Welcome to the ultimate guide on finish grind carbide strips customized. If you’re delving into the world of precision machining and tooling, you’ve probably heard a lot about carbide strips. They are integral to many manufacturing processes due to their exceptional hardness, wear resistance, and versatility. This article aims to provide you with a comprehensive understanding of finish grind carbide strips customized, their types, applications, properties, and much more. Let’s get started!
Overview
Finish grind carbide strips are essential components used in various industries for their remarkable durability and performance in high-stress environments. These strips are made from tungsten carbide powder, which is known for its incredible hardness and resistance to wear and tear. Customizing these strips allows them to meet specific requirements of different applications, making them highly valuable in sectors such as aerospace, automotive, and manufacturing.
Key Details of Finish Grind Carbide Strips Customized:
- Material: Tungsten carbide
- Applications: Cutting tools, wear parts, industrial machinery
- Properties: High hardness, wear resistance, toughness
- Customization: Tailored to specific sizes, shapes, and tolerances
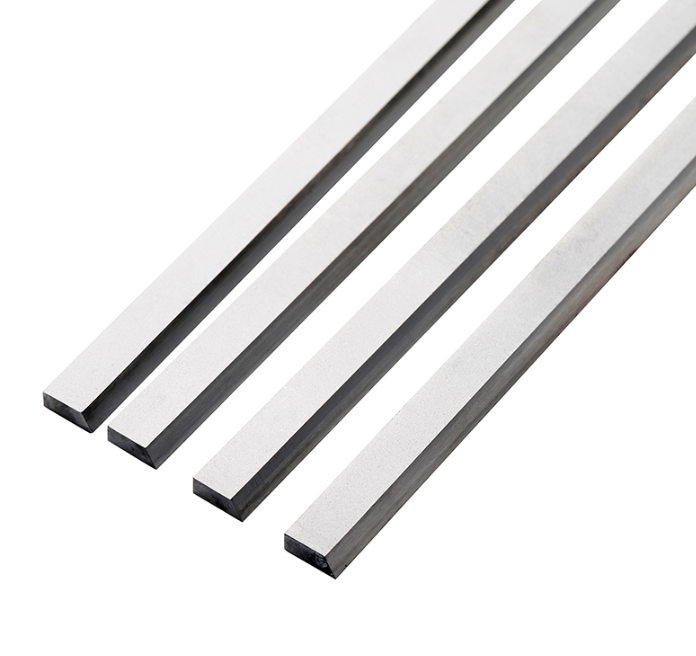
Types of Finish Grind Carbide Strips Customized
To give you a clearer picture, here’s a breakdown of the various types of finish grind carbide strips customized based on their specific applications and properties.
Type | Description |
---|---|
Standard Strips | Basic strips for general purposes, available in various standard sizes. |
High Precision Strips | Strips ground to tight tolerances for high-precision applications. |
Wear-Resistant Strips | Enhanced wear resistance for longer lifespan in abrasive environments. |
Heat-Treated Strips | Designed to withstand high temperatures without losing hardness. |
Impact-Resistant Strips | Optimized for applications involving high impact or shock loads. |
Corrosion-Resistant Strips | Suitable for use in corrosive environments, offering high chemical resistance. |
Custom Alloy Strips | Made with specific alloy compositions to meet unique application needs. |
High Toughness Strips | Balances hardness and toughness for better performance in demanding tasks. |
Coated Strips | Surface coatings for additional protection and performance enhancement. |
Reinforced Strips | Designed with added reinforcement for extreme durability and strength. |
Applications of Finish Grind Carbide Strips Customized
Finish grind carbide strips find their use in a wide range of applications. Here’s a detailed table showing where and how they are used.
Application | Description |
---|---|
Cutting Tools | Used in the production of cutting tools for metalworking and woodworking. |
Wear Parts | Essential in machinery parts that undergo high friction and wear. |
Industrial Machinery | Integral components in heavy machinery used in manufacturing and production lines. |
Aerospace | Used in high-stress aerospace components due to their superior performance characteristics. |
Automotive | Applied in various automotive parts that require high durability and wear resistance. |
Mining Equipment | Utilized in the harsh conditions of mining operations for their toughness and longevity. |
Construction Tools | Employed in the production of construction tools such as drills and saws. |
Textile Machinery | Used in parts of textile machines that require precision and wear resistance. |
Energy Sector | Components in power generation equipment, especially in renewable energy technologies. |
Medical Devices | Incorporated in medical devices that demand precision and high performance under stress. |
Material Properties of Finish Grind Carbide Strips
Understanding the material properties of finish grind carbide strips is crucial for selecting the right type for your application. Here’s a comprehensive table detailing these properties.
Property | Description |
---|---|
Hardness | Exceptionally high hardness, typically measured on the Rockwell or Vickers scales. |
Wear Resistance | High resistance to wear and abrasion, ensuring long-lasting performance. |
Toughness | Balances hardness with toughness to prevent cracking and chipping. |
Thermal Stability | Maintains performance at high temperatures, crucial for cutting and machining applications. |
Corrosion Resistance | Resistant to various chemicals and corrosive environments, extending their lifespan. |
Density | High density, contributing to their robustness and durability. |
Strength | Superior strength, capable of withstanding high stress and impact loads. |
Fracture Toughness | Measures the material’s ability to resist crack propagation. |
Elastic Modulus | Indicates the material’s stiffness and rigidity. |
Thermal Conductivity | Efficient heat dissipation properties, essential for high-speed machining applications. |
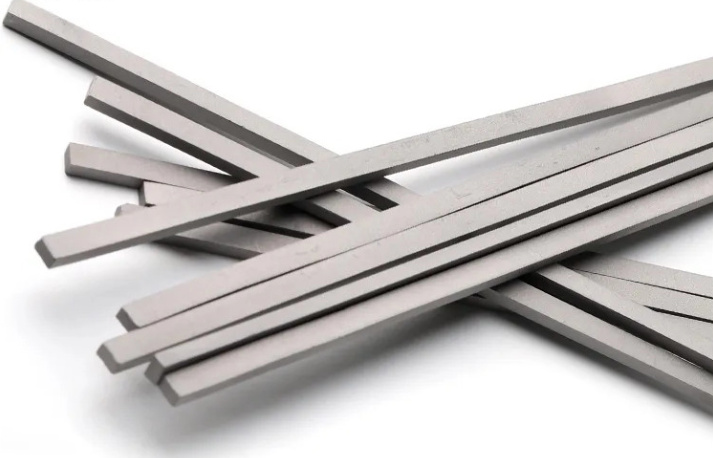
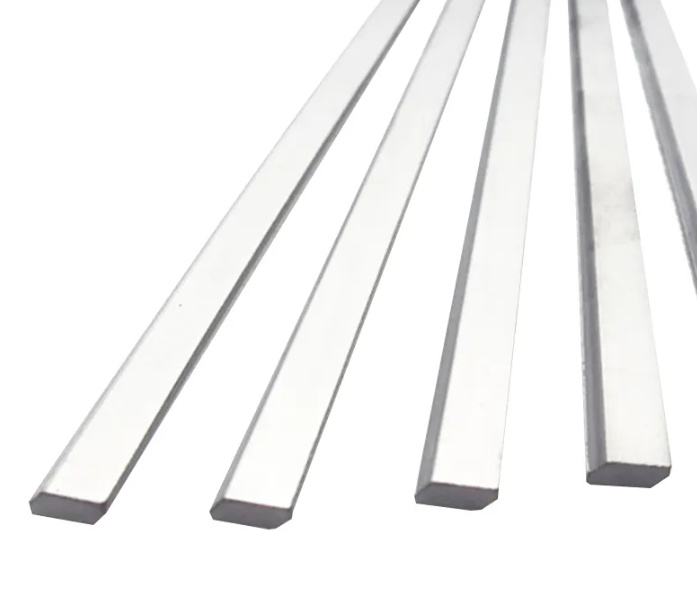
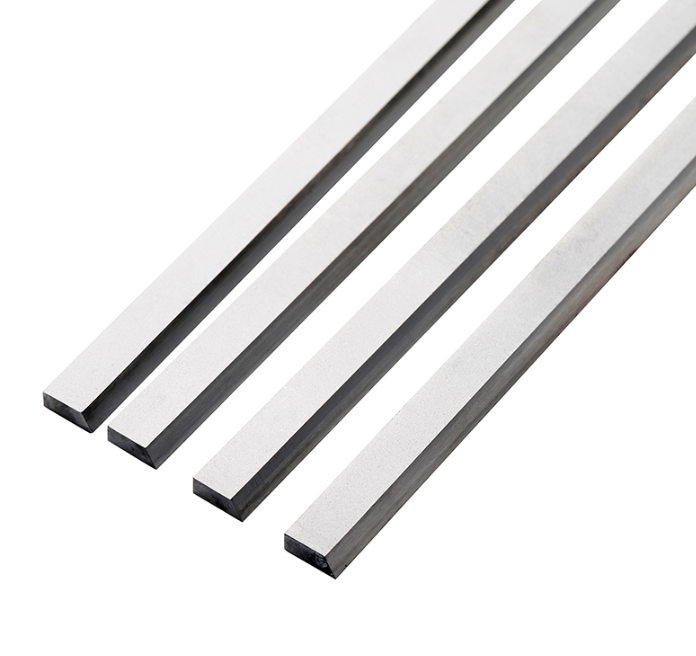
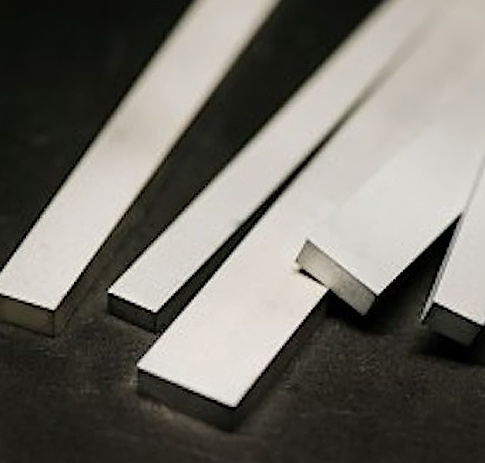
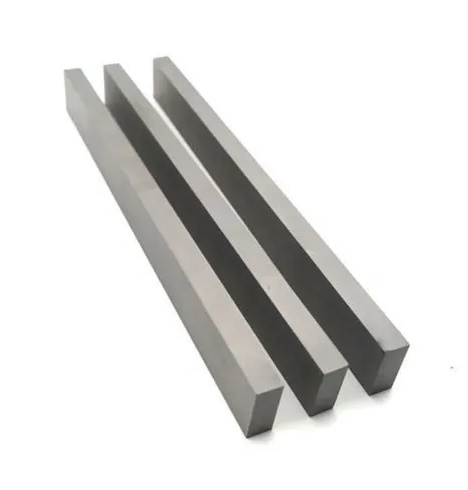
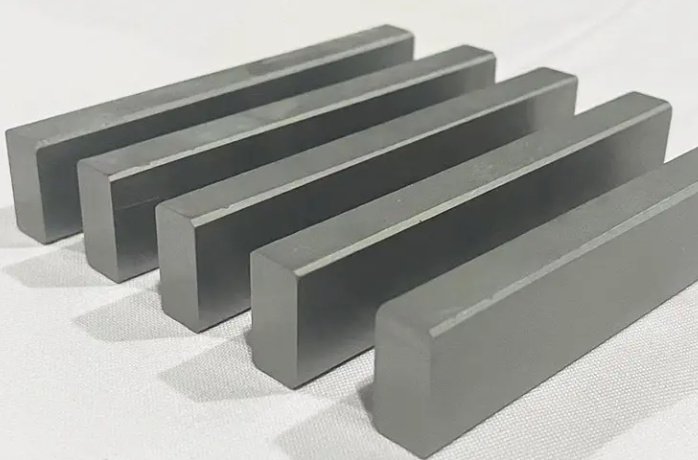
Composition, Properties, and Characteristics
To delve deeper into the specifics, here’s a table summarizing the composition, properties, and characteristics of various tungsten carbide grades used in finish grind strips.
Grade | Composition | Hardness | Wear Resistance | Toughness | Application |
---|---|---|---|---|---|
WC-6%Co | 94% Tungsten Carbide, 6% Cobalt | 92 HRA | High | Medium | General purpose cutting tools |
WC-10%Co | 90% Tungsten Carbide, 10% Cobalt | 88 HRA | Medium | High | Heavy-duty machining |
WC-12%Co | 88% Tungsten Carbide, 12% Cobalt | 86 HRA | Medium | Very High | Impact-resistant applications |
WC-15%Co | 85% Tungsten Carbide, 15% Cobalt | 84 HRA | Medium | Very High | High impact tools |
WC-TiC-Co | Tungsten Carbide, Titanium Carbide, Cobalt | 90 HRA | Very High | Medium | Abrasive wear parts |
WC-Ni | Tungsten Carbide, Nickel Binder | 89 HRA | High | Medium | Corrosion-resistant applications |
WC-Fe | Tungsten Carbide, Iron Binder | 87 HRA | Medium | High | General industrial applications |
WC-20%Co | 80% Tungsten Carbide, 20% Cobalt | 82 HRA | Medium | Very High | Heavy wear parts |
WC-Cr3C2 | Tungsten Carbide, Chromium Carbide | 90 HRA | High | Medium | High temperature applications |
WC-NiCr | Tungsten Carbide, Nickel-Chromium Binder | 88 HRA | High | Medium | Corrosion and heat-resistant |
Hardness, Strength, and Wear Resistance
When selecting carbide strips, understanding the hardness, strength, and wear resistance is crucial. Here’s a detailed table that compares these properties across different grades.
Grade | Hardness (HRA) | Compressive Strength (MPa) | Wear Resistance | Toughness |
---|---|---|---|---|
WC-6%Co | 92 | 3000 | High | Medium |
WC-10%Co | 88 | 2500 | Medium | High |
WC-12%Co | 86 | 2300 | Medium | Very High |
WC-15%Co | 84 | 2200 | Medium | Very High |
WC-TiC-Co | 90 | 2800 | Very High | Medium |
WC-Ni | 89 | 2600 | High | Medium |
WC-Fe | 87 | 2400 | Medium | High |
WC-20%Co | 82 | 2000 | Medium | Very High |
WC-Cr3C2 | 90 | 2700 | High | Medium |
WC-NiCr | 88 | 2500 | High | Medium |
Specifications, Sizes, Shapes, Standards
Customization allows carbide strips to be tailored to specific needs. Here’s a table summarizing the common specifications, sizes, shapes, and standards available.
Specification | Description |
---|---|
Size Range | Lengths from 50mm to 500mm, widths from 10mm to 100mm, thicknesses from 2mm to 20mm |
Shapes | Rectangular, square, round, and custom shapes |
Standards | ISO, ASTM, DIN,JIS |
Surface Finish | Ground, polished, and coated |
Tolerance | Up to ±0.01mm for high precision applications |
Customization Options | Specific sizes, shapes, compositions, and surface treatments as per client requirements |
Heat Treatment | Options for stress relieving, annealing, and other thermal processes |
Coatings | TiN, TiC, TiCN, and other coatings for enhanced performance |
Binder Types | Cobalt, nickel, iron, and custom binder compositions |
Grain Sizes | Ultra-fine, fine, medium, coarse |
Suppliers and Pricing Details
Finding the right supplier is key to obtaining high-quality finish grind carbide strips. Here’s a table with supplier information and pricing details.
Supplier | Location | Product Range | Pricing (USD) | Contact Information |
---|---|---|---|---|
Kennametal | USA | Wide range of carbide strips and custom solutions | $20 – $200 per piece | www.kennametal.com |
Sandvik | Sweden | High-quality carbide products | $25 – $250 per piece | www.sandvik.com |
Ceratizit | Luxembourg | Custom carbide solutions | $30 – $300 per piece | www.ceratizit.com |
Sumitomo Electric | Japan | Advanced carbide technologies | $35 – $350 per piece | www.sumitomoelectric.com |
Guhring | Germany | Precision carbide tools | $40 – $400 per piece | www.guhring.com |
Komet | Germany | Innovative carbide products | $45 – $450 per piece | www.kometgroup.com |
Mitsubishi Materials | Japan | Comprehensive carbide solutions | $50 – $500 per piece | www.mitsubishicarbide.com |
ISCAR | Israel | High-performance carbide tools | $55 – $550 per piece | www.iscar.com |
YG-1 | South Korea | Diverse carbide product range | $60 – $600 per piece | www.yg1.kr |
Walter AG | Germany | Premium carbide solutions | $65 – $650 per piece | www.walter-tools.com |
Selecting the Right Finish Grind Carbide Strips Customized
Choosing the right carbide strip can be a daunting task. Here’s a table to help you understand the factors you need to consider and how to select the right strip for your application.
Factor | Consideration |
---|---|
Application | Determine the specific application and its requirements (e.g., cutting, wear resistance, impact resistance). |
Material Grade | Select the appropriate grade based on hardness, toughness, and wear resistance. |
Size and Shape | Ensure the size and shape match the application requirements. |
Tolerance | Choose the tolerance level required for your precision needs. |
Surface Finish | Consider the type of surface finish needed (e.g., ground, polished, coated). |
Cost | Balance the cost against the performance and lifespan of the strip. |
Supplier Reputation | Choose a reputable supplier known for quality and reliability. |
Customization Options | Look for suppliers that offer customization to meet specific needs. |
Environmental Factors | Consider factors such as temperature, corrosion, and wear conditions. |
Support and Service | Evaluate the level of support and service provided by the supplier. |
Advantages and Limitations
Understanding the pros and cons of finish grind carbide strips can help you make an informed decision. Here’s a comparison table highlighting the advantages and limitations.
Aspect | Advantages | Limitations |
---|---|---|
Durability | Extremely durable and long-lasting | Higher initial cost compared to other materials |
Performance | Superior performance in high-stress and high-temperature environments | Requires precise machining and handling |
Customization | Can be customized to meet specific application requirements | Longer lead times for custom orders |
Wear Resistance | High resistance to wear and abrasion | May be overkill for low-stress applications |
Toughness | Balances hardness with toughness to prevent cracking | Limited flexibility in certain shapes and sizes |
Thermal Stability | Maintains properties at high temperatures | Potential brittleness under certain conditions |
Versatility | Suitable for a wide range of applications | Specialized equipment needed for manufacturing |
Strength | High compressive strength and impact resistance | More challenging to work with compared to softer materials |
Consistency | Consistent performance and reliable quality | Limited availability of certain grades or compositions |
Environmental Resistance | Resistant to corrosion and chemicals | May require specific coatings for extreme environments |
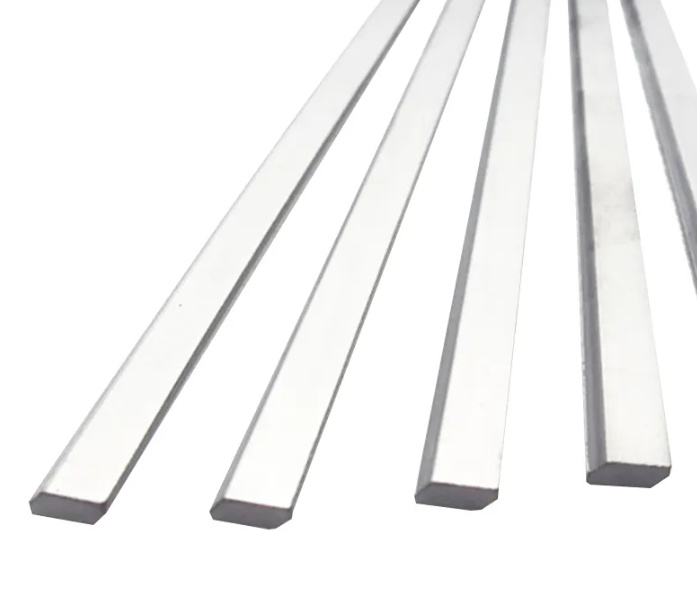
FAQs
To wrap up, here are some frequently asked questions about finish grind carbide strips customized.
Question | Answer |
---|---|
What are finish grind carbide strips? | These are tungsten carbide strips that have been precision ground to meet specific application needs. |
Why customize carbide strips? | Customization ensures the strips meet exact specifications for performance, size, and shape. |
How do I choose the right carbide strip? | Consider application requirements, material grade, size, shape, tolerance, and cost. |
What industries use carbide strips? | Aerospace, automotive, manufacturing, mining, construction, and more. |
What are the benefits of carbide strips? | High durability, wear resistance, thermal stability, and customization. |
Are carbide strips expensive? | They can be more expensive than other materials but offer superior performance and longevity. |
Can carbide strips be recycled? | Yes, tungsten carbide is recyclable, and many suppliers offer recycling services. |
What are the common sizes of carbide strips? | Sizes vary widely, with common lengths from 50mm to 500mm, widths from 10mm to 100mm, and thicknesses from 2mm to 20mm. |
How are carbide strips made? | They are typically made from tungsten carbide powder, which is pressed, sintered, and ground to the desired shape and size. |
What coatings are available for carbide strips? | Common coatings include TiN, TiC, and TiCN, which enhance performance and durability. |
In conclusion, finish grind carbide strips customized offer unmatched performance for a variety of industrial applications. Whether you need standard strips or highly customized solutions, understanding the properties, applications, and selection criteria is essential. With this comprehensive guide, you’re well-equipped to make informed decisions and optimize your operations with the right carbide strips.