Imagine this: you’re in the throes of a metalworking project, meticulously shaping a piece of steel to your exact specifications. But then, disaster strikes! Your cutting tool dulls, leaving behind ragged edges and frustration in its wake. This is where square carbide inserts come in, the tiny titans of the metalworking world that can revolutionize your cutting experience.
Introduction to Square Carbide Inserts
Square carbide inserts are like the workhorses of metal cutting tools. They’re small, square-shaped pieces of incredibly hard tungsten carbide, a metal alloy renowned for its exceptional strength and wear resistance. These inserts are strategically mounted on cutting tool holders, sacrificing themselves first as they make contact with the metal being worked on. The beauty lies in their disposability. Once a carbide insert dulls, you simply rotate it to a fresh edge, or replace it entirely with a new one, extending the lifespan of your cutting tool significantly.
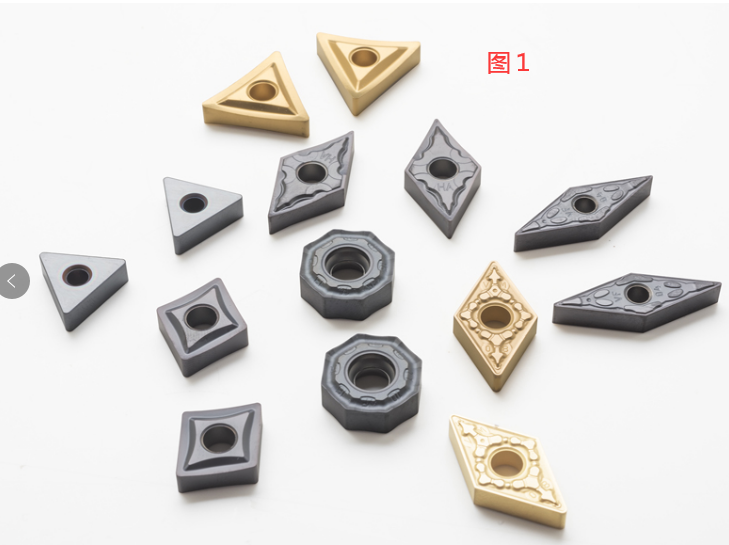
The Production Process of Square Carbide Inserts
Crafting a square carbide insert is no small feat. It’s an intricate process that demands precision and high-quality materials. Here’s a glimpse into the journey of these tiny powerhouses:
- Raw Material Selection: The process starts with meticulously chosen tungsten carbide powder. Manufacturers specifically select a grade of carbide best suited for the intended application. Factors like the type of metal being cut and the desired wear resistance come into play.
- Powder Mixing and Pressing: The carbide powder is meticulously blended with specific additives to enhance its properties. This mixture is then subjected to immense pressure in specialized molds, shaping it into the desired square form.
- Sintering: The compacted carbide undergoes a high-temperature furnace treatment called sintering. This process binds the particles together, forming a solid and incredibly strong carbide blank.
- Brazing: A thin layer of brazing material is applied to the carbide blank. This creates a strong bond between the insert and the tool holder, ensuring it stays securely fastened during operation.
- Grinding and Finishing: The final step involves grinding the carbide insert to achieve the precise cutting geometry needed for its specific application. This ensures clean, efficient cutting performance.
Selection of Square Carbide Inserts
With a vast array of square carbide inserts available, selecting the right one for your project can feel overwhelming. Here’s a breakdown of key factors to consider:
- Substrate Material: Different carbide grades are formulated to excel at cutting specific materials. For instance, inserts designed for cast iron might not perform optimally on stainless steel, and vice versa.
- Application: Consider the specific metalworking task at hand. Are you facing heavy-duty material removal or intricate finishing work? Different insert geometries cater to these varying needs.
- Cutting Edge Geometry: The insert’s cutting edge geometry significantly impacts performance. Factors like rake angle (the angle of the cutting face) and relief angle (the angle between the flank and the workpiece) influence chip formation and cutting efficiency.
- Number of Cutting Edges: Many square carbide inserts boast multiple cutting edges. As one edge dulls, you can simply rotate the insert to expose a fresh edge, maximizing its lifespan.
Advantages of Square Carbide Inserts
- Superior Wear Resistance: Compared to traditional tool steels, carbide inserts boast exceptional wear resistance. This translates to longer cutting times and fewer insert changes, ultimately saving you time and money.
- Clean Cutting Performance: The sharp cutting edges of carbide inserts deliver clean, precise cuts, minimizing tool chatter and imperfections on the workpiece.
- Versatility: Square carbide inserts come in a wide range of sizes, grades, and geometries, catering to diverse metalworking applications.
- Cost-Effectiveness: While the upfront cost of a carbide insert might seem higher than traditional tool steel bits, their extended lifespan and ability to produce more parts per insert make them a cost-effective choice in the long run.
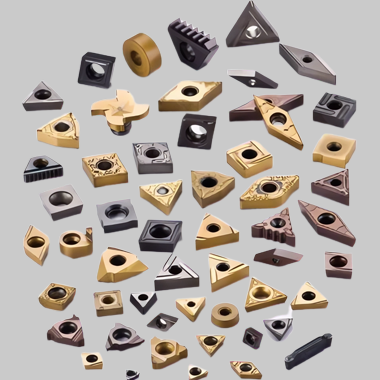
Disadvantages of Square Carbide Inserts
- Fragility: Carbide inserts, despite their strength, can be susceptible to chipping or fracturing if subjected to excessive impact or used incorrectly.
- Heat Sensitivity: Extreme heat generated during cutting can damage the carbide insert. Using proper cutting parameters and coolants is crucial to prevent this.
- Upfront Cost: As mentioned earlier, the initial cost of carbide inserts can be higher compared to traditional tool steel bits. However, their extended lifespan often evens out the cost in the long run.
Applications of Square Carbide Inserts
Square carbide inserts are ubiquitous in the metalworking world, finding application in various processes, including:
- Turning: Used on lathe tools for shaping and contouring metal workpieces.
- Milling: Employed in milling machines for creating pockets, slots, and flat surfaces on metal parts.
- Drilling: Specific carbide inserts can be used on drilling machines to create precise holes in metal.
- Boring: These inserts can be utilized for boring applications, enlarging existing holes in metal parts with high accuracy.
- Facing: Square carbide inserts are suitable for facing operations, creating a smooth and flat surface on the end of a metal workpiece.
Advanced Considerations for Square Carbide Inserts
While the core concepts have been covered, there’s a whole world of intricacies to explore within the realm of square carbide inserts. Here’s a deeper dive into some advanced considerations:
- Chip Control: Managing the chips produced during metal cutting is crucial. The insert’s geometry and the selection of the appropriate coolant can significantly impact chip control, preventing them from re-welding to the workpiece and ensuring a smooth cutting process.
- Coolant Selection: Using the right coolant plays a vital role in maximizing tool life and achieving optimal cutting performance. Coolants lubricate the cutting interface, reducing friction and heat generation. Different coolants are formulated for specific materials and applications.
- Cutting Speeds and Feeds: Selecting the optimal cutting speeds and feeds for the insert, material, and application is essential. Running the tool at incorrect parameters can lead to premature insert wear, compromised surface finish, or even tool breakage.
- Coating Technology: Many square carbide inserts come coated with a thin layer of ceramic or other materials. These coatings enhance wear resistance, improve chip control, and can even allow for higher cutting speeds.
Examples of Square Carbide Inserts in Action
Let’s delve into some real-world scenarios where square carbide inserts shine:
- The Busy Machine Shop: Imagine a bustling machine shop working on a tight deadline. Square carbide inserts come to the rescue. Their extended lifespan minimizes downtime for insert changes, allowing for uninterrupted production and timely project completion.
- The Home Hobbyist: Even hobbyist metalworkers can benefit from square carbide inserts. The clean cuts and extended life they provide can elevate the quality of their projects and reduce frustration caused by dull tools.
- The Art of CNC Machining: In the world of Computer Numerical Control (CNC) machining, square carbide inserts are instrumental. Their precise geometries and ability to maintain sharp edges ensure consistent, high-quality results on complex CNC projects.
Square Carbide Inserts vs. Other Cutting Tools
While square carbide inserts reign supreme in many metalworking applications, it’s important to understand how they stack up against other cutting tool options:
- High-Speed Steel (HSS) Tools: HSS tools are a traditional and affordable option. However, they wear out quicker than carbide inserts and require more frequent sharpening.
- Brazed Tip Tools: These tools feature a carbide tip brazed onto a steel shank. They offer a balance between affordability and wear resistance, but might not be suitable for heavy-duty applications compared to solid carbide inserts.
- Diamond Cutting Tools: Diamond offers unparalleled cutting hardness. However, diamond tools come at a significantly higher cost and are often reserved for specialized applications or very hard materials like composites.
The Future of Square Carbide Inserts
The world of square carbide inserts is constantly evolving. Here’s a glimpse into what the future might hold:
- Advanced Coatings: Expect advancements in coating technologies that further enhance wear resistance, heat dissipation, and even self-lubricating properties.
- Automation and Optimization: The integration of sensor technology and automated tool selection systems could optimize cutting parameters for even better performance and insert life.
- Sustainable Manufacturing: The development of eco-friendly manufacturing processes and recyclable carbide insert materials is a growing area of exploration.
FAQ
Q: How long do square carbide inserts last?
A: The lifespan of a square carbide insert depends on various factors like the material being cut, cutting parameters, and the insert’s grade and geometry. Generally, they can last significantly longer than traditional tool steel bits, reducing the need for frequent replacements.
Q: Can I sharpen square carbide inserts?
A: No, square carbide inserts are not designed for sharpening. However, their multiple cutting edges allow for rotation to expose fresh edges as they dull. Once all edges are used, the insert is simply replaced with a new one.
Q: Are square carbide inserts safe?
A: When used properly with appropriate safety gear, square carbide inserts are safe. However, it’s crucial to follow safety guidelines like wearing eye protection and ensuring the insert is securely fastened to the tool holder to avoid potential hazards.