Straight coolant holes carbide rods are the backbone of many precision machining applications, combining durability, precision, and reliability. In this guide, we’ll delve into everything you need to know about straight coolant holes carbide rods. From their composition to their applications, production processes, and beyond, this comprehensive guide will help you become an expert on the topic.
What are Straight Coolant Holes Carbide Rods?
Straight coolant holes carbide rods are cylindrical rods made from tungsten carbide with integrated straight coolant holes running longitudinally. These holes improve machining performance by allowing coolant to flow directly to the cutting edge, reducing heat buildup, and enhancing tool life.
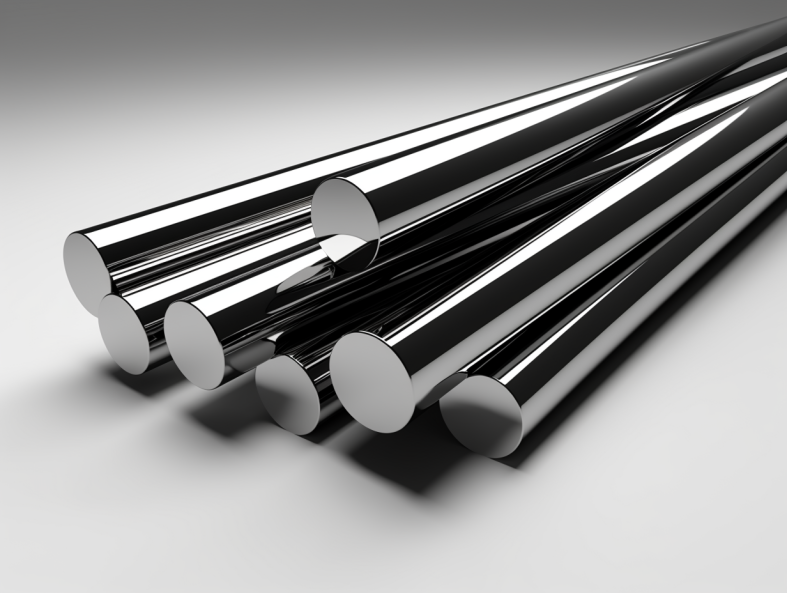
Raw Material and Composition Analysis of Straight Coolant Holes Carbide Rod
The strength and durability of these rods come from their material composition. Let’s break it down.
- Tungsten Carbide (WC): Forms the base matrix, known for its exceptional hardness and wear resistance.
- Cobalt (Co): Acts as a binder, providing toughness and elasticity.
- Metallic Additives: Often include tantalum (Ta), titanium (Ti), or niobium (Nb) to enhance specific properties.
- Grain Size: Fine-grained powders (0.5-2 µm) are used for higher hardness and strength, while coarse grains (>2 µm) add toughness.
Composition Breakdown of Straight Coolant Holes Carbide Rods
Material | Function | Typical Proportion (%) |
---|---|---|
Tungsten Carbide | Base material for hardness | 70-90 |
Cobalt | Binder for toughness | 6-12 |
Metallic Additives | Property enhancers (e.g., Ta, Ti) | 0-10 |
Others (e.g., Ni) | Fine-tuning mechanical behavior | <1 |
Production Process Flow of Straight Coolant Holes Carbide Rod
Creating straight coolant holes carbide rods involves precision engineering. Here’s a detailed walkthrough of the production process:
- Powder Preparation: High-purity tungsten carbide and cobalt powders are mixed with additives and binders.
- Pressing: The powder mixture is pressed into cylindrical green compacts with straight holes created using pin molds.
- Pre-Sintering: These green compacts are pre-sintered to achieve initial strength.
- Final Sintering: Rods are sintered in a high-temperature furnace, where tungsten carbide and cobalt bond chemically.
- Grinding and Polishing: Rods undergo precise machining to achieve dimensional accuracy and surface finish.
Visual Representation:
Step | Process Description |
---|---|
Powder Preparation | Mixing tungsten carbide, cobalt, and additives |
Pressing | Forming the raw shape with holes |
Pre-Sintering | Strengthening green compacts |
Final Sintering | Heating to bond the materials |
Grinding and Polishing | Achieving final size and surface quality |
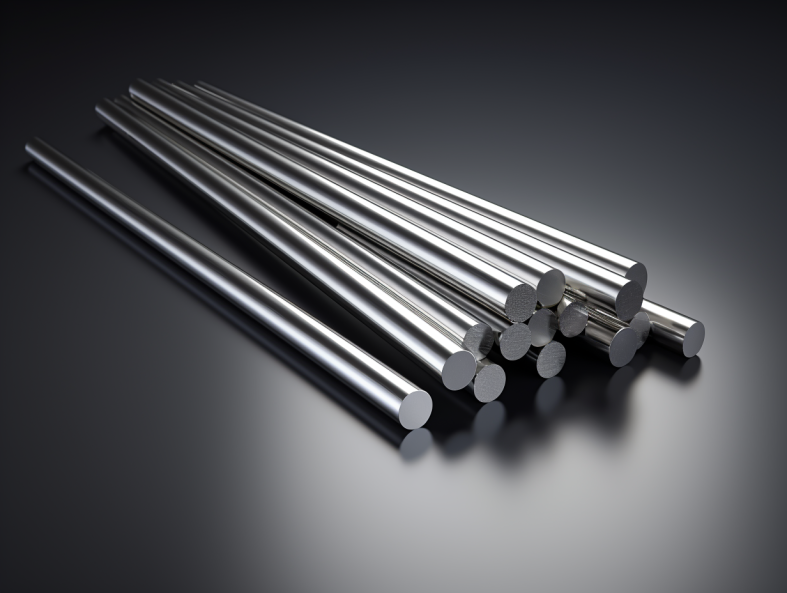
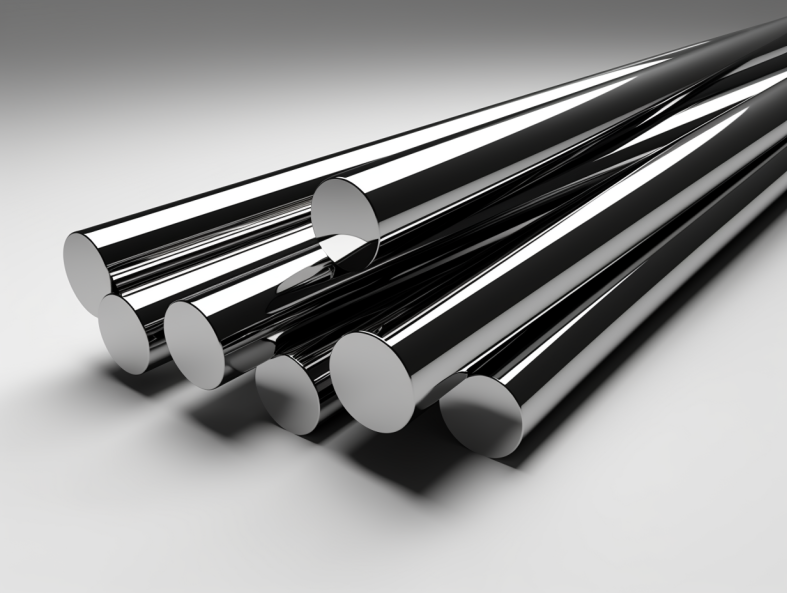
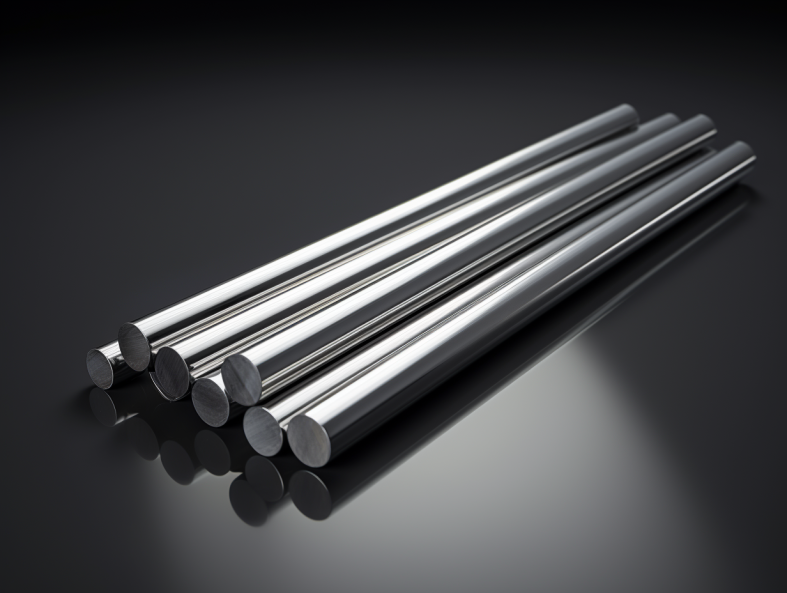
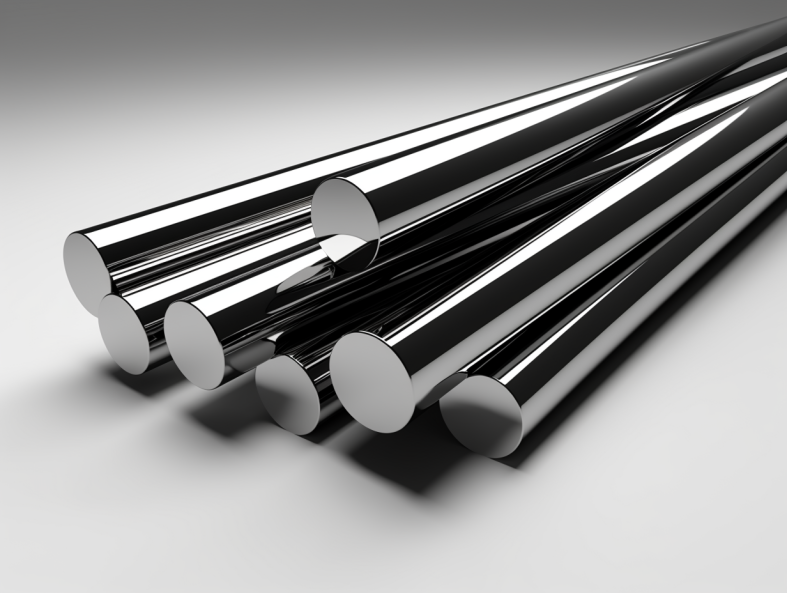
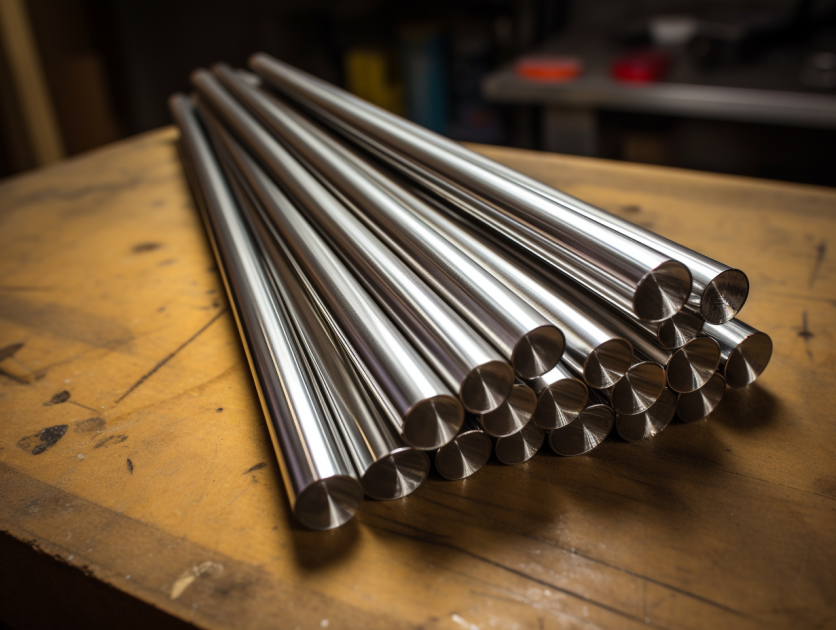
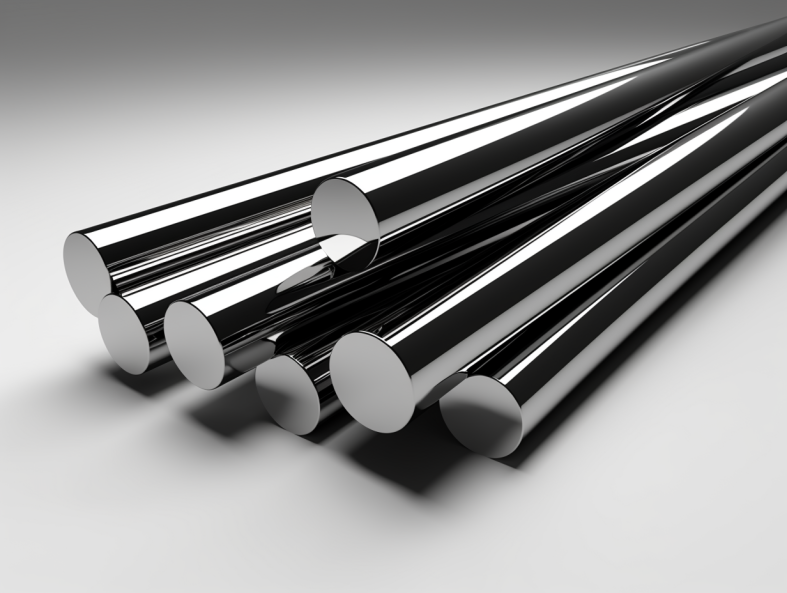
Applications of Straight Coolant Holes Carbide Rod
Key Industries Utilizing These Rods
Straight coolant holes carbide rods are essential in industries demanding precision and durability. Let’s explore their common applications:
Industry | Application |
---|---|
Automotive | Drilling engine blocks, crankshafts, and precision components |
Aerospace | Cutting heat-resistant superalloys |
Medical | Manufacturing surgical tools and orthopedic implants |
Electronics | Machining small, precise parts |
General Machining | High-speed and precision milling, drilling, and cutting |
Why Are They Preferred?
- Enhanced Cooling: Direct coolant flow reduces thermal damage.
- Increased Tool Life: Lowers wear and tear.
- High Precision: Maintains accuracy in demanding applications.
Material Properties of Straight Coolant Holes Carbide Rod
Let’s analyze the properties that make these rods indispensable.
Property | Description |
---|---|
Hardness (HRA) | 89-93, ensuring wear resistance |
Density (g/cm³) | 14.0-14.5, denoting material compactness |
Flexural Strength (MPa) | 2800-4000, allowing high stress handling |
Thermal Conductivity | Excellent, enhancing heat dissipation |
Corrosion Resistance | Resistant to most chemical attacks |
Comparison of Metal Powder Models
Below are some specific tungsten carbide powder models used in straight coolant holes carbide rods:
Model | Description |
---|---|
WC-10 | Standard grain size, suitable for general-purpose machining. |
WC-20 | Fine grain, designed for high-precision drilling applications. |
WC-30 | Medium grain, balanced between toughness and wear resistance. |
WC-40 | Coarse grain for heavy-duty applications with extended tool life. |
TaC-1 | Tantalum-enriched powder for added heat resistance. |
TiC-2 | Titanium additive for corrosion-resistant applications. |
NbC-3 | Niobium carbide for improved toughness in challenging conditions. |
Ni-Co Blend 1 | Nickel-cobalt blend for improved flexibility in impact-prone environments. |
Ultra-Micron | Ultra-fine powder for ultra-precise machining tasks. |
Eco-Carbide | Environmentally friendly composition with reduced cobalt content. |
Specifications, Sizes, Shapes, and Standards
Specification Overview
Parameter | Range/Options |
---|---|
Diameter | 3 mm to 30 mm |
Length | 50 mm to 330 mm |
Coolant Hole Diameter | 0.5 mm to 5 mm |
Tolerances | Up to ±0.01 mm |
Standards | ISO, DIN, ANSI |
Selecting the Right Straight Coolant Holes Carbide Rod
Here’s how to choose the perfect rod for your needs:
Factors to Consider
Factor | Description |
---|---|
Material Properties | Match hardness, toughness, and wear resistance to the application. |
Coolant Hole Size | Ensure compatibility with your cooling system. |
Tolerance Requirements | Check dimensional precision needs. |
Price vs. Performance | Balance cost with durability and performance benefits. |
Advantages and Limitations
Advantages | Limitations |
---|---|
Enhanced tool life due to effective cooling. | Higher initial cost compared to standard rods. |
Improved machining performance at higher speeds. | Specialized handling required during production. |
Versatile applications in multiple industries. | May require specific coolant systems for optimum performance. |
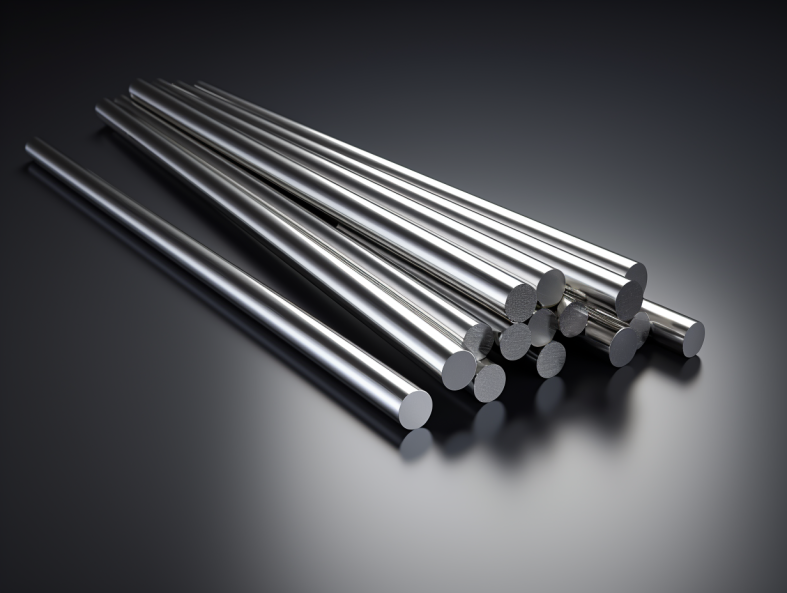
Suppliers and Pricing Details
Top Suppliers
Supplier | Location | Price Range (USD) |
---|---|---|
Kennametal | Global | $30 – $150 per piece |
Sandvik | Sweden | $40 – $200 per piece |
Ceratizit | Luxembourg | $50 – $180 per piece |
Zhuzhou Cemented | China | $20 – $100 per piece |
Sumitomo Electric | Japan | $35 – $160 per piece |
FAQ
Question | Answer |
---|---|
What are straight coolant holes for? | They allow coolant to reach the cutting edge, reducing heat and extending tool life. |
How are they better than solid rods? | They improve cooling and are more effective in high-speed machining. |
What industries use them? | Automotive, aerospace, medical, electronics, and general machining. |
Can I use these rods without coolant? | It’s not recommended, as they’re designed for use with a cooling system. |