Overview of Finish Grind Carbide Strips
Finish grind carbide strips are a crucial component in various industrial applications, renowned for their durability, hardness, and wear resistance. These strips are primarily used in cutting, machining, and abrasive operations, offering high performance and longevity. As a result, they are highly sought after in industries such as automotive, aerospace, and manufacturing.
In this article, we will delve into the world of finish grind carbide strips, exploring their types, applications, material properties, and how to choose the right manufacturer. We will also compare different metal powder models and provide detailed tables for easy reference.
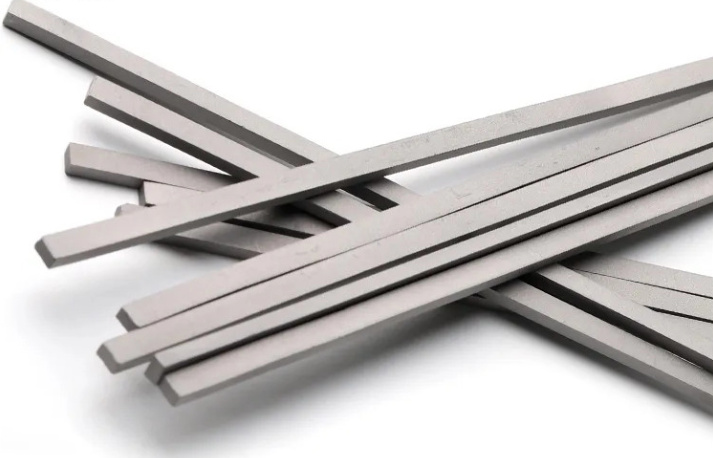
Types of Finish Grind Carbide Strips
Different types of finish grind carbide strips are available, each designed for specific applications and performance requirements. Here is a detailed table summarizing the types of finish grind carbide strips:
Type | Description |
---|---|
Solid Carbide Strips | Made entirely from tungsten carbide, these strips offer maximum hardness and wear resistance. |
Cobalt-Bonded Strips | Featuring a cobalt binder, these strips provide enhanced toughness and impact resistance. |
Nickel-Bonded Strips | Using nickel as a binder, these strips are known for their excellent corrosion resistance. |
Titanium Carbide Strips | Combines titanium with carbide for improved high-temperature stability and wear resistance. |
Multilayered Strips | Composed of multiple layers of different carbide compositions to optimize performance in varied conditions. |
Micro-Grain Carbide Strips | These strips have a fine grain structure, offering superior edge retention and sharpness. |
Coated Carbide Strips | Features a coating such as TiN or TiC to enhance surface hardness and reduce friction. |
Reinforced Carbide Strips | Designed with additional reinforcement for applications requiring extreme durability. |
Customized Strips | Tailored to specific customer requirements for unique applications. |
Applications of Finish Grind Carbide Strips
Finish grind carbide strips are used across a variety of industries. Here is a comprehensive table of applications:
Application | Description |
---|---|
Cutting Tools | Used in the manufacture of saw blades, milling cutters, and drills. |
Machining | Essential in precision machining operations for metal and non-metal materials. |
Abrasive Tools | Employed in grinding wheels and other abrasive tools for material removal. |
Woodworking | Utilized in tools for cutting, shaping, and finishing wood products. |
Mining and Construction | Key component in tools and machinery for mining, drilling, and construction activities. |
Automotive | Integral in manufacturing automotive components, ensuring high precision and durability. |
Aerospace | Critical in producing aerospace parts that demand exceptional strength and wear resistance. |
Medical Instruments | Used in creating medical cutting tools and devices that require precise, sterile operations. |
Metal Forming | Applied in tools for metal stamping, bending, and forming processes. |
Electronic Components | Essential in the production of electronic parts requiring high precision and wear resistance. |
Material Properties of Finish Grind Carbide Strips
Understanding the material properties of finish grind carbide strips is crucial for selecting the right type for specific applications. The table below highlights these properties:
Property | Description |
---|---|
Hardness | Measures the ability to resist deformation and wear. |
Toughness | Indicates the material’s ability to absorb energy and resist fractures. |
Wear Resistance | Defines the material’s ability to withstand surface wear and abrasion. |
Compressive Strength | The capacity to withstand loads tending to reduce size. |
Thermal Conductivity | The ability to conduct heat, important for high-temperature applications. |
Corrosion Resistance | Resistance to chemical deterioration and oxidation. |
Density | The mass per unit volume, influencing the weight and stability of the strips. |
Fracture Toughness | Measures the material’s ability to resist crack propagation. |
Young’s Modulus | Indicates the stiffness of the material. |
Coefficient of Thermal Expansion | The rate at which the material expands with temperature changes. |
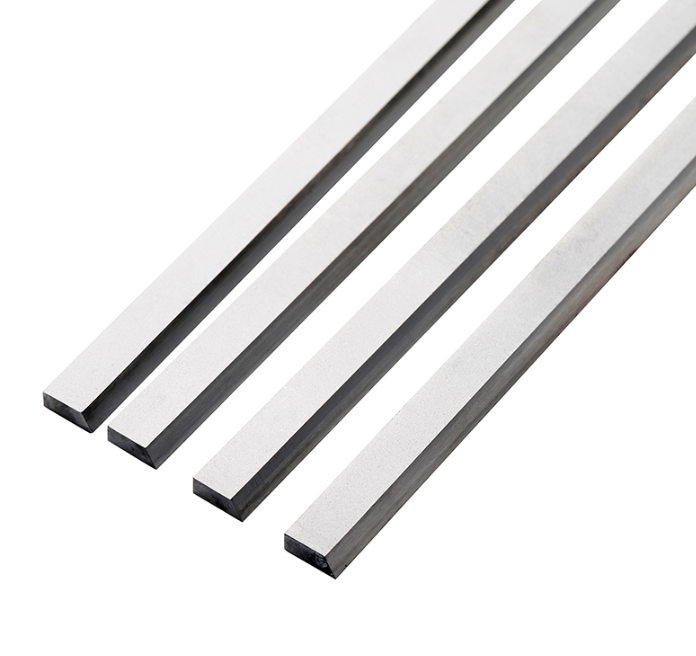
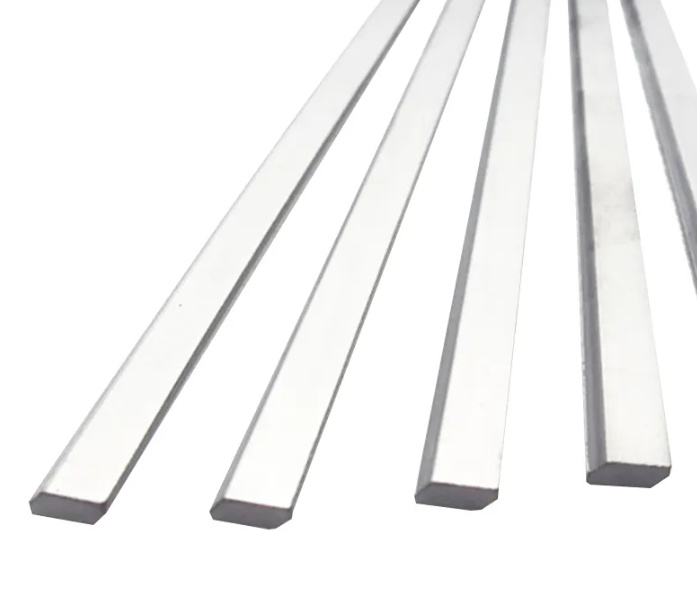
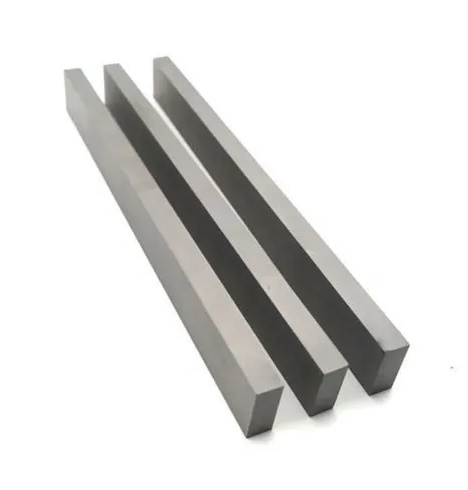
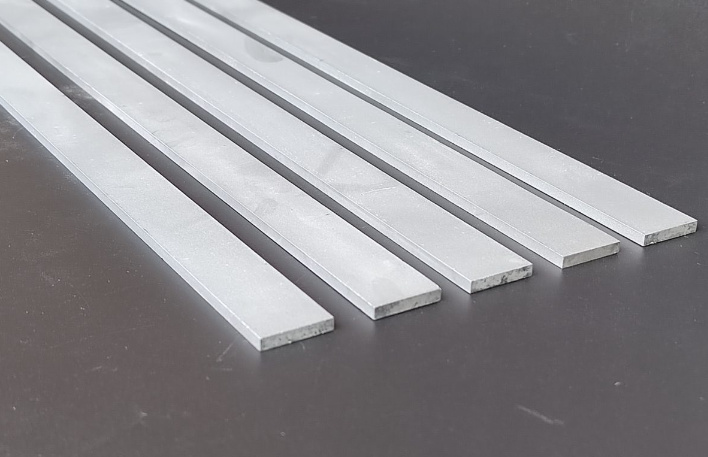
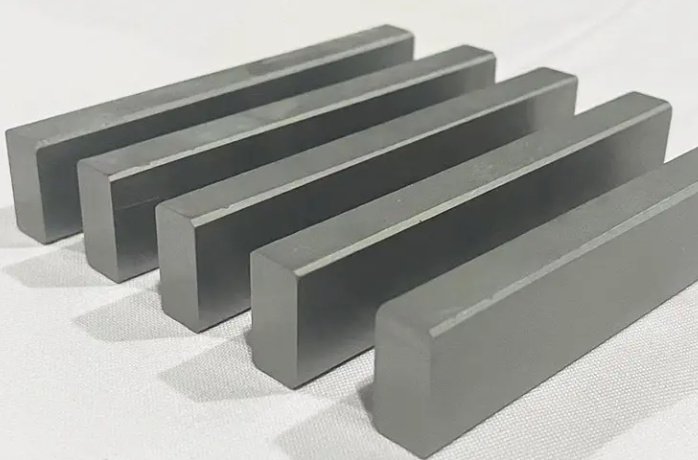
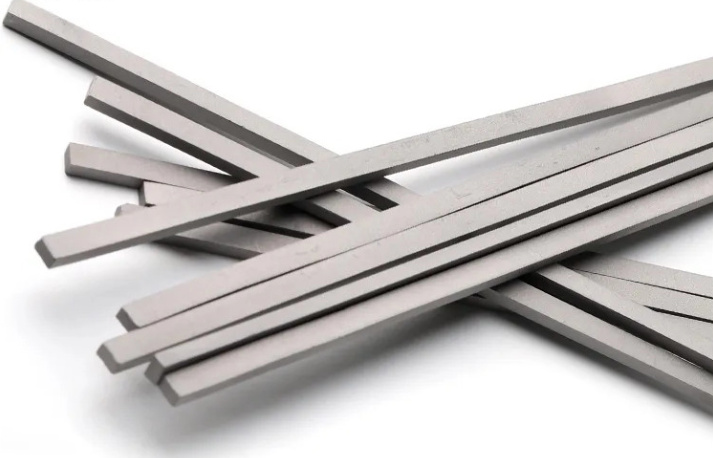
Composition, Properties, and Characteristics
The composition of finish grind carbide strips significantly affects their performance. The following table outlines the typical composition and characteristics:
Component | Percentage | Characteristic |
---|---|---|
Tungsten Carbide | 70-97% | Provides extreme hardness and wear resistance. |
Cobalt | 3-30% | Acts as a binder, enhancing toughness and impact resistance. |
Nickel | Up to 20% | Increases corrosion resistance and toughness. |
Titanium Carbide | Up to 10% | Improves high-temperature stability and wear resistance. |
Vanadium Carbide | Up to 2% | Enhances grain growth control and abrasion resistance. |
Tantalum Carbide | Up to 3% | Increases hardness and oxidation resistance at high temperatures. |
Chromium Carbide | Up to 5% | Adds corrosion resistance and hardness. |
Other Elements | Variable | Can be added to customize properties for specific applications. |
Hardness, Strength, and Wear Resistance
The hardness, strength, and wear resistance of finish grind carbide strips are key parameters influencing their performance. Here’s a detailed comparison:
Parameter | Value Range | Description |
---|---|---|
Hardness (Vickers) | 1300-2000 HV | Indicates the material’s resistance to indentation. |
Compressive Strength | 4000-7000 MPa | Measures the ability to withstand compressive loads. |
Wear Resistance | High | Defines the material’s ability to resist surface wear and abrasion. |
Fracture Toughness | 10-15 MPa·m^1/2 | Indicates the material’s resistance to crack propagation. |
Young’s Modulus | 500-700 GPa | Reflects the stiffness of the material. |
Thermal Conductivity | 50-100 W/m·K | The ability to conduct heat, important for dissipating thermal loads. |
Coefficient of Thermal Expansion | 4-7 µm/m·K | The rate at which the material expands with temperature changes. |
Density | 14.5-15.5 g/cm^3 | The mass per unit volume, affecting weight and stability. |
Specifications, Sizes, Shapes, and Standards
Finish grind carbide strips come in various specifications, sizes, shapes, and standards to meet diverse application needs. Here’s a comprehensive overview:
Specification | Details |
---|---|
Sizes | Length: 50-200 mm, Width: 10-50 mm, Thickness: 2-10 mm |
Shapes | Rectangular, Square, Customized |
Standards | ISO, ASTM, DIN, JIS, Customized |
Tolerances | Tight tolerances available for precision applications |
Surface Finish | Polished, Ground, Coated |
Edge Configurations | Sharp, Beveled, Rounded |
Special Features | Corrosion-resistant coatings, High-temperature capabilities, Reinforced layers |
Suppliers and Pricing Details
Choosing the right supplier is essential for obtaining high-quality finish grind carbide strips at competitive prices. Here’s a detailed table of suppliers and pricing:
Supplier | Location | Product Range | Pricing (per kg) | Special Offers |
---|---|---|---|---|
Kennametal | USA | Solid Carbide, Cobalt-Bonded, Nickel-Bonded | $50-$100 | Bulk discounts, Custom orders |
Sandvik | Sweden | Multilayered, Micro-Grain, Coated | $60-$110 | Free shipping on large orders |
Ceratizit | Luxembourg | Solid Carbide, Reinforced, Customized | $55-$105 | Volume discounts, Custom solutions |
Sumitomo Electric | Japan | Solid Carbide, Titanium Carbide, Micro-Grain | $65-$115 | Technical support, OEM services |
Zhuzhou Cemented Carbide | China | Cobalt-Bonded, Nickel-Bonded, Customized | $45-$95 | Competitive pricing, Custom designs |
Mitsubishi Materials | Japan | Multilayered, Coated, Reinforced | $70-$120 | Exclusive deals, Custom fabrication |
H.C. Starck | Germany | Solid Carbide, Micro-Grain, Coated | $55-$100 | Technical assistance, Custom orders |
Hyperion Materials & Technologies | USA | Solid Carbide, Multilayered, Titanium Carbide | $60-$110 | Special promotions, Custom solutions |
IMC Group | Israel | Cobalt-Bonded, Nickel-Bonded, Customized | $50-$105 | Bulk purchase discounts, Custom orders |
Seco Tools | Sweden | Solid Carbide, Reinforced, Customized | $65-$115 | Free technical support, Custom designs |
Selecting the Right Finish Grind Carbide Strips Manufacturers
Choosing the right manufacturer involves considering various factors such as product quality, pricing, technical support, and customization options. Here is a detailed table to guide you in selecting the right finish grind carbide strips manufacturer:
Factor | Consideration |
---|---|
Product Quality | Look for manufacturers with a reputation for high-quality products and strict quality control. |
Pricing | Compare pricing across multiple suppliers to find competitive rates without compromising quality. |
Technical Support | Ensure the manufacturer offers robust technical support and after-sales service. |
Customization Options | Choose manufacturers that provide customization to meet specific application requirements. |
Lead Times | Consider the lead times for production and delivery to ensure timely supply. |
Certifications | Verify that the manufacturer holds relevant certifications such as ISO, ASTM, etc. |
Customer Reviews | Check customer reviews and testimonials to gauge satisfaction and reliability. |
Experience | Opt for manufacturers with extensive experience and expertise in producing carbide strips. |
Innovation | Look for manufacturers that invest in R&D and offer innovative solutions. |
Advantages and Limitations of Finish Grind Carbide Strips
Finish grind carbide strips offer numerous advantages but also come with certain limitations. Here’s a comparison:
Aspect | Advantages | Limitations |
---|---|---|
Hardness | Extremely hard, providing superior wear resistance and longevity. | High hardness can make them brittle and prone to cracking under high impact. |
Toughness | Good toughness, especially with cobalt or nickel binders. | May not match the toughness of some other materials like steel. |
Wear Resistance | Excellent wear resistance, suitable for abrasive environments. | Requires proper maintenance to retain wear resistance over time. |
Corrosion Resistance | High resistance to corrosion, especially with nickel or chromium carbide compositions. | Can be susceptible to specific corrosive environments if not properly selected. |
Thermal Stability | Maintains properties at high temperatures, ideal for high-heat applications. | Thermal conductivity can be lower compared to metals, affecting heat dissipation. |
Customization | Can be tailored to specific applications with varied compositions and shapes. | Customization can increase cost and lead times. |
Cost | Long-term cost-effective due to durability and low replacement frequency. | Higher initial cost compared to some other materials. |
Precision | Offers high precision in cutting and machining applications. | Precision can be affected if not manufactured to tight tolerances. |
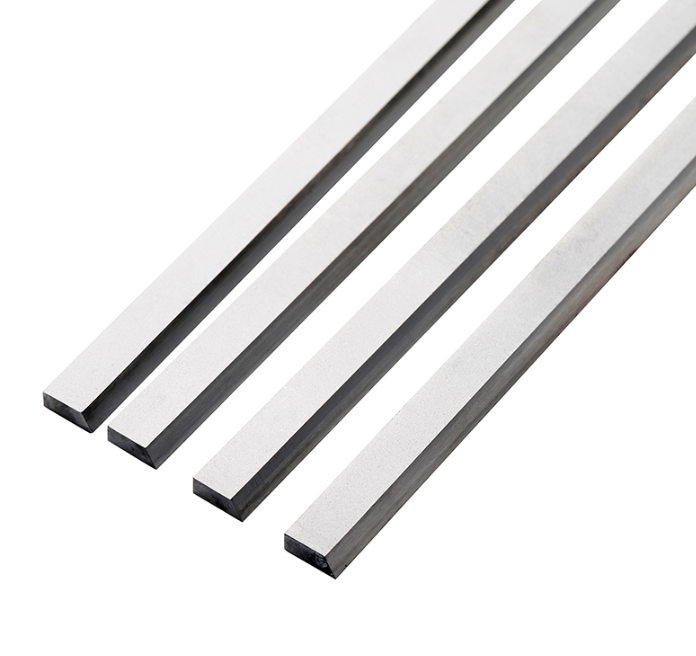
FAQs
Here are some frequently asked questions about finish grind carbide strips:
Question | Answer |
---|---|
What are finish grind carbide strips? | These are strips made of tungsten carbide, used for cutting, machining, and abrasive applications. |
Why are they called “finish grind”? | The term “finish grind” refers to the final grinding process that ensures precise dimensions and a smooth surface. |
What industries use these strips? | Automotive, aerospace, manufacturing, woodworking, mining, and medical, among others. |
How do I choose the right strip? | Consider factors like hardness, toughness, wear resistance, and the specific application needs. |
Can they be customized? | Yes, many manufacturers offer customization options to meet specific requirements. |
What are the benefits of using carbide strips? | They offer superior hardness, wear resistance, and longevity compared to other materials. |
Are they expensive? | While the initial cost may be higher, their durability makes them cost-effective in the long run. |
How are they manufactured? | Typically, they are produced by powder metallurgy techniques, followed by grinding and finishing processes. |
What maintenance do they require? | Regular inspection and proper usage can prolong their lifespan, but minimal maintenance is typically required. |
Where can I buy them? | Numerous suppliers worldwide, including Kennametal, Sandvik, and Ceratizit, among others. |
Conclusion
Finish grind carbide strips are indispensable in many industrial applications due to their unparalleled hardness, wear resistance, and durability. Whether you’re in the automotive, aerospace, or manufacturing industry, understanding the various types, properties, and applications of these strips is crucial for making informed decisions. By considering factors such as product quality, customization options, and supplier reputation, you can select the right manufacturer to meet your specific needs.
This comprehensive guide aims to provide you with all the information you need to navigate the world of finish grind carbide strips. From their types and applications to material properties and supplier details, we’ve covered everything to help you make the best choice for your industrial requirements.