If you’re navigating the world of carbide saw tips, you’ve landed in the right spot! These small but mighty components are the unsung heroes of cutting tools in industries ranging from woodworking to metal fabrication. But what exactly are they, how are they made, and how do you choose the right ones? Sit tight because we’re diving deep into everything you need to know about carbide saw tips.
What Are Carbide Saw Tips?
Carbide saw tips are specialized cutting edges made from tungsten carbide, a hard material used for high-speed, precision cutting. They’re typically attached to saw blades to enhance durability, maintain sharpness longer, and improve cutting efficiency. Think of them as the workhorse that powers through tough materials where ordinary steel would wear out.
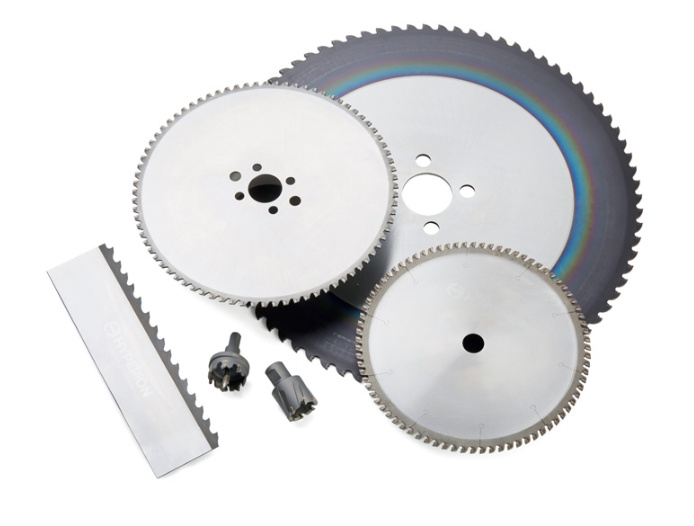
Types of Carbide Saw Tips
When it comes to carbide saw tips, you have options. Each type is tailored for specific cutting tasks, materials, and industries. Below is a table that breaks down common types of carbide saw tips based on their composition and application.
Type | Description | Best For |
---|---|---|
C1 Grade | General-purpose tips with medium hardness and wear resistance. | Woodworking, plastics |
C2 Grade | Balanced toughness and hardness, versatile for a variety of cutting needs. | Non-ferrous metals, hardwoods |
C3 Grade | Harder tips offering superior wear resistance but less toughness. | Abrasive materials, MDF, composites |
Micrograin Carbide | Made with ultra-fine grains for sharper edges and high precision. | Detailed cuts, precision tools |
TiC-Coated Carbide | Coated with titanium carbide for improved hardness and wear resistance. | High-performance metal cutting |
Submicron Carbide | Features even finer grain size for maximum edge retention. | High-speed machining |
Nano-Carbide Tips | Incorporates nanostructures for enhanced strength and thermal stability. | Advanced industrial applications |
Multilayer-Coated | Layers of wear-resistant coatings, such as TiAlN or AlCrN, for superior durability. | Aerospace, automotive, hard alloys |
Alloyed Carbides | Includes additional metals like cobalt or vanadium for enhanced toughness. | Impact-heavy applications |
Recycled Carbides | Made from reclaimed tungsten carbide, offering eco-friendly options with slight trade-offs. | Cost-conscious applications |
Raw Materials and Composition Analysis
The magic of carbide saw tips lies in their raw materials. Primarily composed of tungsten carbide (WC), they are bound with cobalt (Co) to achieve an unbeatable combination of hardness and toughness. Here’s a deeper look:
Material | Percentage (%) | Purpose |
---|---|---|
Tungsten Carbide (WC) | 85–95 | Provides hardness and wear resistance |
Cobalt (Co) | 5–15 | Adds toughness and binds the material |
Additives (TaC, TiC) | 0–5 | Enhances heat resistance and durability |
The unique composition of tungsten carbide ensures that saw tips can cut through tough materials like butter while retaining their edge for extended periods.
Applications of Carbide Saw Tips
Carbide saw tips are versatile and indispensable across industries. Here’s a table showcasing their applications:
Industry | Application | Examples |
---|---|---|
Woodworking | Cutting wood, laminates, and plywood | Circular saw blades |
Metalworking | Cutting aluminum, copper, and mild steel | Band saws, cold saws |
Construction | Cutting concrete, bricks, and tiles | Masonry saws |
Aerospace | Precision cutting of composite materials and hard alloys | Specialized saws |
Automotive | Cutting high-strength steel for vehicle components | CNC saw machines |
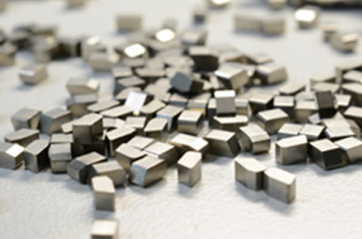
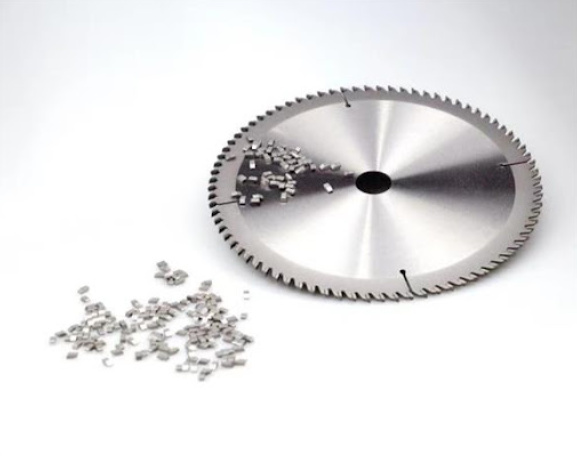
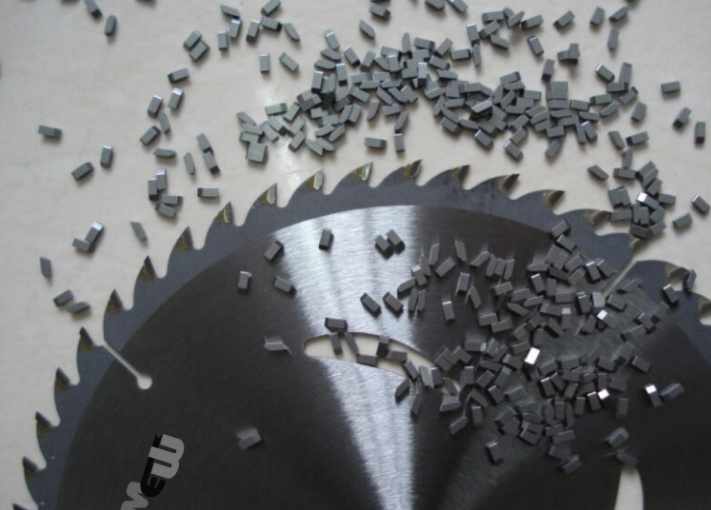
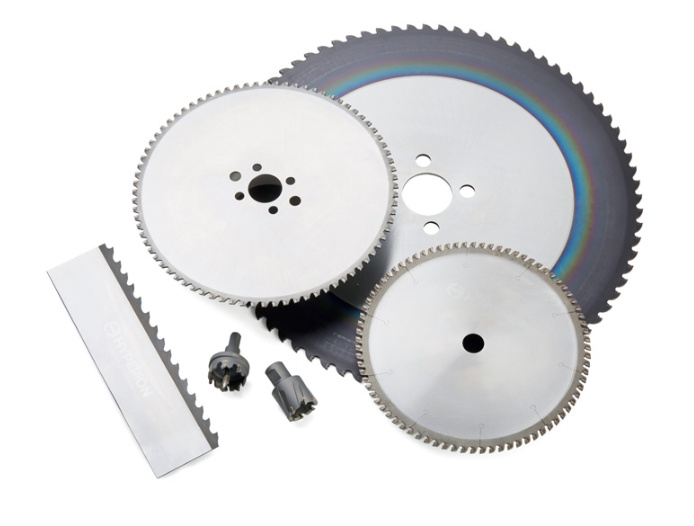
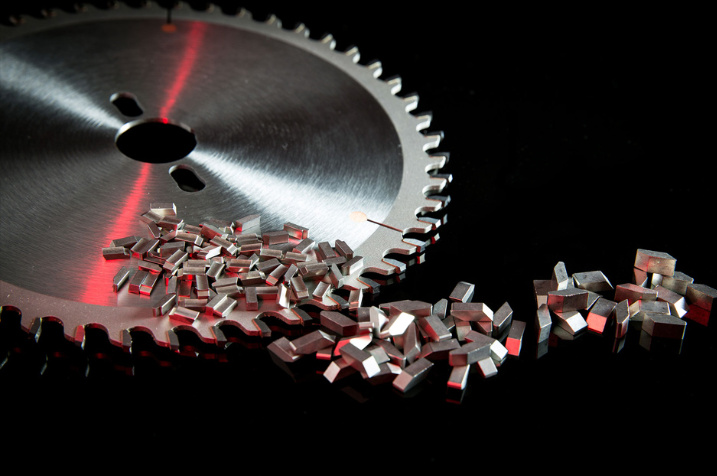
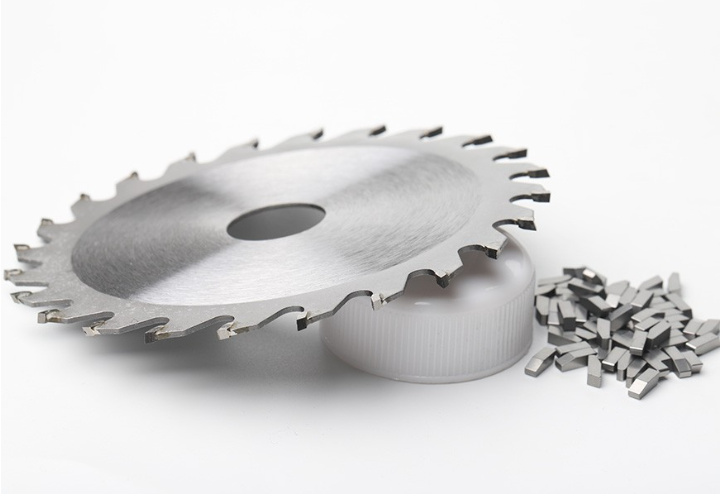
Production Process Flow of Carbide Saw Tips
Creating carbide saw tips is a meticulous process that balances science and craftsmanship. Let’s break it down step-by-step:
- Raw Material Preparation: Tungsten carbide powder and cobalt are blended to form a homogenous mixture.
- Powder Mixing: Additional elements like tantalum carbide (TaC) are added, depending on the required properties.
- Pressing: The mixture is compressed into a green compact, often in the desired shape of the tip.
- Sintering: The compact is heated at high temperatures to form a dense, solid tip.
- Coating (Optional): A wear-resistant layer like titanium carbide (TiC) is applied for specialized applications.
- Grinding and Polishing: Tips are ground to precise dimensions and polished for sharpness.
Material Properties of Carbide Saw Tips
Here’s a detailed table showcasing the impressive properties of carbide saw tips:
Property | Value | Significance |
---|---|---|
Hardness | 88–92 HRA | Superior cutting performance |
Density | 14.5–15.1 g/cm³ | High material strength |
Flexural Strength | ~3000 MPa | Resistance to cracking under stress |
Thermal Conductivity | 70–90 W/mK | Handles high heat during cutting |
Wear Resistance | Excellent | Longer tool life in abrasive environments |
Hardness, Strength, and Wear Resistance
Let’s take a closer look at the cutting-edge (pun intended) performance metrics of carbide saw tips:
Grade | Hardness (HRA) | Flexural Strength (MPa) | Wear Resistance |
---|---|---|---|
C1 | 88 | 2200 | Moderate |
C2 | 90 | 3000 | High |
C3 | 92 | 2800 | Very High |
Micrograin | 91 | 3100 | Exceptional |
Specifications, Sizes, and Standards
Carbide saw tips come in a variety of shapes, sizes, and standards to meet industry-specific needs. Here’s an overview:
Shape | Dimensions | Standards |
---|---|---|
Rectangular | 5 x 10 x 2 mm | ISO 513, DIN 6527 |
Trapezoidal | 8 x 12 x 2.5 mm | ANSI B212 |
Round | Diameter: 10–20 mm | ASTM B611 |
Custom Shapes | Varies per application | Manufacturer-specific |
Suppliers and Pricing Details
Finding the right supplier is key to sourcing quality carbide saw tips. Here’s a table to get you started:
Supplier | Region | Price Range | Specialization |
---|---|---|---|
Sandvik | Global | $20–$50 per tip | High-performance tips |
Kennametal | North America | $15–$45 per tip | Coated carbide solutions |
Zhuzhou Cemented Carbide | China | $10–$30 per tip | Cost-effective options |
How to Select the Right Carbide Saw Tips
Selecting carbide saw tips can feel overwhelming. Here’s a helpful table to guide you:
Parameter | Consideration | Example |
---|---|---|
Material to Cut | Hardness, abrasiveness | Wood vs. steel |
Tip Grade | Hardness vs. toughness balance | C2 for versatility |
Coating Requirements | TiC or multilayer coatings for extended life | Metal cutting |
Price | Balancing cost and performance | Recycled options |
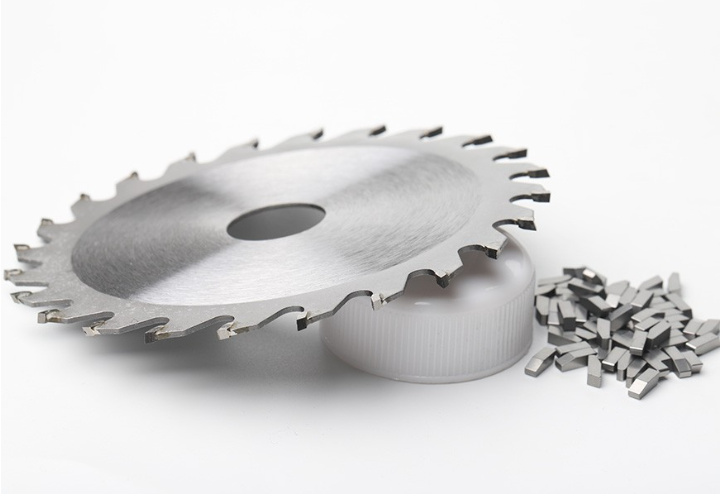
Advantages and Limitations
Carbide saw tips come with their own set of pros and cons:
Advantages | Limitations |
---|---|
Exceptional hardness and wear resistance | More expensive than HSS or steel tips |
Long-lasting sharpness | Brittle, prone to chipping under impact |
Versatile across various materials | Requires specialized tools for re-sharpening |
FAQ
Question | Answer |
---|---|
What are carbide saw tips made of? | Mainly tungsten carbide, with cobalt as a binder. |
Are carbide saw tips reusable? | Yes, they can often be re-sharpened or recycled. |
How long do carbide saw tips last? | Depends on usage; typically 5–10 times longer than steel tips. |
Can carbide tips cut hardened steel? | Yes, especially if coated with wear-resistant materials. |