carbide boring bar inserts are cutting tool tips attached to boring bars used to accurately enlarge existing holes to precise diameters and finishes. Hard carbide grades and optimized insert geometries enable efficient boring operations on metals and alloys across industrial machining applications.
This guide covers boring insert specifications, boring bar system configurations, grades and coatings, operational parameters, quality considerations and advice on boring system component selection.
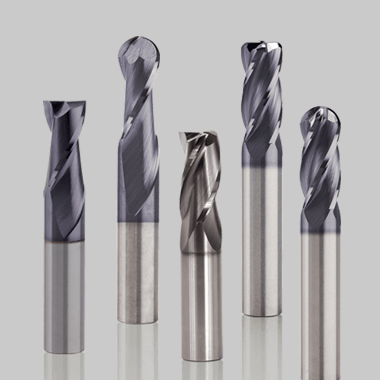
carbide boring bar inserts Types
Common replaceable boring head inserts:
- Singlesided square insert with multiple cutting corners
- Double-sided square insert for rough boring applications
- Single-sided round insert for finishing bores
- Trigon insert with three cutting edges
- Rectangle, rhombic, parallelogram other specialty shapes
Choose insert style based on hole size, tolerance needs and workpiece material. Larger neutral negative rake inserts withstand high feed rates well. Smaller inserts enable tight precision boring.
Boring Bar Toolholders
Carbide inserts precisely lock into these toolholder styles:
- Solid type holders for stiffness and accuracy
- Screw-on block type holders offering high versatility
- Quick change style holders for fast insert indexing
- Special boring bar holders with dampening features
Select toolholders to match insert shape securing it tightly without compromising precision. Consider vibration damping for optimal surface finishes.
Composition and Grades
Made from cemented carbides of:
- Tungsten carbide (WC) providing wear resistance
- Titanium carbide (TiC) for high toughness
- Tantalum carbide (TaC) with good thermal properties
- Niobium carbide (NbC) improving chemical resistance
Binder materials like Cobalt, Nickel and Chrome enable tailoring of hardness, toughness and heat resistance properties.
Common boring insert grades:
Grade | Hardness | Toughness | Comments |
---|---|---|---|
C2/C4 | Hard | Brittle | For soft workpieces <45 HRC. Low speeds, feeds. |
C5/C6 | Medium | Strong | General purpose finishing to semi-roughing |
C7/C8 | Very hard | Brittle | Highly abrasive difficult to machine materials |
Harder grades cut faster but are more prone to chipping requiring conservative operational parameters.
Geometric Characteristics
Parameter | Options | Impact |
---|---|---|
Lead angle/Nose radius | Sharper < 20° or blunter > 30° | Sharp is weaker but low cutting forces suitable for finish passes. Blunt is much stronger for rough boring able to take higher feeds/speeds |
Rake angles | Positive/Neutral/Negative 0°- 25° | More positive rake is better shearing but weaker edge. Negative rake stronger but requires higher cutting forces |
Relief angles | Degree of back taper 5°- 15° | Higher relief angles offer more wear resistance but compromise edge strength |
Chip breakers | Varied notch patterns on rake face | Breaks chips into small segments to prevent long continuous swarf tangling around tool |
Properly match insert geometry to boring bar system rigidity, hole size precision needs and work material hardness characteristics balancing tradeoffs.
Insert Coatings
Common PVD, CVD coatings deposited onto carbide insert substrates to reduce friction and enhance heat resistance:
Coating | Composition | Properties |
---|---|---|
TiAlN | Titanium aluminum nitride | High hardness and heat resistance. Wear protection ~700°C. General machining. |
AlCrN | Aluminum chromium nitride | Tougher coating than TiAlN, stable to higher temperatures 800°C+. Used for steels |
TiN | Titanium nitride | Gold colored standard coating. Stable to ~500°C. Low friction good for aluminum, brass, bronze |
TiCN | Titanium carbon nitride | Good adhesion and lubrication. Used on ferrous metals and nickel alloys |
Coatings help sustain sharp cutting edge and prevent built up edge. Check certification friction testing data. May use multiple layer combinations.
Work Materials
Hardness level determines suitable insert grades and operational parameters:
Category | Materials | Hardness Range | Insert Grades |
---|---|---|---|
Soft low carbon steels, plastic | Carbon steels, alloys steels through 45 HRC; stainless steels, inconels and titanium alloys, graphite composites, plastics. | BHN 100-300. Under HRC 45 | C2, C4 |
Hardened steels and irons, titanium, hastelloys | Through hardened alloy steels 48-65 HRC; pearlitic, martensitic and tool steels; titanium & nickel iron superalloys | BHN Over 300. HRC 48+ | C5, C6, C7+ |
Cast Iron | Gray, ductile, malleable, compacted graphite | 120-450 BHN | C6, C7, C8 |
Assess workpiece material specification hardness carefully before purchase. Harder materials require more precision in operational parameters to prevent premature edge chipping or insert breakage.
Cutting Parameters
Parameter | Finishing | Medium Roughing | Heavy Roughing |
---|---|---|---|
Speed (SFPM) | 400-800 | 600-1000 | 800-1200 |
Feed Rate (IPR) | 0.0005-0.003” | 0.003-0.012” | 0.012-0.025” |
Depth of Cut (IPM) | Under 0.020” | 0.020-0.100” | 0.100-0.400” |
Balance parameters relative to insert style and flank wear requirements to sustain sufficient material removal rates and precision bored finishes and geometries.
Industry Standards
- ISO 1832:2012 – Numbering system for cutting tools
- ANSI B212.4-1986 – Cutting tool inserts shape and size classification
- ISO 513:2002 – Classification and application of hard cutting materials for metal removal with defined cutting edges
- VDI 3323:2018 – Carbide boring bars – Design and application
Review statistical process control batch data against these and other global standards ensuring boring bar tooling quality.
Quality Metrics
- Edge integrity
- Consistent substrate and coating adhesion
- Micro cracking prevention
- Surface finish certification
- Camber, thickness, form geometries
- ISO certification on metalcutting performance
Validate performance consistency across batches, especially for custom boring programs.
Global Suppliers
Leading boring bar cutting tool manufacturers include:
- [Mitsubishi Carbide]
- [Kennametal]
- [Korloy Inc.]
- [Tungaloy America Inc]
- [Iscar Metals Inc.]
Evaluate supplier consistency to quality metrics above supported by statistical batch data and customer references before purchase across locations.
Cost Considerations
carbide boring bar inserts range from:
- $5 – $20 per insert for standard geometries and common sizes
- $30+ for specialized custom insert designs and dimensions
- $100+ for solid carbide one-piece adjustable boring heads
Compare rates across shortlisted vendors aligned to quantity and certification requirements. Consider custom boring needs but start testing with standard catalog inserts first to establish optimal grade and geometry.
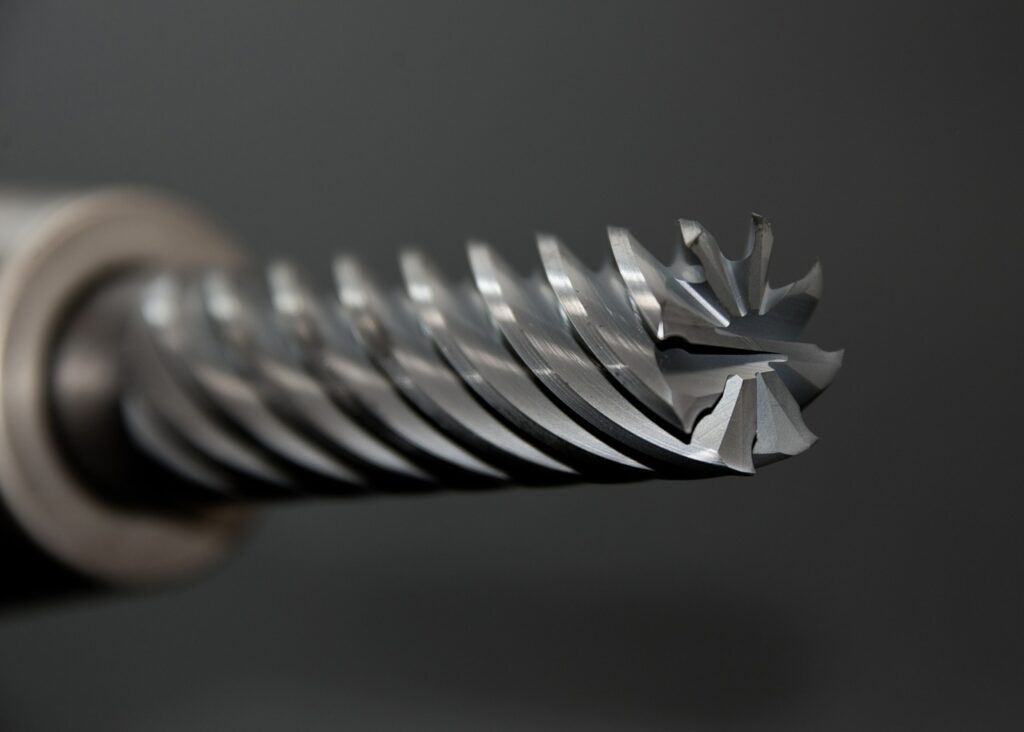
Buying Criteria
Parameter | Importance |
---|---|
Technical Datasheets | High |
Grade Availability | High |
Consistency | High |
Location | Medium |
Pricing | Low |
Vendor Comparison
Manufacturer | Range Offered | Lead Times | Pricing | Technical Expertise |
---|---|---|---|---|
[Kennametal] | Broad application coverage | Custom quote 2 weeks | 100 | Industry leader with proven results |
[ARCH®] | Focus on steel boring | Stock ship within 5 days | 9 | Limited boring application experience |
[TRUER] | General boring needs | 2 week manufacturing | 50 | Wide range of indexable tooling lineup |
Choose most experienced carbide boring bar cutting tool partner with stringent manufacturing quality systems aligned to work metals, hole specifications and delivery constraints.
FAQs
Q: What is the best insert shape for precision boring bars?
A: Round inserts offer the most precise boring finish quality and dimensional accuracy for small boring bars, while triangular inserts maximize stiffness offering faster MRR in larger rough boring bars.
Q: How long do carbide boring bar inserts last?
A: Carbide boring life depends significantly on work material hardness and operating parameters. At conservative speeds, feeds and depths of cut, boring tool life between 60-90 minutes of cutting time can be expected from a sharp carbide insert.
Q: What causes early boring insert failure?
A: The main causes of premature boring insert breakage or rapid wear are insufficient rigidity in the boring bar system relative to operational forces and hardness or abrasiveness of the workpiece material requiring reduced feeds/speeds.
Q: How are boring bars resharpened?
A: Indexable inserts are designed to be replaced after dulling while the toolholder boring bar is reused indefinitely. Brazed tip bars may be detachable and retipped while solid carbide bars require grinding equipment to resharpen tips as needed over time.