Tungsten carbide turning inserts are an extremely hard and durable cutting tool material used on lathes and other machine tools to effectively machine steels, cast iron, hardened materials, and other difficult-to-cut metals. This article provides a comprehensive guide to tungsten carbide inserts, including an overview of sizes, grades, coatings, applications, operating parameters, costs, suppliers, installation, maintenance, and more.
tungsten carbide turning insert Shapes and Standard Designations
Tungsten carbide inserts come in a wide variety of standardized shapes and sizes, referred to by an ANSI or ISO shape code. The insert shape impacts the suitable applications and operating parameters. Common insert styles include CNMG, DNMG, SNMA, VNMG, TNMG, WNMG among many others.
Table 1: Common Tungsten Carbide Insert Shapes
Shape Code | Description |
---|---|
CNMG | Square insert with neutral rake angles, multi-use for steel turning, grooving, cut-off |
DNMG | 55° diamond-shaped insert for light finishing cuts |
SNMA | Round insert with positive rake for softer non-ferrous metals |
VNMG | 80° diamond insert with very sharp tip for hardened steels |
TNMG | Triangle-shaped insert with 3 cutting corners for steel, iron roughing |
WNMG | 80° diamond insert for high feed rough machining |
The nomenclature translates the tolerances, clearances, and other geometric attributes. Additionally, a size number denotes the inscribed circle diameter. For example, CNMG 432 indicates a 1/2” square insert. Always select inserts based on operational requirements.
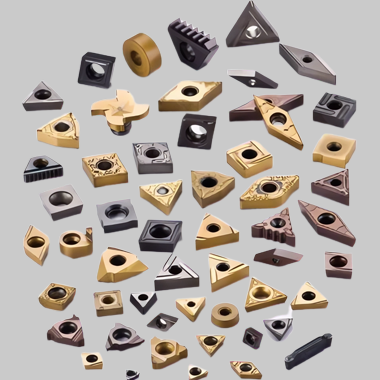
Tungsten Carbide Grades and Compositions
Tungsten carbide powders are blended with cobalt or nickel binders plus additives and sintered into inserts of exceptional hardness and heat resistance compared to tool steel alternatives. Different binder percentages and grain sizes produce inserts tailored towards specific machining scenarios balancing toughness, strength and temperatures.
Table 2: Common Tungsten Carbide Grades
Grade | Binder | Hardness | Toughness | Suitable Operations |
---|---|---|---|---|
C1, C2 | 6% Cobalt | Hard, 85.7 HRA | Brittle | High speed steel finishing |
C3, C4 | 8-10% Cobalt | Medium | Good | Hardened steel turning and milling |
C5, C6 | 12-13% Cobalt | Tougher | Very good | Interrupted and high feed cuts |
C7, C8 | 14-16% Cobalt | Tough | Excellent | Extreme rigidity/vibration, stainless steel |
Advanced substrate compositions called cermets combining titanium carbonitride with nickel/molybdenum binders offer alternatives to tungsten grades focused on high speed machining with lower temperatures. Various other exotic grades expand possibilities for extreme conditions. Select inserts according to work material machinability and cutting forces.
Tungsten Carbide Insert Coatings
Coatings applied via CVD or PVD deposition on the substrate improve wear resistance and lubricity keeping cutting edges sharper longer under high loads. Common tungsten carbide insert coating types include:
Table 3: Tungsten Carbide Insert Coatings
Coating | Description | Benefits |
---|---|---|
TiCN | Titanium carbonitride | Tough general turning and milling |
TiN | Titanium nitride | High lubricity, heat resistance |
Al2O3 | Aluminum oxide | Wear-resistant, insulative |
TiAlN | Titanium aluminum nitride | High speed machining up to 1000°F |
TiSiN | Titanium silicon nitride | Extreme heat and wear resistance |
Coatings allow higher speeds and feeds. Start with TiCN or TiN for steels. Use premium coatings like TiSiN for hardened materials where high cutting temperatures are reached. Coatings facilitate 5-10x life over uncoated insert grades dependent on work material and parameters.
Tungsten Carbide Insert Operating Parameters
Contrary to HSS tools, carbide inserts perform best at high speeds, feeds and depths of cut. The rigidity of insert geometries paired with hardened grades supports aggressive material removal rates not suitable for formed tool bits. However, constants for a given setup remain critical.
Table 4: Tungsten Carbide Insert Machining Suggestions
Parameter | Suggested Range |
---|---|
Speed | 400-600 SFM |
Feed Rate | 0.010-0.020 IPR |
Depth of Cut | Up to 0.250” |
Coolant | Flood or High Pressure |
Vary rates appropriately for facing versus turning and differing work piece diameters. Program maximum volumetric removal the tool, machine and work material combination allow. This maximizes productivity and defrays the higher insert costs compared to HSS alternatives. Ground inserts permit doubling stated feeds and speeds in rigid set ups.
Cost Considerations for Tungsten Carbide Inserts
Carbide inserts far surpass tool steel bits regarding tool life and speeds/feeds, but consumable prices ranging $5-50+ per insert can intimidate considering one-time HSS tool cost. However, incorporating associated machining productivity and downtime factors, carbide becomes less expensive on a per-part cost basis.
Table 5: Tungsten Carbide Insert Price Considerations
Insert Size | Price Range per Insert |
---|---|
CNMG 432 (1/2″ sq.) | $8 – 15 |
DNMG 332 (3/8“ dia.) | $6 – 12 |
SNMA 432 (1/2″ dia.) | $10 – 25 |
TNMG 332 (3/8″ triangle) | $6 – 15 |
WNMG 432 (1/2″ 80° dia.) | $12 – 30 |
Larger sizes for rough machining cost more but enable deeper cuts and higher metal removal rates offsetting additional insert expense through time savings. Experiment with insert styles and brands balancing quality/longevity against price to discover the most economical option for a given application. Consider total machining time improvements with carbide rather than just insert pricing.
Tungsten Carbide Insert Suppliers
Many cutting tool manufacturers and distributors supply tungsten carbide inserts to fit any specification requirement or budget. Some notable carbide insert brands include:
Table 6: Notable Tungsten Carbide Insert Manufacturers
Brand | Reputation | Origin | Pricing |
---|---|---|---|
Kennametal | Premium Performance | United States | $$$ |
Iscar | Advanced Grades | Israel | $$ |
Sandvik | Leading Coatings | Sweden | $$$ |
Kyocera | Rigidity | Japan | $$ |
Mitsubishi | Diverse Applications | Japan | $ |
Korloy | Economical | South Korea | $ |
Tungaloy | Productivity | Japan | $$ |
WIDIA | Custom Solutions | Germany | $$$ |
Within brands, various product lines cater towards general purpose, high performance, or economy applications balancing speed, tool life, and cost factors. Wide availability online simplifies searching tooling catalogs filtering on size, coating, grade specifics. While absolute pricing fluctuates continually, expect premium grades near $50 and basic inserts around $5 subject to size considerations. Consider total operational impact rather than upfront insert expense alone.
Insert Holders for Tungsten Carbide Turning
Carbide inserts mount to tool holders or blocks rigidity fitted to machine turrets or tool posts. Many standard holder styles exist for turning, boring, grooving, cutoff, and threading applications. Indexable block geometries boost rigidity leveraging inserts’ multi-corner capabilities.
Table 7: Style Comparison of Carbide Insert Tool Holders
Holder | Rigidity | Insert Compatibility | Cost |
---|---|---|---|
Solid block | Highest | Least Flexible | $$$ |
Modular | Very Good | Application Specific | $$ |
Single Insert | Good | 1 Insert Size/Type | $ |
Brazed tip | Low | Custom Fixed Insert | $ |
Choose tool blocks balancing insert location/quantity, replaceability, material options like steel versus carbide bodies, and practical factors like cost for the operation. Hardened steel holders often suffice for common turning scenarios. Leverage inserts’ interchangeability on CNCs minimizing holders for efficiency. Consider shrink fit insert retention for demanding situations
Inspecting and Maintaining Carbide Insert Tooling
Like any machining system component, apply prudent maintenance practices ensuring continued working order for tungsten carbide inserts and holders. Follow usage monitoring, integrity checks before/after operations, storage care, and insert rotation behaviors to maximize productivity.
Table 9: Carbide Insert and Holder Tooling Maintenance
Maintenance Activity | Step-by-Step Instructions | Interval |
---|---|---|
Usage Tracking | Document insert grades, life cycles, feeds/speeds | Each tool setup |
Pre-Operation Inspection | Check insert sharpness, edge integrity | Shift beginning |
Post-Operation Inspection | Inspect inserts for wear, cratering, cracks | Shift end |
Insert Indexing/Rotation | Rotate to unused corners or flip to new edge | At specific cut time or wear percentage thresholds |
Coolant Cleaning | Remove visible debris around inserts/holders | Daily |
Storage Precautions | Avoid exposing inserts/holders to moisture | Always |
Fixture Inspection | Confirm seals, connections intact | Monthly |
Cut Quality Analysis | Detect wear progression through tolerance changes | Per part procedures |
Programmatically tracking inserts based on characteristics and tool life empowers data-driven decisions improving machining efficiency over time.
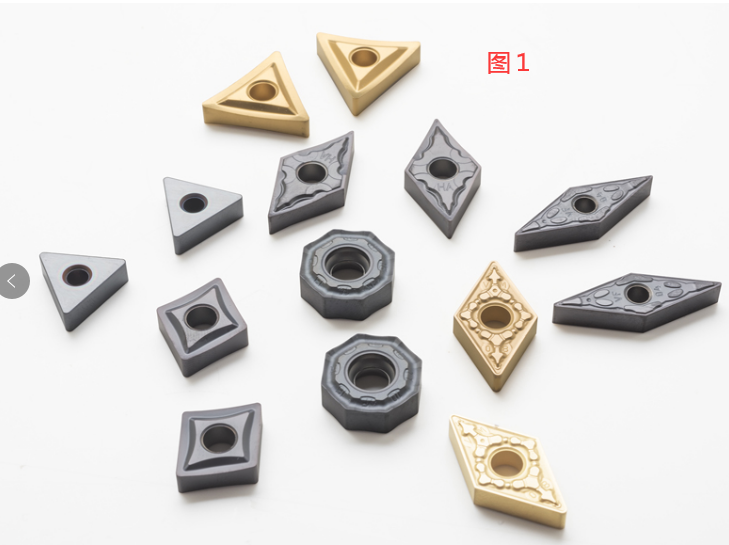
Optimizing Tungsten Carbide Insert Performance
Given insert grades and operational parameters substantially impact longevity, optimize these factors first before tweaking speeds/feeds/depths chasing tool life improvements. Consider the following priority order adjusting variables:
- Insert substrate – Start with a basic C2/C6 grade and spline for precise fit
- Work material specifics – Check hardness and tool alloy suitability
- Rigidity – Minimize overhangs, apply backing blocks, shrink fit holders
- Coolant usage – Ensure high pressure directed flow to cutting zone
- Speeds/feeds – Dial in conservative start points and adjust in small increments
- Depth of cuts – Balance tool deflection and material removal rate
Record insert performance at each setting level to hone in on the sweet spot maximizing longevity suitable for your machining environment.
FAQ
What is the best tungsten carbide insert grade?
The optimum grade depends on your specific machining application and work material. Harder grades like C1/C2 accomodate high precision finishing passes while tougher C5 inserts withstand interrupted cuts. Evaluate tool life, part tolerance, and productivity balance when selecting inserts.
How long should carbide inserts last?
Carefully applied carbide inserts often reach 60-120 minutes of cut time for steel turning operations. At optimal speeds and feeds conducive to the setup’s rigidity, insert life spans 100+ parts are common depending on work material specifics, necessary finish quality, and run durations.
Why did my carbide insert break, chip, or wear out quickly?
Excessive insert wear or tool failure typically indicates overly aggressive speeds/feeds or issues with clamping stability, vibrations, or harmonics. Ensure inserts are completely clean and seated properly. Index to unused cutting edges. Check system rigidity. Lower speed and feeds in a methodical fashion until reaching target tool life spans. Use suitable insert grades for the alloy.
How can I maximize carbide insert tool life?
Reducing operating temperatures prolongs carbide integrity. Ensure sharp cutting edges, positive rake angles aligned with the cut direction, conservative depths, controlled feeds, rigid clamping, and copious coolant stream application to constantly dissipate generated heat from the interface. Select premium coatings like aluminum oxide Al2O3 or consider an upgrade to ceramic inserts boosting heat tolerance further where cost-effective.