Carbide rods are a powerhouse in the world of machining and industrial applications. They offer unmatched durability, hardness, and wear resistance, which makes them a go-to choice in industries ranging from metal cutting to drilling and beyond. But what exactly are carbide rods, and why are they so highly valued? Let’s dive deep into the world of carbide rods and find out everything there is to know!
What Are Carbide Rods?
Carbide rods are cylindrical, durable rods made primarily of tungsten carbide, a compound known for its extreme hardness and wear resistance. They are engineered to withstand high-impact conditions, making them a favorite for tools that require longevity and strength, such as drills, cutters, and grinding equipment. But how exactly are these rods made, and what gives them such incredible properties?
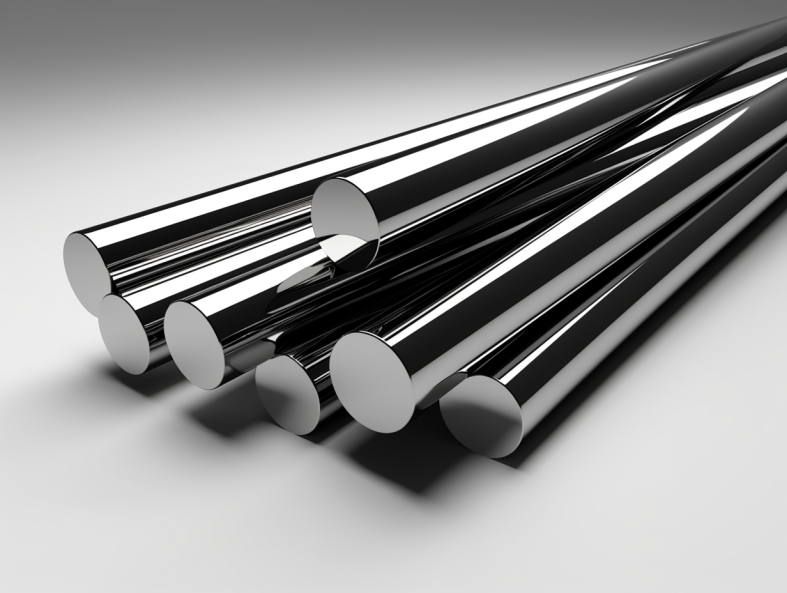
Raw Material and Composition Analysis of Carbide Rods
Carbide rods are typically made from tungsten carbide powder mixed with cobalt as a binder. The resulting compound is pressed and sintered into a rod form that is capable of handling high-pressure applications without breaking down.
- Tungsten Carbide (WC): The primary component, tungsten carbide, makes up about 85-95% of the composition, offering hardness.
- Cobalt (Co): Cobalt binds the tungsten carbide particles together, enhancing durability and providing slight flexibility.
Example Composition Table
Component | Percentage (%) | Function |
---|---|---|
Tungsten Carbide | 85-95 | Hardness, wear resistance |
Cobalt | 5-15 | Binding agent, adds toughness |
Titanium Carbide | Up to 5 | Enhances high-temperature strength |
Tantalum Carbide | Up to 2 | Increases hardness and stability |
Types of Carbide Rods
Carbide rods come in various types to cater to specific industrial needs. Each type differs in composition, hardness, wear resistance, and intended use. Here’s a rundown of some of the primary types available.
Table of Types of Carbide Rods
Type | Description |
---|---|
Solid Carbide Rods | Standard type for wear resistance, used in general applications. |
Double Helix Rods | Designed with a double helix for superior chip removal, ideal for drilling. |
Micro Grain Carbide Rods | Consist of smaller carbide particles, offering a smoother finish in fine machining. |
Ultra-Fine Grain Rods | Extremely fine particles, optimized for very precise, delicate machining tasks. |
Coolant Hole Rods | Feature internal holes to allow coolant flow, used in high-speed drilling. |
Submicron Carbide Rods | For extreme precision applications, especially in micro drilling. |
Rod Blanks | Unfinished rods that can be shaped according to specific requirements. |
Cemented Carbide Rods | Rods mixed with cementing agents for added durability in high-impact conditions. |
Applications of Carbide Rods
Carbide rods are renowned for their versatility. They’re widely used across multiple industries due to their toughness, wear resistance, and high thermal stability. Let’s explore the applications.
Table of Carbide Rod Applications
Application | Description |
---|---|
Metal Cutting | Used in drills, end mills, and lathe tools for precise, efficient cutting. |
Mining | Suitable for rock drilling tools, thanks to their ability to endure pressure |
Woodworking | Used in routers for shaping and cutting wood with precision. |
Aerospace | Employed in high-temperature components that withstand wear and tear. |
Automotive Manufacturing | Essential for making parts like cylinder liners, piston rings, etc. |
Oil and Gas Industry | Vital for drilling equipment as they handle abrasive conditions well. |
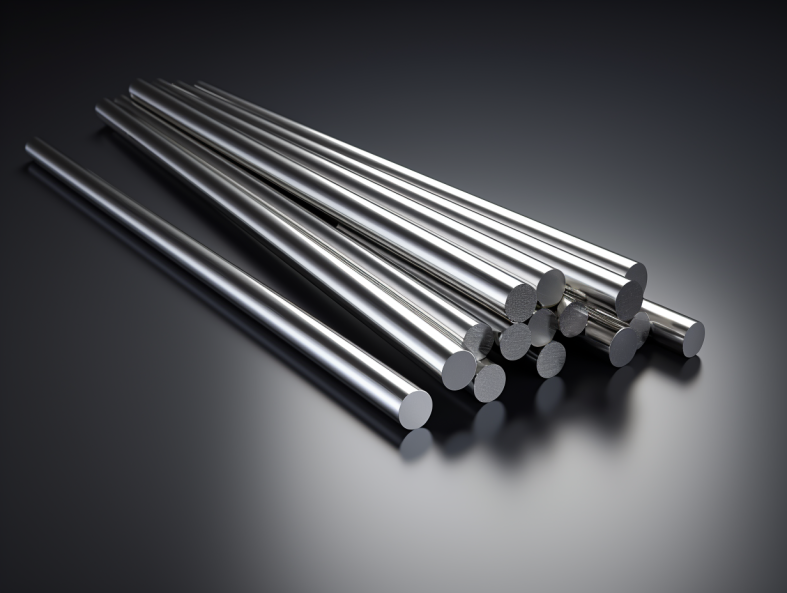
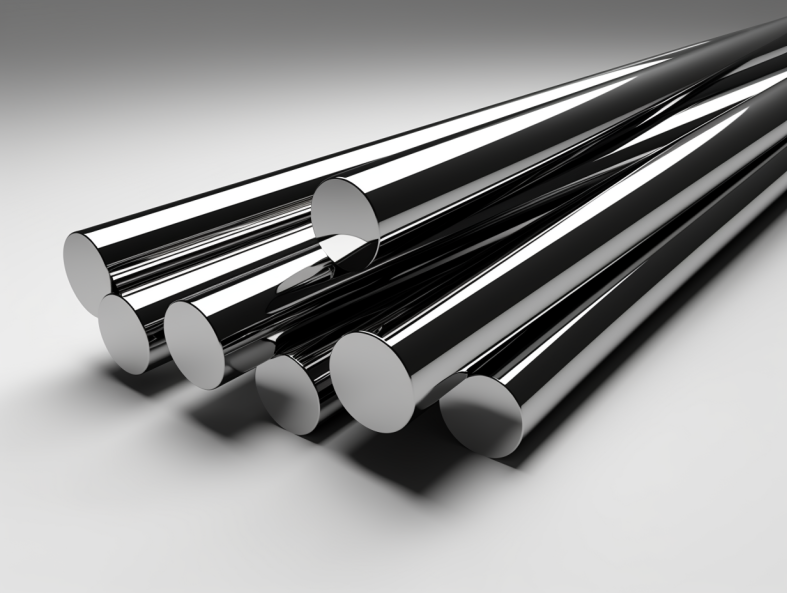
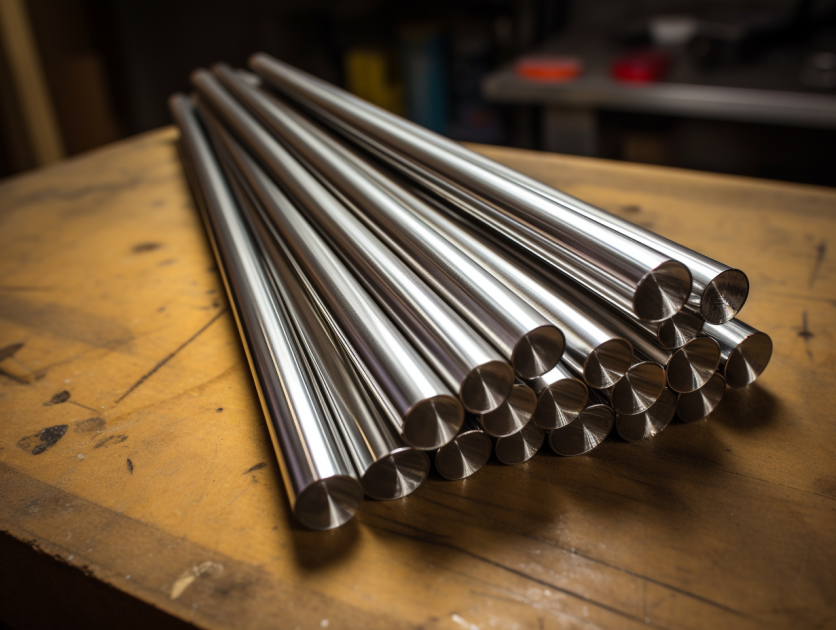
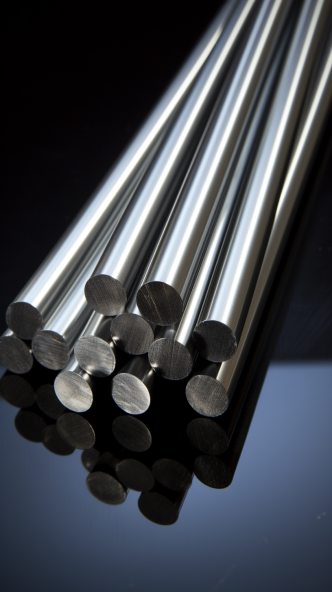
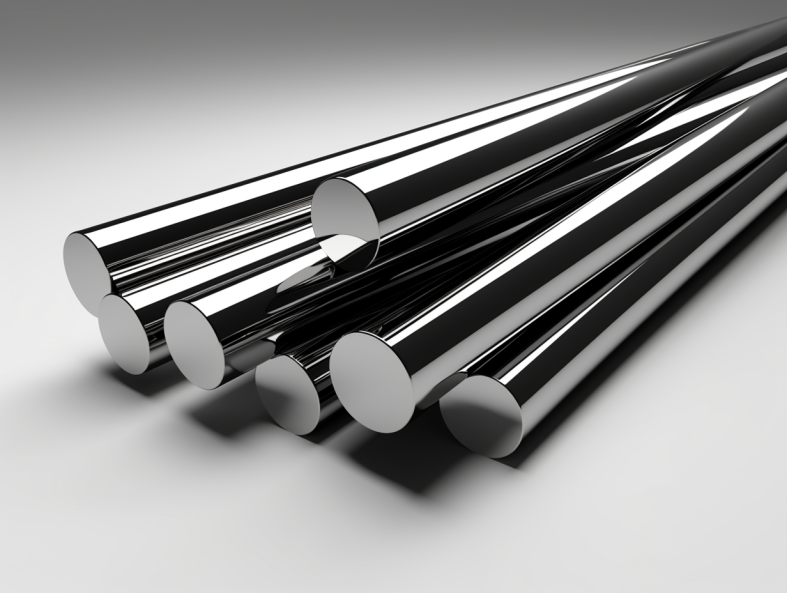
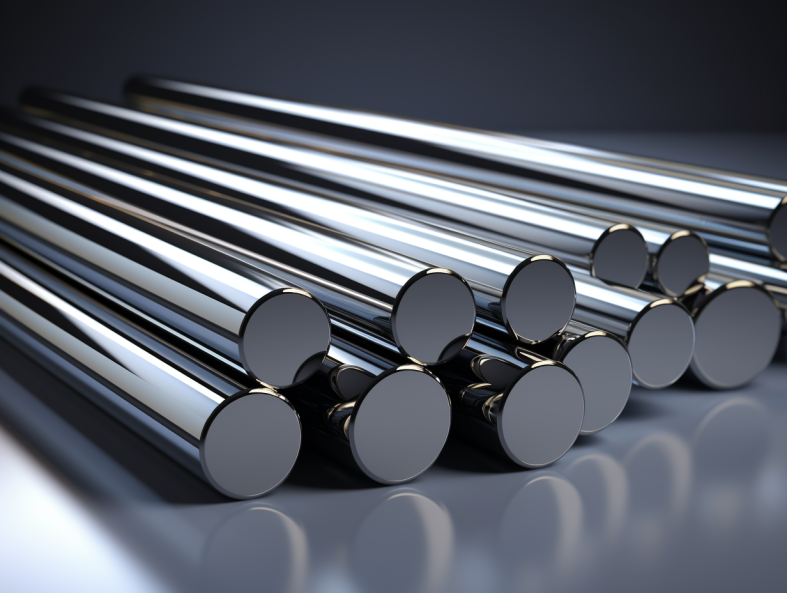
Production Process Flow of Carbide Rods
Carbide rods are produced through a complex, multi-step process to ensure they meet strict industry standards. Here’s an overview of the main steps in carbide rod production:
- Powder Preparation: Tungsten and cobalt powders are mixed, often with a wet binder.
- Compaction: The powder mix is compacted under high pressure to create a ‘green’ rod.
- Sintering: The compacted rod is sintered at high temperatures to achieve full density.
- Grinding: After sintering, the rod undergoes grinding for a smooth surface.
- Finishing: Surface treatments or additional machining can be done based on customer needs.
Material Properties of Carbide Rods
The material properties of carbide rods define their performance in various applications. Here’s a detailed look at the core properties.
Table of Material Properties of Carbide Rods
Property | Description |
---|---|
Hardness | Extremely hard, typically ranging between HRA 89-93 |
Density | High density (14.5 – 15.0 g/cm³), ensuring durability |
Flexural Strength | High flexural strength, about 2000 – 3000 MPa |
Thermal Conductivity | Moderate thermal conductivity for heat dissipation |
Elastic Modulus | Typically around 600 – 700 GPa |
Specifications, Sizes, Shapes, and Standards
Carbide rods come in various shapes and sizes to meet industry demands. Here’s a look at common specifications.
Table of Carbide Rod Specifications
Size | Diameter (mm) | Length (mm) | Shape Options |
---|---|---|---|
Small | 1-4 | 50-100 | Round, Square |
Medium | 4-10 | 100-200 | Round, Rectangular, Helical |
Large | 10-20 | 200+ | Round, Customizable (e.g., for coolant holes) |
How to Select the Right Carbide Rod
Selecting the right carbide rod is crucial. Factors to consider include application type, hardness, thermal stability, and cost.
Table for Selecting the Right Carbide Rod
Application | Ideal Type of Carbide Rod | Key Selection Criteria |
---|---|---|
Precision Machining | Micro Grain Carbide Rod | Smooth finish, low wear |
High-Speed Drilling | Coolant Hole Rod | Heat resistance, efficient chip removal |
Heavy-Duty Cutting | Cemented Carbide Rod | Extreme hardness, impact resistance |
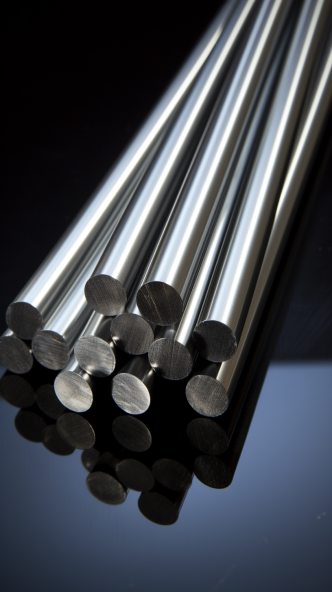
Comparison of Advantages and Limitations
Carbide rods are fantastic, but they aren’t without trade-offs. Here’s how they stack up.
Table of Carbide Rod Advantages and Limitations
Factor | Advantages | Limitations |
---|---|---|
Durability | High wear resistance, lasts longer | Higher upfront cost |
Thermal Stability | Maintains properties under heat | Potential brittleness at low temperatures |
Precision | Excellent dimensional control | Difficult to machine without specialized tools |
FAQ
Question | Answer |
---|---|
What is a carbide rod? | A carbide rod is a tungsten carbide tool known for high wear resistance and hardness. |
How do I choose a carbide rod for my application? | Consider factors like application, hardness, size, and cost to find the ideal carbide rod. |
Can carbide rods handle high temperatures? | Yes, they maintain stability in high temperatures, making them ideal for heavy-duty tasks. |