Introduction: The Cornerstone of Performance – Understanding Carbide Hardness
In the realm of materials science and engineering, hardness reigns supreme as a critical indicator of a material’s ability to resist deformation, wear, and tear. This principle holds particularly true for carbide block blanks, the robust foundation upon which countless industrial applications are built. Understanding carbide block blank hardness measurements is paramount for selecting the right material for a specific application and ensuring optimal performance and longevity.
What are Carbide Block Blank Hardness Measurements?
Quantifying Resistance: The Science Behind the Numbers
Carbide block blank hardness measurements quantify a material’s resistance to indentation or scratching. These measurements are crucial for predicting how a carbide blank will perform under various stresses, including:
- Wear Resistance: Harder carbides exhibit superior resistance to abrasive wear, extending tool life and reducing maintenance costs.
- Cutting Performance: Higher hardness translates to sharper cutting edges, enabling cleaner cuts, tighter tolerances, and improved surface finishes.
- Impact Resistance: While not directly correlated, higher hardness often indicates greater resistance to chipping and fracturing under impact loads.
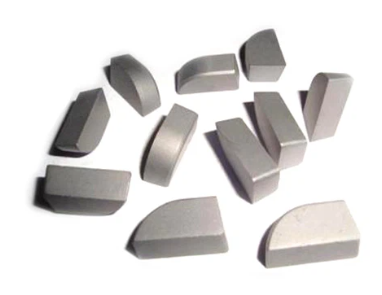
Methods of Measurement: Unveiling the Hardness Secrets
Table 1: Common Hardness Tests for Carbide Block Blanks
Test Method | Description | Scale | Typical Range for Carbide (HV) |
---|---|---|---|
Vickers Hardness (HV) | Measures the indentation size made by a diamond pyramid indenter. | HV | 1200 – 2400 HV |
Rockwell Hardness (HRA) | Measures the depth of penetration of a diamond cone indenter. | HRA | 85 – 95 HRA |
Note: Vickers Hardness (HV) is the most commonly used method for carbide block blanks due to its accuracy and suitability for hard materials.
Factors Influencing Hardness: A Complex Interplay
Beyond the Numbers: Understanding the Underlying Factors
Carbide block blank hardness is not an inherent property but rather a result of complex interactions between various factors during the manufacturing process:
- Carbide Grain Size: Finer carbide grain structures generally result in higher hardness and improved wear resistance.
- Cobalt Content: Cobalt acts as a binder in carbide, with lower cobalt content typically leading to higher hardness but reduced toughness.
- Sintering Temperature and Time: Higher sintering temperatures and longer durations promote densification and grain growth, influencing final hardness.
- Cooling Rate: Rapid cooling rates can result in finer grain structures and increased hardness.
Applications: Where Hardness Dictates Performance
The importance of carbide block blank hardness is reflected in its diverse applications:
- Cutting Tools: Drills, end mills, inserts, and other cutting tools rely on high hardness for wear resistance and cutting efficiency.
- Wear Parts: Components subjected to abrasion, erosion, or high-pressure contact, such as nozzles, dies, and bearings, benefit from hard carbide grades.
- Mining & Construction: Drilling bits, rock crushers, and other equipment used in harsh environments demand exceptional hardness and wear resistance.
Comparing Suppliers: Navigating the Hardness Landscape
Table 2: Carbide Block Blank Suppliers and Hardness Capabilities
Supplier | Location | Typical Hardness Range (HV) | Specialties |
---|---|---|---|
Kennametal | USA | 1200 – 2300 HV | Wide range of carbide grades, advanced material technologies, custom solutions |
Sandvik Coromant | Sweden | 1300 – 2400 HV | Focus on high-performance grades, precision machining, application expertise |
Element Six | UK, Global | 1400 – 2500 HV | Expertise in advanced materials, including PCD and CBN, tailored solutions for demanding applications |
Ceratizit | Luxembourg | 1250 – 2200 HV | Broad portfolio of carbide grades, competitive pricing, customized solutions |
TRUER | China | 1300 – 2300 HV | Specializes in high-quality blanks, competitive pricing, fast lead times for custom orders |
Note: Hardness ranges are approximate and may vary depending on specific carbide grades and manufacturing processes.
Advantages and Limitations: Balancing Hardness and Toughness
Table 3: The Trade-off Between Hardness and Toughness
Advantages of High Hardness | Limitations of High Hardness |
---|---|
Exceptional Wear Resistance: Longer tool life, reduced maintenance, and improved component durability. | Reduced Toughness: Higher susceptibility to chipping and fracturing under impact or shock loads. |
Enhanced Cutting Performance: Sharper cutting edges, cleaner cuts, tighter tolerances, and improved surface finishes. | Increased Brittleness: May require careful handling and machining parameters to prevent breakage. |
Suitable for Abrasive Materials: Excellent performance in applications involving abrasive materials or environments. | Limited Applications: Not ideal for applications where impact resistance or toughness are critical factors. |
Beyond Hardness: The Importance of Comprehensive Material Selection
While hardness is a crucial factor, selecting the optimal carbide block blank involves considering a holistic set of material properties:
- Transverse Rupture Strength (TRS): Measures a material’s resistance to fracture under bending stress, indicating toughness.
- Fracture Toughness: Quantifies a material’s ability to resist crack propagation, crucial for impact-resistant applications.
- Thermal Conductivity: Influences heat dissipation during machining, impacting tool life and workpiece quality.
Why Choose TRUER for Your Carbide Block Blank Needs?
TRUER stands out as a premier supplier of high-quality tungsten carbide products, including carbide block blanks, for several compelling reasons:
- Uncompromising Quality: TRUER utilizes premium raw materials and advanced manufacturing processes to ensure consistent quality and exceptional performance.
- Vertical Integration: With a complete production line, from powder to finished product, TRUER maintains strict control over every stage of the manufacturing process.
- Advanced Technology: TRUER employs state-of-the-art equipment, including electric direct drive automatic presses for high-precision molding, ensuring product consistency and tight tolerances.
- Competitive Pricing: TRUER’s efficient operations and commitment to customer value enable them to offer competitive pricing without compromising quality.
- Customer Focus: TRUER prioritizes customer satisfaction, providing personalized service, technical support, and flexible solutions to meet specific requirements.
FAQs: Addressing Your Carbide Block Blank Hardness Queries
1. What is the ideal hardness for my application?
The optimal hardness depends on the specific application requirements, including the material being machined, cutting parameters, and desired tool life. Consulting with a carbide expert, like those at TRUER, can help determine the most suitable hardness grade.
2. Can the hardness of a carbide block blank be modified after sintering?
While some minor hardness adjustments might be achievable through post-sintering treatments, significant changes are unlikely. Selecting the correct grade during the initial manufacturing process is crucial.
3. How does the hardness of carbide compare to other materials?
Carbide exhibits significantly higher hardness compared to most metals, including steel, stainless steel, and even hardened tool steels. This exceptional hardness makes carbide ideal for wear-resistant and high-performance cutting applications.
4. What is the relationship between hardness and cobalt content in carbide?
Generally, lower cobalt content results in higher hardness but reduced toughness. Finding the right balance between these properties is essential for optimal performance.
5. How can I ensure the accuracy of carbide block blank hardness measurements?
Accurate hardness measurements require calibrated equipment, proper sample preparation, and adherence to standardized testing procedures. Working with reputable suppliers, like TRUER, who prioritize quality control and utilize certified testing methods, ensures reliable and accurate hardness data.
TRUER: Your Partner in Precision Carbide Solutions
TRUER specializes in the production of high-quality tungsten carbide products, including carbide rod strips, indexable inserts, wear parts, and other types of cemented carbide geological mining products. With a commitment to innovation, quality, and customer satisfaction, TRUER is your trusted source for all your carbide needs.