Imagine this: you’re a sculptor, meticulously shaping a stubborn block of granite. Your chisel, the instrument of your vision, keeps dulling with each forceful strike. Now, picture a revolutionary tool – one that carves through the toughest materials with enduring sharpness. That’s the power of negative rake carbide inserts.
What are Negative Rake Carbide Inserts?
Negative rake carbide inserts are tiny, replaceable cutting edges made from incredibly hard and wear-resistant tungsten carbide. Unlike traditional inserts where the cutting surface is perpendicular to the body (neutral rake), negative rake inserts have a cutting edge that angles away from the workpiece (negative rake). This seemingly subtle difference unlocks a treasure trove of benefits for metalworkers.
The Production Process of Negative Rake Carbide Inserts
Crafting these miniature marvels is a fascinating dance of science and technology. Here’s a glimpse into their creation:
- Powder Preparation: Tungsten carbide powder, the backbone of the insert, is meticulously formulated with specific ratios of other elements like cobalt for strength and toughness.
- Molding and Pressing: The powder is precisely shaped using high-pressure molds, ensuring consistent geometry for each insert.
- Sintering: The molded powder undergoes a high-temperature furnace treatment, fusing the particles into a solid yet highly porous structure.
- Hipping (Hot Isostatic Pressing): Under extreme heat and pressure, the pores in the sintered material are virtually eliminated, resulting in a super-dense and robust insert.
- Grinding: Specialized grinding machines meticulously shape the cutting edge and other features of the insert to precise tolerances.
- Coating (Optional): For enhanced performance, some inserts receive a thin layer of ceramic or other coatings, boosting wear resistance and heat tolerance.
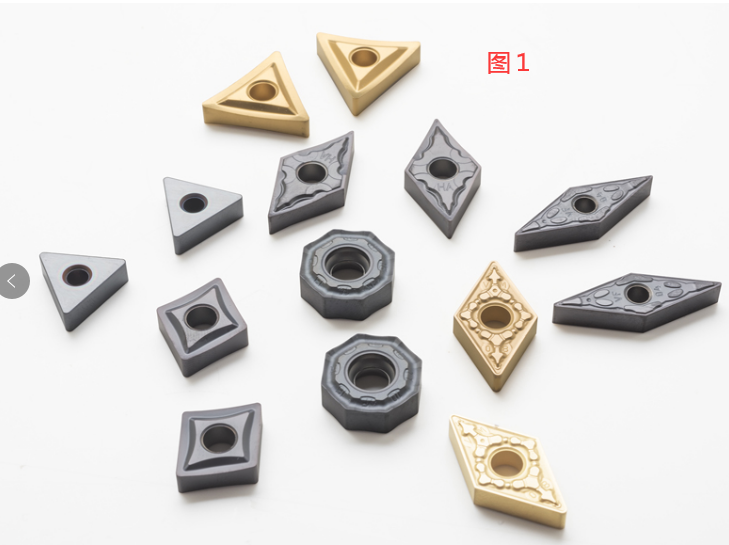
Selection of Negative Rake Carbide Inserts
Choosing the right negative rake carbide insert requires considering several crucial factors:
- Material to be Cut: Different insert grades are formulated to excel with specific materials like steel, stainless steel, cast iron, or aluminum. Consider the material’s hardness, abrasiveness, and machinability.
- Application: Are you roughing out a large workpiece or achieving a fine finish? Roughing applications demand tougher inserts that can withstand heavy chip loads, while finishing requires sharper inserts for a smooth surface.
- Cutting Parameters: Speed, feed rate, and depth of cut all influence insert selection. Higher speeds and deeper cuts often necessitate inserts with superior heat resistance and strength.
- Machine Capability: Ensure your machine has the power and rigidity to handle the cutting forces generated by negative rake inserts, which tend to be higher compared to neutral rake inserts.
Advantages of Negative Rake Carbide Inserts
Negative rake carbide inserts offer a compelling array of advantages that elevate metalworking efficiency and quality:
- Superior Wear Resistance: The negative rake geometry creates a thicker cutting edge, significantly extending insert life compared to neutral rake inserts. This translates to fewer insert changes, reduced downtime, and lower overall machining costs.
- Improved Chip Control: The negative rake angle promotes better chip formation and evacuation, preventing chip buildup that can mar the workpiece surface and damage the cutting tool.
- Enhanced Surface Finish: By minimizing chatter and vibration, negative rake inserts can produce smoother surface finishes, especially advantageous for finishing applications.
- Increased Productivity: The combination of longer insert life and improved chip control leads to increased productivity, allowing you to machine more parts in less time.
- Stronger Cutting Forces: The negative rake geometry allows for heavier cuts and higher feed rates, ideal for high-volume production environments.
Disadvantages of Negative Rake Carbide Inserts
While undeniably powerful, negative rake carbide inserts also have some limitations:
- Higher Initial Cost: Compared to neutral rake inserts, negative rake inserts typically have a higher upfront cost. However, their extended lifespan often offsets the initial investment.
- Higher Cutting Forces: The negative rake design generates more significant cutting forces, requiring a machine with sufficient power and rigidity to handle them effectively.
- Limited Finishing Capabilities: While negative rake inserts can achieve good surface finishes, they might not be the ideal choice for achieving ultra-fine finishes where a neutral or positive rake insert might be preferred.
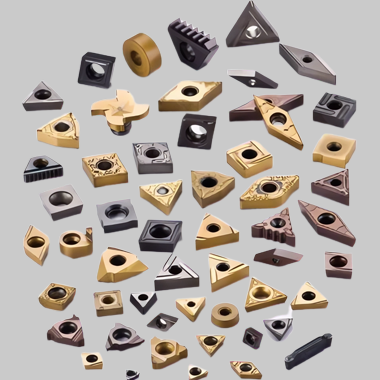
Applications of Negative Rake Carbide Inserts
Negative rake carbide inserts shine in various metalworking applications, including:
- Roughing: Their exceptional wear resistance makes them perfect for removing large amounts of material quickly and efficiently.
- Turning: They excel in turning operations, particularly for high-volume production of shafts, discs, and other cylindrical components.
- Facing: Their ability to generate clean and flat surfaces makes them ideal for facing operations, ensuring proper mating surfaces for components.
- Milling: Specific negative rake insert geometries can be effective in certain milling applications, particularly for roughing and slotting operations.
- Boring: When boring holes with larger diameters, negative rake inserts can provide the necessary strength and wear resistance.
Popular Negative Rake Carbide Insert Geometries
The world of negative rake carbide inserts boasts a diverse range of geometries, each catering to specific machining requirements. Here are some commonly encountered types:
- CNMG: This versatile geometry features a four-corner cutting edge, maximizing insert life and offering multiple cutting positions before requiring indexing.
- SNMG: Similar to CNMG, the SNMG geometry also has four cutting edges but with a sharper cutting point, making it suitable for both roughing and finishing applications.
- TNMG: This triangular insert geometry offers three cutting edges and is often used for high-feed machining due to its excellent chip control characteristics.
- DNMX: This geometry is specifically designed for deep grooving and parting operations, featuring a thick and robust cutting edge.
Coatings and Grades
While geometry plays a crucial role in insert performance, coatings and insert grades further enhance their capabilities.
- Coatings: Inserts can be coated with various materials like titanium nitride (TiN), titanium aluminum nitride (TiAlN), and diamond-like carbon (DLC) to improve wear resistance, reduce friction, and enhance heat dissipation. The specific coating chosen depends on the material being machined and the machining conditions.
- Grades: Insert manufacturers offer a wide range of insert grades, each formulated with a specific combination of carbide grain size, cobalt content, and other elements. The grade selection hinges on the material being machined, with harder grades better suited for abrasive materials and softer grades preferred for softer materials and achieving smooth finishes.
Examples of Leading Negative Rake Carbide Insert Manufacturers
The market for negative rake carbide inserts is populated by a multitude of reputable manufacturers. Here are a few prominent players:
- Kennametal: A renowned cutting tool leader, Kennametal offers a comprehensive range of negative rake carbide inserts in various geometries, grades, and coatings.
- Sandvik Coromant: Another industry giant, Sandvik Coromant is known for its innovative insert designs and high-performance coatings, ensuring optimal insert performance.
- Mitsubishi Materials: A Japanese multinational, Mitsubishi Materials is a frontrunner in carbide technology, offering a diverse selection of negative rake carbide inserts for diverse applications.
- OSG (Oriental SYSCON Corporation): A leading Japanese manufacturer, OSG is recognized for its high-quality inserts and commitment to technological advancements.
- Sumitomo Tool Corporation: Another Japanese powerhouse, Sumitomo Tool Corporation offers a vast selection of negative rake carbide inserts catering to a wide spectrum of machining needs.
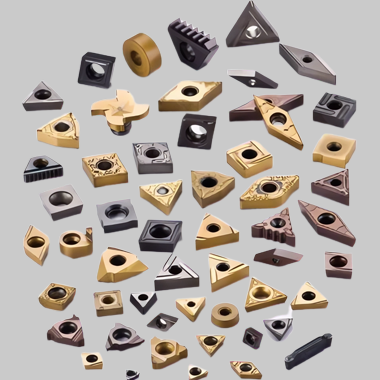
Tips for Choosing Negative Rake Carbide Inserts
Selecting the optimal negative rake carbide insert requires careful consideration of several factors:
- Consult the Manufacturer’s Recommendations: Insert manufacturers provide extensive technical data and application guides to assist you in choosing the most suitable inserts for your specific needs.
- Seek Expert Advice: If you’re unsure about insert selection, don’t hesitate to consult with a cutting tool distributor or a machining expert. Their experience can prove invaluable in making an informed decision.
- Consider Trial Inserts: Many manufacturers offer trial insert programs that allow you to test different inserts in your own machining environment before committing to a larger purchase.
Negative Rake Carbide Inserts vs. Neutral Rake Carbide Inserts
Here’s a head-to-head comparison of negative rake and neutral rake carbide inserts to help you understand their relative strengths and weaknesses:
Feature | Negative Rake Carbide Inserts | Neutral Rake Carbide Inserts |
---|---|---|
Cutting Edge Angle | Negative | Neutral (perpendicular to the body) |
Wear Resistance | Superior | Good |
Chip Control | Excellent | Moderate |
Surface Finish | Good (especially for roughing) | Excellent (ideal for finishing) |
Cutting Forces | Higher | Lower |
Initial Cost | Higher | Lower |
Applications | Roughing, turning, facing, some milling | Finishing, turning, milling |
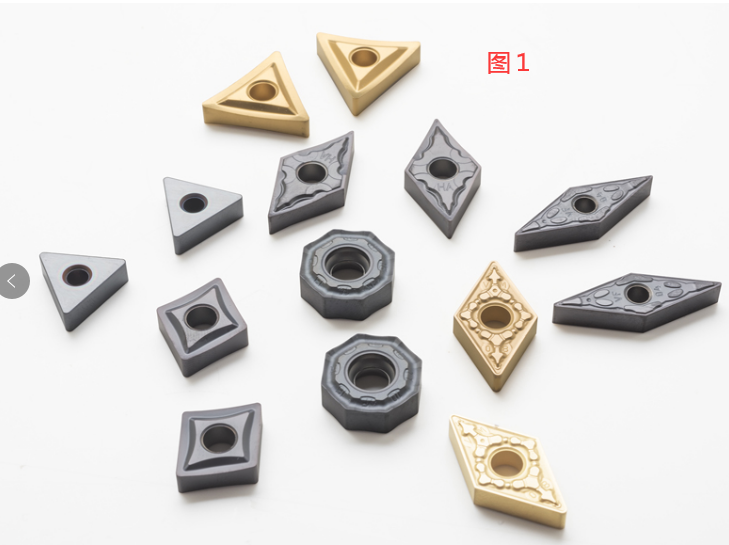
The Future of Negative Rake Carbide Inserts
- Advanced Materials: As the demand for machining ever-tougher materials like high-strength steels and superalloys grows, insert manufacturers will continue to develop even more robust and wear-resistant negative rake carbide insert grades.
- Intelligent Inserts: The integration of sensor technology into inserts could pave the way for “smart” inserts that monitor cutting forces, temperatures, and other parameters, enabling real-time process optimization and predictive maintenance.
- Sustainable Manufacturing: The development of eco-friendly coatings and more efficient insert production processes will be at the forefront, minimizing the environmental impact of negative rake carbide inserts.
FAQ
Q: Are negative rake carbide inserts always the best choice?
A: Not necessarily. While they excel in roughing and high-volume production, negative rake inserts might not be the optimal solution for achieving ultra-fine finishes where a neutral or positive rake insert might be preferred. Additionally, their higher cutting forces necessitate a machine with sufficient power and rigidity.
Q: How often should I change negative rake carbide inserts?
A: The insert change frequency depends on various factors like the material being machined, cutting parameters, and insert wear. Regularly inspecting the insert for signs of wear like chipping, cracking, or excessive flank wear is crucial. Most manufacturers provide guidelines for insert replacement based on specific application parameters.
Q: Can negative rake carbide inserts be sharpened?
A: In most cases, no. Due to their small size and the precise geometry, sharpening negative rake carbide inserts is generally not recommended or cost-effective. However, some manufacturers offer specialty inserts designed for regrinding.
Q: How should I store negative rake carbide inserts?
A: To preserve their sharpness and prevent damage, store negative rake carbide inserts in their original packaging or a designated insert holder. Keep them in a dry and clean environment away from excessive heat or moisture.
In Conclusion
Negative rake carbide inserts have revolutionized metalworking, offering a potent blend of wear resistance, chip control, and productivity. By understanding their properties, selecting the right inserts for your application, and staying informed about the latest advancements, you can leverage these remarkable tools to achieve superior machining results and elevate your workshop’s capabilities.