Carbide inserts are indexable cutting tools essential across metalworking industries for machining components efficiently. This guide covers various special grade carbide insert types, manufacturing methods, key applications and considerations for material selection.
Compositions of special carbide inserts Grades
Grade Family | Major Alloying Elements | Common Grades |
---|---|---|
Coated carbides | TiC, TiCN, TiAlN, AlCrN | GC4225, IC907, AC630 |
Cermets | TiCN–Ni/Mo | TF35, 883 |
CBN/PCBN | CBN, TiC binder | BN250, BZN800 |
Ceramics | Al203, SiC, Si3N4 | CC670, SC850 |
Diamond | CVD/PCD diamond | DA100, PD5100 |
Special carbide inserts utilize exotic coatings, ceramic composites and polycrystalline diamond for extreme hardness, heat resistance and tool life.
Manufacturing Processes
Method | Description |
---|---|
Powder metallurgy | Blended powders compacted and sintered to shape |
Physical vapor deposition | Evaporated metal/ceramic coatings 1-10 μm thick |
Chemical vapor deposition | Diamond film grown on insert substrate |
High pressure high temp | Converts graphite powder into polycrystalline CBN/diamond |
Precision subtractive grinding defines final insert geometries and edge preparations needed for intended operations like turning, milling or drilling.
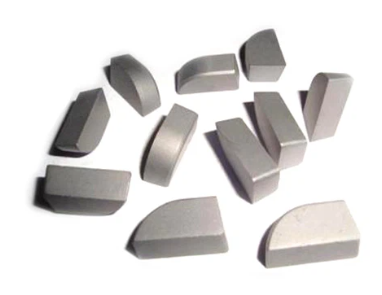
special carbide inserts Typical Applications
Industry | Common Machining Operations |
---|---|
Automotive | High speed machining of engine blocks or drivetrain components |
Aerospace | Difficult to machine alloys, precision boring/drilling |
Die mold | Hardened steels mold and die making |
Medical | Biocompatible alloys, tight tolerance cuts |
Oil and Gas | Turning and boring for valves, compressors, piping |
CBN/ceramic grades boost tool life on hardened ferrous materials. Diamond inserts excel at carbon fiber composites or AlSi alloys for transportation. TiAlN/TiSiN PVD films ideal general purpose stable coatings.
Insert Specifications
Standard | Description |
---|---|
ISO 1832 | Indexable inserts for cutting tools – Designation |
ANSI B212.4-1986 | Carbide Inserts – Identification |
JIS B4104 | Designation of Indexable Inserts |
Standards help classify insert shape, size, tolerance, grade and manufacturer for proper identification and replacement.
Global Suppliers
Company | Grades Offered |
---|---|
Sandvik | GC415, RX720, PC5025 |
Kennametal | KC730, KC935M |
Mitsubishi | VP15TF, SDEH120 |
Sumitomo | AC700G, S700 |
Kyocera | CX610, HD2050 |
All major cutting tool manufacturers offer an extensive range of proprietary insert grades tailored for specific workpiece materials and operating conditions.
Insert Selection Criteria
Key considerations when choosing insert grade:
- Workpiece material type and hardness
- Target cutting parameters (speeds/feeds)
- Cooling method used
- Tolerance and surface finish needs
- Machine tool rigidity and vibration levels
- Relative insert cost vs tool life
Understand machining environment constraints before selecting special grades for cost-effective processes. Get supplier technical support.
Pros vs Cons of Special Insert Grades
Advantages | Disadvantages |
---|---|
Very high metal removal rates | Much higher cost per edge |
Extended and consistent tool life | Limited insert geometries available |
Improved surface finish possible | Need appropriate machine capabilities |
Low forces and power needs | Application support essential |
Can facilitate dry/near dry machining | Changes overall process economics |
Assess specific process benefits against higher insert costs when evaluating special carbide grades.
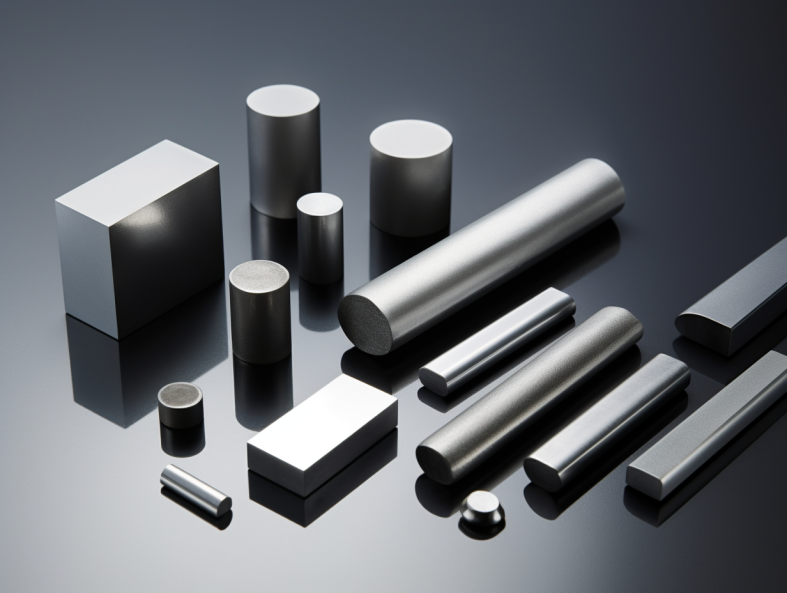
FAQ
How should special coated inserts be handled and stored?
With care to avoid chipping coated edges. No solvent cleaning. Some coatings reactive when heated. Follow manufacturer guidelines on allowable operating environments.
When does using CBN inserts make economic sense?
Typically on stable precision machine tools when machining over 50-60 HRC hardened steels over long production runs. Worthwhen 20-50X tool life increase offsets higher insert cost.
What causes rapid flank wear on ceramic inserts?
Poor surface finish, vibration issues, built up edge due to low feeds/speeds, inadequate coolant impingement, chemical dissolution of binder phase etc. Need rigid machining system.
Why are thicker CVD diamond coatings not necessarily better?
While prolonging substrate exposure, too thick a film strains adhesion and abrades away at cutting edges losing precision. Optimal balancing avoids exponential cost.
Which machining methods can leverage solid CBN (SCBN) inserts?
Applications restricted to non-ferrous alloys like aluminum, brass and copper. Very low thermal expansion combined with extreme hardness makes SCBN inserts too brittle for interrupted cuts.
Conclusion
In closing, special carbide insert grades enable predictable tool life and high performance machining capabilities essential for competitive manufacturing across several modern industries. Careful process analysis and matching grade properties to work environments facilitates productivity gains.