Sintered carbide plates, also known as cemented carbide plates, are made by compacting and sintering powders of refractory metal carbides with metallic binders. They have very high hardness and wear resistance, making them suitable for applications requiring durability under extreme conditions.
Overview of Sintered Carbide Plates
Sintered carbide plates are composite materials that consist of:
- Hard carbide particles like tungsten carbide (WC), titanium carbide (TiC), tantalum carbide (TaC) that provide wear resistance
- Metallic binders like cobalt, nickel or iron that hold the carbide particles together
They are produced through powder metallurgy – compacting and then sintering the powder mixture at high temperatures. This fuses the carbide particles and binder together into a microstructure of carbides dispersed in the binder matrix.
Benefits of Sintered Carbide Plates:
- Extremely high hardness and wear resistance
- Maintain strength at high temperatures
- Resistant to abrasion, erosion and corrosion
- Dimensional stability across range of temperatures
- Tailorable properties by changing powder composition
- Complex geometries can be produced
Applications:
Sintered carbide plates sees use in applications that demand durability under extreme mechanical, thermal or chemical stress:
- Cutting tools, milling, drilling
- Dies, punches
- Seal faces, nozzles
- High wear linings and plates
- Mining and oil drilling equipment
- High temperature furnace elements
Here is a comparison of sintered carbide grades and their properties:
Grade | Hardness (HRA) | Transverse Rupture Strength (MPa) | Key Applications |
---|---|---|---|
P10-P20 | 86-90 | 340-550 | General purpose wear parts |
P30-P40 | 90-94 | 550-970 | Drawing dies, shear blades |
P50-P60 | 92-96 | 690-1100 | Cutting inserts, drilling, milling |
P01 | 89-93 | 480-690 | High temperature and chemically resistant |
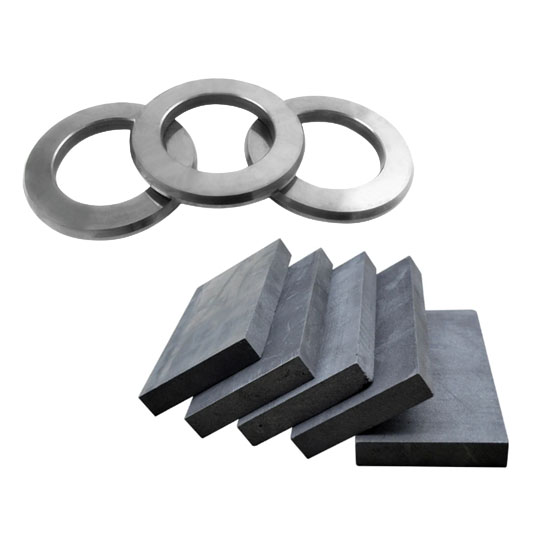
Composition of Sintered Carbide Plates
The key ingredients in sintered carbide plates are:
Carbide Powders:
- Tungsten carbide (WC) – Most widely used due to its wear resistance
- Titanium carbide (TiC) – High hardness at elevated temperatures
- Tantalum carbide (TaC) – Extremely hard with good chemical stability
- Niobium carbide (NbC) – High strength and fracture toughness
Binder Metals:
- Cobalt (Co) – Most common, provides strength and toughness
- Nickel (Ni) – Added for acid resistance
- Iron (Fe) – Cheaper alternative to cobalt
Additional Elements:
- Vanadium, chromium, molybdenum – For inhibition of grain growth
- Carbon, nitrogen – For influencing phase transformations
The composition can be varied to optimize physical, mechanical and chemical properties. Some examples:
Grade | Composition |
---|---|
General purpose | 88% WC – 12% Co |
High toughness | 76% WC – 10% TiC – 14% Co |
High heat resistance | 65% WC – 35% TaC – 9% Co |
Acid resistance | 73% WC – 8% TiC – 8% TaC – 3% Ni – 8% Co |
Properties of Sintered Carbide Plates
The unique properties of sintered carbide plates stem from their special composite microstructure of hard carbide grains supported by a tougher metallic binder matrix:
Physical Properties
Property | Value |
---|---|
Density | 13-16 g/cc |
Porosity | <1% for P/M grades |
Grain size | 1-10 microns |
Coefficient of expansion | 4-6 x 10<sup>-6</sup> /K |
Mechanical Properties
Property | Value |
---|---|
Hardness | Up to 96 HRA (1700 HV) |
Transverse rupture strength | Up to 2.5 GPa |
Compressive strength | Up to 8 GPa |
Fracture toughness | Up to 30 MPa√m |
Young’s modulus | 500-700 GPa |
The physical and mechanical properties can be tailored based on composition, powder characteristics, sintering parameters and heat treatment conditions.
Key Material Characteristics:
- Microstructure with angular carbide grains supported by metallic binder
- High relative density > 98% theoretical density
- Uniform distribution of fine 1-10 micron carbide grains
- Optimal amount of binder for strength and toughness
- Minimal intrinsic defects like pores or cracks
Manufacturing Process for Sintered Carbide Plates
Sintered carbide plates and various products are manufactured through powder metallurgy techniques:
Steps
- Milling: Carbide and binder metal powders are milled together to ensure uniform mixing
- Compacting: Granular powder mix is compacted into desired shapes at pressures of 100-300 MPa
- Debinding: Organic binders are removed from compacted shapes
- Sintering: Green compact is densified by heating to 1400-1500°C in a controlled atmosphere furnace
- Finishing: Sintered parts are ground, machined and lapped to final dimensions
Sintering Process Parameters:
- Temperature: 1350-1500°C
- Atmosphere: Vacuum or inert hydrogen/nitrogen
- Time: Several hours up to tens of hours
- Pressure assist: Hot pressing or hot isostatic pressing
- Cooling rate: Important for development of optimal microstructure
Advanced Manufacturing Methods
- Metal Injection Molding (MIM) allows complex geometries
- Additive Manufacturing (AM) via binder jetting and selective laser melting
- Hybrid Layered Manufacturing (HLM) combines AM and machining
Characteristics and Features
Microstructural Features
- Angular WC grains in Co matrix with some eta phase
- Average WC grain size between 1-10 microns
- Uniform microstructure without abnormally large grains
- Near full density with minimal intrinsic porosity
- No cracks, voids, inclusions or similar defects
Physical Characteristics
- Dense structure with high relative density >98% theoretical
- Uniform shape and geometry per design specifications
- Smooth surface finish under 10 microns Ra
- Chamfered edges or external and internal profiles
- Dimensional tolerance ±0.2% nominal dimension
Mechanical Properties
- Vickers hardness of 1600-1800 HV depending on grade
- Excellent abrasion and erosive wear resistance
- Strong resistance to chipping, cracking or fracturing
- Good edge strength and impact resistance
- Average fracture toughness around 12-18 MPa√m
Performance Characteristics
- Consistent and predictable wear behavior across operating conditions
- Long and reliable tool life under extreme pressures and temperatures
- Excellent thermal shock resistance due to low CTE
- Chemically inert to most acids besides nitric or hydrofluoric
- Minimal corrosion in wet environments
Typical Applications of Sintered Carbide Plates
Due to their optimized balance of hardness, strength and refractory properties, sintered carbide plates offer exceptional service life across the following harsh applications:
Wear and Abrasion Resistance
- Cutting inserts and cutting tools
- Drawing dies
- Nozzles, seals, valve seats
- Pump impellers and casings
- Pelletizing equipment liners
- Chutes, screws, mills in mining industry
High Temperature and Corrosion Resistance
- Kiln cars and furnace linings
- Thermocouple protection tubes
- Sputtering targets in semiconductor industry
- Plungers and stems in chemical industry
Specialized Engineering Applications
- Bulletproof armor and composite plates
- Microdrill bits
- Optics and laser equipment components
For most applications, sintered carbide grades with varying amounts of metallic binders are used based on the level of toughness, impact or thermal shock resistance needed. The appropriate grade, thickness, size and tolerances of the plates can be selected based on service conditions.
Industry | Components | Grade Examples |
---|---|---|
Machining | Cutting Inserts | P25 for steel turning P35 for aluminum machining P50-P60 for high speed machining |
Metal forming | Drawing dies, punches | P20-P40 with Mixed Ceramics |
Oil drilling | Seal faces, fluid nozzles | C1-C3 for erosion resistance C5-C7 for wear resistance |
Size Specifications of Sintered Carbide Plates
Sintered carbide plates are produced in standard and customized sizes with typical thickness ranging from 1 mm to 50 mm. Plates over 4 mm thickness are manufactured by sinter-HIP while thinner 1-3 mm plates can be made by pressing and sintering:
Standard Sizes Available
- Square plates up to 400 mm x 400 mm sizes
- Rectangular plates in various lengths and widths
- Round plates or discs with diameter up to 300 mm
- Cut to size pieces for customer requirements
Thickness Range
- Ultra-thin plates of 0.5 mm to 1 mm thickness
- Standard plates from >1 mm to 4 mm thickness
- Thick plates over 4 mm made via Hot Isostatic Pressing
Dimensional Tolerances
Dimension | Tolerance |
---|---|
Length / Width | ±0.20% |
Thickness | ±0.25% |
Flatness | ±0.10% per 25 mm |
Angularity | 1 degree |
The appropriate plate dimensions – thickness, surface area and size are chosen based on end application requirements. Thicker plates withstand higher loads in wear applications while thin 0.5-1 mm grades are used as seal faces or sputtering targets.
Grades and Standards of Sintered Carbide Plates
Sintered carbide grades have standardized compositions referenced by composite class, powder sources and processes under classification systems published by ISO, ASTM and national standards bodies:
Composite Class
- Cemented carbides designated as P, M or K grades based on structure
- P grades based on WC-Co with various carbide additions
- M grades with Mo additions for high temperature strength
- K grades with NbC and TaC content for wear resistance
Powder Feedstocks
- Carbide powder sources qualified based on purity
- Metallic binder powders must have particle size and shape
- Carbon content, inhibitors, grain growth agents
Classification Standards
Standard | Grades Defined |
---|---|
ISO 513 | Cemented carbide grades composition and application |
ASTM B766 | Requirements for microstructure, physical and mechanical properties |
JIS C 4020 | Japanese industrial standard for cemented carbide grades |
These standards ensure that sintered carbide product specifications and grades have standardized properties globally for quality control and part interchangeability.
Suppliers and Costs of Sintered Carbide Plates
Sintered carbide plates are offered by several global suppliers that specialize in cemented carbides and technical ceramics production. Asian manufacturers dominate the market due to lower raw material and energy costs.
Major Sintered Carbide Suppliers
- Sandvik Hard Materials (Sweden)
- Ceratizit Group (Luxembourg)
- NTK Cutting Tools (Japan)
- Zhuzhou Cemented Carbide (China)
- Tungaloy Corporation (Japan)
Pricing
- Cost per plate depends on size, grade required, order volumes
- Ranges from $5 per piece for P10 grade up to $250 per piece for ultrafine or hot pressed grades
- Average cost is $25-50 per plate for common mid-range grades
Sourcing Considerations
- Lead time for customized grades can be 10-12 weeks
- Ready stock available faster for standard catalog sizes
- Optimal to source via authorized distributors
When estimating budgets, the end application requirements drive material grade selection, which subsequently determines cost per plate. It helps to consult application engineers to select the most cost-effective grade for given working conditions.
Pros vs Cons of Sintered Carbide Plates
Advantages | Disadvantages |
---|---|
Excellent hardness and wear resistance | Brittle with lower fracture toughness |
Strength maintained at high temperatures | Sensitive to thermal shock cracking |
Chemically inert to most acids and solvents | Relatively more expensive than steel |
Consistent and reliable behavior | Needs diamond grinding due to hardness |
Complex shapes can be produced | Lower bend strength compared to steel |
Tailorable via composition and processing | Requires cobalt binder for strength |
Better finish than cast carbides | Difficult to machine due to hardness |
When to Use Sintered Carbide?
Consider sintered carbides when steel cannot survive the operating conditions:
- Extremely abrasive wear
- High load and contact stresses
- Repeated impact or cyclic loading
- Temperatures exceeding 500°C
- Very corrosive chemical exposure
When to Avoid Sintered Carbide?
- For flexible components requiring spring-back
- Applications with possibility of mechanical shock loads
- Situations requiring high fracture toughness
- Cost-driven applications where steel may suffice
For many critical components working under extreme conditions like nozzles, seals and dies, sintered carbide is the best material choice despite higher upfront price.
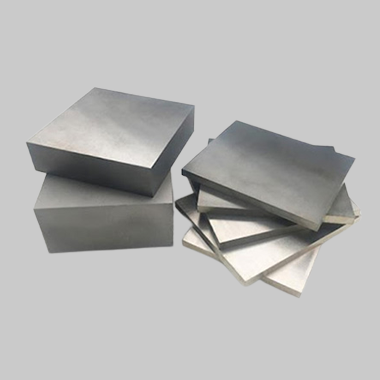
Comparison to Other Carbide Grades
Parameter | Sintered Carbide | Cast Carbide | PVD Coated Carbides |
---|---|---|---|
Composition | WC-Co with sintering | No binder, cast microstructure | WC-Co substrate with PVD coating |
Hardness | Up to 96 HRA | 85-88 HRA | 92-94 HRA |
Transverse rupture strength | 550 – 1100 MPa | 210 – 350 MPa | 500 – 600 MPa |
Fracture toughness | 10 – 25 MPa√m | 3 – 6 MPa√m | 8 – 15 MPa√m |
Chemical resistance | Average | Excellent | Good corrosion protection |
Thermal shock resistance | Fair | Best | Good resistance to thermal fatigue |
Manufacturability | Complex PM parts | Geometry limits for casting | Coating after sintering |
Example applications | Cutting tools, dies | Seal faces, valve parts | Drilling, milling, turning inserts |
Main Differences:
- Cast carbide has lower binder hence extremely brittle
- Sintered grades offer best balance of hardness and toughness via tailored WC-Co composition
- PVD coating improves inertness and oxidation resistance
The optimum carbide solution depends on end application requirements – expected stresses, temperatures, precision needs, etc. Consultation with material experts is recommended.
FAQ
Q: Are sintered carbide plates suitable for use in acids?
A: Sintered carbide plates offer average chemical resistance. Customized grades with nickel binder provide improved resistance to acids. But they should not be used with concentrated HF, HNO3 or hot H2SO4 which attack both WC and binder.
Q: What are the function of grain growth inhibitors in cemented carbides?
A: Small additions of VC, Cr3C2, TaC control WC grain size during sintering. Fine < 2 micron grains improve hardness and strength. Grain growth inhibitors limit Ostwald ripening by forming second phases on WC-Co boundaries.
Q: Should I use grades with higher or lower Cobalt content for my application?
A: Higher 9-15% cobalt binds WC grains improving fracture strength and impact resistance but lowers hardness slightly. Lower 3-6% cobalt maximizes hardness for abrasion resistance but makes product more brittle with lower TRS.
Q: What causes thermal cracks in sintered carbide components?
A: Carbides have much lower thermal expansion relative to steel parts. Rapid heating or cooling induces thermal stresses due to CTE mismatch. These temporary stresses lead to crack initiation and propagation inside the carbide, reducing strength drastically.
Q: How are complex shapes of seals, dies produced from sintered carbide?
A: Complex near-net shape components are manufactured starting from fine powders via powder injection molding. This allows precise components matching the design specifications to be sintered after binder removal and densification.