Introduction: Tailored Precision for Demanding Applications
In the world of high-performance machining and wear-resistant components, precision is paramount. Customizable carbide blank dimensions offer manufacturers the ultimate flexibility to create tools and parts tailored to their exact specifications. No longer constrained by standard sizes, engineers and machinists can unlock new levels of performance, efficiency, and cost-effectiveness.
What are Customizable Carbide Blank Dimensions?
Beyond the Catalog: Precision at Your Fingertips
Customizable carbide blank dimensions refer to the ability to order Customizable carbide blanks – the foundational blocks from which cutting tools, wear parts, and other components are made – in non-standard sizes and shapes. This level of customization empowers manufacturers to:
- Optimize Tool Geometry: Achieve ideal cutting edge geometries for specific materials and machining operations.
- Minimize Material Waste: Reduce unnecessary material removal and associated costs.
- Create Unique Components: Manufacture parts with complex shapes and features not possible with standard blanks.
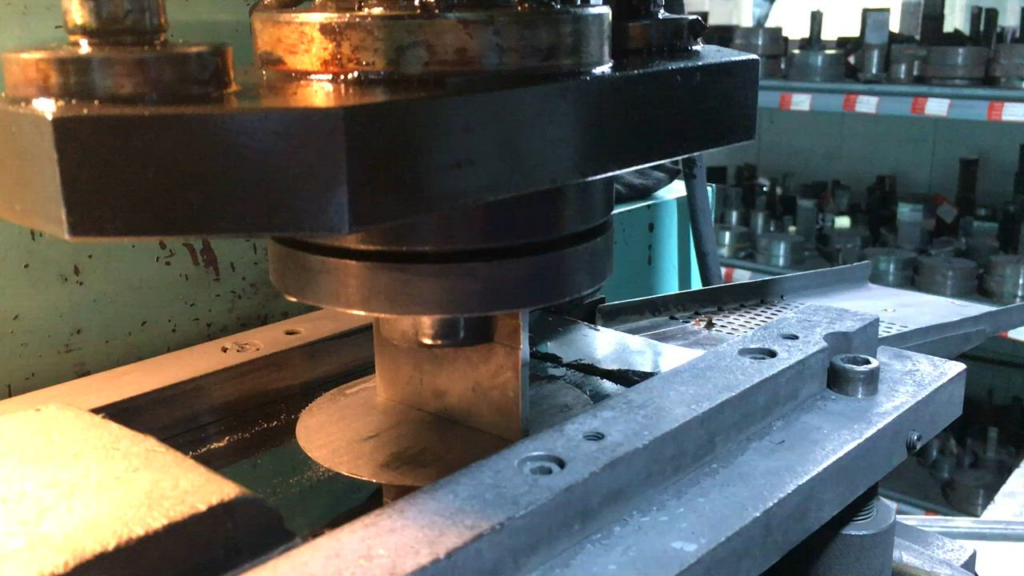
The Advantages of Customization: Why Choose Bespoke Blanks?
Tailored Solutions for Enhanced Performance
- Improved Tool Life: Optimized geometries and material utilization can significantly extend tool lifespan, reducing downtime and replacement costs.
- Enhanced Cutting Performance: Achieve higher cutting speeds, improved surface finishes, and tighter tolerances.
- Reduced Machining Time: Starting with a near-net-shape blank minimizes material removal, streamlining the machining process.
- Cost Savings: While custom blanks may have a slightly higher initial cost, the long-term savings in tool life, machining efficiency, and material waste often outweigh the upfront investment.
Customizable Carbide Blank Dimensions: Key Considerations
Table 1: Factors Influencing Customizable Blank Dimensions
Factor | Description |
---|---|
Material Grade | Different carbide grades have varying machinability characteristics, influencing achievable tolerances and surface finishes. |
Desired Shape & Size | Complexity of the final component geometry and overall dimensions drive blank customization. |
Tolerances | Required precision levels for critical dimensions impact the manufacturing process and cost. |
Surface Finish | Desired surface roughness influences finishing operations and achievable quality. |
Quantity | Production volumes play a role in determining the most cost-effective manufacturing approach. |
Applications: Where Customization Makes a Difference
Customizable carbide blanks find applications in a diverse range of industries:
- Aerospace: Turbine blades, engine components, and structural parts demanding high precision and complex geometries.
- Automotive: Cutting tools for machining engine blocks, transmission components, and other critical parts.
- Medical: Surgical instruments, implants, and dental tools requiring intricate shapes and biocompatible materials.
- Oil & Gas: Downhole drilling tools, wear parts, and valves operating in extreme environments.
- Tool & Die Making: Custom punches, dies, and forming tools for specialized manufacturing processes.
Comparing Suppliers: Navigating the Customizable Carbide Blank
Table 2: A Comparative Analysis of Customizable Carbide Blank Suppliers
Supplier | Location | Price Range (per piece, USD, approximate) | Specialties |
---|---|---|---|
Kennametal | USA | $80 – $1,000+ | Wide range of carbide grades, complex geometries, advanced machining capabilities |
Sandvik Coromant | Sweden | $90 – $1,200+ | Focus on high-performance grades, precision machining, application expertise |
Element Six | UK, Global | $100 – $1,500+ | Expertise in advanced materials, including PCD and CBN, custom tooling solutions |
Ceratizit | Luxembourg | $75 – $900+ | Broad portfolio of carbide grades, competitive pricing for customized solutions |
TRUER | China | $65 – $800+ | Specializes in high-quality blanks, competitive pricing, fast lead times for custom orders |
Note: Prices for custom blanks are highly variable and depend on material grade, complexity, tolerances, quantity, and other factors.
Advantages and Limitations: A Balanced Perspective
Table 3: Weighing the Pros and Cons of Customizable Carbide Blank
Advantages | Limitations |
---|---|
Design Freedom: Enables the creation of components with optimized geometries and features. | Higher Initial Cost: Custom blanks typically have a higher upfront cost compared to standard sizes. |
Enhanced Performance: Tailored designs can improve tool life, cutting efficiency, and part quality. | Longer Lead Times: Custom orders may require longer lead times due to the specialized manufacturing process. |
Material Savings: Near-net-shape blanks minimize material waste and associated costs. | Minimum Order Quantities: Some suppliers may have minimum order requirements for custom blanks. |
Competitive Advantage: Custom solutions can provide a competitive edge in demanding industries. | Design Expertise Required: Effective customization requires engineering knowledge and collaboration with suppliers. |
Beyond Dimensions: The Importance of Material Selection
While Customizable Carbide Blank dimensions offer significant advantages, selecting the right carbide grade is equally crucial. Factors to consider include:
- Wear Resistance: Choose grades with high abrasion resistance for applications involving abrasive materials.
- Toughness: Opt for tougher grades when impact resistance and edge strength are paramount.
- Corrosion Resistance: Select grades specifically designed to withstand corrosive environments.
- Hot Hardness: For high-temperature applications, prioritize grades that maintain hardness at elevated temperatures.
FAQs: Addressing Your Customization Queries
1. What is the smallest possible size for a custom carbide blank?
Minimum achievable sizes depend on the carbide grade, desired tolerances, and manufacturing capabilities. It’s best to consult with a carbide supplier to discuss your specific requirements.
2. What types of shapes can be produced with custom blanks?
Customizable shapes are virtually limitless, including round, square, rectangular, hexagonal, and complex geometries with intricate features.
3. How do I provide my custom blank specifications to a supplier?
Most suppliers accept technical drawings, CAD models, or detailed sketches with precise dimensions and tolerances.
4. What is the typical lead time for custom carbide blanks?
Lead times vary depending on the complexity of the design, material availability, and production capacity. Expect lead times ranging from a few weeks to several months for highly specialized blanks.
5. Can I request a prototype before placing a full production order?
Yes, many suppliers offer prototyping services to ensure the design meets your exact specifications before committing to a large order.