Tungsten carbide saw tips are an extremely hard and durable material used on the teeth of saw blades. The high hardness and wear resistance of tungsten carbide allows saw tips to stay sharp much longer than standard steel teeth. Tungsten carbide saw tips dramatically extend blade life and allow much faster cutting rates.
Overview of Tungsten Carbide Saw Tips
Tungsten carbide, often referred to as simply carbide, is made by mixing tungsten powder and carbon. It is then formed and heated to produce an incredibly robust material that is two to three times stiffer than steel with double the density. Here is a quick overview of tungsten carbide saw tips:
Property | Description |
---|---|
Hardness | 89-93 HRA which is equivalent to 85-88 HRC on the Rockwell Scale |
Strength | Very high compressive and tensile strength |
Toughness | Hard yet reasonably tough composite |
Density | Roughly double that of steel |
Stiffness | Triple the stiffness of steel |
Thermal conductivity | Poor conductor compared to metals |
Electrical conductivity | Low, can spark if struck |
Corrosion resistance | Resists corrosion well |
Common forms | Pellets, powder, coatings, tools |
Manufacturing | Powder metallurgy and sintering |
Main uses | Cutting tools, dies, saw blades, drills |
The extreme hardness of tungsten carbide allows it to resist abrasive wear much better than standard carbon or alloy steels. At the same time, it retains reasonable toughness thanks to its composite structure and manufacturing process.
This combination of hardness, strength, and toughness makes tungsten carbide the ideal material for saw blade teeth that must withstand significant forces and temperatures. The hardness preserves a sharp cutting edge which is paramount for fast, clean cuts.
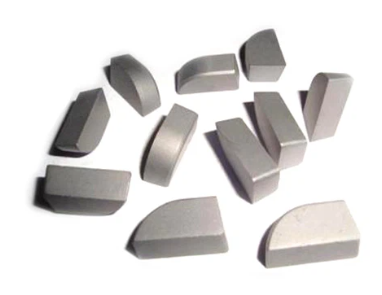
Applications of Tungsten Carbide Saw Tips
Tungsten carbide saw tips have become ubiquitous across nearly every industry that requires cutting hard or abrasive materials. If you need to saw concrete, stone, tile, masonry, refractory brick, ductile iron, or other hard substances, a carbide-tipped blade is essential.
Here are some of the most common applications that use saw blades with tungsten carbide tips:
Application | Materials Cut |
---|---|
Construction and demolition | Concrete, reinforced concrete, stone, masonry, tile, cement board |
Tile and flooring | Ceramic tile, porcelain, granite |
Metal fabrication shops | Steel alloys, tool steel, cast iron, ductile iron |
Foundries and smelters | Cast iron, alloy steels, heat-resistant alloys |
Refractory manufacturing | Refractory bricks, ceramic fiber insulation |
Infrastructure | Concrete runways, roads, bridges |
Tungsten carbide allows these blades to withstand the abrasion and impacts inherent to sawing such hard or fibrous materials. The extreme hardness preserves the cutting geometry and tips stay sharper longer than alternatives.
This hardness comes at a price, however. Tungsten carbide is still reasonably brittle compared to steel. Striking solid objects or twisting a blade can cause individual tips to crack or break off entirely. Proper blade selection and usage is important to get full value from carbide-tipped designs.
Grades and Specifications of Tungsten Carbide
Like other powder metallurgy products, the properties of tungsten carbide can be customized during manufacturing. Varying the tungsten-carbon ratio, cobalt content, corrosion inhibitors, grain size, and more allows carbide to be tailored to different functions.
There are four primary tungsten carbide grades used for saw tip applications:
Grade | Hardness | Total Cobalt Content | Key Characteristics |
---|---|---|---|
C1 | 86-88 HRA | 3-6% | Excellent wear resistance and edge retention, brittle |
C2 | 86-88 HRA | 6-10% | Very good wear resistance with added toughness |
C3 | 84-86 HRA | 10-13% | Tougher grade for interrupted cuts |
C4 | 83-88 HRA | 13-30% | Maximum resistance to shocks and impact |
The cobalt acts as a cementing agent to enhance fracture resistance. In general, higher cobalt grades trade off some hardness for significantly better impact resistance and toughness. C2 and C3 grades offer the best all-around properties for cutting very hard materials.
Carbide saw tips must withstand high cyclic stresses from material chips striking them as the alternate teeth of a blade cut in succession. Grades and geometries are application-specific depending on the brittleness or abrasiveness of the material being cut.
Manufacturing Processes
Tungsten carbide is manufactured via powder metallurgy techniques that blend fine particles of tungsten and carbon compounds. Here is a quick overview of the stages:
1. Mixing – Tungsten, carbon, and cobalt powders are measured and blended together with temporary binders. This can be done via ball milling or attrition mills.
2. Pressing – The powder mix is pressed into a die at high pressures, up to 4 tons per square inch. This fuses particles together and forms the compact into standard shapes.
3. Sintering – Pressed parts are put through an extremely high temperature kiln under vacuum or hydrogen atmosphere. Temperatures exceed 2,800°F fusing powders into dense, consolidated parts through diffusion bonding and liquid phase sintering of cobalt.
4. Conditioning – Final conditioning processes thegrain structure and dimensions the carbide into final tolerances through grinding/lapping. The parts can also be treated or coated.
This powder metallurgy technique allows very homogeneous mixes and consistent material properties. The fine carbide particles provide hardness while cobalt acts as a ductile binder to enhance fracture toughness. Varying mixes and process parameters creates grades optimized for different cutting applications.
Comparative Properties of Carbide Saw Tips
Here is how tungsten carbide tips compare to common steel alloys used for saw blades:
Property | Tungsten Carbide | High Speed Steel | Carbon Steel |
---|---|---|---|
Hardness | Up to 93 HRA | 62-65 HRC | 50-55 HRC |
Strength | Very high | High | Medium |
Toughness | Medium | High | Higher |
Wear resistance | Extremely high | Medium | Low |
Thermal conductivity | Low | Medium | Higher |
Corrosion resistance | High | Medium | Low |
Price | High | Medium | Low |
Clearly tungsten carbide has overriding advantages in hardness, strength, and wear resistance compared to standard tool or alloy steels. This comes at the expense of reduced toughness and fracture resistance. Hardness does decrease at elevated temperatures so thermal management is still important to avoid rapid dulling.
Proper blade designs mitigate these tradeoffs by using the minimum amount of carbide necessary only on critical wear surfaces. This preserves cost-effectiveness of steel while maximizing benefits of the carbide cutting edges.
Types and Styles of Carbide-Tipped Saw Blades
There are many possible saw blade designs, diameters, arbors, tooth geometries, and more that influence cutting performance and suitability to applications. However, most industrial carbide saw blades fall into a few main styles:
Circular Saws
These common circular saw blades cover diameters from 4 inches to well over 4 feet for large masonry or concrete saws. Teeth are often brazed or laser welded in segments around the perimeter of steel cores:
Carbide tips maximize abrasion resistance on the cutting edges. They can be molded symmetrical teeth or contain specialized geometries with leading/trailing edges and chip breakers all ground into the carbide.
Band Blades
Band saws consist of a thin, continuous band of steel wrapped around two pulley wheels. Carbide can be brazed across the leading tooth edges:
These blades make curved or irregular cuts in materials like tool steels or cast iron. Variable tooth geometry helps clear chips.
Reciprocating/Jigsaw Blades
The typical reciprocating saw blade consists of hardened tool steel with teeth ground into one side. Carbide tips may overlay the teeth to enhance hardness:
Jigsaw designs allow adjusting orbital action to vary cutting aggression in soft or hard materials.
Oscillating Multi-Tool Blades
Small oscillating tool blades have become popular for detail cuts. Carbide grades enhance life when sawing tiles, nails, drywall, etc.
There are unlimited specialty shapes and custom blades possible. In general, circular saws emphasize speed and efficiency while reciprocating/band designs allow more flexibility in following curved cuts.
Cost Analysis of Carbide-Tipped Blades
Carbide tipped blades carry a significant price premium over steel teeth. However, long-term cost per cut can be lower by extending lifespan. Here are typical prices and longevity for 7-1/4” 24-tooth framing saws cutting nails/timber:
Blade Type | Price Range | Average Life | Cuts Before Dulling | Est. Cuts Over Life | Cost Per Cut |
---|---|---|---|---|---|
Steel | $8 – $15 | 1 – 3 days | ~500 | 1,500 – 4,500 | $0.006 – $0.02 |
Carbide | $25 – $60 | 30 – 90 days | ~5,000 | 150,000 – 450,000 | $0.0006 – $0.0008 |
While sticker price is far higher for carbide, conservatively they can cut at least 30x as much material over lifespan. This results in 5-10x lower amortized cost per cut. For high volume tradesmen or commercial sites, the productivity boost easily justifies the larger upfront investment. Homeowners that only make occasional cuts would likely not benefit cost-wise.
Cutting Tips and Precautions
Carbide grades transform the productivity possible when sawing very hard or abrasive substances. However, the extreme hardness comes with tradeoffs in toughness and shock resistance. Some basic tips include:
- Let blade do the work – avoid excessive feed forces bending/twisting blade
- Ensure stability of workpiece to minimize deflection as blade passes through
- Clean chips frequently to prevent carbide fracture from accumulated debris
- Use lowest blade speed that provides good chip formation
- Allow sufficient set on teeth so body does not rub and wear gullets
- Apply cutting fluids for better chip removal and cooling
- Periodically sharpen/dress tips when cutting rate noticeably slows
- Avoid cutting material like hardware, rebar, or sand in concrete that can rapidly break individual tips
Proper precautions maximize runtime between blade rotations. However, carbide is still a wear item that requires replacement once graded down too far. Runtime stretches from days to months based on usage aggressiveness.
FAQ
Q: Why are carbide-tipped blades so expensive?
A: Tungsten carbide is costly to manufacture given powder metallurgy methods and extensive processing. Limited availability of tungsten also contributes to prices 2-4x that of tool steel. However, carbide tips greatly extend lifespan to offset higher initial cost over total cuts.
Q: Can I sharpen carbide saw blades?
A: Yes, light honing or grinding restores the extremely hard cutting edge as it wears gradually over time. However, broken tips would need brazing/welding to replace. Avoid highly abrasive wheels that remove material too quickly.
Q: What causes carbide teeth to break?
A: Fractures usually result from sudden dynamic impact loads exceeding the toughness capacity. Built-up chips strike tips at high velocities as alternating teeth cut. Striking hidden nails or rebar also cracks teeth. Higher cobalt grades better resist breakage.
Q: How long do carbide-tipped blades last?
A: Estimates range from 30-100x the life of steel blades based on application. Cutting highly abrasive materials shortens runs. With proper precautions, carbide tips can last weeks to months of regular use. Temperature and wear eventually degrade cutting geometry.
Q: Can I cut steel with a carbide blade?
A: Carbide has higher hardness than standard tool steels so it can cut soft metals. However, friction rapidly degrades cutting edges. Abrasive cut-off wheels are better for steel. Limit use on steel to occasional alloy cuts or nails embedded in wood.