs
Here carbide inserts are brazed onto custom tool shanks to provide one-piece solid tools eliminating separate holders. Common types include:
Name | Composition | Purpose |
---|---|---|
Easy Wood Tools | Solid carbide brazed tip + steel shank | General wood turning ops |
Carter & Son Toolworks | Solid carbide brazed on steel | Robust roughing, detailing |
Hunter Osprey | Solid carbide brazed on steel | Smooth finishing cuts |
Custom ground brazed | User defined carbide grades/geometries | Specialized cuts |
These are sharpenable but need bonding repairs after repeated regrinds. Brazed tools aim for vibration resistance given their unitary construct versus separate holder plus inserts.
Wood Turning Insert Grades
Carbide insert hardness, strength, wear resistance and toughness are tailored to woodturning needs via optimized composition, grain size and binder content.
Base Grades
Grade | Hardness Range | Key Features |
---|---|---|
C2 & C4 | 86-88 HRA | High wear resistance for abrasive exotic woods, MDF |
C6-C8 | 82-86 HRA | Good all-round grades balancing life and toughness |
Coated Grades
Grade | Coating | Benefits |
---|---|---|
CC650 | TiCN | doubles roughing tool life in hardwoods |
CC670 | TiN | Excellent general purpose grade |
CC685 | TiAIN | High lubricity coating for difficult woods |
CC695 | ZrN | Resists abrasive dust buildup |
Toolmakers optimize proprietary compositions and coatings to boost speed, feed rates and finish quality across varying species.
Insert Specifications
Key wood turning insert dimensions and mounting details are governed by ISO standards for consistent performance across global brands.
Indexable Insert Sizes
Dimension | Standard Values |
---|---|
Inscribed Circle | 11, 16, 21, 25 mm |
Thickness | 3.18, 4.76, 6.35 mm |
Hole diameter | Screw sizes M4, M5 |
Hole position | Centered per IC size to fit holders |
Brazed Tip Dimensions
Custom tool makers offer varying carbide tip lengths, widths and cutting profiles brazed to steel shanks sized for common wood lathe spindle bores:
Parameter | Typical Range |
---|---|
Shank diameter | 1/2”, 5/8”, 3/4″ |
Shank length | 6-8 inches |
Carbide tip height | 0.5-1 inch |
Carbide tip width | 0.25-1 inch |
These solid one-piece brazed tools aim for added rigidity and strength over indexable inserts requiring holders.
Cutting Parameters
Optimal speeds, feeds, depths of cut and tool angles minimize cutting forces while maximizing finish quality across workpiece materials.
Feed Rates
Carbide tool feed per revolution values for varying wood species:
Wood Type | Feed Rate (IPR) |
---|---|
Hard woods like oak, maple, hickory | 0.002-0.010″ |
Medium woods like cherry, walnut | 0.010-0.025″ |
Soft woods like pine, cedar, redwood | 0.025-0.050” |
Abrasive exotic woods | 0.002-0.005” |
Cutting Speeds
Higher cutting speeds boost productivity but generate heat affecting finish. Typical ranges:
Material | Speed (RPM) |
---|---|
General purpose roughing | 1600-2400 rpm |
Precision finishing | 800-1600 rpm |
Abrasive/brittle woods | 500-1000 rpm |
DOC and Tool Angles
Parameter | Value | Comments |
---|---|---|
Depth of cut | Up to 0.25″ | Higher DOC raises insert temperatures |
Side cutting edge angle | 8-15° | Higher angles resist dig-in on problem woods |
End/face cutting edge angle | 8-12° | Angles under 8° prone to edge breakdown on abrasive species |
Coolants like spray mist or gels help regulate insert temperature and boost longevity when running at higher speeds and feeds. Custom toolmakers also alter carbide substrate and post-coat treatments to enhance thermal shock resistance.
Suppliers
Leading manufacturers offer optimized woodturning grades across indexable and brazed tipped lines.
Indexable Insert Brands
Company | Grades Offered | Holder Systems |
---|---|---|
Sandvik Coromant | CC670, CC685, CC695 | Coromant Capto, ISO standard |
Iscar | IC, IR, Sumo grades | Iscar Tetra |
Kennametal | Beyond grades | KM quick change |
TaeguTec | XX700 Series | Custom shanks |
Brazed Tip Providers
Company | Tip Styles | Shank Options |
---|---|---|
Easy Wood Tools | Square Scraper, Pointed Detailer | Steel shanks 1/2″, 5/8″ |
Carter Products | Circle Cutter, Cove-D, Curve Router | Steel shanks 5/8″, 3/4″ |
Hunter Tool Systems | Long & Short Barrel | Steel shanks 1/2″, 5/8″, 3/4″ |
Reputable suppliers provide comprehensive technical datasheets on insert grades detailing composition, properties data, cutting guidelines and Holder details with associated set screws, nuts and fastening hardware.
Cost Analysis
Carbide Insert Pricing
Insert Type | Cost per Piece at Small Volumes |
---|---|
Indexable turning inserts | $3-10 per tip |
Brazed solid carbide bars | $50-150 per bar |
Economical indexable inserts help reduce replacement costs over single-piece bars requiring full replacements despite localized edge wear. Large OEM orders fetch bulk discounting up to 60% on batches above 5000 inserts.
Tool Holders Cost
Indexable systems need dedicated holders and associated mounting hardware driving up initial tooling cost:
Holder Type | Price Range |
---|---|
Base holders without quick change | $15-25 per piece |
Quick change modular holders | $35-60 per piece |
Over long production runs, indexable inserts offset these expenses through lower insert unit costs and easier tip changes.
Brazed vs Indexable Tips – Comparative Analysis
Brazed Carbide Tools
Pros | Cons |
---|---|
One piece solid construction adds stiffness | Requires braze repair after 3-5 sharpenings |
Lower cost per tool versus holders plus inserts | Limited cutting profile and diameter options per tool |
Easier to master for beginners | Regrinding alters approach angle losing original geometry |
Provides visibility close to work | Full tool replacement despite localized damage |
Indexable Insert Systems
Pros | Cons |
---|---|
Economic inserts vs full tool cost | Separate holders increase startup costs |
Loose inserts facilitate profiling flexibility | Perceived complexity for beginners |
Designed chipbreakers improve performance | Need maintaining larger insert inventory |
Maintains original geometry after indexing | Additional holders needed for multiple profiles |
While indexable systems imply higher startup costs, easier grade/profile changes and consistent cutting action optimize productivity – key factors for professional shops.
Insert Optimization
Boosting Tool Life
- Choose appropriate insert grade for work material hardness/abrasiveness
- Reduce speeds/feeds when encountering problematic woods
- Use strict SFM/DOC/IPR values from datasheets
- Apply mist cooling when running at higher parameters
- Ensure rigid setups that minimize vibration and chatter
Improving Finish Quality
- Light finishing passes under 0.01” DOC
- Lower spindle RPM between 500 and 1000
- Sharpen inserts via diamond laps when edges show wear
- Upgrade to polished inserts from roughers if needed
- Verify tool alignment to minimize radial runout
Allowing Easy Insert Changes
- Standardize on a quick change holder system
- Use holders with clear numerical indexes
- Maintain spare sets of calibrated holders
- Log change dates/reasons to track insert duty cycles
These measures help boost consistency and productivity with minimal downtime when running indexable inserts across varying turning operations.
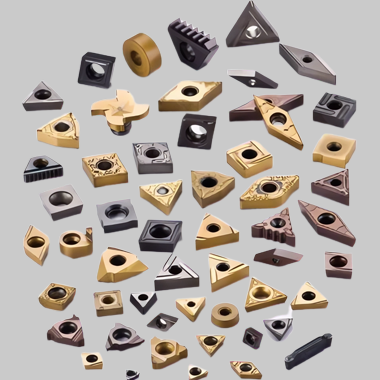
Summary
Wood lathes employ indexable or brazed carbide inserts to achieve high metal removal rates along with excellent finish quality. Proper insert selection and cutting parameters play a key role in optimizing tool life, cycle times and process reliability when working with varying wood species. Leading manufacturers offer dedicated woodturning grades and geometries to balance longevity, cutting forces and temperature management across light roughing, medium duty profiling and aggressive duty bowl hollowing operations.
FAQs
What are the best carbide inserts for woodturning?
Top grades for wood lathes include CC670 TiN coated general purpose inserts along with CC650 TiCN and CC685 TiAIN variants for high abrasion and difficult species. These strike optimal life vs cutting performance.
What information do I need for choosing woodturning inserts?
Main considerations are – type of cuts (roughing vs finishing), workpiece hardness and composition (softwood vs maple vs MDF), desired feed rates and finish quality. These dictate insert shape, geometry, carbide grade and coating.
When should I use brazed vs indexable inserts?
Brazed one-piece bars suit hobbyists given lower initial costs. Production shops running varying profiles prefer indexable inserts for their economic tip changes despite higher startup tooling costs.
How much do replaceable carbide inserts cost?
Indexable carbide tips for wood lathes range from $3 to $15 depending on grade, coating and purchase volumes. Reputable suppliers offer technical advice on appropriate inserts even for small batch trial orders.
What are typical feed rates for turning different woods?
Hard woods allow 0.002-0.010 IPR while softwoods and MDF permit up to 0.025-0.050 IPR. Abrasive exotic species require more conservative 0.002-0.005 IPR feeds with suitable insert grades.
How long should carbide inserts last on wood?
With optimal speeds, feeds and rigidity, advanced grades like CC670 coating permit 30-60 minutes edge life on tough hardwoods while CC650 versions double roughing life to over 120 minutes before visible wear or edge breakdown.
What are the benefits of using carbide over HSS?
Carbide inserts boost lathe productivity 2-10X over HSS tools with higher feeds/speeds, lower temperatures plus consistency from indexable inserts. Rigid holders and defined cutting angles also minimize vibration challenges.