Tungsten carbide plates deliver extreme hardness, strength and wear resistance for the most demanding industrial applications. This guide provides an overview of grades, properties, manufacturing processes, sizes, finishing options and comparative assessment.
Overview of tungsten carbide plate
Tungsten carbide (WC) plates offer unmatched performance under harsh conditions:
Composition | Tungsten carbide particles in cobalt binder matrix |
Hardness | Up to 92 HRA |
Wear resistance | Hundreds of times higher than alloy steels |
Manufacturing | Powder metallurgy compaction followed by sintering |
Typical applications | Mining, mineral processing, pulp and paper |
Key benefits | Extreme hardness, abrasion resistance, thermal/impact stress resilience |
In plate form factors, tungsten carbide enables localized wear protection and enhanced longevity for critical equipment across extraction and bulk materials handling industries.
tungsten carbide plate Types
Grade | Hardness Range | Key Properties |
---|---|---|
Simplex | 88-92 HRA | Highest hardness and wear resistance suitable for fine particle erosion |
Duplex | 82-88 HRA | Good combination of hardness and moderate impact strength |
Standard | 78-85 HRA | Most widely used grade balancing hardness, strength and cost |
Grain size, binder percentage and additional alloying enables tailored grades from fine grained high hardness to more shock resistant variants.
Mechanical Properties
Property | Typical Values |
---|---|
Hardness | 80-92 HRA |
Transverse rupture strength | 2-3 GPa |
Fracture toughness | 8-12 MPa√m |
Young’s modulus | ~550 GPa |
Properties vary based on carbide grain size, cobalt percentage and microstructural uniformity influenced by manufacturing process controls.
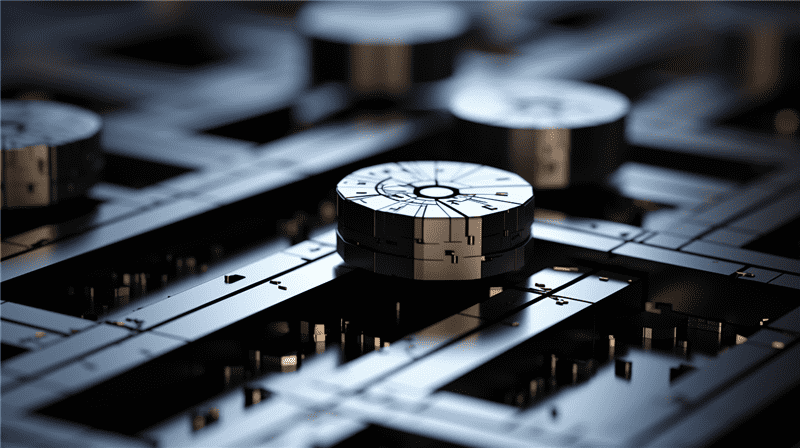
Size Availability
Standard plate sizes:
Thickness | Plates sizes |
---|---|
3-6 mm | Up to 200mm x 200mm |
8-11 mm | Up to 100mm x 100mm |
Larger plates up to 400mm x 400mm sizes possible depending on thickness. Custom machining and hole drilling services enable application-specific configurations.
Manufacturing Process
Step | Description |
---|---|
Milling | Raw material powder particles size reduced via wet or dry milling |
Spray drying | Granulation into spherical agglomerates feeding pressing operation |
Compaction | Cold/hot isostatic pressing forms green body |
Dewax | Removes polymer binders before sintering |
Sintering | 1400-1500°C consolidates to near full density |
Finishing | Grinding, lapping, EDM and other machining processes |
Strict process controls during compaction, dewax and sintering are vital to achieve uniform microstructure and minimize defects.
Finishing Options
Treatment | Function |
---|---|
Grinding | High precision thickness and flatness control |
Lapping | Superfine surface finish down to <0.5 micron roughness |
Polishing | Mirror surface finishes |
Surface coatings | Enhanced galling resistance, friction and wear performance |
Combinations of mechanical, chemical and thermal finishing processes impart tailored functional enhancements aligned to wearing duty and environmental conditions.
Leading Manufacturers
Company | ||
---|---|---|
Kennametal | Widest grade range | Large custom plate fabrication |
Sandvik | High performance oil and gas plates | Stringent quality assurance |
Ceratizit | Specialized wood and paper industry plates | Cost competitive |
Mitsubishi Materials | Reputable mining segment plates | Advanced cobalt gradient bonds |
Application-specific custom plate development leveraging proprietary grade and processing know-how. Harsher environments justify premium grades and tightly controlled QA.
Comparative Assessment
Carbon Steels | Stainless Steels | Cast Alloys | |
---|---|---|---|
Wear resistance | Low | Medium | High |
Toughness | High | Medium | Low |
Fabrication | Easy | Moderate | Difficult |
Cost | Low | Moderate | High |
Key Takeaways
- Rigorous QA to minimize defects is imperative with large WC plates
- No alternative offers wear capabilities equivalent to thick tungsten carbide
- Proper grade matching and machining finishing is crucial
FAQs
Q: What industries use tungsten carbide plating?
A: Mining, dredging, minerals processing and pulp/paper industries leverage tungsten carbide plates for unparalleled erosion, abrasion and impact resistance
Q: How do you attach tungsten carbide plates?
A: Plates are usually affixed via shielded metal arc welding, bolt through anchors, or specially formulated high strength adhesive bonding dependent on requirements.
Q: How thick can tungsten carbide plates be made?
A: While plates over 25mm introduce quality challenges during manufacturing, specialized processes have demonstrated capability up to 75-100mm thickness ranges.
Q: Can other hard materials substitute for tungsten carbide plates?
A: Only chromium carbide overlays offer comparability with slightly lower wear rates but easier application via thermal spray coatings rather than welded plates.