Imagine this: you’re a sculptor, meticulously shaping a block of granite. But instead of a chisel, you have a high-tech tool that can tackle even the toughest materials with incredible precision and extended life. That’s the magic of standard carbide inserts!
These are like tiny, replaceable cutting edges made from an incredibly hard material called tungsten carbide. They’re the workhorses of metal cutting operations, seamlessly integrated into cutting tools like turning inserts, milling inserts, and drilling inserts.
Why standard carbide inserts? Well, traditional high-speed steel (HSS) tools can get dull quickly, especially when dealing with hard metals. Standard carbide inserts, on the other hand, boast exceptional:
- Hardness: Tungsten carbide ranks second only to diamond in hardness, allowing them to slice through tough metals like butter.
- Wear Resistance: Standard carbide inserts can withstand extreme temperatures and friction generated during metal cutting, lasting significantly longer than HSS tools.
- Versatility: These inserts come in a wide range of shapes, sizes, and grades, enabling them to tackle various machining applications.
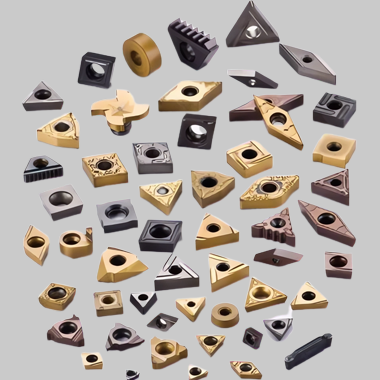
The Production Process of Standard Carbide Inserts
The creation of a standard carbide insert is a fascinating dance between chemistry, physics, and engineering. Here’s a simplified glimpse into their journey:
- Powder Powerhouse: The process begins with a meticulously formulated blend of tungsten carbide powder, along with other elements like cobalt for binding.
- Shaping the Future: The powder is then compacted into the desired insert shapes using high-pressure presses. Imagine tightly packing wet sand into intricate molds.
- High Heat, High Stakes: The compacted shapes are subjected to incredibly high temperatures in a furnace, a process called sintering. This fuses the particles together, forming a rock-solid structure.
- Sharpening Up: Once sintered, the inserts are precisely ground to achieve the exact cutting geometries needed for optimal performance. Think of sharpening a high-end kitchen knife to razor-like perfection.
- Coating for Champions: In many cases, a final layer of exotic coatings like titanium nitride (TiN) or aluminum chromium nitride (AlCrN) is applied. These coatings further enhance wear resistance, heat tolerance, and chip control.
Selecting Standard Carbide Inserts
Just like choosing the right paintbrush for your artistic vision, selecting the ideal standard carbide insert requires careful consideration. Here are some key factors to ponder:
- Material to be Machined: Different metals have varying properties. For example, inserts designed for steel might not be the best choice for machining aluminum.
- Cutting Operation: Are you turning, milling, drilling, or facing? Each operation demands specific insert geometries for optimal chip control and surface finish.
- Cutting Conditions: Factors like cutting speed, feed rate, and depth of cut all influence insert selection. Higher speeds and deeper cuts often necessitate tougher insert grades.
Here’s an analogy: Think of standard carbide inserts as specialized athletes. You wouldn’t pick a marathon runner for a weightlifting competition, would you? Similarly, the insert needs to be a perfect fit for the specific machining task.
Thankfully, insert manufacturers provide comprehensive selection guides that consider these factors. Additionally, experienced machinists can offer valuable insights to help you choose the winning insert for your project.
Advantages and Considerations of Standard Carbide Inserts
While standard carbide inserts offer a multitude of benefits, it’s essential to be aware of some considerations:
Advantages:
- Increased Productivity: Longer tool life translates to less downtime for changing inserts, leading to significant productivity gains.
- Superior Surface Finish: The sharp cutting edges of carbide inserts produce exceptional surface finishes on machined parts, often eliminating the need for secondary finishing operations.
- Cost-Effectiveness: While the initial cost of carbide inserts might be higher than HSS tools, their extended lifespan and improved productivity often lead to lower overall machining costs.
Considerations:
- Higher Initial Investment: As mentioned earlier, the upfront cost of standard carbide inserts can be higher than HSS tools.
- Brittleness: While incredibly hard, carbide inserts can be brittle. Improper handling or exceeding recommended cutting parameters can lead to insert chipping or breakage.
- Need for Specialized Tooling: Standard carbide inserts require compatible tool holders designed to securely hold the inserts and deliver the necessary cutting forces.
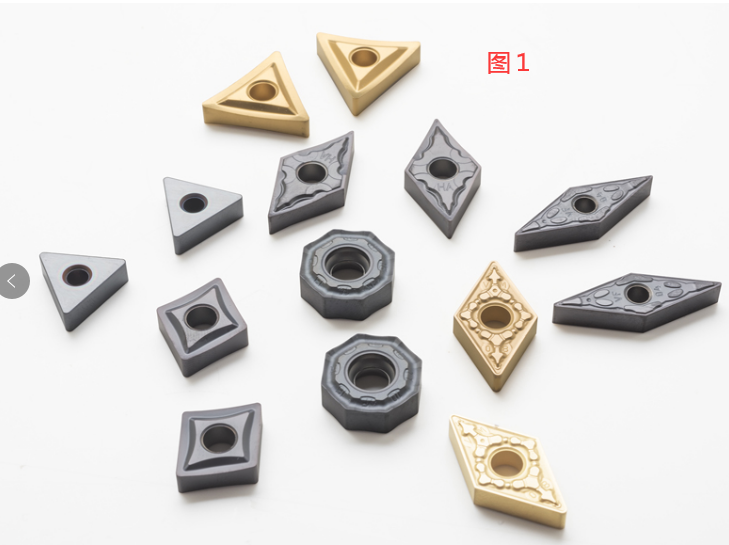
Shining a Light on Different Insert Geometries
The world of standard carbide inserts boasts a diverse range of shapes and sizes, each catering to specific machining applications. Here are a few common insert geometries, along with their strengths:
- Turning Inserts:
- Triangle (TNMG): A versatile choice for various turning operations, offering good chip control and strength.
- Diamond (CNMG): Often used for finishing cuts due to its sharp cutting edge and smooth chip formation.
- Round (RNMG): Ideal for continuous cutting operations and generating good surface finishes.
- Milling Inserts:
- Square (SE): A popular choice for face milling and shoulder milling, providing excellent stability and edge strength.
- Ballnose (R): Perfect for contour milling and creating intricate profiles, thanks to its rounded cutting edge.
- End Mill (APMT): Designed for high-performance slotting and pocketing operations, offering efficient chip evacuation.
- Drilling Inserts:
- Triangular (TPC): A common choice for general-purpose drilling, delivering good centering and chip control.
- Square (SC): Often used for deep hole drilling applications due to its robust design and ability to handle high cutting forces.
- CoroDrill (CHO): A specialized insert for high-speed drilling, featuring unique geometries for optimal chip evacuation and hole quality.
Beyond Shapes: Delving Deeper into Insert Grades
The “secret sauce” within a standard carbide insert lies in its grade. Each grade is meticulously formulated with a varying composition of tungsten carbide, cobalt, and other elements. This unique blend determines the insert’s:
- Hardness: Higher hardness translates to better wear resistance for tougher materials.
- Toughness: Increased toughness improves resistance to chipping and breakage, especially during interrupted cuts.
- Cratering Resistance: Certain grades excel at resisting crater wear on the insert’s face caused by high temperatures and chip abrasion.
Understanding Insert Grades: A Balancing Act
Selecting the optimal insert grade involves a balancing act. For instance, an extremely hard grade might provide excellent wear resistance but could be more susceptible to chipping. Here’s a table summarizing some common insert grade characteristics:
Grade Characteristics | Applications |
---|---|
High Hardness, Low Toughness | Machining of hard and abrasive materials like cast iron and some alloy steels. |
Balanced Hardness and Toughness | A versatile choice for a wide range of steel machining operations. |
High Toughness, Moderate Hardness | Suited for interrupted cuts and applications prone to vibrations. |
Remember: Insert manufacturers provide detailed grade recommendations based on the material being machined and the specific cutting operation. Consulting these resources or seeking advice from a machining expert can ensure you select the winning grade for your project.
Keeping Your Standard Carbide Inserts in Top Shape
Standard carbide inserts are a valuable investment, and proper care extends their lifespan and optimizes performance. Here are some essential tips:
- Handle with Care: Treat your inserts with respect! Avoid dropping them or subjecting them to unnecessary impacts that can cause chipping.
- Store them Safely: Keep your inserts in their designated holders or protective containers when not in use. This prevents damage and ensures they’re readily accessible when needed.
- Clean Regularly: Built-up chips and debris can hinder insert performance and even damage the cutting edge. Regularly clean your inserts with a soft brush and compressed air.
- Follow Recommended Cutting Parameters: Exceeding the insert’s recommended speeds, feeds, and depths of cut can lead to premature wear and breakage. Refer to the manufacturer’s specifications and adjust your cutting parameters accordingly.
- Invest in Quality Tooling: Using compatible tool holders designed for the specific insert geometry ensures proper clamping, cutting force transmission, and insert stability.
By following these simple tips, you can maximize the life and performance of your standard carbide inserts, ensuring exceptional results in your metalworking projects.
The Future of Standard Carbide Inserts
The world of standard carbide inserts is constantly evolving. Here are some exciting trends to keep an eye on:
- Advanced Coatings: Expect to see the development of even more sophisticated coatings that further enhance wear resistance, heat tolerance, and chip control.
- Automation and Integration: The growing adoption of automation in machining will likely lead to inserts specifically designed for automated processes and optimized tool life in unmanned environments.
- Sustainable Materials: As sustainability becomes a top priority, manufacturers might explore the use of recycled or eco-friendly materials in insert production.
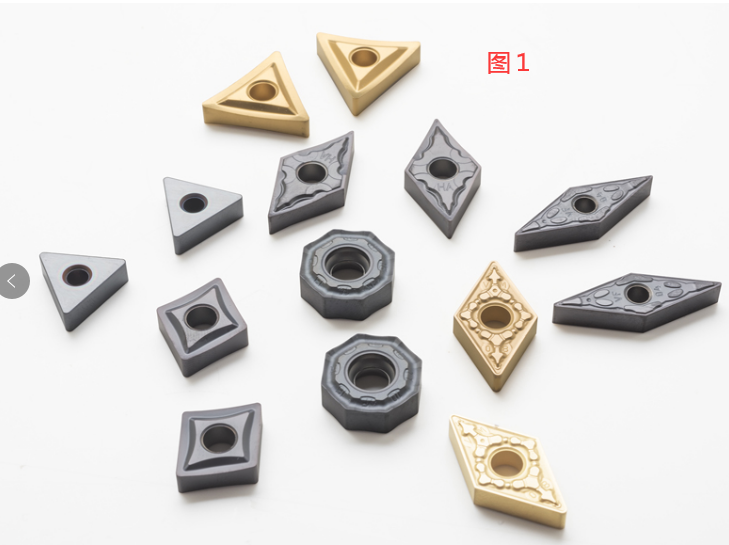
FAQ
Here are some frequently asked questions (FAQs) regarding standard carbide inserts:
Q: How long do standard carbide inserts typically last?
A: The lifespan of a standard carbide insert depends on several factors, including:
- Material being machined: Harder materials will cause the insert to wear faster.
- Cutting parameters: Higher speeds, feeds, and depths of cut will lead to quicker wear.
- Insert grade: Harder grades offer better wear resistance but might be more prone to chipping.
- Coolant application: Proper use of coolant can significantly extend insert life by reducing heat buildup.
With proper care and selection, a single standard carbide insert can last for hundreds or even thousands of machining cycles.
Q: Can I sharpen standard carbide inserts?
A: No, standard carbide inserts are not designed to be sharpened like traditional HSS tools. The grinding process can damage the insert’s delicate geometry and compromise its performance. However, some manufacturers offer insert resharpening services for specific insert types. It’s essential to weigh the cost of resharpening versus purchasing new inserts.
Q: Are there any alternatives to standard carbide inserts?
A: Yes, there are a few alternatives to standard carbide inserts, each with its own advantages and limitations:
- Ceramic Inserts: Excel at high-speed machining applications due to their excellent heat resistance. However, they are more fragile than carbide inserts.
- Cubic Boron Nitride (CBN) Inserts: Offer exceptional wear resistance for machining very hard materials like hardened steel. The downside is their higher cost compared to carbide inserts.
- High-Speed Steel (HSS) Tools: A traditional and cost-effective option, but HSS tools wear out much faster than carbide inserts and require more frequent tool changes.
The best choice depends on your specific machining needs, budget, and material considerations.
Q: Where can I buy standard carbide inserts?
A: Standard carbide inserts are available from a variety of sources, including:
- Machining tool suppliers: These companies offer a wide selection of inserts from various manufacturers.
- Industrial online retailers: Several online platforms specialize in selling industrial cutting tools, including standard carbide inserts.
- Manufacturer websites: Many carbide insert manufacturers sell their products directly through their online stores.
Remember: When purchasing inserts, ensure you choose a reputable brand and the correct insert geometry and grade for your application.
In Conclusion
Standard carbide inserts are a powerful force in the metalworking world. Their exceptional hardness, wear resistance, and versatility make them a go-to choice for various machining applications. By understanding their properties, selecting the right inserts for the job, and following proper care practices, you can unlock the full potential of these remarkable tools and achieve superior results in your metalworking projects.