Introduction
Definition of micrograin carbide blanks
Micrograin carbide blanks are high-performance materials used in various industries, particularly in the manufacturing and machining sector. These blanks are made from a fine-grained carbide material, which gives them exceptional hardness, strength, and wear resistance. The term ‘micrograin’ refers to the small grain size of the carbide particles used in the production of these blanks, resulting in a dense and uniform structure. Micrograin carbide blanks are commonly used in the production of cutting tools, such as drills, end mills, and inserts, as well as in the fabrication of wear parts and components for machinery and equipment. Their superior properties make them ideal for applications that require precision, durability, and high performance.
Importance of micrograin carbide blanks
Micrograin carbide blanks play a crucial role in various industries due to their exceptional properties. These blanks are made from a fine-grained carbide material, which results in a dense and uniform structure. This characteristic allows micrograin carbide blanks to have excellent hardness, wear resistance, and toughness. They are widely used in the manufacturing of cutting tools, such as drills, end mills, and inserts, as well as in the production of wear parts and precision components. The importance of micrograin carbide blanks lies in their ability to provide superior performance and durability, leading to improved productivity and cost-effectiveness in machining operations. With their high strength and resistance to wear, micrograin carbide blanks are essential for achieving precision and efficiency in various applications across industries.
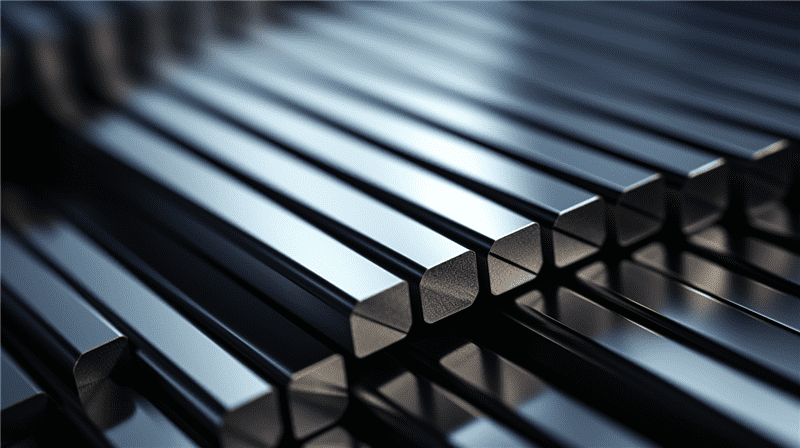
Applications of micrograin carbide blanks
Micrograin carbide blanks have a wide range of applications in various industries. One of the key applications of micrograin carbide blanks is in the manufacturing of cutting tools. These blanks are known for their high hardness and wear resistance, making them ideal for the production of precision cutting tools such as drills, end mills, and reamers. Additionally, micrograin carbide blanks are also used in the production of molds and dies, where their excellent dimensional stability and thermal conductivity are highly valued. Furthermore, these blanks find applications in the aerospace and automotive industries, where they are used for machining complex parts and components. Overall, the versatility and performance of micrograin carbide blanks make them an essential material in various applications across different industries.
Properties of Micrograin Carbide Blanks
High hardness and wear resistance
Micrograin carbide blanks are known for their high hardness and wear resistance. These blanks are made from fine-grain carbide materials, which undergo a specialized manufacturing process to enhance their properties. The high hardness of micrograin carbide blanks makes them ideal for applications that require cutting, drilling, or milling tough materials such as stainless steel, cast iron, and hardened alloys. Additionally, their exceptional wear resistance ensures long tool life and reduces the need for frequent replacements. Whether in the automotive, aerospace, or manufacturing industries, micrograin carbide blanks are a reliable choice for achieving precise and efficient machining results.
Excellent heat resistance
Micrograin carbide blanks exhibit excellent heat resistance. This unique property makes them highly suitable for applications that involve high temperatures and thermal stress. The micrograin structure of the carbide blanks enhances their ability to withstand extreme heat, ensuring their durability and performance in demanding conditions. Whether it is in the aerospace industry, automotive sector, or manufacturing processes, micrograin carbide blanks offer exceptional heat resistance, providing reliable and long-lasting performance.
Superior toughness and impact resistance
Micrograin carbide blanks possess superior toughness and impact resistance, making them highly sought after in various industries. These blanks are specially engineered to withstand heavy loads and harsh operating conditions, ensuring reliable performance and extended tool life. The micrograin structure of the carbide material provides exceptional strength and durability, allowing the blanks to effectively resist chipping, cracking, and wear. Whether used in cutting tools, molds, or wear parts, micrograin carbide blanks deliver exceptional performance and longevity, making them the preferred choice for demanding applications.
Manufacturing Process
Selection of raw materials
Micrograin carbide blanks are a crucial component in various industries, especially in the manufacturing sector. The selection of raw materials plays a significant role in determining the quality and performance of these blanks. When it comes to micrograin carbide blanks, manufacturers carefully choose the raw materials to ensure superior strength, hardness, and wear resistance. The use of high-quality carbide materials with fine grain size allows for precise machining and excellent surface finish. Additionally, the selection process involves considering factors such as chemical composition, purity, and uniformity to achieve consistent and reliable results. Overall, the meticulous selection of raw materials for micrograin carbide blanks is essential to meet the demanding requirements of modern industrial applications.
Powder metallurgy process
The powder metallurgy process is a manufacturing method used to produce micrograin carbide blanks. This process involves the blending of fine metal powders, such as tungsten and cobalt, with a binder material. The mixture is then compacted into a desired shape and subjected to high temperatures and pressures in a sintering furnace. During sintering, the binder material is removed, and the metal powders are fused together to form a solid, dense carbide blank. The micrograin structure of the carbide blank provides excellent hardness, toughness, and wear resistance, making it suitable for various industrial applications, including cutting tools and wear parts.
Sintering and post-processing
Sintering and post-processing play a crucial role in the production of micrograin carbide blanks. Sintering is a process in which the powdered carbide material is heated to a high temperature, causing the particles to bond together and form a solid mass. This step is essential for achieving the desired density and strength of the carbide blanks. Post-processing involves various treatments such as grinding, polishing, and coating to refine the surface finish and improve the overall quality of the blanks. These processes ensure that the micrograin carbide blanks meet the stringent requirements of precision machining applications, providing exceptional hardness, wear resistance, and dimensional stability.
Advantages of Micrograin Carbide Blanks
Extended tool life
Micrograin carbide blanks offer an extended tool life, making them a preferred choice for various machining applications. These blanks are manufactured using a fine-grained carbide material, which provides exceptional hardness and wear resistance. With their superior durability, micrograin carbide blanks can withstand high-speed machining operations, reducing the need for frequent tool replacements. This not only improves productivity but also lowers manufacturing costs. Additionally, the extended tool life of micrograin carbide blanks ensures consistent performance and precision, resulting in high-quality finished products. Whether it’s milling, drilling, or turning, these blanks deliver exceptional performance and reliability, making them an ideal option for industries that require long-lasting cutting tools.
Improved cutting performance
Micrograin carbide blanks have revolutionized cutting performance in various industries. With their fine grain structure and high hardness, these blanks offer exceptional strength and durability. They provide improved cutting performance by reducing tool wear and increasing tool life. The precision and sharpness of micrograin carbide blanks enable efficient material removal and enhance the overall cutting process. Additionally, their superior heat resistance allows for higher cutting speeds and feeds, resulting in faster and more efficient machining operations. Overall, the use of micrograin carbide blanks in cutting applications has significantly enhanced productivity and quality in the manufacturing sector.
Enhanced productivity
Micrograin carbide blanks are known for their ability to enhance productivity in various industries. With their fine grain structure and high hardness, these blanks are designed to withstand the most demanding machining applications. They provide superior wear resistance, allowing for longer tool life and reduced downtime. Additionally, micrograin carbide blanks offer excellent thermal conductivity, ensuring efficient heat dissipation during machining processes. This results in improved cutting speeds and higher material removal rates, leading to enhanced productivity and cost savings. Whether it’s in the automotive, aerospace, or manufacturing sector, the use of micrograin carbide blanks can significantly boost efficiency and overall performance.
Applications of Micrograin Carbide Blanks
Metalworking industry
The metalworking industry plays a vital role in various manufacturing processes, and one important aspect of this industry is the use of micrograin carbide blanks. These carbide blanks are highly durable and offer exceptional performance in cutting, drilling, and shaping metal materials. With their fine grain structure, micrograin carbide blanks provide superior strength and wear resistance, making them ideal for precision machining applications. Moreover, their high thermal conductivity helps to dissipate heat during machining, resulting in improved tool life and reduced machining costs. In the metalworking industry, micrograin carbide blanks have become essential tools for achieving high-quality and efficient metal processing.
Woodworking industry
The woodworking industry has greatly benefited from the use of micrograin carbide blanks. These high-quality blanks provide exceptional durability and precision, making them ideal for various woodworking applications. Whether it’s shaping, cutting, or carving, micrograin carbide blanks offer superior performance and longevity. Woodworkers can rely on these blanks to deliver precise and clean cuts, resulting in high-quality craftsmanship. Additionally, the use of micrograin carbide blanks reduces the need for frequent tool replacements, saving both time and money for woodworking professionals. Overall, micrograin carbide blanks have revolutionized the woodworking industry by enhancing productivity, accuracy, and cost-efficiency.
Automotive industry
Micrograin carbide blanks have become an essential component in the automotive industry. With their exceptional hardness and durability, these carbide blanks are used in various applications such as cutting tools, dies, and molds. Their high wear resistance allows them to withstand the demanding conditions of the automotive manufacturing process, ensuring precision and efficiency. Additionally, micrograin carbide blanks offer superior performance in machining operations, delivering precise and smooth finishes. As the automotive industry continues to evolve, the demand for micrograin carbide blanks is expected to rise, making them a crucial material for the production of high-quality automotive components.
Conclusion
Summary of key points
Micrograin carbide blanks are a type of material widely used in various industries. These blanks are known for their exceptional hardness, durability, and resistance to wear and tear. They are commonly used in the manufacturing of cutting tools, such as drills, end mills, and inserts, as well as in the production of wear-resistant parts and components. The micrograin structure of these carbide blanks allows for superior performance and precision in machining operations. Additionally, their high heat resistance makes them suitable for use in high-speed machining applications. Overall, micrograin carbide blanks play a crucial role in enhancing productivity and efficiency in the manufacturing sector.
Future prospects
The future prospects for micrograin carbide blanks are promising. With advancements in technology and increasing demand for precision machining, micrograin carbide blanks offer numerous benefits. These blanks are known for their high hardness, wear resistance, and excellent thermal conductivity, making them ideal for applications in industries such as aerospace, automotive, and medical. Additionally, the ability of micrograin carbide blanks to maintain their shape and dimension even under extreme conditions further enhances their appeal. As the manufacturing industry continues to evolve and demand for high-performance materials grows, the future of micrograin carbide blanks looks bright.
Final thoughts
In conclusion, micrograin carbide blanks are an essential tool in various industries. Their high hardness, wear resistance, and toughness make them ideal for applications that require precision and durability. Whether used in cutting tools, molds, or other machining applications, micrograin carbide blanks provide superior performance and longevity. Additionally, their fine grain structure ensures consistent and reliable performance, making them a preferred choice for professionals. With their exceptional properties, micrograin carbide blanks continue to play a crucial role in advancing technology and driving innovation in manufacturing processes.