Introduction
Definition of Carbide Rods
Carbide rods are a type of tooling material that are widely used in various industries, including manufacturing and construction. These rods are made from a combination of carbide and other metals, which gives them exceptional hardness and durability. The main purpose of carbide rods is to provide a cutting or drilling surface that can withstand high temperatures and heavy loads. They are commonly used in applications such as milling, drilling, and turning, where precision and reliability are crucial. Carbide rods offer superior performance compared to traditional steel rods, making them a preferred choice for many professionals in the industry.
Applications of Carbide Rods
Carbide rods are widely used in various applications due to their exceptional hardness and durability. One of the main applications of carbide rods is in the manufacturing of cutting tools, such as drills, end mills, and reamers. The high hardness of carbide rods allows these cutting tools to withstand high temperatures and maintain sharp edges, resulting in improved cutting performance and longer tool life. Additionally, carbide rods are also used in the production of wear-resistant parts, such as nozzles, dies, and molds. The superior wear resistance of carbide rods ensures the longevity and efficiency of these parts, even under harsh operating conditions. Furthermore, carbide rods find applications in the woodworking industry, where they are used to make router bits and saw blades. The hardness and strength of carbide rods enable these tools to cut through various types of wood with precision and ease. Overall, the applications of carbide rods are vast and diverse, making them an essential component in many industries.
Importance of Carbide Rods in Manufacturing
Carbide rods play a crucial role in the manufacturing industry due to their numerous benefits and applications. These rods are made from a combination of carbon and metal, making them highly durable and resistant to wear and tear. One of the key advantages of carbide rods is their exceptional hardness, which allows them to withstand high temperatures and pressures. This makes them ideal for use in cutting tools, such as drills and end mills, where precision and longevity are essential. Additionally, carbide rods offer excellent performance in machining operations, providing superior cutting speeds and improved tool life. The use of carbide rods in manufacturing ensures enhanced productivity and efficiency, leading to cost savings and improved product quality. Overall, the importance of carbide rods in manufacturing cannot be overstated, as they enable the production of high-quality products with precision and reliability.
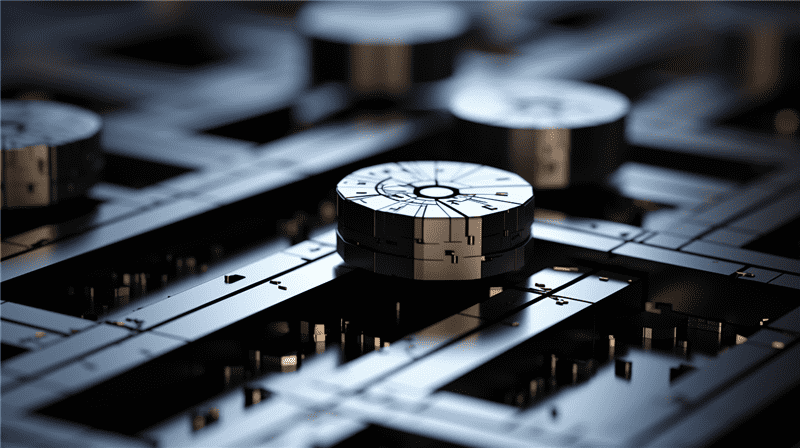
Properties of finished carbide rods
Hardness
Carbide rods are known for their exceptional hardness, making them a popular choice in various industries. The hardness of these rods is achieved through a combination of high-quality materials and precise manufacturing processes. This hardness allows carbide rods to withstand extreme conditions and resist wear and tear, making them ideal for applications that require high levels of durability and strength. Additionally, the hardness of carbide rods ensures excellent performance and longevity, making them a reliable option for professionals and enthusiasts alike.
Wear Resistance
Carbide rods are widely used in various industries due to their exceptional wear resistance. The unique composition of carbide materials, such as tungsten carbide, provides high hardness and toughness, making them ideal for applications that involve heavy wear and abrasion. The wear resistance of carbide rods ensures a longer lifespan and reduces the need for frequent replacements, resulting in cost savings for businesses. Additionally, the superior wear resistance of carbide rods allows for increased productivity and efficiency in machining operations, as they can withstand high-speed cutting and drilling without significant wear or damage. Overall, the wear resistance of carbide rods plays a vital role in enhancing the performance and durability of various tools and components in industries such as automotive, aerospace, and manufacturing.
Heat Resistance
Heat resistance is a crucial factor when it comes to evaluating the quality of finished carbide rods. These rods are designed to withstand high temperatures without losing their structural integrity or performance. The heat resistance of carbide rods is determined by the composition of the materials used and the manufacturing processes involved. By ensuring superior heat resistance, carbide rods can be relied upon for various applications that involve extreme heat conditions, such as metal cutting, drilling, and machining. The ability of finished carbide rods to maintain their strength and hardness at elevated temperatures makes them a preferred choice in industries where thermal stability is paramount. With their exceptional heat resistance, carbide rods provide reliable and long-lasting performance, ensuring efficiency and precision in demanding operations.
Manufacturing Process
Raw Material Selection
Raw material selection is a crucial step in the production of finished carbide rods. The quality and performance of these rods greatly depend on the type of raw materials used. Careful consideration is given to factors such as purity, hardness, and composition when selecting the raw materials. High-quality tungsten carbide and cobalt are typically chosen for their excellent wear resistance and strength. By choosing the right raw materials, manufacturers can ensure that the finished carbide rods meet the highest standards of quality and durability.
Mixing and Grinding
Mixing and grinding are essential processes in the production of finished carbide rods. During the mixing phase, various raw materials are combined to create a homogeneous mixture. This ensures that the carbide rods have consistent composition and properties. The grinding process involves shaping and refining the carbide rods to achieve the desired dimensions and surface finish. It requires precision and expertise to ensure that the rods meet the required specifications. Both mixing and grinding play a crucial role in the manufacturing of high-quality finished carbide rods.
Molding and Sintering
Molding and sintering are crucial steps in the production of finished carbide rods. During the molding process, a mixture of tungsten carbide powder and a binder material is shaped into the desired form using specialized molds. This ensures that the rods have the correct dimensions and geometry. Once molded, the rods are then subjected to a sintering process. Sintering involves heating the molded rods in a controlled environment to a high temperature, causing the tungsten carbide particles to bond together and form a solid structure. This process enhances the strength and durability of the carbide rods, making them suitable for various industrial applications. Molding and sintering are integral to achieving the desired quality and performance of finished carbide rods.
Types of Carbide Rods
Solid Carbide Rods
Solid carbide rods are a type of tooling material that is widely used in various industries. These rods are made from a combination of tungsten carbide and cobalt, which gives them exceptional hardness and durability. They are commonly used in the manufacturing of cutting tools, such as drills, end mills, and reamers. Solid carbide rods are known for their high heat resistance, allowing them to withstand the extreme temperatures generated during machining operations. Additionally, they have excellent wear resistance, ensuring a longer tool life and reducing the need for frequent replacements. With their superior performance and reliability, solid carbide rods are an essential component in the production of precision components and parts.
Tungsten Carbide Rods
Tungsten Carbide Rods are a type of high-performance cutting tool used in various industries, including manufacturing, construction, and mining. These rods are made of a combination of tungsten and carbon, which results in a strong and durable material that can withstand extreme conditions. The finished carbide rods are meticulously crafted to ensure precision and accuracy in cutting applications. With their excellent hardness and wear resistance, tungsten carbide rods are highly sought after for their ability to deliver efficient and reliable performance. Whether it’s for drilling, milling, or turning, these rods are essential tools for achieving optimal results in machining operations. In addition, the versatility of tungsten carbide rods allows them to be used in a wide range of applications, making them a valuable asset for any industry.
Titanium Carbide Rods
Titanium carbide rods are a type of carbide rod that has been finished to meet specific requirements. These rods are made from a combination of titanium and carbon, resulting in a material that is extremely strong and durable. The finishing process involves shaping and polishing the rods to ensure they have a smooth surface and precise dimensions. This allows them to be used in various applications, such as cutting tools, drills, and wear-resistant parts. The high hardness and excellent thermal stability of titanium carbide rods make them suitable for demanding industrial environments. With their exceptional properties and quality finishing, titanium carbide rods are essential components in many industries.
Applications
Metal Cutting
Metal cutting is a fundamental process in the manufacturing industry. It involves the removal of material from a workpiece to create a desired shape or size. One of the key tools used in metal cutting is the carbide rod. Carbide rods are made from a combination of tungsten carbide and cobalt, making them extremely durable and resistant to wear. These rods are commonly used in industries such as aerospace, automotive, and machining. The finished carbide rods undergo a series of precision grinding and polishing processes to ensure their accuracy and smooth surface finish. With their exceptional hardness and toughness, finished carbide rods are essential for achieving high precision and efficiency in metal cutting operations.
Woodworking
Woodworking is a versatile and creative craft that involves shaping and transforming wood into functional and aesthetic objects. Whether it’s crafting furniture, carving intricate designs, or building structures, woodworking offers endless possibilities for those with a passion for working with their hands. One important aspect of woodworking is the use of high-quality tools and materials, such as finished carbide rods. These rods, made from durable and long-lasting carbide, are essential for precision cutting and shaping wood. With finished carbide rods, woodworkers can achieve clean and precise cuts, resulting in beautifully crafted pieces. Whether you’re a seasoned professional or a beginner, incorporating finished carbide rods into your woodworking projects will undoubtedly enhance the quality and precision of your work.
Mining and Construction
Mining and construction industries heavily rely on carbide rods for their various applications. These durable and high-performance rods are widely used in drilling, cutting, and shaping hard materials such as rocks, concrete, and metals. Carbide rods provide excellent strength, wear resistance, and heat resistance, making them ideal for demanding mining and construction tasks. With their exceptional performance and reliability, carbide rods have become an essential tool in the advancement of mining and construction projects, ensuring efficient and precise operations.
Advantages and Disadvantages
Advantages of Carbide Rods
Carbide rods offer numerous advantages in various industries. Firstly, they have exceptional hardness and wear resistance, making them ideal for applications that require cutting, drilling, or machining. Additionally, carbide rods have excellent heat resistance, allowing them to withstand high temperatures without deformation or loss of performance. Another advantage of carbide rods is their corrosion resistance, ensuring their durability and longevity. Moreover, these rods have high strength and toughness, enabling them to handle heavy loads and intense working conditions. Lastly, carbide rods have a longer lifespan compared to other materials, reducing the need for frequent replacements and resulting in cost savings. Overall, the advantages of carbide rods make them a reliable and efficient choice for various industrial applications.
Disadvantages of Carbide Rods
Carbide rods, despite their many advantages, also have some notable disadvantages. One major drawback is their brittleness. Due to their high hardness, carbide rods are prone to cracking or breaking under excessive stress or impact. This limits their application in certain industries where toughness and durability are paramount. Another disadvantage is their high cost. Carbide rods are generally more expensive than other types of tooling materials, making them less accessible to smaller businesses or individuals. Additionally, carbide rods require specialized equipment and expertise for proper handling and machining, further adding to the overall cost. Despite these disadvantages, carbide rods remain a popular choice for many applications due to their exceptional hardness, wear resistance, and heat resistance.
Comparison with Other Materials
Carbide rods have gained popularity in various industries due to their exceptional properties and performance. When compared to other materials, such as steel and ceramic, carbide rods offer superior hardness, wear resistance, and high temperature resistance. This makes them ideal for applications that require cutting, drilling, and milling. Additionally, carbide rods have excellent dimensional stability and can maintain their shape even under extreme conditions. Their exceptional strength-to-weight ratio also makes them a preferred choice in industries where lightweight and durable materials are essential. Overall, the use of carbide rods in various industries has revolutionized manufacturing processes and improved efficiency and productivity.