Introduction
What is tungsten carbide rod?
Tungsten carbide rod is a type of material that is widely used in various industries due to its exceptional hardness and strength. It is composed of tungsten and carbon atoms, which are combined through a process called sintering. This results in a dense and durable rod that is resistant to wear, corrosion, and high temperatures. Tungsten carbide rod is commonly used in cutting tools, such as drills, end mills, and reamers, as it can easily cut through tough materials like steel, stainless steel, and cast iron. Its superior performance and longevity make it a preferred choice for applications that require precision and reliability.
Applications of tungsten carbide rod
Tungsten carbide rod finds a wide range of applications due to its exceptional hardness and strength. One of the primary uses of tungsten carbide rod is in the cutting industry. It is extensively used for cutting and shaping hard materials such as metals, wood, plastics, and ceramics. The superior hardness of tungsten carbide rod allows it to withstand high temperatures and maintain its sharpness for a longer period, making it ideal for precision cutting and machining operations. Additionally, tungsten carbide rod is also used in the manufacturing of drill bits, milling cutters, and other cutting tools, where its high wear resistance and toughness are highly valued. Overall, the applications of tungsten carbide rod are essential in various industries that require durable and efficient cutting solutions.
Importance of cutting tungsten carbide rod
Cutting tungsten carbide rod is a crucial process in various industries, and its importance cannot be overstated. Tungsten carbide is an incredibly hard and durable material, making it ideal for applications that require high wear resistance and strength. However, due to its hardness, cutting tungsten carbide rod can be challenging and requires specialized tools and techniques. The precision and accuracy of the cutting process are crucial to ensure the desired shape and dimensions of the rod. Additionally, proper cutting techniques are essential to prevent damage to the cutting tools and to maintain the integrity of the tungsten carbide rod. Therefore, understanding the importance of cutting tungsten carbide rod and employing the right methods is vital for achieving optimal results in various industrial applications.
Properties of Tungsten Carbide Rod
Hardness and wear resistance
Tungsten carbide is well-known for its exceptional hardness and wear resistance. It is one of the hardest materials known to man, second only to diamonds. This unique property makes tungsten carbide rods an ideal choice for applications that require high levels of durability and resistance to wear and tear. Whether it is for cutting tools, drilling equipment, or wear parts, tungsten carbide rods are widely used in various industries. The hardness and wear resistance of tungsten carbide rods ensure that they can withstand the most demanding conditions and provide long-lasting performance.
High melting point
Tungsten carbide is well-known for its exceptional properties, and one of its most notable characteristics is its high melting point. With a melting point of approximately 2,870 degrees Celsius, tungsten carbide is one of the highest melting point materials known to man. This remarkable feature makes it an ideal choice for applications that require extreme heat resistance, such as cutting tools. The ability of tungsten carbide to withstand high temperatures without compromising its structural integrity allows it to maintain its sharpness and durability even under the most demanding conditions. As a result, cutting tungsten carbide rod becomes a precise and efficient process, ensuring clean and accurate cuts in various industries including manufacturing, construction, and aerospace.
Chemical stability
Chemical stability is an important characteristic of tungsten carbide rod. Tungsten carbide is highly resistant to chemical reactions, making it ideal for use in various industrial applications. It is known to withstand exposure to acids, alkalis, and other corrosive substances, ensuring its durability and longevity. This exceptional chemical stability allows tungsten carbide rod to maintain its structural integrity and performance even in harsh environments. Whether it is used in cutting tools, wear-resistant parts, or drilling equipment, the chemical stability of tungsten carbide rod ensures reliable and consistent performance.
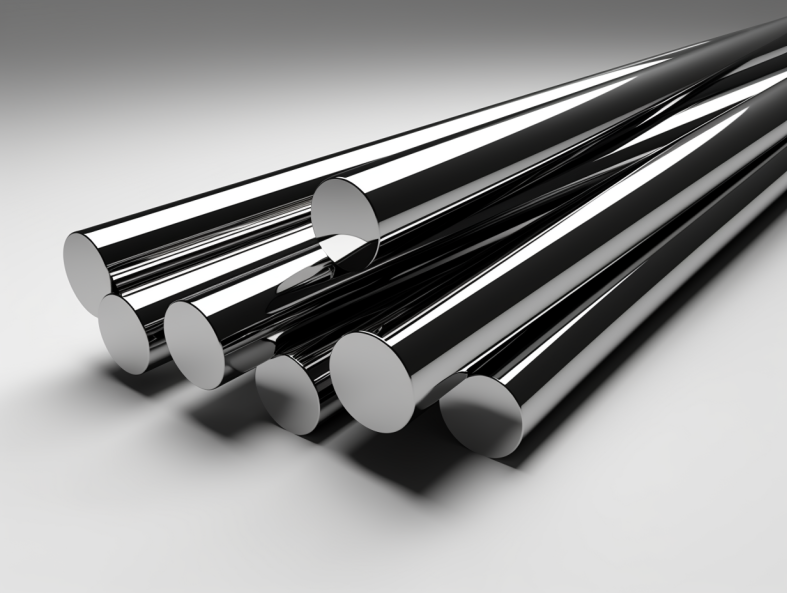
Cutting Techniques
Diamond cutting
Diamond cutting is a widely used method for cutting tungsten carbide rods. This technique utilizes the hardness and durability of diamonds to effectively cut through the tough material. The process involves using diamond-tipped tools or blades to create precise cuts and shapes in the tungsten carbide rod. Diamond cutting offers several advantages, including high precision, minimal material loss, and a smooth finish. It is commonly employed in various industries such as manufacturing, construction, and jewelry making. With its ability to handle the hardness of tungsten carbide, diamond cutting has become an essential technique in working with this challenging material.
Grinding
Grinding tungsten carbide rods is an essential process in the manufacturing industry. It involves using abrasive materials to remove excess material and shape the rods to the desired dimensions. The grinding process requires precision and expertise to ensure the rods are ground evenly and smoothly. Various grinding techniques, such as centerless grinding and surface grinding, can be employed to achieve the desired results. Additionally, proper coolant and lubrication are essential to prevent overheating and maintain the integrity of the tungsten carbide rods. Overall, grinding plays a crucial role in producing high-quality tungsten carbide rods that meet the stringent requirements of various industries.
Laser cutting
Laser cutting is a highly precise and efficient method used in various industries, including the cutting of tungsten carbide rods. This advanced technology utilizes a focused laser beam to melt, vaporize, or burn through the material, resulting in clean and accurate cuts. The intense heat generated by the laser allows for the precise control of the cutting process, ensuring minimal material wastage and excellent edge quality. Additionally, laser cutting offers the advantage of non-contact processing, eliminating the need for physical force and reducing the risk of damage to the tungsten carbide rod. With its ability to cut complex shapes and intricate designs, laser cutting has become an indispensable tool in the machining of tungsten carbide rods, providing manufacturers with a cost-effective and efficient solution for their cutting needs.
Tools and Equipment
Diamond cutting tools
Diamond cutting tools are widely used in various industries, including the cutting of tungsten carbide rods. These tools are known for their exceptional hardness and durability, making them perfect for the task. The diamond particles embedded in the cutting edge of these tools allow for precise and efficient cutting of tungsten carbide rods. With their superior cutting performance, diamond cutting tools ensure clean and accurate cuts, resulting in high-quality finished products. Whether it’s for industrial or personal use, diamond cutting tools are the go-to choice when it comes to cutting tungsten carbide rods.
Grinding machines
Grinding machines play a crucial role in the process of cutting tungsten carbide rod. These machines are specifically designed to perform the task of grinding and shaping the rod to achieve the desired dimensions and surface finish. With their robust construction and precise control systems, grinding machines ensure the accurate removal of material from the tungsten carbide rod, resulting in a smooth and uniform surface. Additionally, these machines offer flexibility in terms of adjusting the grinding parameters to meet different requirements, making them indispensable in the manufacturing industry for cutting tungsten carbide rod.
Laser cutting machines
Laser cutting machines have revolutionized the process of cutting tungsten carbide rods. These advanced machines utilize high-powered lasers to precisely and efficiently cut through the extremely hard and durable tungsten carbide material. The laser cutting technology allows for clean and accurate cuts, ensuring minimal material wastage and superior quality results. With the ability to achieve intricate designs and complex shapes, laser cutting machines have become indispensable in the tungsten carbide rod cutting industry. The precision and speed offered by these machines have greatly enhanced productivity and reduced production time, making them a preferred choice for manufacturers and craftsmen alike.
Safety Precautions
Wear protective gear
When cutting tungsten carbide rod, it is crucial to wear protective gear. This includes safety goggles, gloves, and a face shield to protect against flying debris and potential injury. Tungsten carbide is a hard and brittle material that can produce sharp fragments when cut, posing a risk to the eyes, hands, and face. By wearing the appropriate protective gear, you can minimize the risk of accidents and ensure your safety while working with tungsten carbide rod.
Proper ventilation
Proper ventilation is crucial when cutting tungsten carbide rod. Tungsten carbide is a hard and dense material that releases harmful dust and particles when cut. Without proper ventilation, these particles can accumulate in the air and pose a health risk to the operator. It is important to have a well-ventilated workspace with adequate air circulation and filtration systems in place. This will help to minimize the inhalation of hazardous particles and ensure a safe working environment. Additionally, wearing appropriate personal protective equipment, such as a respirator, is recommended when working with tungsten carbide rod to further protect against airborne contaminants.
Avoid direct contact with skin
When cutting tungsten carbide rod, it is crucial to avoid direct contact with the skin. Tungsten carbide is a hard and abrasive material that can cause skin irritation and injury. To protect yourself, always wear appropriate personal protective equipment, such as gloves and safety glasses. Additionally, ensure that the cutting process is carried out in a well-ventilated area to minimize the risk of inhaling any dust or particles. By taking these precautions, you can safely handle and cut tungsten carbide rod without putting your skin at risk.
Conclusion
Summary of cutting techniques
Cutting tungsten carbide rod requires specialized techniques due to its hardness and durability. The summary of cutting techniques for tungsten carbide rod includes various methods such as diamond cutting, laser cutting, and abrasive cutting. Diamond cutting involves the use of diamond-coated tools to slice through the rod with precision. Laser cutting utilizes a high-powered laser beam to melt and vaporize the material, creating a clean and precise cut. Abrasive cutting involves the use of abrasive materials, such as diamond or tungsten carbide, to grind away the rod. Each cutting technique has its advantages and limitations, and the choice of method depends on factors such as the desired precision, material thickness, and production volume. It is crucial to select the appropriate cutting technique to ensure efficient and accurate cutting of tungsten carbide rod.
Importance of proper tools and safety precautions
When it comes to cutting tungsten carbide rod, using the proper tools and following safety precautions is of utmost importance. Tungsten carbide is an extremely hard and brittle material, making it challenging to cut without the right tools. Using improper tools can not only lead to inefficient cutting but also pose serious safety risks. It is essential to use tools specifically designed for cutting tungsten carbide, such as diamond tools or carbide-tipped blades. Additionally, wearing appropriate personal protective equipment, such as safety glasses, gloves, and a dust mask, is crucial to protect against potential hazards. By using the right tools and taking necessary safety precautions, the cutting process can be performed effectively and safely.
Future developments in cutting tungsten carbide rod
In recent years, there have been significant advancements in the cutting of tungsten carbide rod, and the future holds even more promising developments. One of the key areas of focus is improving the efficiency and precision of the cutting process. Researchers are exploring new cutting techniques, such as laser cutting and electrical discharge machining, which have shown great potential in achieving higher cutting speeds and reducing tool wear. Additionally, advancements in tool materials and coatings are being made to enhance the durability and performance of cutting tools when working with tungsten carbide rod. These developments aim to increase productivity and reduce costs in industries that heavily rely on tungsten carbide rod cutting, such as manufacturing, aerospace, and automotive. With ongoing research and innovation, the future of cutting tungsten carbide rod looks bright and promising.