Overview of tungsten carbide mining buttons
Tungsten carbide mining buttons are made of tungsten carbide, one of the hardest materials used in industrial applications. They are extremely wear resistant buttons inserted on digging tools in the mining industry such as on bucket wheel excavators, roadheaders, shearers, and continuous miners.
Tungsten carbide mining buttons protect the cutting edges and surfaces of these machines that have to withstand very abrasive operating environments when working with hard rock. The properties of tungsten carbide make it ideal for prolonging the service life of mining equipment and reducing wear part replacement frequency.
Key details:
- Made of tungsten carbide containing over 90% tungsten mixed with cobalt as binder
- Extreme hardness around 90 on the Rockwell A scale
- Compressive strength over 5500 MPa
- High density around 15 g/cm3
- Very abrasion and erosion resistant
- Withstands high impact
- Resists deformation at high temperatures
- Used to line high wear areas on mineral extraction machines
- Provides protection from abrasive rocks
- Reduces downtime for maintenance
- Comes in various shapes like hexagonal, round, square etc.
- Many sizes options starting from 10mm across
- Needs precision manufacturing
Types of Tungsten Carbide Mining Buttons
There are several types of tungsten carbide mining buttons categorized by properties, manufacturing method and application:
Type | Hardness | Grain Size | Key Properties | Main Applications |
---|---|---|---|---|
Cast carbide buttons | 88-90 HRA | Small, heterogeneous grains | Impact resistance, strength | Roadheaders, shearers |
Sintered carbide buttons | ~92 HRA | Medium, tightly packed grains | Wear resistance | Bucket wheel excavators |
PDS carbide buttons | Up to 96 HRA | Ultrafine, homogeneous grains | Extreme abrasion resistance | Continuous miners |
Carbide buttons with TiC, TaC, NbC | Higher as per additive | Depends on WC used | Enhanced mechanical characteristics | Highly abrasive environments |
Carbide-ceramic composite buttons | >92 HRA | Ultrafine WC with ceramic | High fracture toughness | Medium impact, high abrasion |
Cast carbide buttons are tougher types made by infiltrating tungsten carbide particles into a cobalt based melt pool. They exhibit slightly lower hardness but greater impact strength. These are suited for mining machines like roadheaders and shearers.
Sintered carbide buttons are created from tungsten carbide powders containing small amounts of cobalt or nickel bond material compacted under high temperature into dense buttons. They demonstrate higher hardness and are applied on bucket wheel excavators.
PDS carbide buttons use extremely fine grained tungsten carbide powders produced by advanced sintering techniques. Their fine grain structure imparts great resistance to abrasive wear making them last longer in continuous miners.
Grades with carbides of titanium, tantalum or niobium as additives manifest greater fracture toughness or strength to withstand heavy impacts during drilling or digging hard rocky material.
Carbide-ceramic composite buttons fuse fine grained tungsten carbide particles with a ceramic compound like titanium carbonitride. They exhibit combined advantages of high hardness from the ceramics and toughness from the tungsten carbide.
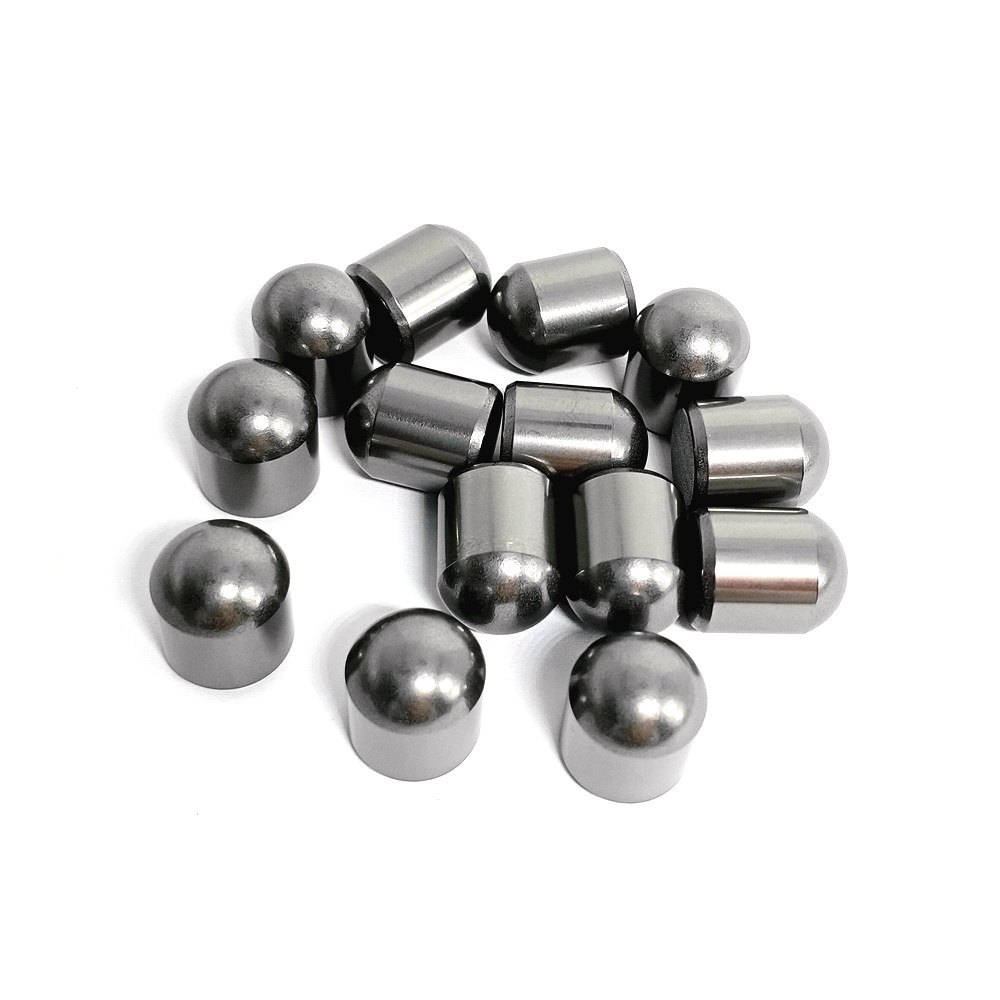
Properties of Tungsten Carbide Mining Buttons
Tungsten carbide mining buttons have exceptional physical and mechanical properties that make them ubiquitous across excavation and drilling equipment employed in the mining sector:
Property | Values |
---|---|
Chemical composition | WC over 90%, Co 6-10% |
Hardness | 88 – 96 HRA |
Density | 14.95 – 15.10 g/cm3 |
Compressive strength | 5500 – 8000 MPa |
Flexural strength | 3500 – 5500 MPa |
Fracture toughness | 8 – 15 MPa√m |
Maximum service temperature | 500°C in air |
Melting point | 2870°C |
Coefficient of thermal expansion | ~5 μm/m-K |
Electrical resistivity | 25 – 35 μΩ-cm |
Poisson’s ratio | 0.22 – 0.28 |
Shear modulus | 3.5 – 6.0 GPa |
Thermal conductivity | 60 – 90 W/m-K |
The outstanding mechanical strength, high density, extreme hardness, impressive thermal characteristics, and electrical conductivity make these buttons perfect for withstanding tremendous stresses on mining equipment. Selected properties can be enhanced further through innovative powder processing and sintering methods or by adding specific metal carbides.
Characteristics of Tungsten Carbide
Tungsten carbide possesses certain unique characteristics that enable it to perform excellently across mining machinery:
Extreme hardness and abrasion resistance – With hardness rivaling that of synthetic diamonds and boron nitride, tungsten carbide mining buttons easily withstand harsh impacts and scratches from drill bits and rocky material during excavation. The fine, dense structure of tungsten carbide grains hardly allows solid particles to penetrate through buttons’ surface leading to remarkably high wear resistance.
Strength and toughness – Tungsten carbide combines impressive strength levels comparable to alloy steels with reasonable fracture toughness from the cobalt binder which prevents sudden brittle failures through crack propagation stopping mechanisms. This permits mining buttons to endure cyclical loading across drilling, ripping, and crushing machines with intermittent high-stress peaks.
High temperature stability – The refractory attributes of tungsten metal confer substantial hot hardness on the compound permitting mining equipment exposed to frictional heat and high temperatures deep underground to retain much of its mechanical strength. Tungsten carbide buttons outlast steel alternatives which lose hardness precipitously above 350°C.
Corrosion and oxidation resistance – Tungsten carbide buttons resist degradation from moisture, acidic/alkaline solutions, organic chemicals etc. enabling sustained use around corrosive ores or minerals. The cobalt binder however may get affected under extreme conditions necessitating alternative binders. Oxidation resistance in dry atmospheres allows durable operation but buttons may need ceramic coats in highly humid mining environments.
Thermal shock resistance – The capacity to endure repeated cycles or fluctuations in operating temperatures without fracturing makes tungsten carbide well suited for heavy machinery prone to such thermal stresses especially during start-stop procedures underground. Their higher thermal conductivity compared to other hard materials prevents localized buildup of internal thermal gradients.
Electrical/thermal conductivity – Tungsten carbide buttons conduct heat and electricity relatively well because of metallic tungsten grains. Certain mining applications capitalize on this attribute beyond simply wear resistance like electrical discharge machining (EDM) electrodes or heating elements for ore smelting vessels. Specific grades manifest much higher conductivities.
Applications and Uses
Tungsten carbide mining buttons serve in diverse applications across mineral and metal extraction processes because of remarkable physical properties:
Industry | Machinery/Equipment | Function |
---|---|---|
Underground mining | Roadheaders, shearers, continuous miners | Wear protection pads, cutting picks, drilling inserts |
Surface mining | Bucket wheel excavators, conveying systems | Lining for impellers, housing, conveyor belts |
Oil and gas drilling | Downhole hammers, top-hammer drill bits | Inserts and buttons on drilling surfaces |
Mineral processing | Crushing machines, pulverizer barrels | High wear area cladding, percussion elements |
Welding and cutting | Plasma torches, welding tips | Current conduits, orifice inserts |
Wastewater treatment | Slurry pumping impellers | Layering on surfaces handling abrasive slurries |
Underground mining machinery broadly empowers two key functionalities – drilling holes and tunnels through hard rock by roadheaders, and extracting exposed mineral seams via shearers and continuous miners. Carbide inserts arm the cutting, boring and crushing elements like disc cutters, picks, drums to enormously enhance durability and productivity.
Surface mining bucket wheel excavators allow low-cost open pit mining but require tungsten carbide clad buckets and conveyor screw housing to handle high-friction ore and rocks. Even haul trucks transporting aggregates benefit from carbide buttons on dumping surfaces.
Within oil and gas drilling, the incredibly hard and temperature resistant tungsten carbide facilitates economical and faster penetration through tough rock layers by lining drill bits and downhole jackhammer components.
For mineral processing, carbide buttons help ore grinding machines efficiently pulverize large volumes of extremely abrasive gold or platinum containing gangue. Carbide-steel composite liners minimize wear inside crushing units that handle quartz, silicates and abrasive copper deposits.
Carbide’s heat and current carrying capabilities are applied in welding to manufacture durable plasma arc electrodes and nozzles resisting melt erosion and high temperatures.
Specifications
Tungsten carbide mining buttons are available in standardized grades but can be tailor-made to suit specific equipment needs or operating conditions. Key specifications cover:
Sizes and Shapes
- Round buttons from 10mm dia. to 100mm dia.
- Square buttons from 10mm to 80mm
- Rectangle variants from 10x20mm to 50x100mm
- Hexagonal, octagonal, trapezoid shapes possible
- Cutting insert thickness ranges 0.5mm to 20mm based on application
- Custom configurations created depending on mining machine part geometry
Mechanical Properties
- Cobalt content between 6% and 30% by weight
- Hardness spanning 85 HRA for tough buttons to 96 HRA for extreme abrasion resistance
- Transverse rupture strength from 3000 MPa to beyond 6000 MPa
- Tungsten carbide content minimum 90% to assure performance
Standards and Grades
- Most buttons made to ASTM, ISO or proprietary specifications
- Common ASTM specifications – B777 and B779 dealing with tungsten carbide hardmetal properties
- Numerous proprietary grades based on intended functionality
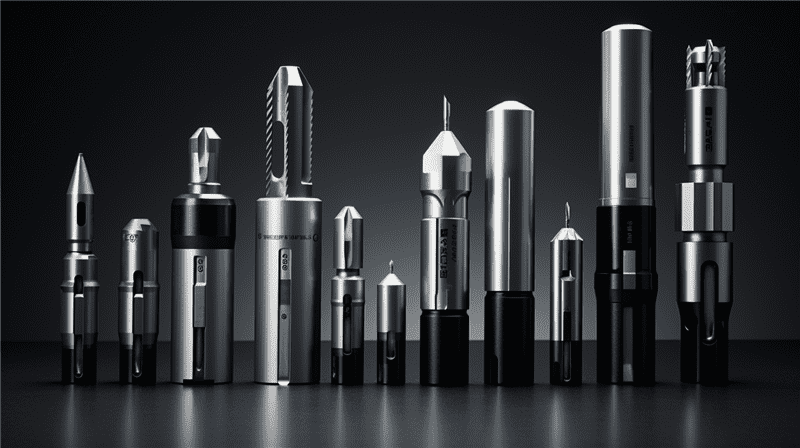
Manufacturers and Suppliers
As a specialty industrial product serving niche applications, tungsten carbide mining buttons require advanced powder metallurgy techniques combined with precision machining for shaping into end-use components.
Leading global manufacturers of tungsten carbide mining buttons include:
Manufacturer | Headquarters | Product Grades |
---|---|---|
Sandvik | Sweden | CC650, CC680, CC690, CC695 |
Kennametal | USA | Grade A, B, C, K68 |
Ceratizit | Luxembourg | TAZ8880, TAZ1090 |
Iscar | Israel | IC807, IC908 |
Carbide button suppliers typically stock an inventory of popular grades, sizes and offer customization as per mining equipment requirements. Large projects may warrant direct supply from the OEM carbide producers.
Online distributors provide the flexibility to directly purchase smaller quantities or samples for feasibility from their e-commerce stores before committing to bulk orders.
Cost Analysis
Raw material costs – Tungsten pricing is volatile being a rare metal dictated by global supply and demand. Prices range $250–$400 per MTU of 88.5% ammonium paratungstate. Grades depend on other carbide additives.
Manufacturing processes like multistage powder preparation, pressing and high temperature sintering add to product costs. Additional diamond grinding, laser cutting raises precision-made components price.
Tungsten carbide mining buttons cost on average $8 to $40 per kg depending on size, grade required, order volumes and levels of customization. Typically large OEM batches are most economical.
Operational cost savings from enhanced wear resistance and longer service life offset higher initial purchase costs. Consider entire mining equipment TCO.
Tungsten Carbide Button Costs | |
---|---|
Raw material | $25 to $250 per kg |
Manufacturing | $15 to $30 per kg |
Product price range | $40 to $300 per kg |
Cost drivers: raw material purity, powder size and processing method, hardness level demanded, order size, special treatments like shape forming or coatings etc. Grade selection is optimized based on operational needs.
Pros and Cons
Advantages
- Extreme hardness avoids premature wear failure
- Withstands high impact loads without fracturing
- Resists abrasion from mineral ores and gangue
- Survives exposure to heat, corrosion, oxidation
- Reduces overall mining equipment operating costs
- Prolongs service life manyfold over steel parts
Limitations
- Brittle material prone to breakage under bending
- Lower fracture toughness necessitates shock mounts
- Chipping at sharp cutting edges over prolonged use
- Care needed around brazing, welding procedures
- Relatively costly manufacturing and metal powder
- Supply volatility concerns over tungsten access
For most underground mining machinery, tungsten carbide inserts offer profound performance and economics benefits over any alternatives. Advancements in binder technology and nanostructured grades herald future opportunities.
Initial higher price remains main downside, calling for optimal insert placement balancing durability and budgets. Cobalt dependence also pushes development of cobalt-free grades. Integrated supply chain agreements help alleviate raw material availability risks from major global carbide producers.
FAQs
Q: Why choose tungsten carbide mining buttons over other materials?
A: Tungsten carbide mining buttons outperform alternatives like tool steel, hardened steel, chromium carbide overlay (CCO) plasma welds, ceramic inserts on two critical fronts – extreme hardness around 90 HRA manifesting as wear resistance along with higher toughness from cobalt metal binder enabling durability against fracture. Engineering the nanostructure of ultrafine tungsten carbide coupled with percentages and properties of the binder metal matrix paved the way for buttons combining hardness approaching diamond with toughness rivaling alloy steels.
Q: What are the different mining buttons manufacturing methods?
A: Cast tungsten carbide buttons see molten cobalt infiltrate compacted WC particles producing slightly porous buttons with lower hardness but high toughness. Sintered buttons get powdered raw materials compressed then heat treated under vacuum causing densification and solid bonding. This generates fine grade microstructure with over 92 HRA hardness. Further powder modifications via advanced spray drying or spraying/ pelletizing followed by optimized liquid phase or hot isostatic pressing boosts wear performance. Encapsulated buttons embed the entire WC-Co composite within a steel ring improving shock absorption. Surface treatments like TiN, TiCN or diamond coats on buttons also add functionality.
Q: How to select the right grade of tungsten carbide mining button?
A: Optimize grade selection balancing wear resistance, impact strength and budget for the specific mining machine component based on expected operational conditions – abrasion or erosion intensity, particle sizes handled, impacts, operating temperatures etc. Finer microstructure and higher hardness assures greater wear life but lower toughness and costlier price. Extremely abrasive applications would mandate ultrafine PDS carbide buttons or specialized complex graded metal carbide blends containing tantalum or niobium carbides dispersed in the WC-Co matrix. Basic guide – smaller the carbide grain size, the higher the performance and price. Consider trial testing onsite too.
Q: Why is cobalt the universal tungsten carbide binder for mining buttons?
A: Elemental cobalt uniformly dispersed in the tungsten carbide matrix acts as the gluing agent imparting crack stopping capability and shock absorbing capacity to the otherwise brittle WC particles. This cobalt binder toughening mechanism delivers unrivaled strength, hardness and fracture resistance to tungsten carbide mining buttons making them survive harsh, high stress digging, drilling and crushing environments. Cobalt possesses optimal melting, infiltrating, wetting and mechanical compatibility characteristics essential for liquid phase sintering based powder metallurgy production of tungsten carbide hardmetals. Recyclability of Co also assures security of supply and environmental sustainability.
Q: How are tungsten carbide buttons replaced or repaired?
A: Damaged buttons manifesting wear, cracks or missing portions need immediate replacement to avoid catastrophic tool failure. Based on mining machine repair philosophy – wear components like bucket teeth, cutting bits, wear pads often get replaced after usage thresholds while critical load bearing elements may allow minor refurbishment if engineering integrity remains intact. Remove worn buttons, clean mounting holes, ensure matching fits and secure new buttons strongly using bolts, brazing or specified means. Button resetting jigs aid efficient replacements. Repairs involve limited weld recoating or diamond coats.
Conclusion
Tungsten carbide mining buttons deliver substantial performance edge and cost savings in excavating machinery employed across demanding surface and underground mining environments. Metallurgical innovations reinforce properties most valued by asset owners – wear life, mechanical strength and temperature resistance while powder processing upgrades make ultrafine or complex graded metal carbides economically viable, tailored to specific rock types or operating conditions. With their profound impact on operational efficiency and reduced downtimes, these ubiquitous wear components represent one of the best industry technology investments, emphasized by their expanding adoption across construction, demolition and other off-road equipment categories. Assured access to raw materials and descending real prices driven by recycling initiatives and supply chain integration with major global producers will expand applicability across general engineering. Emergence of carbon composites, cermets and cubic boron nitride alternative materials however promise to diversify the product mix for niche functionality opportunities in future.