Imagine a tiny warrior, forged from a blend of extreme hardness and remarkable toughness, capable of conquering even the most stubborn metals with unwavering precision. That’s the essence of a carbide machining insert, a small but mighty player in the world of metalworking.
The Characteristics of Carbide Machining Inserts
Characteristic | Description |
---|---|
Composition | Primarily composed of tungsten carbide (WC), a ceramic material renowned for its exceptional hardness and wear resistance. Additional elements like cobalt (Co) and tantalum carbide (TaC) are often incorporated to fine-tune specific properties. |
Hardness | Boasts a Rockwell hardness (HR) exceeding 90, significantly surpassing even the toughest steels. This translates to the ability to withstand extreme cutting forces and maintain sharp edges for extended periods. |
Toughness | While hardness signifies the resistance to penetration, toughness represents the material’s ability to absorb energy and resist fracturing. Carbide inserts strike a remarkable balance between these two crucial properties, allowing them to tackle challenging materials and machining operations effectively. |
Heat Resistance | Carbide exhibits superior heat resistance compared to traditional tool materials like high-speed steel (HSS). This characteristic minimizes tool wear and ensures dimensional accuracy during high-speed machining processes. |
Chemical Resistance | Carbide demonstrates commendable resistance to chemical degradation, particularly when compared to HSS. This attribute makes it well-suited for machining various metals, including those prone to work hardening and chip welding. |
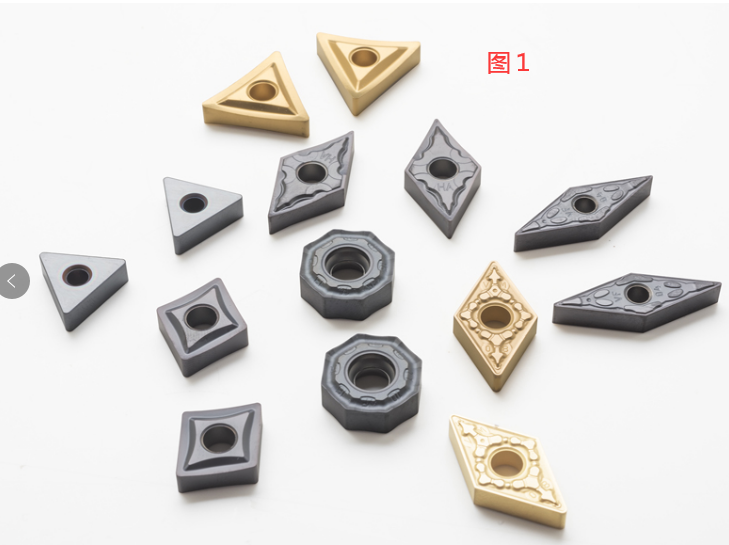
The Applications of Carbide Machining Inserts
Carbide machining inserts find application in a diverse range of metalworking operations, including:
Application | Description |
---|---|
Turning | Used for shaping and reducing the diameter of a rotating workpiece. Inserts are mounted on lathe tools and engage the workpiece at various points to achieve the desired profile. |
Milling | Employed in milling machines to remove material from a workpiece using a rotating tool with multiple cutting edges. Inserts are brazed or clamped onto the milling cutter, significantly enhancing its lifespan and performance. |
Facing | Employed to create a flat and smooth surface on a workpiece. Facing inserts are specifically designed for this purpose and offer exceptional wear resistance for extended operation. |
Boring | Used to enlarge existing holes in a workpiece precisely. Boring inserts possess high dimensional stability and ensure accurate hole geometries. |
Grooving | Employed to create narrow channels or grooves on a workpiece surface. Grooving inserts come in various shapes and sizes to accommodate different groove profiles. |
Threading | Employed to create external or internal threads on a workpiece. Threading inserts feature specialized geometries that precisely match the desired thread profile. |
The Production Method of Carbide Machining Inserts
The creation of carbide machining inserts involves a meticulous process that combines cutting-edge technology with precise craftsmanship:
- Powder Preparation: Raw materials like tungsten carbide, cobalt, and other additives are transformed into fine powders with specific particle size distributions and chemical compositions.
- Mixing and Pressing: The prepared powders are meticulously weighed and blended to achieve the desired material properties. The mixture is then compacted under high pressure into the near-net shape of the insert.
- Sintering: The compacted shapes undergo a high-temperature heating process (sintering) in a controlled atmosphere. This process fuses the powder particles together, forming a solid and dense carbide body.
- Grinding: The sintered inserts are precisely ground using specialized grinding wheels to achieve the final dimensions, tolerances, and cutting edge geometries.
- Coating: In many cases, the inserts are coated with a thin layer of ceramic or metallic material (e.g., titanium nitride (TiN), titanium aluminum nitride (TiAlN)) using techniques like physical vapor deposition (PVD) or chemical vapor deposition (CVD). These coatings further enhance wear resistance, heat resistance, and chip flow characteristics.
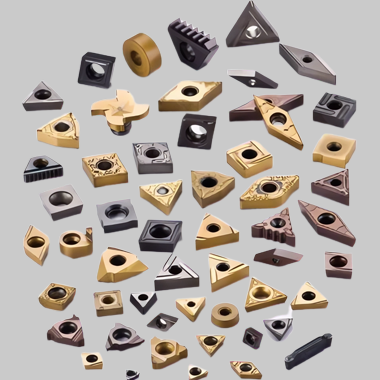
A Multitude of Metal Powders
The performance and suitability of carbide machining inserts hinge significantly on the specific metal powders employed in their fabrication. Here’s a glimpse into ten commonly utilized metal powders and their distinctive characteristics:
Metal Powder | Description | Applications |
---|---|---|
Tungsten Carbide (WC) | The cornerstone of carbide inserts, offering exceptional hardness, wear resistance, and red hardness (the ability to retain hardness at elevated temperatures). | Found in virtually all carbide inserts, particularly suitable for machining ferrous materials like steel and cast iron. |
Cobalt (Co) | Acts as a binder, holding the WC particles together and contributing to the overall toughness of the insert. The cobalt content significantly influences the insert’s wear resistance, toughness, and fracture resistance. | Inserts with higher cobalt content |
Cobalt (Co) | – Higher cobalt content generally translates to improved toughness and fracture resistance but comes at the expense of slightly lower hardness. | Inserts with balanced cobalt content are ideal for a wide range of machining operations, while those with a higher cobalt content are preferred for applications demanding high impact resistance, such as interrupted cuts or machining of tough materials. |
Tantalum Carbide (TaC) | Renowned for its exceptional chemical stability, particularly against abrasive materials like aluminum and silicon. It also contributes to improved wear resistance and crater resistance. | Primarily used in inserts designed for machining aluminum alloys, silicon-rich cast iron, and other abrasive materials. |
Titanium Carbide (TiC) Offers a combination of high hardness, wear resistance, and good chemical stability. It also enhances crater wear resistance and exhibits excellent performance at elevated temperatures. | Utilized in inserts for machining various materials, including steel, stainless steel, and nickel alloys, particularly at high cutting speeds and temperatures. | |
Niobium Carbide (NbC) Possesses superior oxidation resistance and high-temperature strength, making it suitable for high-speed machining applications. | Primarily used in inserts designed for high-speed machining of steels and nickel alloys, where heat generation is a significant concern. | |
Aluminum Oxide (Al2O3) Known for its excellent chemical stability and wear resistance, particularly against abrasive materials like aluminum and silicon carbide. | Employed in inserts specifically designed for machining aluminum alloys and other abrasive materials. | |
Silicon Carbide (SiC) Exceptionally hard and wear-resistant, particularly effective against abrasive materials like composites and ceramics. | Primarily used in inserts for machining advanced materials like metal matrix composites (MMCs) and fiber-reinforced plastics (FRPs). | |
Boron Nitride (BN) Offers superior lubricity and chemical stability, making it suitable for machining sticky materials prone to chip welding. | Employed in inserts designed for machining difficult-to-cut materials like nickel alloys, titanium alloys, and magnesium alloys. |
Specifications, Sizes, Grades, and Standards
The selection of appropriate carbide machining inserts involves considering various factors, including:
- Insert size: Inserts come in various standardized sizes (e.g., ISO, ANSI) to fit specific tool holders and applications.
- Insert grade: Different insert grades are formulated with varying combinations of metal powders to cater to specific machining requirements. Common grading systems include ISO and proprietary systems from individual manufacturers.
- Cutting edge geometry: The geometry of the cutting edge significantly influences chip formation, cutting forces, and surface finish. Common geometries include negative rake angles, positive rake angles, and chip breakers.
- Coating: The type of coating applied to the insert can significantly impact its performance. Common coatings include TiN, TiAlN, and diamond-like carbon (DLC).
Suppliers and Pricing
Carbide machining inserts are readily available from a wide range of global and regional suppliers. Pricing varies depending on factors like insert size, grade, coating, and brand. Here’s a brief overview of some prominent suppliers:
- Kennamétal
- Sandvik Coromant
- Mitsubishi Materials
- Sumitomo Tool
- OSCARbide
- Iscar
- Walter
- Seco Tools
It’s crucial to consult with reputable suppliers and leverage their expertise to select the most suitable inserts for your specific machining requirements.
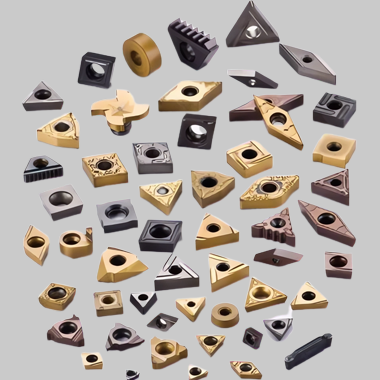
The Pros and Cons of Carbide Machining Inserts
Pros:
- Exceptional hardness and wear resistance: Enables longer tool life and reduces downtime for tool changes.
- Improved machining efficiency: Allows for higher cutting speeds and feed rates, leading to faster production times.
- Superior surface finish: Contributes to high-quality machined parts with minimal surface imperfections.
- Dimensional accuracy: Maintains consistent tool dimensions for precise machining results.
- Versatility: Available in a wide range of sizes, grades, and geometries to suit diverse machining applications.
Cons:
- Higher initial cost: Compared to traditional tool materials like HSS, carbide inserts typically have a higher upfront cost.
- Brittleness: Carbide inserts can be susceptible to chipping or fracturing under excessive impact or shock loads.
- Requirement for specialized tooling: Carbide inserts necessitate compatible tool holders and machining equipment designed to handle their specific characteristics.
FAQ
Q: What are the different factors to consider when choosing carbide machining inserts?
A: Several factors should be taken into account when selecting carbide machining inserts, including:
- Workpiece material: Different insert grades are formulated to excel when machining specific materials like steel, stainless steel, aluminum, cast iron, and more.
- Machining operation: The type of machining operation (turning, milling, facing, etc.) will influence the appropriate insert geometry and size.
- Cutting speed and feed rate: Higher cutting speeds and feed rates often necessitate inserts with specific properties like higher hardness and wear resistance.
- Machining environment: Factors like coolant type and presence of interruptions (e.g., interrupted cuts) can influence insert selection.
Q: How long do carbide machining inserts last?
A: The lifespan of a carbide machining insert depends significantly on various factors, including:
- Workpiece material and hardness: Machining harder materials generally leads to faster insert wear.
- Cutting parameters: Higher cutting speeds and feed rates typically result in shorter insert life.
- Coolant application: Proper coolant application can significantly extend insert life by reducing heat generation and chip welding.
- Machining conditions: Factors like vibration and excessive tool deflection can accelerate insert wear.
As a general guideline, carbide inserts can last significantly longer than traditional tool materials like HSS, with some inserts capable of operating for hours or even days depending on the application. However, it’s crucial to monitor insert wear and replace them promptly to maintain optimal machining performance and avoid potential workpiece damage.
Q: Can carbide machining inserts be recycled?
A: While not as readily recyclable as some other materials, carbide inserts can be recycled through specialized processes. Reputable insert manufacturers often offer recycling programs where used inserts are collected and reprocessed into new inserts or other carbide products. Recycling not only benefits the environment by reducing waste but can also provide cost savings for manufacturers.
Conclusion
Carbide machining inserts have revolutionized the metalworking industry, offering exceptional performance, efficiency, and precision. By understanding their characteristics, applications, and selection factors, machinists can leverage the full potential of these workhorses to achieve superior results and enhance their overall productivity.
Remember, selecting the right carbide machining insert for your specific needs is crucial. Consulting with reputable suppliers and experienced machinists is highly recommended to ensure you make the most informed decision for your unique machining requirements.