Imagine you’re a sculptor, meticulously shaping a piece of granite. But instead of a hammer and chisel, you wield a high-powered machine. That’s the world of metal machining, and carbide milling inserts are the sculptor’s sharp tools, meticulously removing excess material to create precise shapes.
What are Carbide Milling Inserts?
Carbide milling inserts are small, replaceable cutting tools used in milling machines. They’re typically crafted from tungsten carbide, an incredibly hard and wear-resistant material that can withstand the intense heat and friction generated during metal cutting. Think of them as the workhorses of milling operations, delivering superior performance and extended tool life compared to traditional high-speed steel tools.
Types of Carbide Milling Inserts
Carbide milling inserts come in a diverse range to tackle various machining tasks. Here’s a glimpse into the most common types:
Type | Description | Applications |
---|---|---|
Face Milling Inserts | Feature a large cutting surface for efficient removal of material across flat surfaces. | Machining large, flat areas on plates, blocks, and castings. |
End Milling Inserts | Possess a single cutting end for precise milling of pockets, slots, and profiles. | Milling intricate features, grooves, and cavities. |
Ball Nose Milling Inserts | Have a rounded cutting edge ideal for creating curved surfaces and contours. | Contour milling, finishing operations, and creating radii. |
Shoulder Milling Inserts | Incorporate a distinct shoulder for machining precise depths and creating square edges. | Slotting, profiling, and creating steps and ledges. |
Corner Radius Milling Inserts | Boast a rounded corner for generating smooth transitions and reducing stress concentrations. | Finishing delicate edges, chamfering, and reducing machining marks. |
This is just a sampling; the world of carbide milling inserts offers a vast selection to address specific machining requirements.
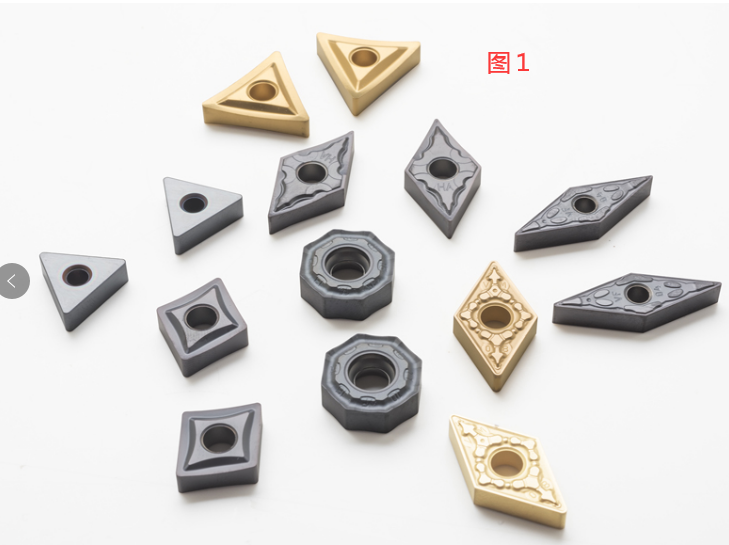
Understanding Carbide Insert Composition and Properties
The magic behind carbide milling inserts lies in their unique composition. Tungsten carbide, the primary ingredient, is a ceramic material renowned for its exceptional hardness, exceeding even that of steel. However, raw tungsten carbide is inherently brittle. To address this, it’s bonded with a metallic binder, typically cobalt, creating a composite material that retains the hardness of tungsten carbide while offering improved toughness and fracture resistance.
The specific composition and ratio of tungsten carbide to cobalt determine the insert’s grade. Higher tungsten carbide content translates to greater hardness and wear resistance, ideal for machining tough materials like steel. Conversely, a higher cobalt content enhances toughness, making the insert more suitable for interrupted cuts or shock-prone applications.
Here’s a table outlining some key properties of carbide milling inserts:
Property | Description | Impact on Machining |
---|---|---|
Hardness | Resistance to permanent indentation. | Enables machining of hard materials with minimal insert wear. |
Toughness | Ability to absorb energy and resist fracture. | Crucial for withstanding shock loads and interrupted cuts. |
Wear Resistance | Ability to maintain cutting edge sharpness over time. | Influences tool life and the quality of the machined surface. |
Heat Resistance | Capacity to withstand high temperatures generated during cutting. | Ensures optimal performance and prevents insert degradation. |
The Applications of Carbide Milling Inserts
Carbide milling inserts are the go-to choice for various metal machining applications. Their versatility shines across different industries:
Industry | Applications | Benefits |
---|---|---|
Automotive | Engine components, transmission parts, molds, and dies. | High-precision machining, extended tool life, and excellent surface finish. |
Aerospace | Landing gear components, wing structures, and engine parts. | Superior wear resistance for machining high-strength alloys. |
Mold Making | Injection mold cavities, cores, and mold bases. | Exceptional dimensional accuracy and smooth finishes for high-quality mold production. |
General Machining | Gears, shafts, flanges, and various machined parts. | Cost-effective solution for a wide range of machining tasks. |
Carbide Milling Insert Specifications, Sizes, and Grades
Carbide milling inserts come in a plethora of sizes and grades to cater to diverse machining needs. Here’s a breakdown of some key specifications:
- Insert Size (IC): This refers to the insert’s overall dimensions, designated by a standardized code. Common sizes include APKT, VP15TF, and SEHL. Selecting the appropriate size depends on the workpiece dimensions, depth of cut, and desired machining characteristics.
- Insert Thickness (IC): This indicates the insert’s width, impacting the rigidity and stability during cutting. Thicker inserts are better suited for heavy-duty machining, while thinner inserts offer improved chip evacuation for finer finishes.
- Corner Radius (R): The radius of the insert’s cutting edge, influencing the profile of the machined surface. Smaller radii generate sharper corners, while larger radii create smoother transitions.
- Grade: As mentioned earlier, the grade signifies the insert’s composition, specifically the tungsten carbide to cobalt ratio. Popular grades include ISO K-〇〇 (for steel machining), ISO M-〇〇 (for cast iron), and ISO N-〇〇 (for non-ferrous materials).
Here’s a table to illustrate the concept of grades:
Grade | Application | Description |
---|---|---|
ISO K10 | Steel Machining (General Purpose) | Balanced combination of hardness and toughness for various steel types. |
ISO K20 | Steel Machining (Tough Steels) | Higher cobalt content for improved toughness when machining high-strength or abrasive steels. |
ISO K30 | Steel Machining (Finishing) | Increased tungsten carbide content for exceptional hardness and wear resistance, ideal for finishing cuts on steel. |
ISO M20 | Cast Iron Machining | Optimized for machining cast iron, with properties that prevent chipping and edge breakage. |
ISO N30 | Non-Ferrous Machining | Tailored for machining aluminum, copper, and other soft metals, ensuring clean cuts and minimal tool wear. |
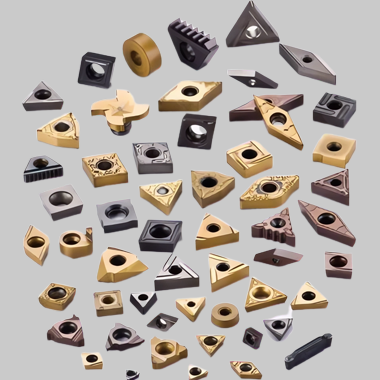
Carbide Milling Insert Suppliers and Pricing
Carbide milling inserts are readily available from a wide range of industrial tool suppliers. Here’s a glimpse into some prominent players:
- Kennametal
- Sandvik Coromant
- Seco Tools
- Walter Technologies
- Mitsubishi Materials (Mitsubishi Carbide)
- OSG Corporation
- Iscar Ltd.
Pricing for carbide milling inserts can vary considerably depending on the insert size, grade, coating (if applicable), and brand. Generally, larger and higher-grade inserts with specialized coatings will command a higher price. A typical carbide milling insert can range from around $20 to $200, with some specialty inserts reaching even higher costs.
Carbide Milling Inserts: Pros and Cons
While carbide milling inserts offer numerous advantages, it’s essential to consider their limitations for informed decision-making.
Pros
- Exceptional Wear Resistance: Carbide’s inherent hardness translates to extended tool life, reducing downtime for insert changes and lowering overall machining costs.
- Superior Machining Performance: The ability to withstand high temperatures enables faster cutting speeds and improved surface finishes on machined parts.
- Versatility: The wide variety of insert types, sizes, and grades caters to a broad spectrum of machining applications.
- Dimensional Accuracy: Carbide inserts maintain their sharp edges during cutting, leading to precise and consistent machining dimensions.
Cons
- Higher Initial Cost: Compared to traditional high-speed steel tools, carbide milling inserts carry a higher upfront cost.
- Brittleness: While tougher than raw tungsten carbide, inserts can still chip or fracture under excessive impact or improper machining conditions.
- Heat Sensitivity: Though heat resistant, prolonged exposure to extreme temperatures can weaken the insert and accelerate wear.
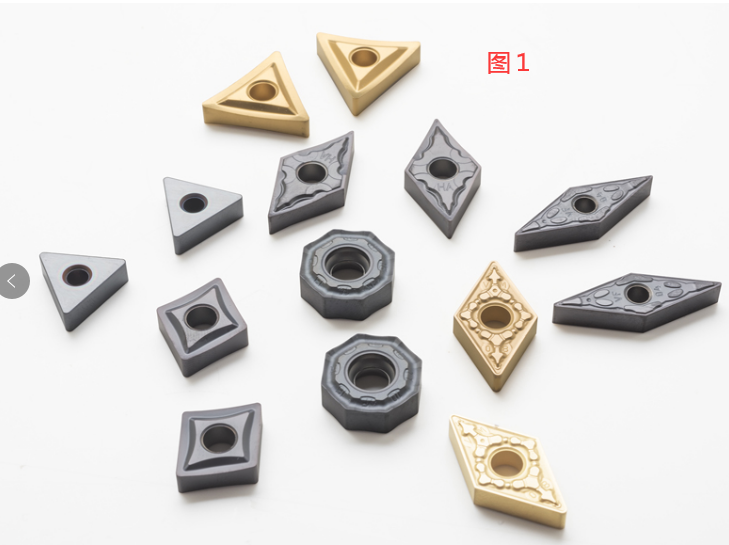
FAQ
Here are some frequently asked questions regarding carbide milling inserts, presented in a table format for easy reference:
Question | Answer |
---|---|
What are the benefits of using carbide milling inserts? | Superior wear resistance, improved machining performance, versatility, and dimensional accuracy. |
How do I choose the right carbide milling insert for my application? | Consider the material being machined, the desired surface finish, and the specific machining operation. Factors like insert size, grade, and corner radius also play a crucial role. |
Can I use carbide milling inserts for all types of metals? | Yes, but different grades are optimized for specific metals. For instance, some grades excel at machining steel, while others are better suited for cast iron or non-ferrous materials. |
How long do carbide milling inserts last? | The lifespan depends on various factors like machining conditions, material being cut, and insert grade. However, carbide inserts generally offer significantly longer tool life compared to high-speed steel tools. |