Overview of Sintered Carbide Strips
Sintered carbide strips refer to rectangular precision strip metals made from cemented carbides utilizing powder metallurgy methods involving compacting and sintering carbide powders into high performance wear parts. Key attributes include extreme hardness, strength, and corrosion resistance for cutting tools, forming dies,machine part coatings exposed to demanding conditions.
Table 1: Overview of Sintered Carbide Strips
Key Attributes | Details |
---|---|
Typical Composition | WC-Co with grain growth inhibitors |
Hardness Range | Up to 1900 HV (64 HRC) |
Key Properties | Wear resistance, high strength, hardness at temperature |
Manufacturing Method | Pressing and sintering carbide powders |
Main Applications | Cutting inserts, punching dies, micro drills, nozzles |
With tailored cobalt binder systems concentrating ultrahard carbide grains forged together under heat and pressure, sintered carbide strips offer an unrivaled balance of hardness, fracture toughness, and manufacturability vital for modern machining, metalworking, and industrial wear applications.
Understanding attributes around composition, properties, and fabrication processes assists engineers in specifying the optimal grade matching service conditions and production methods.
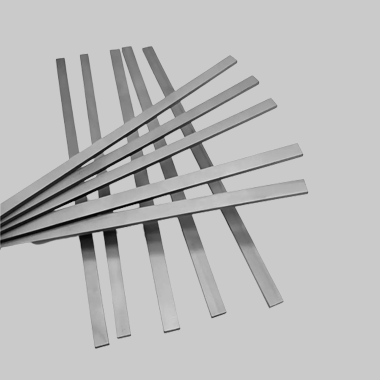
Composition and Microstructure of Sintered Carbide Strips
Sintered carbide strip products utilize powder metallurgy techniques to fuse fine carbide particles with cobalt binder systems under heat and pressure to achieve unique physical properties unrealizable through other manufacturing processes.
Table 2: Typical Compositions of Carbide Strips
Constituent | Role | Weight % Range |
---|---|---|
Tungsten carbide (WC) with grain growth inhibitors | Primary hard phase | 82-97% |
Cobalt (Co) binder | Binder matrix | 3-12% |
Tantalum carbide (TaC) | Inhibits grain growth | 0.4-8% |
Titanium carbide (TiC) | Mixed carbides | 0-5% |
Niobium carbide (NbC) | Grain refinement | 0-2% |
The exceptional hardness stems from extensively fine, interlocked tungsten carbide grains dispersed uniformly through the cobalt matrix. Meanwhile, additions of TaC, TiC, NbC serve to pin grain boundaries preventing uncontrolled grain growth which negatively impacts strength. These compositions are tailored to balance hardness, fracture resistance, and manufacturability for cutting, punching, coining operations.
Understanding microstructure evolution during liquid phase sintering assists engineers in optimizing custom alloys for customer needs regarding wear performance in specific sliding, rolling, or impact service conditions. Carbide grain size, shape, and volume fractions represent key tuning levers.
Properties of Sintered Carbide Strips
Thanks to an optimized balance between hard carbide phases resisting wear coupled with tougher cobalt matrix that limits crack propagation, sintered carbide strips offer a unique combination of properties otherwise unattainable.
Table 3: Overview of Sintered Carbide Strip Properties
Property | Contributing Factors | Typical Values |
---|---|---|
Hardness | Ultrafine WC grains, inhibitors | Up to 1900 HV (64 HRC) |
Transverse rupture strength | Cobalt content, porosity levels | 500-2000 MPa |
Fracture toughness | Cobalt mean free path, grain size | 8-30 MPa-m^1/2 |
Young’s modulus | Relative density, phase composition | 500-700 GPa |
Corrosion resistance | Cobalt/carbide ratio, porosity | Resists most inorganic acids, bases, and salts |
Max service temperature | Phase changes, oxidation resistance | 500-800°C in air |
These attributes satisfy demanding production conditions encompassing high machining forces and temperatures seen in cutting tools plus the repetitive impact stresses when punching or stamping intricate geometries in hardened steels up to 62 HRC.
By tailoring powder composition and pressing parameters before sintering, carbide strips can be customized towards an optimal balance of hardness, strength, and fracture resistance required by the operating environment. These capabilities facilitate substantial performance gains and longer service life over conventional tooling materials.
Production Process for Carbide Strips
Sintered carbide strips leverage powder metallurgy compaction followed by liquid phase sintering to deliver exceptional hardness and strength over competing metal cutting, punching, and wear solutions.
Table 4: Overview of Carbide Strip Production Methods
Stage | Details | Parameters |
---|---|---|
Powder mixing | Carbides + cobalt powders | Chemistry, powder size distribution |
Compaction | Uniaxially pressed in dies | Pressure of 1-4 tons/in2 |
Dewaxing | Thermally remove binders | Time, temperature, atmosphere |
Sintering | Heat to fuse powder particles | Temperature, time, atmosphere control |
Post-processing | Grinding, hone edges | Size and surface tolerance |
By tailoring the powder chemistry, pressing behavior, dewax approach, sintering cycle, and post-processing steps, the microstructure of sintered carbide components evolve dramatically impacting resultant hardness, wear performance and service life in cutting, punching, coining applications.
For example, higher compacting pressures increase densification rates during sintering by facilitating easier binder escape while improved powder flow characteristics help completely fill dies for maximum green density. Understanding connections between processing routes, microscopic structure evolution, and macroscopic properties empowers proper alloy and sinter recipe selections delivering optimal customer results.
Grades and Classifications of Carbide Strips
With different compositions tailored towards distinct machining, metal forming, and wear environments, numerous carbide grade options have emerged classified by properties like hardness, toughness, grain size, or cobalt binder ratio. Common systems include:
Table 5: Classifications of Sintered Carbide Strips
Grade Class | Compositions | Key Features | Typical Uses |
---|---|---|---|
C1–C4 | Mixed carbides with low Co | Exceptional wear performance for interrupted cuts | Cast alloys turning/milling |
P10-P50 | WC-Co up to 10% Co | Higher fracture resistance and edge toughness | Intricate punching/forming operations |
M10-M50 | WC-Co up to 2% Co | Ultrafine grain for superior hardness and polish | Precision boring, gear cutting |
The C-type grades using mixed carbides resist cyclic load variations seen in rough casting/mold machining, while tougher P class formulations accomodate blanking and punching shock stresses.
Meanwhile, finishing applications utilize super-fine grain M class products where maximizing hardness and attaining mirror surface finish are vital. By mapping customer needs and operating parameters appropriately against available compositions in the marketplace via testing, optimal grade selection delivers dramatically extended operational lifetimes translating into substantial per-part cost savings.
Specifications for Sintered Carbide Strips
Thanks to wide adoption across machining and metalworking industries, various national and international specifications exist guiding consistent manufacturing, testing methods, and quality standards for sintered carbide strip products.
Table 6: Standard Specifications for Carbide Strips
Standard | Description | Required Properties | Test Methods |
---|---|---|---|
ISO 513 | Carbide classifications by composition and grain size | Binder content, metallographic grain size | Hardness, bending strength, microstructure |
ASTM B831 | North American specification for sintered carbide plates | Carbide composition ranges | Chemistry, apparent porosity, volume change |
JIS C 4080 | Japanese industrial standard | Grade compositions, tolerances | Transverse rupture strength, corrosion, microhardness |
These standards aim to facilitate customers performing consistent comparisons evaluating factors like:
- Hardness ranges based on common Rockwell C and Vickers scales
- Transverse rupture strength correlating with in-service impact stresses
- Toughness according to various metrologies from Palmqvist crack lengths to fracture mechanics
- Corrosion resistance against organic chemicals or inorganic bases/acids
- Metallographic grain sizes, porosity levels, binder pool formation
With Carbide strip products utilized globally across critical production components, standard methods and quality conformance drive improved consistency, performance benchmarking, and ultimately end-user value creation.
Uses and Applications of Carbide Strips
Thanks to an exceptional balance of hardness, fracture toughness, and corrosion resistance all attainable in geometrically complex shapes using powder metallurgy techniques, sintered carbide strip solutions empower radical performance gains across cutting, punching, and high speed machining arenas.
Table 7: Common Applications for Carbide Strips
Category | Uses | Benefits |
---|---|---|
Cutting tools | Saws, drills, lathe tooling | Increased productivity in alloys |
Metalforming dies | Progressive, fineblanking | Longer life for complex geometries |
Wear parts | Nozzles, drawing dies | Superior abrasion/erosion resistance |
Micro tools | Endmills, routers | Scale intricacy and precision |
While various industries leverage sintered carbides, some notable niche use cases where carbide strips generate tremendous value encompass:
- Enabling miniaturized medical components like stents, valves, actuators in biocompatible grades
- Unlocking up to 20X productivity gains machining exotic alloys for aerospace engines and airframes
- Supporting high capacity automotive panel stamping operations through rapid die changes
- Improving reliability of oil drilling equipment via enhanced downhole sensor packages
- Achieving mirror surface finishes across rolling and slide bearings used in high-end automobile powertrains and performance transmissions
In each situation, exploiting the extreme hardness and tailored cobalt toughening strike the ideal economic balance between operational life and requisite quality or complexity demands currently unattainable with traditional cutting materials.
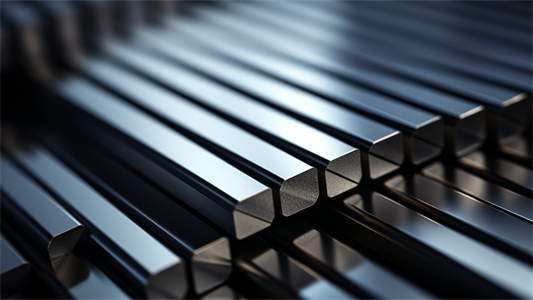
Suppliers of Sintered Carbide Strips
With applications for cemented carbide strip products spanning industries from semiconductors to automobiles to oil exploration, numerous specialized producers offer wide-ranging capabilities globally. Aside from industry leaders, smaller regional experts offer extensive customization services across carbide grade selection, geometry, post-processing, and coating services.
Table 8: Major Sintered Carbide Strip Companies
Supplier | Product Sectors | Production Capabilities |
---|---|---|
Sandvik | Insert grades, round tools | Advanced nano-structured grades, custom geometries |
Ceratizit | Indexable inserts, cutting tools | Complex 6-sided geometries, quick turn tooling concepts |
Tunco Manufacturing | Punching/forming, stamping | Rapid prototyping, short run production |
Precision Carbide | CNC cutting inserts, router bits | Advanced cermet and whisker reinforced compositions |
Mid-America Carbide | Oil/mining components, wear surfaces | Large custom rectangular geometries |
These leading producers offer extensive strip dimension ranges spanning fractions of a millimeter for micro drills and miniature components up to over 500 mm lengths for large indexable inserts servicing heavy roughing cuts. Rectangular widths from under 1 mm to beyond 300 mm also accommodate tiny electrical discharge machining components up to substantial press and form punching elements. With vertical markets constantly evolving metalcutting requirements and innovations around tool geometries, coatings, and custom holder solutions, continued partnerships between customers, carbide producers, equipment OEMs proves vital for advancing performance.
Cost Analysis
Thanks to engineered compositions and tight tolerances, sintered carbide strips sell for many multiples over standard tool steel or stainless steel used for conventional cutting and punching applications. However costs per fabricated part remain highly competitive given significantly longer operational lifetimes in production environments.
Table 9: Price Considerations for Sintered Carbide Strips
Parameter | Price | Commentary |
---|---|---|
Carbide strip blanks | $40-200 per kg | Scaling with grade, hardness, cobalt content |
Insert blanks | $2-10 per in2 | Geometry and size considerations |
Final machined inserts | $4-30 per insert | Tighter tolerances command premium |
Relative lifetime advantage | Up to 20x over tool steel | Reduces cost per hole drilled or parts stamped |
For example:
- Custom rectangular grades for aerospace customers in small batches present costs nearing $150-200/kg.
- Meanwhile larger batches of standard insert geometries in well-established C2-C5 grades range $50-80/kg.
- However, inserts lasting for for example 1000 holes versus 50 holes with tool steel inserts support 8-10x productivity upside per cutting edge, rapidly offsetting higher initial carbide material prices.
By actively mapping detailed cost drivers against value opportunities on parameters like per hole drilled/ stamped part costs compared to current solutions, sintered carbide strips readily justify investments thanks to order of magnitude gains in longevity and associated productivity. Ongoing improvements across powder quality and tool design also continue driving economic advancements over incumbent options across manufacturing sectors.
Future Outlook for Carbide Strip Adoption Trends
Ongoing advances developing tailored powder compositions around manipulated carbide grain sizes and cobalt ratio tuning coupled with innovations in geometries/coatings for custom toolholder solutions points toward an upswing in adoption rates across durable goods manufacturing sectors over the next 5-7 years.
In particular, market analysts predict carbide strip volumes expanding over 7% CAGR globally through 2025 with above average uptake anticipated across aerospace, medical devices, automotive, and energy industries. This uptrend coincides with higher complex, exotic metal usage plus demand for improved productivity and precision in metal cutting/forming operations.
However, price instability around constituent cobalt in formulas paired with energy and transportation cost spikes may momentarily slow growth rates for commoditized lower tier carbide inserts segments catering to general engineering users.
Leading experts encourage domestic raw material production including rare earth mineral refining and independent cobalt sources to hedge against supply chain uncertainties. Cooperatives between manufacturers, government labs, and universities also seek to lower end-user adoption barriers around design, prototyping, testing, and qualification efforts vital for specialized strips displacing conventional tooling.
FAQ
Q: What coating options exist for carbide strips and what benefits do they offer?
A: Common coatings add wear protection, higher lubricity, or heat resistance. Top options include titanium aluminum nitride (TiAlN), titanium nitride (TiN), and diamond-like carbon (DLC) applied via PVD or CVD methods.
Q: What causes cracks in carbide strips and how can they be prevented?
A: Fractures stem from tensile stresses exceeding material strength. Triggers involve mechanical or thermal impacts, fatigue, or corrosive environments. Modulating cobalt content, grain sizes, geometry, and operating conditions preserves toughness.
Q: How weldable are carbide strips using common methods?
A: Carbide cannot be fusion welded. Brazing offers an alternate joining approach for carbide strips using high silver content alloys. Fit-up, joint cleanliness, and process atmosphere control are vital.
Q: What are recommended best practices for machining carbide strips?
A: Rigid setups with sharp tooling and abundant cooling minimizes edge chipping. Slower speeds with positive rake tools and stepped roughing approaches also yield better finish and accuracy over brittle grades.
Q: What industries show the greatest growth potential for carbide strip adoption?
A: Aerospace, medical devices, die mold sectors demonstrate tremendous expansion prospects thanks to expanding usage of difficult exotic alloys combined with rising quality and precision demands unattainable with conventional tooling.