Introduction
Definition of cutting tool carbide blanks
A cutting tool carbide blank refers to a piece of carbide material that is specifically designed for the manufacturing of cutting tools. It serves as the starting point for the production of various types of cutting tools, such as drills, end mills, and inserts. The carbide blank is typically made from tungsten carbide, a hard and durable material that is known for its excellent wear resistance and high heat resistance. The manufacturing process involves shaping the carbide blank into the desired tool geometry and then applying coatings or treatments to enhance its performance. Cutting tool carbide blanks play a crucial role in the machining industry, as they provide the foundation for creating efficient and long-lasting cutting tools that are essential for various applications in metalworking, woodworking, and other industries.
Importance of cutting tool carbide blanks
Cutting tool carbide blanks play a crucial role in various industries, especially in the manufacturing and machining sector. These blanks serve as the foundation for creating high-quality cutting tools that are essential for precision cutting, drilling, and shaping processes. The importance of cutting tool carbide blanks lies in their exceptional hardness, durability, and resistance to wear and heat. This enables them to withstand the demanding conditions of heavy-duty cutting operations, ensuring consistent performance and extended tool life. Additionally, the use of carbide blanks allows for the production of cutting tools with sharp edges and precise cutting angles, resulting in enhanced cutting efficiency and accuracy. Therefore, understanding the significance of cutting tool carbide blanks is essential for businesses and professionals involved in the field of machining and manufacturing.
Overview of the article
The article titled ‘Cutting Tool Carbide Blanks’ provides a comprehensive overview of the various aspects related to carbide blanks used in cutting tools. It delves into the characteristics, manufacturing process, and applications of carbide blanks, highlighting their importance in the machining industry. The article also discusses the advantages of using carbide blanks, such as their high hardness, wear resistance, and ability to withstand high temperatures. Furthermore, it explores the different types of carbide blanks available in the market and their specific uses in various cutting tool applications. Overall, this article serves as a valuable resource for anyone seeking to understand the role and significance of carbide blanks in the cutting tool industry.
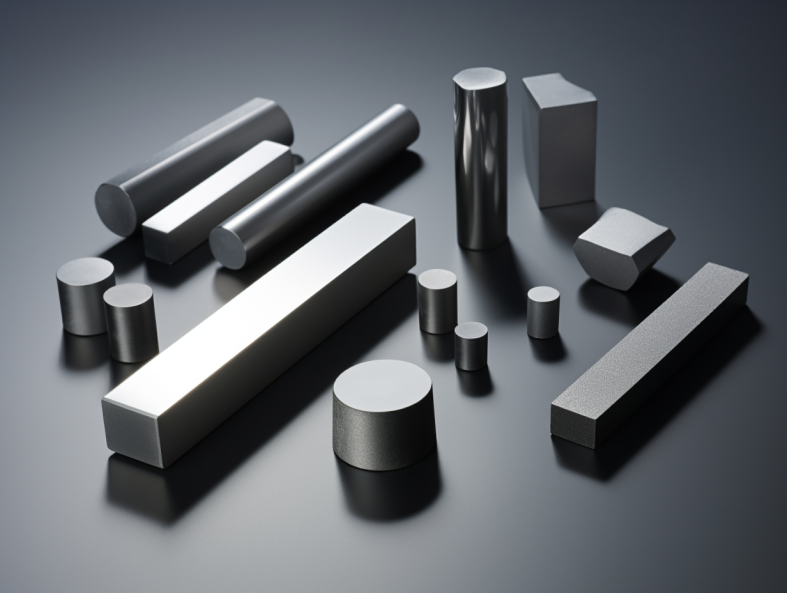
Properties of Cutting Tool Carbide Blanks
Hardness and wear resistance
Hardness and wear resistance are crucial factors to consider when selecting cutting tool carbide blanks. The hardness of the carbide material determines its ability to withstand high temperatures and resist deformation during cutting operations. Additionally, a high level of wear resistance ensures that the cutting tool maintains its sharpness and cutting efficiency over an extended period. By choosing carbide blanks with optimal hardness and wear resistance properties, manufacturers can enhance the performance and longevity of their cutting tools, resulting in improved productivity and cost-effectiveness.
Heat resistance
Carbide blanks used in cutting tools are known for their exceptional heat resistance. This characteristic makes them highly suitable for applications that involve high-speed machining and heavy-duty cutting. The heat resistance of carbide blanks allows them to maintain their hardness and strength even at elevated temperatures, reducing the risk of tool wear and improving overall tool life. Additionally, the heat resistance of carbide blanks enables them to withstand the thermal stresses and extreme temperatures generated during the cutting process, ensuring consistent performance and precision. Overall, the heat resistance of carbide blanks is a crucial factor in their effectiveness and longevity as cutting tool materials.
Chemical stability
Chemical stability is an important factor to consider when it comes to cutting tool carbide blanks. These blanks are often exposed to various chemicals during the manufacturing process and while in use. It is crucial for the carbide blanks to maintain their stability and integrity in the presence of these chemicals to ensure optimal performance and longevity. The chemical stability of the carbide blanks is determined by the composition and quality of the carbide material used. Manufacturers carefully select carbide materials that have high chemical resistance to ensure that the cutting tool carbide blanks can withstand the corrosive effects of chemicals and maintain their sharpness and durability over time.
Types of Cutting Tool Carbide Blanks
Solid carbide blanks
Solid carbide blanks are an essential component in the manufacturing of cutting tools. These blanks are made from high-quality carbide materials, which provide exceptional hardness and wear resistance. The use of solid carbide blanks ensures the production of durable and long-lasting cutting tools that can withstand the demands of various machining operations. Additionally, solid carbide blanks offer excellent heat resistance, allowing cutting tools to maintain their performance even at high temperatures. With their superior strength and durability, solid carbide blanks are the preferred choice for professionals in the metalworking industry.
Brazed carbide blanks
Brazed carbide blanks are an essential component in the manufacturing of cutting tools. These blanks are made by joining a carbide insert to a steel body through a brazing process. The carbide insert, known for its exceptional hardness and wear resistance, provides the cutting edge, while the steel body provides the necessary strength and support. The brazing process ensures a strong and durable bond between the carbide insert and the steel body, allowing for efficient and precise cutting. With their high performance and reliability, brazed carbide blanks are widely used in various industries, including automotive, aerospace, and machining.
Indexable carbide blanks
Indexable carbide blanks are an essential component in cutting tool manufacturing. These blanks are made from high-quality carbide materials, which offer excellent hardness and wear resistance. They are designed to be easily mounted onto cutting tools, providing a reliable and efficient cutting edge. Indexable carbide blanks are widely used in various industries, such as automotive, aerospace, and machining. With their superior performance and durability, these blanks play a crucial role in enhancing productivity and achieving precision in cutting operations.
Manufacturing Process of Cutting Tool Carbide Blanks
Powder metallurgy
Powder metallurgy is a manufacturing process used to produce cutting tool carbide blanks. It involves the blending and mixing of fine metal powders, such as tungsten carbide, with binders and additives. The mixture is then compacted into a desired shape and subjected to high temperatures to sinter the powders together. This process results in a dense and durable material with excellent hardness and wear resistance, making it ideal for cutting tools. Powder metallurgy offers precise control over the composition and properties of the carbide blanks, ensuring consistent and high-quality products.
Compaction and sintering
Compaction and sintering are crucial steps in the production of cutting tool carbide blanks. During compaction, the powdered carbide material is compressed into a desired shape using high pressure. This process helps to ensure the density and uniformity of the carbide blank. After compaction, the blanks undergo sintering, where they are heated to a high temperature in a controlled atmosphere. Sintering allows the carbide particles to bond together, creating a strong and durable material. The combination of compaction and sintering results in the production of high-quality carbide blanks that are ready for further processing and finishing.
Finishing operations
Finishing operations are crucial in the manufacturing process of cutting tool carbide blanks. These operations involve the final steps that enhance the quality, precision, and durability of the blanks. One of the common finishing operations is grinding, which helps to achieve the desired shape and dimensions of the blanks. Additionally, polishing is performed to smoothen the surface of the blanks, reducing friction and improving their overall performance. Other finishing operations may include coating application to enhance wear resistance and edge retention. Overall, these finishing operations play a vital role in ensuring that the cutting tool carbide blanks meet the required standards and specifications for optimal performance in various machining applications.
Applications of Cutting Tool Carbide Blanks
Metal cutting
Metal cutting is a fundamental process in manufacturing industries. It involves the removal of material from a workpiece to create the desired shape or size. One of the key elements in metal cutting is the cutting tool. Carbide blanks are widely used as cutting tools due to their high hardness and wear resistance. These blanks are made from a combination of tungsten carbide and cobalt, which gives them the necessary strength and durability. They are commonly used in machining applications for cutting and shaping various types of metals, including steel, aluminum, and cast iron. The use of carbide blanks in metal cutting processes ensures precision, efficiency, and longevity, making them an essential tool for industries involved in metal fabrication and machining.
Woodworking
Woodworking is a versatile and rewarding craft that allows individuals to create functional and decorative items from wood. One essential aspect of woodworking is using the right cutting tools, such as carbide blanks. These specially designed tools are made from high-quality carbide material, which provides exceptional durability and cutting performance. Carbide blanks are known for their ability to maintain a sharp edge for longer periods, allowing woodworkers to achieve precise and clean cuts. Whether you’re a beginner or an experienced woodworker, incorporating carbide blanks into your arsenal of tools can greatly enhance the quality and efficiency of your woodworking projects.
Plastic machining
Plastic machining is a crucial process in various industries, as it allows for the creation of precise and intricate components. When it comes to cutting tool carbide blanks, plastic machining plays a significant role in shaping and forming these essential tools. The process involves using advanced machinery and techniques to accurately cut, shape, and finish carbide blanks, ensuring their optimal performance and longevity. With the advancements in technology, plastic machining has become more efficient and precise, allowing for the production of high-quality cutting tool carbide blanks that meet the demands of diverse industries.
Advantages and Limitations of Cutting Tool Carbide Blanks
Advantages
Carbide blanks for cutting tools offer numerous advantages. Firstly, they have exceptional hardness, which allows them to withstand high temperatures and maintain their cutting edge for longer periods. This makes them ideal for applications that involve heavy machining and extended use. Additionally, carbide blanks have excellent wear resistance, meaning they can withstand the abrasive forces encountered during cutting operations. This results in longer tool life and reduced downtime for tool replacements. Furthermore, carbide blanks have superior strength and toughness, making them less prone to chipping or breaking. This ensures consistent performance and reliable cutting results. Overall, the use of carbide blanks in cutting tools provides significant advantages in terms of durability, efficiency, and cost-effectiveness.
Limitations
Carbide blanks for cutting tools have numerous advantages, such as high hardness, excellent wear resistance, and good thermal stability. However, they also have certain limitations that need to be considered. One limitation is their brittleness, which makes them prone to chipping or breaking under heavy loads or impacts. Another limitation is their high cost compared to other tool materials. Additionally, carbide blanks can be challenging to machine due to their hardness, requiring specialized equipment and expertise. Despite these limitations, carbide blanks remain a popular choice for many cutting tool applications due to their overall performance and durability.
Future developments
In the future, there are several potential developments that could revolutionize the field of cutting tool carbide blanks. One exciting possibility is the use of nanotechnology to enhance the performance and durability of these blanks. By manipulating materials at the atomic and molecular level, researchers may be able to create carbide blanks with unprecedented strength and wear resistance. Another area of potential advancement is the integration of artificial intelligence into the manufacturing process. AI algorithms could analyze data from various sources to optimize the design and production of carbide blanks, resulting in improved efficiency and precision. Additionally, advancements in additive manufacturing techniques may allow for the creation of complex and customized carbide blank geometries that were previously impossible to achieve. These developments have the potential to greatly enhance the performance and versatility of cutting tool carbide blanks in various industries.