Carbide strips are an indispensable component in modern industries, ranging from tooling to heavy manufacturing. But what makes these strips so special? Why are they the go-to choice for many applications requiring hardness and durability? This guide will walk you through everything you need to know about carbide strips, their raw materials, applications, properties, and even how to select the perfect one for your needs.
What Are Carbide Strips?
Carbide strips are high-performance components made from tungsten carbide, a metal matrix composite known for its exceptional hardness, wear resistance, and strength. These strips are primarily used in industrial cutting tools, machining, mining, and wear-resistant applications. Their reliability and performance make them stand out in demanding environments.
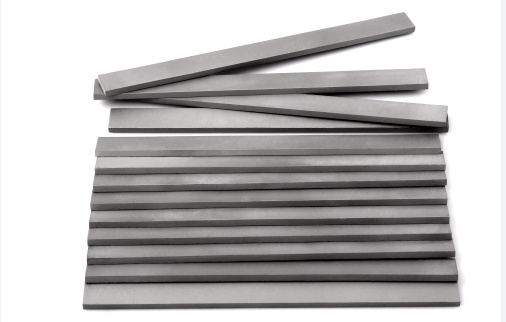
Types of Carbide Strips
Type | Primary Use | Key Features |
---|---|---|
Standard Carbide Strips | General-purpose machining | Durable, versatile |
Abrasion-Resistant Strips | Mining and excavation | High wear resistance |
Heat-Resistant Strips | High-temperature applications | Retain strength at high temps |
Corrosion-Resistant Strips | Chemical environments | Anti-corrosion properties |
Customized Strips | Special tooling requirements | Tailored dimensions and grades |
Raw Material and Composition Analysis of Carbide Strips
Carbide strips are primarily composed of tungsten carbide (WC), combined with cobalt as a binder. This matrix gives the strips a unique balance of hardness and toughness.
Key Raw Materials:
- Tungsten Carbide Powder: The core ingredient providing hardness.
- Cobalt: Acts as a binder, enhancing toughness.
- Other Additives: Nickel or chromium may be added for specific properties like corrosion resistance.
Material | Function | Contribution |
---|---|---|
Tungsten Carbide (WC) | Base material for hardness | Exceptional wear resistance |
Cobalt (Co) | Binder | Improved toughness |
Chromium/Nickel | Optional additives | Corrosion and oxidation resistance |
Applications of Carbide Strips
Application | Industry | Advantages |
---|---|---|
Cutting and Machining Tools | Manufacturing, Tooling | Precise cutting, long-lasting edges |
Mining Equipment | Mining and Excavation | High wear resistance, durability |
Heat-Resistant Components | Aerospace, Industrial Furnaces | Stable at high temperatures |
Wear Parts | Automotive, Heavy Machinery | Longevity in harsh conditions |
Specialized Cutting Tools | Carpentry, Masonry | Consistent performance on hard materials |
Carbide strips are popular in industries that demand performance under pressure. For example, in mining, these strips withstand extreme abrasion while maintaining structural integrity, unlike many other materials.
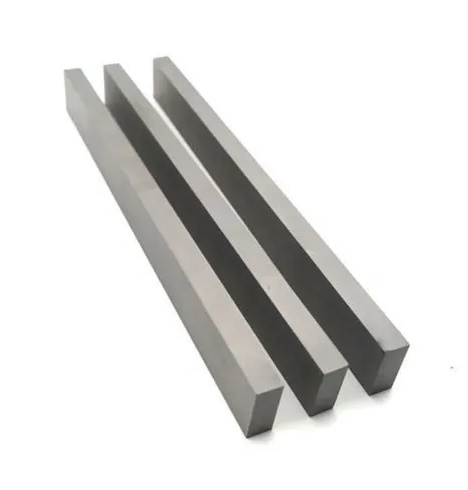
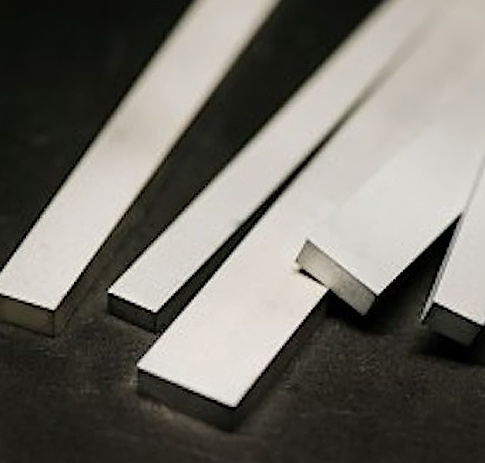
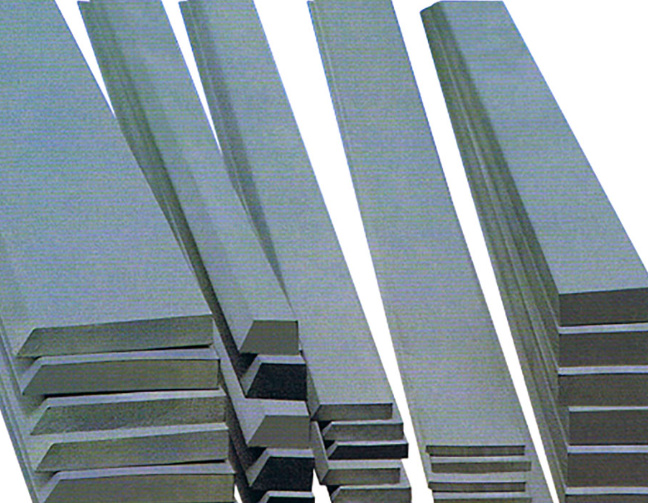
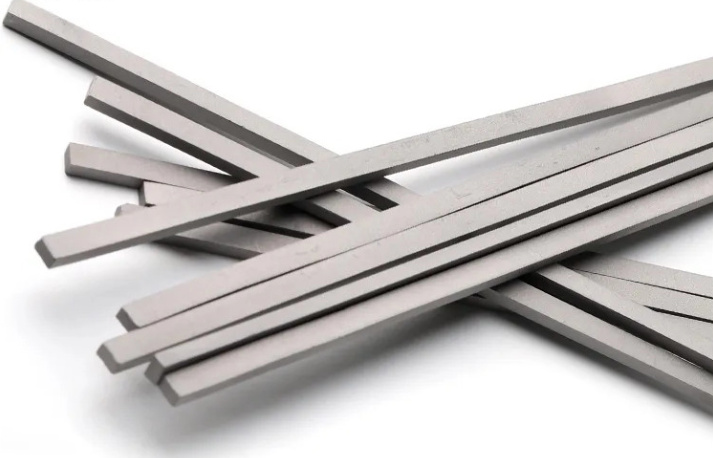
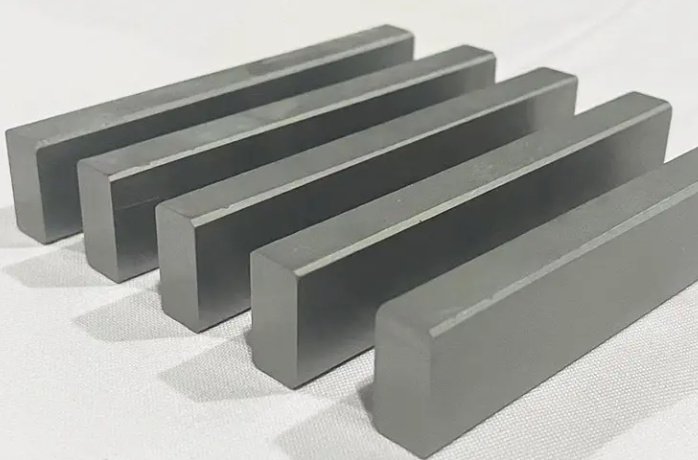
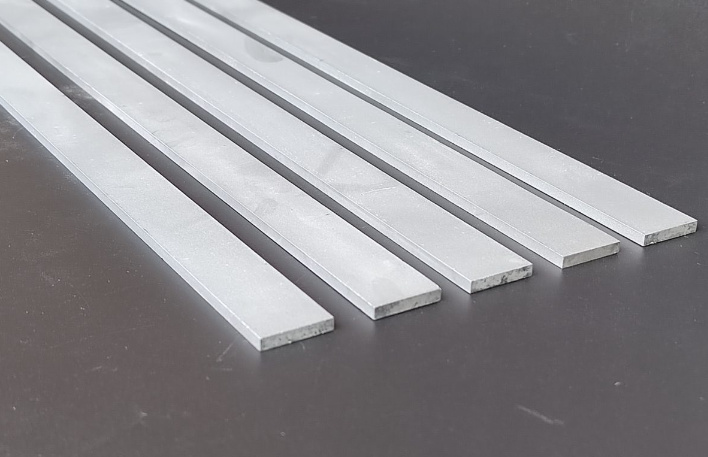
Production Process Flow of Carbide Strips
Step-by-Step Manufacturing Process:
- Powder Preparation: Tungsten carbide powder is mixed with cobalt and any other additives.
- Pressing: The mixture is pressed into strip molds under high pressure.
- Sintering: The pressed strips are heated to high temperatures in a controlled environment to achieve full density and desired properties.
- Grinding and Finishing: The strips are precision-ground to meet required dimensions and surface finish standards.
- Inspection: Rigorous quality checks ensure compliance with industry standards.
Process Step | Details |
---|---|
Powder Preparation | Homogeneous mixing for consistency |
Pressing | High-pressure forming |
Sintering | Densification through heat |
Grinding | Precision dimensioning |
Inspection | Quality assurance |
Material Properties of Carbide Strips
Property | Value Range |
---|---|
Hardness (HRA) | 89-93 |
Density (g/cm³) | 14.4-15.3 |
Flexural Strength (MPa) | 2000-4000 |
Compressive Strength (MPa) | >5000 |
Thermal Conductivity (W/mK) | 50-90 |
Composition, Properties, and Characteristics
Composition | Hardness | Toughness | Wear Resistance | Key Application |
---|---|---|---|---|
90% WC, 10% Co | Very High | Moderate | Exceptional | General machining |
92% WC, 8% Co | High | High | High | Mining tools |
85% WC, 15% Co | Moderate | High | Good | Heavy-duty cutting |
Hardness, Strength, and Wear Resistance
Grade | Hardness (HRA) | Flexural Strength (MPa) | Wear Resistance |
---|---|---|---|
YG6 | 90 | 2400 | Excellent |
YG8 | 89 | 2800 | Very Good |
YG15 | 87 | 4000 | Good for impact resistance |
Specifications, Sizes, Shapes, and Standards
Specification | Size (mm) | Shape | Standard |
---|---|---|---|
Rectangular Strips | 3x20x200 | Flat | ISO 9001 |
Tapered Strips | Custom sizes | Customizable | Industry-specific |
Round-edged Strips | Diameter: 5-50 | Rounded corners | ANSI Standards |
Suppliers and Pricing Details
Supplier | Location | Price Range (per kg) | Special Features |
---|---|---|---|
ABC Carbide Co. | USA | $30-$50 | High precision tooling |
Global Carbides Ltd. | Germany | $40-$60 | Customizable grades |
TungstenPro Inc. | China | $20-$40 | Bulk discounts available |
How to Select the Right Carbide Strips
Criteria | Consideration |
---|---|
Application Requirements | Abrasion, heat, or corrosion resistance? |
Grade Selection | Balance of hardness and toughness for the task. |
Dimensions | Ensure compatibility with tooling or machine setups. |
Cost Considerations | Budget vs. performance trade-offs. |
Supplier Reputation | Ensure reliable and consistent quality. |
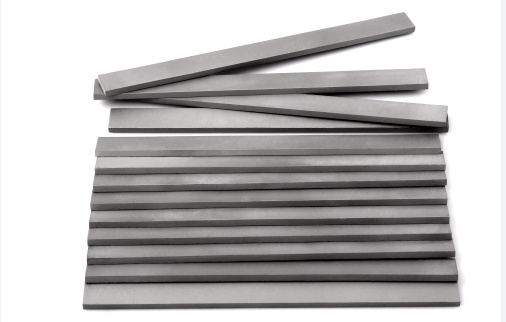
Advantages and Limitations Compared
Aspect | Advantages | Limitations |
---|---|---|
Hardness | Superior cutting efficiency | Brittle under extreme impact |
Wear Resistance | Long service life | Expensive compared to alternatives |
Versatility | Usable across industries | Requires specialized tools for shaping |
FAQ
Question | Answer |
---|---|
What are carbide strips made of? | Mainly tungsten carbide with a cobalt binder. |
What industries use carbide strips? | Manufacturing, mining, construction, and more. |
How long do carbide strips last? | Lifespan varies by application but generally far outlasts steel alternatives. |
Are carbide strips customizable? | Yes, many suppliers offer tailored sizes and grades. |
Can they withstand heat? | Yes, they are highly heat-resistant and ideal for high-temperature tasks. |