Cemented carbide saw tips, also known as tungsten carbide tipped saw blades, are cutting tools used on saws to cut hard materials. They consist of tough tungsten carbide pieces that are brazed to the teeth of saw blades to provide a hard, long-lasting cutting edge.
Overview of cemented carbide saw tips
Cemented carbide tipped saw blades are designed for exceptional performance when cutting hard materials like stone, masonry, concrete, tile, steel, and more. The ultra-hard tungsten carbide tips allow the blades to stay sharp longer, make smooth cuts, and withstand abrasive materials that would quickly wear down standard steel saw teeth.
They offer superior durability, longevity, efficiency, precision and versatility for both handheld power saws and stationary saws compared to other types of abrasive blades. Carbide tipped blades are indispensable cutting tools for professional construction crews as well as DIYers working with metal, stone and concrete.
Key Details:
- Used to cut very hard materials: stone, concrete, tile, steel, reinforced concrete
- Tungsten carbide inserts brazed onto saw blade teeth
- Stay sharp up to 100 times longer than steel
- Used on handheld or stationary saws
- Available in various diameters and arbor sizes
- Graded by carbide type for durability, toughness, shock resistance
Types of Cemented Carbide Saw Tips
There are several compositions of tungsten carbide used in saw tips, which determine properties like strength, hardness, durability and sharpness. Common grades include:
Carbide Type | Description |
---|---|
C1, C2 | Basic grade with 6% cobalt content, lower hardness and toughness for steel cutting |
C3, C4 | Harder grade with 6-8% cobalt content, better wear resistance |
C5 – C8 | Mid-range hardness and durability for most construction materials |
C9 – C11 | Professional quality with high hardness and heat/shock resistance |
In addition, cemented carbide tips feature different geometries and shapes:
- Alternate bevel teeth
- Triple chip tooth
- Flat trapezoidal
- Convex cylinder
These tooth shapes affect chipping, cutting speed, smoothness of cut and more. The optimal design depends on your material and application.
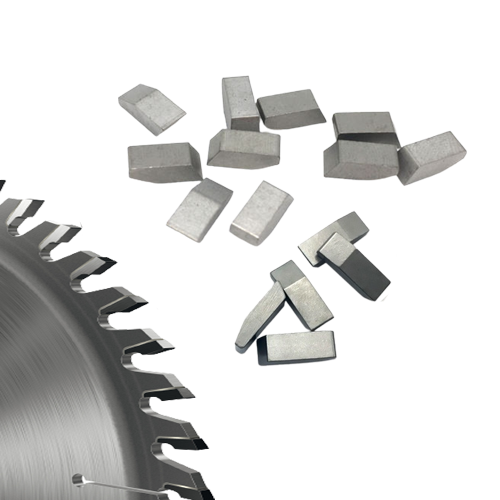
cemented carbide saw tips Composition
Cemented carbide is a composite material manufactured by powder metallurgy methods. It consists of extremely hard carbide particles cemented into a tough cobalt or nickel binder matrix.
Ingredient | Role |
---|---|
Tungsten carbide (70-97%) | Provides extreme hardness and wear resistance |
Cobalt binder (3-30%) | Holds carbide particles together, adds fracture toughness |
Other carbides | Titaniun, niobium, vanadium carbides may be added for hardness/toughness |
Tantalum, niobium | Grain growth inhibitors to optimize particle size |
The precise composition is tailored to the specific demands of the application through variations in:
- Carbide grain size
- Binder percentage
- Alloying elements
- Sintering process parameters
This versatility allows the material properties like hardness, strength and shock resistance to be optimized as needed.
Manufacturing Process
Cemented carbide is manufactured through powder metallurgy techniques:
- Pure tungsten ore is crushed to a powder then combined with carbon and other elements
- This tungsten powder is carburized at 1400-1700°C to form hard tungsten carbide (WC) grains
- The WC powder is milled down to nano-scale particle sizes optimized for the application
- Binder metal powders and grain growth inhibitors are mixed together
- This powder mixture is compacted and heated at 1350-1650°C in vacuum furnaces to form a fully dense cemented carbide
- The sintered carbide is then diamond ground into the necessary tip geometries
- Carbide inserts are induction brazed onto the steel saw blades
Through variations in composition, powder processing steps, sintering and finishing operations – cemented carbides can be tailored with properties unmatched by other materials.
cemented carbide saw tips Properties
The composite nature of cemented carbides leads to an unmatched combination of hardness, strength and fracture toughness:
Property | Description |
---|---|
Hardness | 86-93 Rockwell A, comparable to diamond |
Strength | On par with medium carbon steels |
Toughness | Much higher than ceramic materials |
Wear Resistance | Hundreds of times more resistant to abrasive wear than tool steel |
Chemical Stability | Inert to nearly all chemicals except aqua regia acid |
In particular, the cobalt binder phase in cemented carbides gives them resistance to crack propagation. As cracks form under stress, they are deflected or stopped when they encounter cobalt-carbide boundaries.
This combination of extreme hardness and improved toughness makes cemented carbide suitable for reliable, consistent performance in demanding environments. They retain these outstanding properties even at high operating temperatures.
Characteristics and Features
In addition to hardness and durability, some notable performance characteristics of carbide tipped saw blades include:
Long Lasting Sharpness
The tungsten carbide maintains its incredibly sharp cutting edge, even through extended use in abrasive materials. Carbide teeth stay sharper up to 100 times longer compared to high speed steel.
Fast, Smooth Cuts
The razor-sharp, durable teeth facilitate faster feed rates through hard materials. Quality carbide blades produce very smooth, precise cuts with low vibration.
Stability Under Heat
Carbide has a high heat deflection temperature so it retains hardness and strength in high heat applications like friction-rich cuts.
Superior Toughness
Unlike ceramic inserts which are brittle, carbide inserts resist cracking or chipping when subjected to impact. This reliability leads to excellent productivity.
Broad Compatibility
Available in range of arbor sizes, diameters and tooth configurations to fit common reciprocating saws, chop saws, tile saws, masonry saws and more.
Cost Effectiveness
Despite the upfront price, long lifetimes in abrasive conditions make carbide saw blades more cost effective per cut than competing disposable options.
With outstanding sharpness retention, cutting ability, speed and toughness – carbide tipped blades are indispensable for efficient processing of extremely hard materials.
Applications and Uses
Here are the most common applications best suited to carbide tipped blades:
Material | Applications |
---|---|
Masonry | Concrete, CMU, Brick, Mortar, Tile |
Natural Stone | Granite, Marble, Sandstone |
Refractories | Firebrick, Ceramic Tile |
Metals | Tool Steel, Stainless Steel, Steel Plate |
Composites | Fiber Cement, Cement Board, Fiberglass |
Other | Asphalt, PVC Pipe, Green Concrete |
Carbide blades perform well dry or wet. They stand up to gritty concrete dust as well as acidic brick cleaning solutions.
Suitable uses include:
- Straight Cuts
- Miter Cuts
- Plunge Cuts
- Scroll Cuts
- Slotting
- Grooving
Carbide tipped blades can make precise cuts in dimensional stone for custom countertops or cut steel I-beams on construction sites. They excel at both intricate, delicate tasks and large rugged jobs.
Saw Types Commonly Paired with Carbide-Tipped Blades
Saw Type | Applications |
---|---|
Masonry Saws | Cutting bricks, concrete blocks, stone slabs |
Chop Saws | Metal cutting in fabrication shops |
Circular Saws | Portable jobsite construction tasks |
Tile Saws | Cutting stone/porcelain tiles or similar materials |
Concrete Saws | Cutting joints in concrete walls, floors |
Metal Cutoff Saws | Steel structural members, pipes, metal sheet |
Examples include:
- Gas and electric portable, handheld saws used by construction crews
- High powered stationary saws used in industrial fabrication facilities
- Specialty masonry saws with water feeding systems used to produce custom cut stone or tile
Carbide blades enhance performance for all types of reciprocating, circular and chop saws.
cemented carbide saw tips Specifications
Cemented carbide saw blades are available in range of sizes and configurations to suit different saw types. Common specifications include:
Attribute | Options |
---|---|
Diameter | 4 inches up to 16+ inches |
Arbor Size | 5/8 inch, 1 inch, 1-1/4 inch |
Tooth Style | Alternate Bevel, Triple Chip Grind |
Tooth Count | 12 to >100 teeth |
Cutting Depth | 1 – 6 inches depending on diameter |
Plate Thickness | 0.050 inches up to 0.125 inches |
Teeth per Inch | 4 teeth/inch up to 32 teeth/inch |
Carbide grit size, binder percentage, tooth geometry and more also vary depending on manufacturers. Look for details on composition, number of carbide tips, tip thickness, braze integrity and shock resistance.
Popular standard sizes:
- 4-1/2 inch diameter for angle grinders
- 7-1/4 inch diameter for circular saws
- 14 inch diameter is common for stationary masonry saws
- 16 inch diameter for large metal cutting machines
Matching your saw arbor size and acceptable blade diameters ensures correct fits and safe operation.
cemented carbide saw tips Grades
Like all cemented carbides, saw tips use grading systems to designate properties like hardness, transverse rupture strength and grain size. These affect durability and applications.
Grade Class | Description | Common Grades |
---|---|---|
P, M | Softer grades for steel, non-ferrous metals | P01 – P40, M10 – M40 |
K | General purpose grades balanced hardness/toughness | K01 – K40 |
C | Harder grades for abrasive non-metallic materials | C1 – C8 |
S | Hard precision grades for abrasive materials | S01 – S50 |
Micrograin | Extra fine grain grades for finishing cuts | K05, K10 |
Higher class letters or numbers denote harder, more wear resistant binds best suited to very abrasive materials like concrete and stone.
Choose hardness rating carefully – hard tips last longer in tough materials but are more prone to cracking in highly interrupted cuts.
cemented carbide saw tips Standards
Tungsten carbide grades must meet strict quality standards for reliable performance. Relevant standards include:
Standard | Organization | Description |
---|---|---|
ISO 513 | International Organization for Standardization | Classifies carbide by composition and application |
ASTM B766 | ASTM International | Standard specification for cemented carbides |
US Federal Specification GG-T-650c | General Services Administration | Grades carbides by transverse rupture strength |
Reputable carbide tipped blade manufacturers test blades to quality standards and certify them RoHS Compliant for safety.
Insist on products meeting national and international cement carbide standards for assured performance.
cemented carbide saw tips Cost Analysis
Size | Type | Cost Per Blade | Cost Per Cut |
---|---|---|---|
4.5″ | Handheld | $15 | $0.10 |
7-1/4” | Circular | $25 | $0.05 |
14” | Stationary | $150 | $0.025 |
16” | Industrial | $200 | $0.02 |
- Cost per full-size carbide tipped blade ranges widely from $15 for smaller handheld versions up to $200+ for large industrial stationary blades
- But cost per cut is very low at $0.02 – $0.10 thanks to long life
- Last 5-10 times longer than abrasive blades
- Payback period comes quick then delivers productivity
Advantages of carbide blades:
- Upfront cost per blade higher than competing options
- But last for thousands of cuts so cost per cut is quite low
- Increased productivity over life of blade
- Time savings from faster cut speeds
Disadvantages:
- Require brazing carbide inserts which increases manufacturing complexity
- Brittle carbide tips can crack if blade core body isn’t properly designed
- Not designed for completely interrupted cuts
Overall carbide tipped blades deliver huge performance-per-dollar benefits thanks to durablecomposition and precision manufacturing.
Comparisons to Alternative Blade Types
Carbide Recommendation
With outstanding durability and well-rounded capabilities that diamond and abrasives can’t match – carbide tipped blades are the best choice for efficient processing of extremely hard materials like concrete, stone and steel.
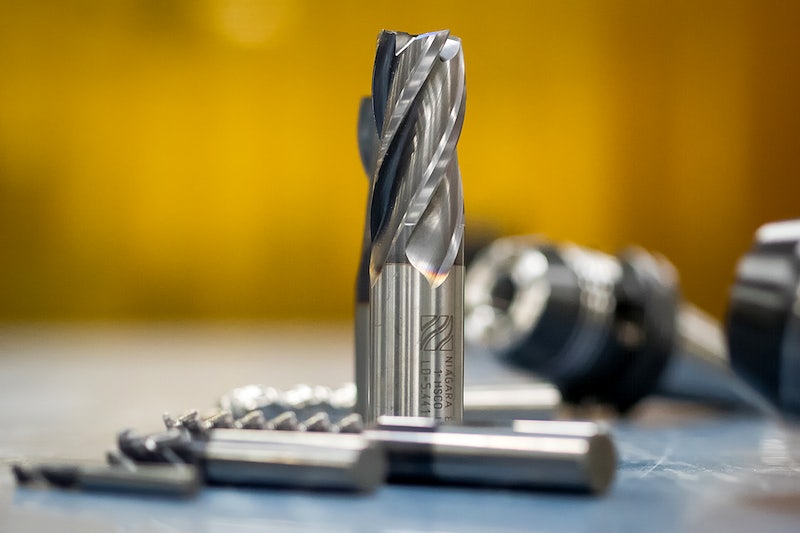
Suppliers and Manufacturers
Top suppliers of carbide tipped saw blades include:
Company | Location | Contact |
---|---|---|
Freud | Italy | freud.com |
Lenox | USA | lenoxtools.com |
Irwin | New Zealand | irwin.com |
M.K. Morse | USA | mkmorse.com |
Bosch | Germany | boschtools.com |
Milwaukee | USA | milwaukeetool.com |
Makita | Japan | makitatools.com |
When selecting blades, look for indications of quality like:
- Grade of carbide inserts used
- Uniformity of brazing
- Carbide thickness/integrity
- Tooth geometry optimized for application
- R&D support and testing data
- Industry certifications
- Manufacturer specialization
FAQs
Q: Why are carbide tipped blades so expensive?
A: Manufacturing carbide inserts and brazing them onto saw bodies requires advanced powder metallurgy techniques. The raw tungsten ore inputs are also expensive. But carbide blades last far longer than cheaper abrasive blades, paying back their price many times over.
Q: Can I sharpen carbide tipped blades?
A: No, attempting to sharpen them will damage the brazed-on inserts. However, carbide tips stay sharp for thousands of cuts if used properly, obviating the need for sharpening.
Q: What are some tips for prolonging carbide blade life?
A: Letting blades overload or overheat is the most common cause of premature wear or breakage. Ensure proper feed rates, cut depths, saw horsepower, blade rpm and cooling. Also periodically inspect teeth for cracks.
Q: Why did my carbide blade crack during use?
A: Carbide blades rely on the shock-absorbing steel core to withstand impact. Cracks happen if this steel body is too thin or hard. Manufacturing defects and improper use can also be causes. Quality control by reputable brands minimizes defects.
Q: Can I use carbide blades on any saw?
A: While carbide blades fit many saw types, very high speed can cause braze failure. Ensure your saw’s max RPM rating exceeds the blade RPM rating for safe operation. Lower power saws may also struggle to feed carbide blades fast enough.
Conclusion
With outstanding wear resistance, hardness and longevity that other blade types can’t match – cemented carbide tipped saws are the ultimate solution for working efficiently in extremely demanding materials like stone, concrete and steel.
Their exceptional sharpness retention and smooth cutting action facilitate productivity across a wide range of construction and fabrication jobs where downtime for blade changes is costly.