Carbide saw tips enable durable and high performance cutting across demanding metal fabrication, construction, and woodworking trade applications. This guide covers carbide grades and coatings, dimensions, technical specifications, pricing, and comparisons to help buyers select optimized blade tips based on material cut types and thickness.
Introduction to Carbide Saw Tips
Carbide saw tips provide extreme hardness for industrial saw blade integrity and longevity unmatched by other materials such as high speed steel. Key advantages of carbide tips:
- Maintain sharp cutting edge
- Resist abrasive wear
- Withstand high temperatures
- Survive repeated high force impact stresses
This guide covers key factors selecting carbide saw tips:
- Composition Grades and Binders
- Coating Types for Enhanced Protection
- International Standard Size Designations
- Technical Specification Considerations
- Unit Pricing Ranges
- Performance Differences Carbide vs Other Materials
- Pros vs Cons Comparisons by Characteristics
- FAQs on Construction Techniques
Carbide Saw Tip Compositions
Carbide refers to compounds of carbon and heavy materials like tungsten, titanium and tantalum providing extreme hardness and thermal resistance.
Table 1 shows common grades used in saw tips with key characteristics:
Grade | Description |
---|---|
C-1, C-2, C-3 | Pure tungsten carbides suitable for steel |
C-4, C-5 | Mixed carbides with 6% cobalt for high toughness and shock resistance |
C-6 to C-9 | Special complex compositions optimized for difficult materials like wood laminates, fiber cement sheet |
Carbides require cobalt or nickel binder metals to facilitate manufacturing processes – 6-10% typical in saw blade edge tips.
Saw Tip Coating Types
Coatings enhance carbide tip protection:
Table 2
Coating | Attributes |
---|---|
Titanium nitride (TiN) | Gold color; heat and abrasion resistance |
Titanium aluminum nitride (TiAlN) | Violet; heat resistance to 1100°C |
Titanium carbon nitride (TiCN) | Gray; shock and fracture resistance |
Multilayer coatings stack benefits – example TiCN + TiN.
Coatings aid lubricity and dissipate heat from friction during cutting. Select coating suited to cut material properties and specific application demands.
International Standard Carbide Tip Size Designations
Carbide saw blade teeth require precision manufacturing for consistent tool inserts fitting clamping systems across brands.
Table 3 shows industry standard ISO size conventions used globally to classify replaceable carbide tip dimensions. Sizes differ by saw type – miter vs tablesaw vs circular.
Size Class | Length (mm) | Width (mm) |
---|---|---|
ISO No 1 | 9.6 | 3.5 |
ISO No 2 | 11.1 | 4.0 |
ISO No 3 | 12.8 | 4.5 |
ISO No 6 | 16.3 | 5.0 |
ISO No 10 | 20.5 | 6.3 |
Carefully confirm carbide type and tip size designations match tooling systems used on specific saw blade models in inventory. Replacements require high precision manufacturing within 0.02mm size tolerances and exact 45 or 80 degree angle consistency.
Reputable manufacturers provide detailed technical drawings. Validate critical dimensions on certificates.
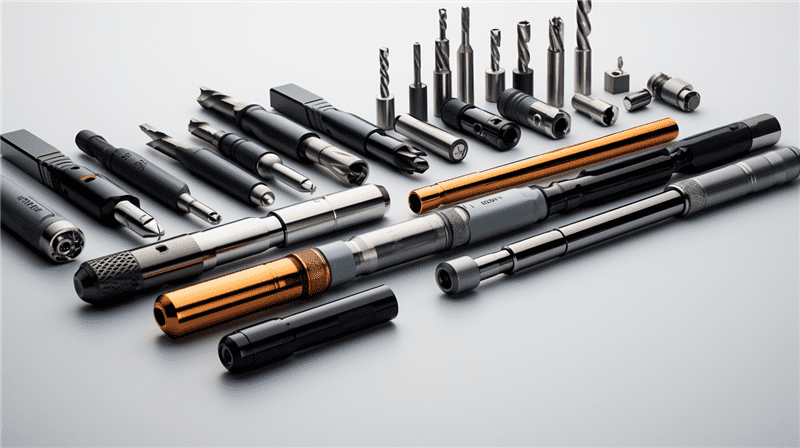
Technical Specification Considerations
Besides composition, coatings and physical size compatibility, additional technical factors matter when evaluating carbide saw blade inserts from suppliers and manufacturers at different tiers:
Table 4
Parameter | Description |
---|---|
Edge Radius | Affects sharpness and brittleness. Larger radiuses withstand higher shock but cut thicker materials. Optimize radius to application. |
Surface Roughness | measured in microns Ra or RMS. Lower roughness enhances cutting action. Under 0.1 um premium. |
Chamfer / Relief Angle | Angled clearance behind cutting edge improves swarf flow. 30 degree tilt common. |
Grade / Concentration Consistency | Minimize porosity and voids. Higher grade powders improve consolidation. |
Grain Structure | Finer uniform carbide grains resist microcracking versus large grains. |
Binder Phase | Too little cobalt risks cracked tips. Too much lowers hardness. Optimized formula critical. |
Thoroughly review technical details and validate conformity through sampling to ensure purchased inserts deliver field performance required. Do not assume all products equal.
Carbide Saw Tip Pricing
Carbide tipped circular saws utilize brazed or clamped on teeth allowing economical replacement refreshing blades versus discarding entire saw bodies.
Table 5 shows rough carbide saw tip pricing under normal market conditions:
Quantity | Price Range |
---|---|
1 – 10 tips | $8 – $12 per tip |
11 – 49 tips | $5 – $8 per tip |
50 – 99 tips | $3 – $5 per tip |
100+ tips | Sub $2 per tip, high volume discounts |
- Per tip pricing shown for ISO No. 2 dimensions
- Small quantities extremely expensive
- Large orders in thousands of units provide 70%+ discounts
- Validate minimum manufacturing batch sizes which affect prototyping costs
Purchasing entire replacement sets simultaneously optimizes value, ensuring matched wear consistency across tips around periphery of saw blade.
Comparing Carbide vs Other Saw Tip Materials
Table 6
Attribute | Carbide Tips | High Speed Steel Tips |
---|---|---|
Hardness | 2800 Vickers typical | 750 Vickers max |
Heat Resistance | Excellent to 1100°C | Fair, loses hardness above 600°C |
Wear Resistance | Extremely high | Moderate, frequent sharpening needed |
Impact Strength | Brittle despite thickness | Highest elasticity and shock tolerance |
Machining Difficulty | Challenging and slow | Easier to produce complex shapes |
Piece Cost | Many times higher | Extremely economical, cost effective |
Suitable Materials | All metals, wood, composites | Wood, soft non-ferrous metals only |
Carbide justify premiums only when cutting ultra hard or thick stock. HSS appropriate for wood or soft, thin non-ferrous cutoff tasks not requiring durability.
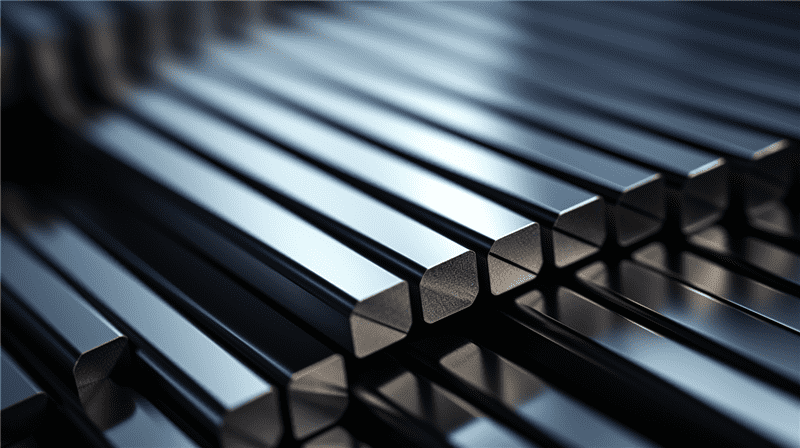
Pros vs Cons of Carbide Saw Tips
Table 7 – Carbide grade variables allow optimizing across tradeoffs:
Advantages | Disadvantages |
---|---|
Extreme hardness and heat resistance | Brittle with sensitive impact tolerances |
Maintains sharp cutting edge | Higher per piece cost |
Long working life if undamaged | Requires advanced bonding technology |
Universal material cut capability | Difficult to sharpen thus replace tips |
By selecting specific binder percentages, grain structure, cutting angles and radius shapes, application-specific tips can balance longevity, precision, speed and cost.
Maximum hardness grades risk fracturing under shocks. Slightly tougher grades with adequate heat tolerance better suit high vibration environments.
FAQs
Table 8 – Carbide saw tip frequently asked questions:
FAQ | Answer |
---|---|
How often should carbide teeth be rotated or replaced? | When cutting rates slow by approx 25%, rotate position or replace if all are worn |
Should I reorder the tungsten carbide grade originally supplied? | Yes, mixing grades risks uneven wear. Reorder identical composition and coating. |
What causes micro-cracking and premature breakage issues? | Usually overheated tips from coolant problems, fast feeds/speeds, or worn bearings increasing friction during cuts |
Is it possible to sharpen carbide tips? | Extremely difficult requiring EDM, special fixtures, diamond wheels – typically not economical vs new tips |