Carbide strips are essential in various industries due to their durability and wear resistance. When it comes to purchasing these strips wholesale, it’s crucial to understand the different types, applications, and properties. This comprehensive guide will walk you through the complexities of finish grind carbide strips, providing all the necessary details to make informed decisions. From metal powder models to their properties and applications, we’ve got you covered.
Overview of Finish Grind Carbide Strips
Finish grind carbide strips are widely used in the manufacturing and engineering sectors for their exceptional hardness and resistance to wear. They are made from a mixture of tungsten carbide powder and cobalt, which are pressed and sintered to form a dense, robust material. These strips are commonly utilized in cutting tools, wear parts, and various machinery components.
Key Features:
- High Hardness: Superior to many other materials.
- Wear Resistance: Ideal for high-abrasion environments.
- Strength: Robust and durable under heavy loads.
- Customization: Available in various sizes and shapes for different applications.
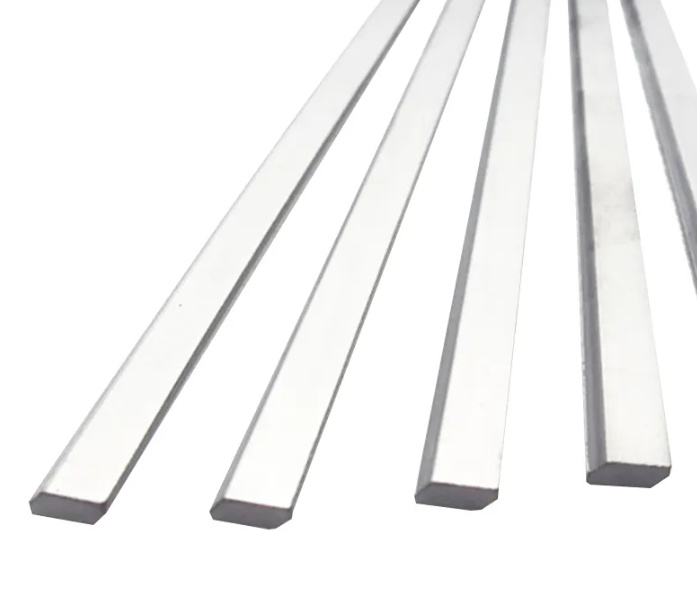
Types of Finish Grind Carbide Strips
To help you choose the right finish grind carbide strips for your needs, here is a detailed list of specific metal powder models, including their descriptions and properties.
Model | Description |
---|---|
YG6X | Excellent hardness and wear resistance, suitable for cutting tools and wear parts. |
YG8 | High strength and moderate wear resistance, commonly used in mining and drilling tools. |
YS2T | High toughness and wear resistance, ideal for precision cutting tools. |
YC20 | Medium hardness with good impact resistance, perfect for mechanical parts. |
YB50 | Excellent for high-speed cutting applications, offering both toughness and wear resistance. |
YN20 | Suitable for high-impact applications due to its high toughness. |
YW1 | Versatile with a good balance of hardness and toughness, used in various cutting and machining tools. |
K10 | Fine-grain carbide with superior wear resistance, used in metal cutting applications. |
K20 | Versatile, with a balance of toughness and hardness, used in woodworking and metalworking. |
K30 | High wear resistance, ideal for heavy-duty cutting and machining applications. |
Applications of Finish Grind Carbide Strips
Carbide strips are used across a range of industries. Their applications vary based on their properties and the specific requirements of the task.
Application | Description |
---|---|
Cutting Tools | Used in manufacturing cutting tools for metal, wood, and plastic due to their high hardness and wear resistance. |
Wear Parts | Utilized in machinery components that experience high abrasion and wear. |
Mining and Drilling | Essential in tools and components for mining and drilling operations, providing durability and toughness. |
Mechanical Parts | Employed in various mechanical parts where impact resistance is crucial. |
High-Speed Cutting | Perfect for high-speed cutting applications due to their toughness and wear resistance. |
Precision Machining | Used in precision machining tools for their accuracy and wear resistance. |
Material Properties of Finish Grind Carbide Strips
Understanding the material properties of carbide strips is crucial for selecting the right type for your application.
Property | Description |
---|---|
Hardness | Measured on the Vickers scale, indicating the material’s resistance to deformation and scratching. |
Toughness | Ability to absorb energy and plastically deform without fracturing. |
Wear Resistance | Resistance to wear and abrasion, essential for long-lasting tools and components. |
Compressive Strength | The capacity of the material to withstand loads tending to reduce size. |
Thermal Conductivity | How well the material conducts heat, important for high-speed and high-temperature applications. |
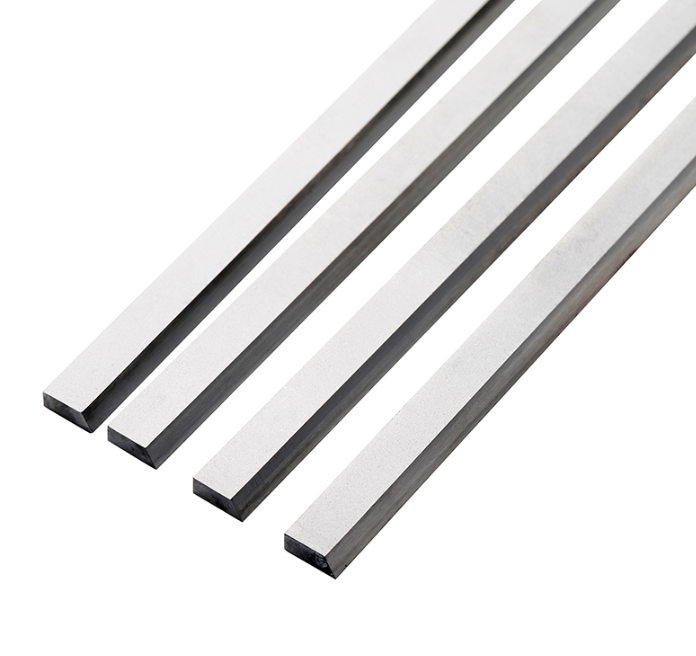
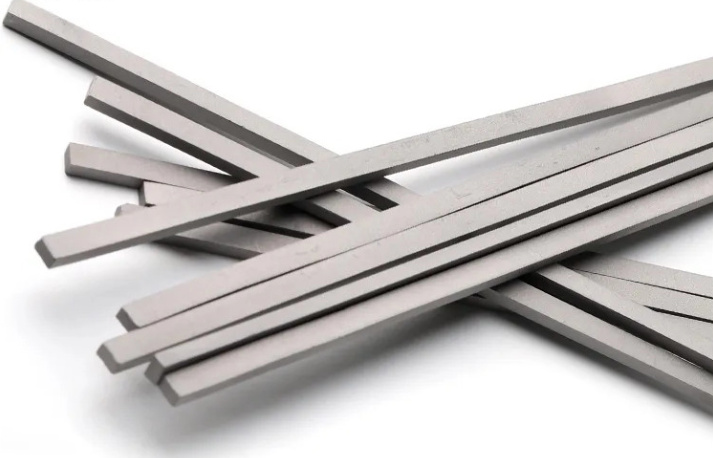
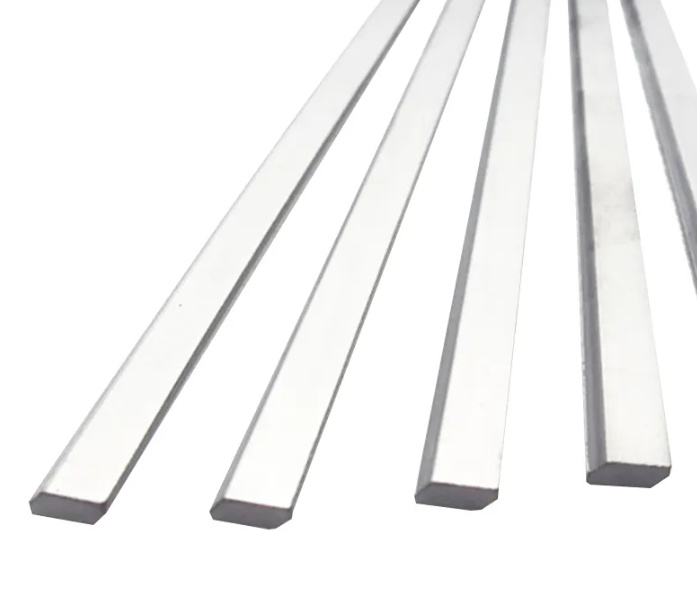
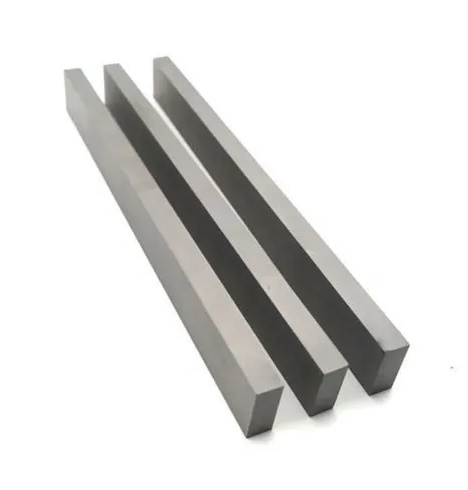
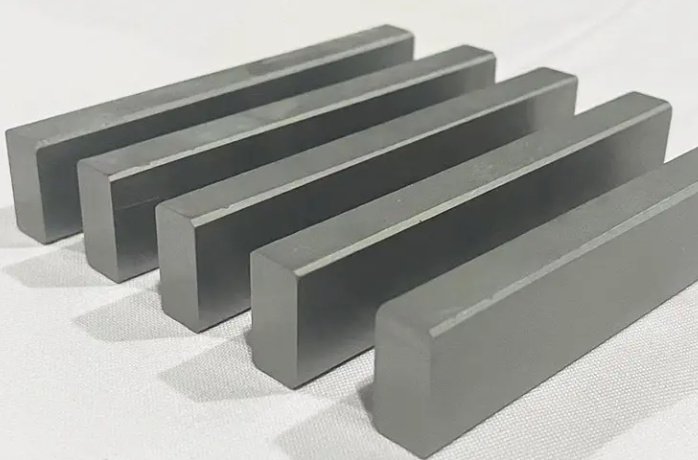
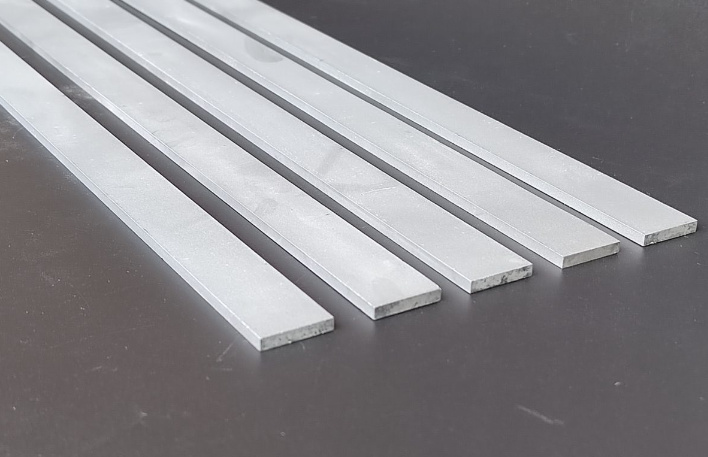
Composition and Characteristics
Different carbide strips have varying compositions, influencing their properties and applications.
Model | Composition | Characteristics |
---|---|---|
YG6X | 94% WC, 6% Co | High hardness, excellent wear resistance. |
YG8 | 92% WC, 8% Co | High strength, moderate wear resistance. |
YS2T | 90% WC, 10% Co | High toughness, excellent wear resistance. |
YC20 | 80% WC, 20% Co | Good impact resistance, moderate hardness. |
YB50 | 95% WC, 5% Co | Superior for high-speed cutting, good wear resistance. |
YN20 | 85% WC, 15% Co | High toughness, suitable for high-impact applications. |
YW1 | 91% WC, 9% Co | Balanced hardness and toughness, versatile usage. |
K10 | 96% WC, 4% Co | Fine-grain structure, superior wear resistance. |
K20 | 94% WC, 6% Co | Good balance of toughness and hardness, versatile applications. |
K30 | 92% WC, 8% Co | High wear resistance, suitable for heavy-duty applications. |
Hardness, Strength, and Wear Resistance
These properties are critical for the performance of carbide strips in various applications.
Model | Hardness (HV) | Compressive Strength (MPa) | Wear Resistance |
---|---|---|---|
YG6X | 1500 | 4000 | Excellent |
YG8 | 1400 | 3500 | High |
YS2T | 1600 | 3800 | Excellent |
YC20 | 1200 | 3000 | Good |
YB50 | 1450 | 3600 | Excellent |
YN20 | 1300 | 3200 | High |
YW1 | 1550 | 3700 | Excellent |
K10 | 1700 | 3900 | Superior |
K20 | 1500 | 3500 | High |
K30 | 1400 | 3400 | Excellent |
Specifications, Sizes, Shapes, and Standards
Carbide strips come in various specifications to meet different industrial requirements.
Specification | Size (mm) | Shape | Standard |
---|---|---|---|
Standard | 300 x 50 x 10 | Rectangular | ISO 9001 |
Custom | Varies by order | Rectangular/Round | ISO 9001 |
Precision | 150 x 25 x 5 | Rectangular | ASTM B777 |
High-Tolerance | 100 x 10 x 3 | Rectangular | DIN 50049 |
Suppliers and Pricing Details
Finding reliable suppliers and understanding pricing is crucial for making cost-effective purchases.
Supplier | Location | Price Range (per kg) | Delivery Time |
---|---|---|---|
Supplier A | USA | $50 – $70 | 2-3 weeks |
Supplier B | China | $40 – $60 | 3-4 weeks |
Supplier C | Germany | $55 – $75 | 1-2 weeks |
Supplier D | India | $45 – $65 | 3-5 weeks |
Selecting the Right Finish Grind Carbide Strips
Choosing the right carbide strips involves considering various factors such as application, material properties, and cost.
Consideration | Description |
---|---|
Application | Determine the specific use to ensure the strip meets the required hardness and wear resistance. |
Material Properties | Evaluate the hardness, toughness, and wear resistance needed for your application. |
Cost | Balance between quality and budget to find the most cost-effective option. |
Supplier Reliability | Choose a supplier with a good reputation and reliable delivery times. |
Advantages and Limitations
When comparing different carbide strips, it’s essential to understand their advantages and limitations.
Model | Advantages | Limitations |
---|---|---|
YG6X | Excellent wear resistance, high hardness. | May be more expensive due to high performance. |
YG8 | Good balance of strength and wear resistance. | Not as hard as YG6X. |
YS2T | High toughness, excellent for precision tools. | Higher cost. |
YC20 | Good impact resistance, versatile usage. | Lower hardness. |
YB50 | Superior for high-speed applications. | Higher price point. |
YN20 | High toughness, suitable for impact applications. | Not as wear-resistant as YG6X. |
YW1 | Balanced properties for various applications. | Moderate in all properties, not specialized. |
K10 | Superior wear resistance, fine-grain structure. | Higher cost. |
K20 | Versatile with good balance of properties. | Mid-range performance. |
K30 | Excellent for heavy-duty applications. | Lower toughness. |
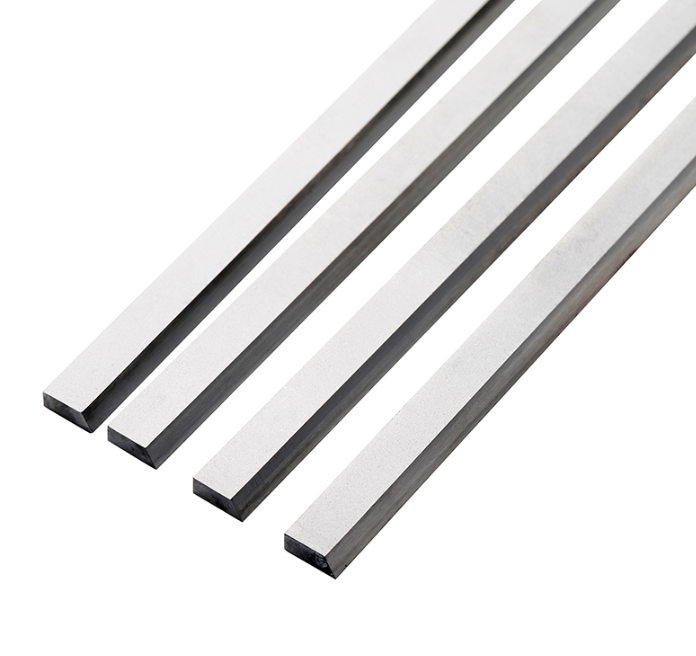
FAQ
What are finish grind carbide strips used for?
Finish grind carbide strips are primarily used in cutting tools, wear parts, mining and drilling tools, and various mechanical components due to their high hardness, wear resistance, and strength.
How do I choose the right carbide strip?
Selecting the right carbide strip depends on the application, required material properties (like hardness and wear resistance), and cost considerations. Evaluating these factors against the specifications of different models can help in making an informed decision.
Why is hardness important in carbide strips?
Hardness is crucial as it determines the strip’s resistance to deformation and scratching. Higher hardness generally means better performance in cutting and wear-resistant applications.
Can carbide strips be customized?
Yes, carbide strips can be customized in terms of size, shape, and composition to meet specific application requirements. Custom orders typically have longer delivery times but can provide better suitability for specialized tasks.
Who are the leading suppliers of carbide strips?
Leading suppliers include companies based in the USA, China, Germany, and India. It’s essential to choose a supplier with a good reputation, reliable delivery times, and competitive pricing.
What factors affect the cost of carbide strips?
The cost of carbide strips is influenced by factors such as material composition, manufacturing process, supplier, and the required specifications. High-performance strips with superior properties generally cost more.
Are there any limitations to using carbide strips?
While carbide strips offer excellent hardness and wear resistance, they can be more expensive than other materials and may have lower toughness in certain applications. It’s important to balance these factors based on the specific needs of the task.
What are the common standards for carbide strips?
Common standards for carbide strips include ISO 9001 for quality management, ASTM B777 for precision, and DIN 50049 for high-tolerance specifications.
How can I ensure the quality of carbide strips?
Ensuring the quality of carbide strips involves selecting reputable suppliers, verifying material properties through testing, and ensuring compliance with industry standards.
Can carbide strips be used in high-temperature applications?
Yes, carbide strips can be used in high-temperature applications due to their high thermal conductivity and resistance to heat. However, it’s essential to choose the right composition and model suited for high-temperature performance.
Conclusion
Choosing the right finish grind carbide strips wholesale involves understanding the specific properties and applications of various models. By considering factors such as hardness, toughness, wear resistance, and cost, you can select the most suitable carbide strips for your needs. With this comprehensive guide, you are now equipped with the knowledge to make informed decisions and ensure high performance in your industrial applications.