Introduction
Definition of Tungsten Carbide Blanks
Tungsten carbide blanks are a type of cutting tool material that is widely used in various industries. These blanks are made from a combination of tungsten and carbon, resulting in a material that is extremely hard and durable. Tungsten carbide blanks are known for their exceptional strength and wear resistance, making them ideal for applications that require high-performance cutting tools. These blanks are commonly used in the manufacturing of drills, end mills, inserts, and other cutting tools. With their excellent hardness and toughness, tungsten carbide blanks are able to withstand extreme heat and pressure, making them suitable for use in demanding machining operations. Overall, tungsten carbide blanks play a crucial role in the production of high-quality cutting tools that are essential for various industrial applications.
Applications of Tungsten Carbide Blanks
Tungsten carbide blanks have a wide range of applications in various industries. One of the key applications of tungsten carbide blanks is in the manufacturing of cutting tools. Due to their exceptional hardness and wear resistance, tungsten carbide blanks are ideal for producing high-quality cutting tools that can withstand the demands of heavy-duty machining operations. Additionally, tungsten carbide blanks are also used in the production of wear parts, such as nozzles, seals, and bearings, where their excellent wear and corrosion resistance properties are highly valued. Furthermore, tungsten carbide blanks find applications in the mining and construction industries, where they are used for drilling and excavation purposes. Overall, the versatility and superior properties of tungsten carbide blanks make them an essential material in various industrial applications.
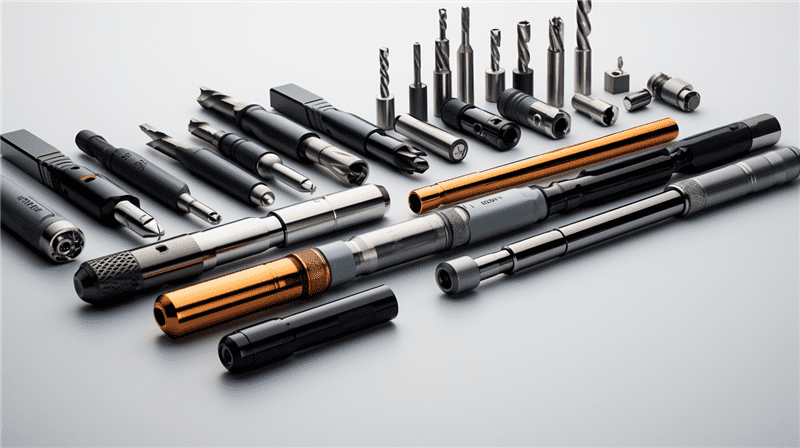
Importance of Tungsten Carbide Blanks
Tungsten carbide blanks play a crucial role in various industries due to their exceptional hardness and wear resistance. These blanks are widely used in the manufacturing of cutting tools, such as drills, end mills, and inserts, as well as in the production of wear parts for mining, construction, and oil and gas industries. The importance of tungsten carbide blanks lies in their ability to withstand high temperatures and maintain their cutting edge even under extreme conditions. With their superior strength and durability, tungsten carbide blanks contribute to improved productivity, reduced downtime, and cost savings for businesses. Moreover, their resistance to corrosion and chemical reactions makes them ideal for applications in harsh environments. Overall, the use of tungsten carbide blanks is essential for achieving precision, efficiency, and longevity in various industrial processes.
Composition of Tungsten Carbide Blanks
Tungsten and Carbon
Tungsten carbide blanks are a type of material that combines the properties of tungsten and carbon. Tungsten, known for its high melting point and durability, provides strength and hardness to the blanks. Carbon, on the other hand, enhances the toughness and wear resistance of the material. This combination makes tungsten carbide blanks ideal for various applications, including cutting tools, drilling equipment, and wear parts. With their exceptional hardness and resistance to heat and wear, tungsten carbide blanks are widely used in industries such as automotive, aerospace, and mining. The unique properties of tungsten carbide blanks make them a valuable and reliable choice for demanding applications where strength and durability are essential.
Binder Material
Tungsten carbide blanks are widely used in various industries due to their exceptional hardness and wear resistance. The binder material used in the production of tungsten carbide blanks plays a crucial role in determining their overall performance and properties. The binder material acts as a matrix that holds the tungsten carbide particles together, providing strength and stability to the blanks. Commonly used binder materials include cobalt, nickel, and iron. Each binder material has its own unique characteristics, affecting the hardness, toughness, and corrosion resistance of the tungsten carbide blanks. The choice of binder material depends on the specific application requirements and desired properties of the blanks. Manufacturers carefully select the appropriate binder material to ensure the tungsten carbide blanks meet the performance standards and deliver optimal results in various cutting, drilling, and wear-resistant applications.
Grain Size
Grain size is an important factor to consider when it comes to tungsten carbide blanks. It refers to the size of the individual grains or particles that make up the material. The grain size can have a significant impact on the properties and performance of the tungsten carbide blanks. Smaller grain sizes generally result in higher hardness and improved wear resistance, while larger grain sizes may provide better toughness and impact resistance. Manufacturers carefully control the grain size during the production process to ensure the desired characteristics of the tungsten carbide blanks are achieved. By understanding and selecting the appropriate grain size, users can optimize the performance of their tungsten carbide blanks for various applications.
Manufacturing Process
Powder Preparation
Powder preparation is a crucial step in the production of tungsten carbide blanks. It involves the careful selection and processing of raw materials to create a high-quality powder. The first step in the preparation process is the selection of tungsten and carbon sources, which are then ground and mixed to form a homogeneous mixture. This mixture is then subjected to a series of heating and cooling steps to ensure the proper formation of tungsten carbide crystals. The resulting powder is then sieved to remove any impurities and ensure a consistent particle size. The quality of the powder obtained during the preparation stage directly impacts the performance and durability of the tungsten carbide blanks.
Mixing and Blending
Mixing and blending are crucial processes in the production of tungsten carbide blanks. These processes involve combining tungsten powder with carbon and other elements to create a homogeneous mixture. The mixture is then subjected to high temperatures and pressure to form the desired tungsten carbide material. Proper mixing and blending ensure the uniform distribution of the elements, resulting in high-quality tungsten carbide blanks with excellent hardness, strength, and wear resistance.
Compaction and Shaping
Compaction and shaping are crucial processes in the production of tungsten carbide blanks. Compaction involves the compression of tungsten carbide powder into a desired shape, typically using a die and a press. This process helps to ensure the uniform distribution of the powder particles and the elimination of any voids or defects. Shaping, on the other hand, involves the refining of the compacted tungsten carbide into its final shape through various methods such as grinding, milling, or turning. These processes not only enhance the dimensional accuracy and surface finish of the blanks but also impart the necessary mechanical properties to meet specific application requirements. Overall, compaction and shaping play a vital role in the manufacturing of high-quality tungsten carbide blanks.
Properties of Tungsten Carbide Blanks
Hardness
Tungsten carbide blanks are known for their exceptional hardness. With a hardness rating of up to 9 on the Mohs scale, these blanks are one of the hardest materials available. This remarkable hardness makes tungsten carbide blanks ideal for applications that require extreme wear resistance and durability. From cutting tools to industrial machinery components, the hardness of tungsten carbide blanks ensures long-lasting performance in demanding environments. Additionally, the hardness of tungsten carbide blanks also contributes to their resistance to deformation and chipping, further enhancing their reliability and longevity.
Wear Resistance
Tungsten carbide blanks are renowned for their exceptional wear resistance. This unique property makes them highly suitable for various industrial applications where materials are subjected to extreme wear and tear. The hardness and durability of tungsten carbide blanks allow them to withstand the harshest conditions, ensuring a longer lifespan and reduced maintenance costs. Whether it’s in the manufacturing of cutting tools, mining equipment, or wear parts for machinery, tungsten carbide blanks provide unmatched performance and reliability. With their superior wear resistance, these blanks are a preferred choice for industries requiring high-performance materials that can withstand heavy use and demanding environments.
High Temperature Resistance
Tungsten carbide blanks are known for their exceptional high temperature resistance. This unique property makes them ideal for various applications that involve extreme heat and pressure. Whether it’s in the aerospace, automotive, or oil and gas industry, tungsten carbide blanks can withstand the harshest conditions without compromising their structural integrity. The high temperature resistance of tungsten carbide blanks is a result of their composition, which includes a combination of tungsten and carbon. This combination creates a material that can withstand temperatures up to 1600 degrees Celsius, making it one of the most reliable and durable materials in high-temperature environments.
Applications of Tungsten Carbide Blanks
Cutting Tools
Tungsten carbide blanks are widely used in the manufacturing of cutting tools. With their exceptional hardness and wear resistance, these blanks provide superior performance and durability. They are commonly used for the production of drills, milling cutters, and inserts for turning tools. The high thermal conductivity of tungsten carbide allows for efficient heat dissipation during cutting, resulting in improved tool life and productivity. Furthermore, their excellent strength and toughness make them suitable for use in high-speed machining applications. Overall, tungsten carbide blanks play a crucial role in the production of high-quality cutting tools that are essential in various industries.
Mining and Drilling Equipment
Mining and drilling equipment play a crucial role in various industries, including the mining and construction sectors. One essential component of such equipment is tungsten carbide blanks. These blanks, made from a combination of tungsten and carbon, offer exceptional hardness and resistance to wear and tear. They are commonly used in the manufacturing of drilling bits, cutting tools, and other components that are subjected to extreme conditions. Tungsten carbide blanks are known for their durability and ability to withstand high temperatures, making them an ideal choice for mining and drilling applications. With their superior strength and performance, these blanks contribute to the efficiency and productivity of mining operations, ensuring smooth and effective drilling processes.
Wear Parts
Tungsten carbide blanks are widely used in the production of wear parts. These wear parts are essential components in various industries, including mining, construction, and manufacturing. The exceptional hardness and resistance to wear make tungsten carbide blanks the ideal choice for applications where durability and longevity are crucial. Whether it’s for cutting tools, drilling bits, or wear plates, tungsten carbide blanks provide superior performance and reliability. With their high strength and toughness, they can withstand extreme conditions and heavy usage, ensuring optimal performance and cost-effectiveness in the long run.
Conclusion
Summary of Tungsten Carbide Blanks
Tungsten carbide blanks are a type of material widely used in various industries due to their exceptional hardness and resistance to wear and tear. These blanks are made by combining tungsten and carbon atoms in a high-temperature process, resulting in a dense and durable material. The summary of tungsten carbide blanks can be described as a versatile and reliable option for manufacturing cutting tools, dies, and wear parts. With their superior strength and toughness, tungsten carbide blanks offer excellent performance and extended tool life, making them a preferred choice in demanding applications. Additionally, their ability to withstand high temperatures and harsh environments further enhances their suitability for a wide range of industrial applications. Overall, tungsten carbide blanks play a crucial role in improving productivity, efficiency, and cost-effectiveness in various manufacturing processes.
Future Developments
Future developments in the field of tungsten carbide blanks are expected to focus on improving their durability, strength, and performance. Researchers are exploring new techniques and materials to enhance the properties of tungsten carbide, allowing it to withstand even harsher conditions. Additionally, advancements in manufacturing processes are being made to produce tungsten carbide blanks with higher precision and consistency. These developments will not only benefit industries such as aerospace, automotive, and mining, but also pave the way for innovative applications in areas like renewable energy and medical devices. With ongoing research and innovation, the future of tungsten carbide blanks looks promising, promising a wide range of possibilities for various industries.
Importance in Various Industries
Tungsten carbide blanks play a crucial role in various industries due to their exceptional properties and durability. These blanks are widely used in manufacturing processes such as cutting, drilling, and grinding, where high hardness and wear resistance are required. The automotive industry relies heavily on tungsten carbide blanks for the production of engine components, cutting tools, and wear parts. In the aerospace industry, these blanks are used for machining turbine blades, nozzles, and other critical components. Additionally, the medical and dental sectors utilize tungsten carbide blanks for the fabrication of surgical instruments and dental drills. Overall, the importance of tungsten carbide blanks in various industries cannot be overstated, as they contribute to increased productivity, efficiency, and cost-effectiveness.