Carbide blanks are an essential material for manufacturing cutting tools and dies. This article provides a comprehensive overview of cutting carbide blanks, covering equipment, types, applications, specifications, suppliers, installation, operation, maintenance, and more.
Overview of Cutting Carbide Blanks
Carbide blanks are blocks or rods made of tungsten carbide that are shaped into cutting tools and dies. Tungsten carbide is an extremely hard metal alloy containing tungsten and carbon. It is known for its high hardness, wear resistance, strength, and toughness.
Carbide blanks allow manufacturers to customize cutting tools and dies to their required shape, size, and features. The blanks are cut and ground to specifications using specialized equipment. The geometry, tolerances, and surface finish requirements depend on the final application.
Key details about carbide blanks:
- Made of tungsten carbide-cobalt alloy
- Very hard, rigid, and wear resistant
- Used as blanks for cutting tools and dies
- Shaped by cutting, grinding, and finishing operations
- Customized to required tool specifications
- Enables optimal tool design for application
- Available in rods, blocks, and various standard sizes
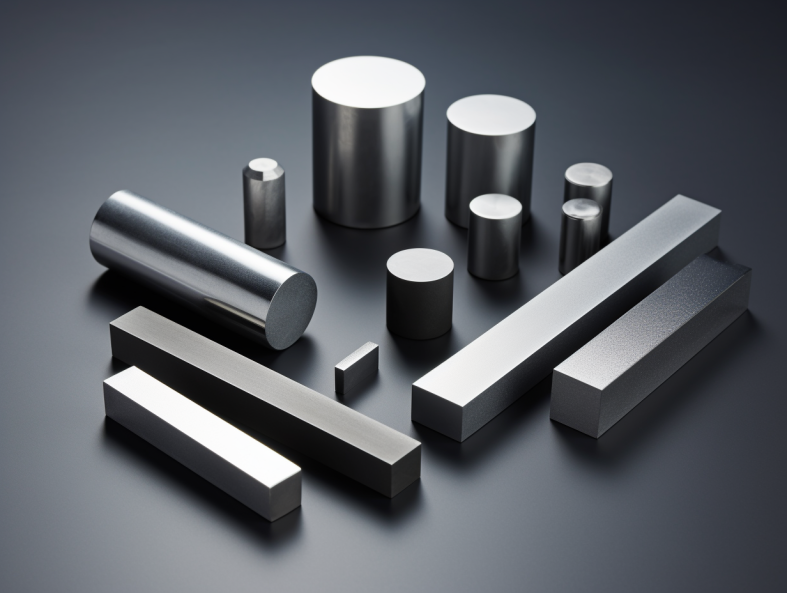
Types of Carbide Blanks
There are several types of carbide blanks available depending on composition, quality, and final application:
By Carbide Grade
Carbide Grade | Description |
---|---|
C1/C2 | Basic carbide grade with 6-8% cobalt content |
C3/C4 | Improved wear resistance with 6-8% cobalt |
C5/C6 | High performance grade with 8-10% cobalt |
C7/C8 | Superior wear resistance with 10-12% cobalt |
By Quality
Quality | Description |
---|---|
Standard | Normal quality blanks for general applications |
Premium | High quality blanks for critical tools |
Recrystallized | Stress-relieved and improved blank quality |
By Application
Application | Blank Type |
---|---|
Cutting Tools | Solid carbide rods |
Drawing Dies | Precision ground carbide blocks |
Forming Dies | EDMed graphite electrodes |
Injection Molds | Carbide inserts, custom shapes |
By Shape and Size
- Rod blanks: Round, square, rectangular, hexagonal etc.
- Block blanks: Rectangular blocks and specialty shapes
- Custom blanks: Any required shape or size
Carbide rods are stocked in standard diameters like 3mm, 5mm, 8mm etc. Blocks come in sizes like 20x20mm, 25x30mm based on application. Custom carbide blanks can be produced to order in precise dimensions.
Applications of Carbide Blanks
Carbide blanks are turned into finished cutting tools and dies across several industries:
Cutting Tools
- End mills
- Drills
- Reamers
- Burrs
- Knives
- Saws
- Router bits
Metalworking
- Drawing dies
- Forming dies
- Extrusion dies
- Stamping dies
Automotive
- Injection molds
- Trimming tools
Aerospace
- Precision cutting tools
- Composite trimming dies
Medical
- Surgical tools
- Implant machining
Carbide blanks enable optimized design of specialized cutting tools and dies for these applications. The blanks are shaped to tight tolerances and finished to meet the requirements.
How to Choose Carbide Blanks
Selecting the right carbide blank depends on several factors:
Carbide Grade
Higher cobalt content improves wear resistance and toughness. C7-C8 is used for critical tools.
Quality
Premium quality for precision tools. Standard for general use.
Size and Shape
Match blank dimensions to finished tool size. Consider Frank use.
Tolerance
Tight tolerance blank for close-fitting parts.
Surface Finish
Finer finish on blank to reduce grinding needed.
Coatings
PVD coatings on blank improve tool performance.
Batch Testing
Sample blanks from new batch should be tested first.
Supplier Reputation
Reputable suppliers provide consistent quality blanks.
Pricing
Balance performance and budget. Avoid very cheap blanks.
Choosing the optimal grade, tolerance, coating, and quality level of blanks is important for productivity and tool life. Discuss requirements with suppliers to select the ideal blank specifications.
How to Cut and Grind Carbide Blanks
Shaping carbide blanks into finished tools involves several machining processes:
Cutting
- Band saws
- Abrasive cutting wheels
- Wire EDM
Carbide is brittle so low-stress cutting methods are used. Wire EDM allows complex 2D/3D shapes.
Grinding
- Surface grinding
- Cylindrical grinding
- Centerless grinding
- Profile grinding
Grinding achieves tight tolerances and fine surface finishes on blanks. Diamond or CBN wheels are used.
Lapping and Polishing
- Loose abrasive lapping
- Diamond paste polishing
Lapping removes minimal material while improving surface finish.
Laser Cutting
- CO2 lasers
- Fiber lasers
- Precision cutting
Laser cutting is a non-contact process suitable for small, complex carbide parts.
Automated 5-axis CNC grinding with robot loading/unloading enables high throughput carbide machining. The appropriate method depends on blank shape, tool geometry, tolerances, and material removal rate.
Equipment for Cutting Carbide Blanks
Specialised equipment is required for machining hard, brittle carbide blanks:
Sawing
Type | Description |
---|---|
Band saws | Bi-metal blades minimize damage |
Abrasive cut-off saws | Use hard bonded wheels |
Grinding
Type | Description |
---|---|
Tool & cutter grinder | For end mills, drills, reamers |
Cylindrical grinder | For outside diameters |
Centerless grinder | For round blanks |
Surface grinder | For faces, shoulders |
EDM grinders | For small hard materials |
Automation
- CNC tool grinding machines
- Automated robotic tool load/unload
- Conveyor systems for workflow
Accessories
- Precision workholding fixtures
- Diamond and CBN grinding wheels
- High pressure coolant systems -Cleaning systems and magnetic filtration
Carbide machining requires rigid, precision construction on all components. Vibration damping and thermal stability are also important.
Specifications and Standards
Carbide blanks have the following key specifications:
Mechanical Properties
- Hardness: 88-93 HRA
- Transverse Rupture Strength: 500-600 ksi
- Compressive strength: 500-700 ksi
Composition
- WC grain size: 0.5-15 microns
- Cobalt content: 6-15% by weight
- Carbon: Balance
Tolerances
- Diameter: +/- 0.001″ to 0.005”
- Flatness: 0.0002” per inch
- Squareness: < 0.001”
Surface Finish
- Ground blanks: 8-25 μin Ra
- As-sintered: Up to 250 μin Ra
Applicable Standards
- ISO 513: Classification and application of hard cutting materials
- ASTM B9455M: Standard specification for tungsten carbide tool blanks
- National tooling standards and tool material specifications
Maintaining stringent standards for composition, mechanical properties, tolerances, and surface finish ensures reliability and performance of carbide tool blanks in service.
Suppliers of Carbide Blanks
There are several major global suppliers that manufacture and source carbide blanks:
Supplier | Description |
---|---|
Kennametal | The top producer of carbide blanks and tools |
Sandvik | Leading manufacturer of cemented carbide products |
Ceratizit | High-quality tungsten carbide milling and turning inserts |
Mitsubishi Materials | Supplies a wide range of carbide blanks |
Guangdong Xianglu Tungsten | Chinese tungsten and cemented carbide supplier |
Tungaloy Corporation | Japanese manufacturer of cutting tools and carbide |
Rock River Tool | Carbide blank distributor in the United States |
Pricing
- Carbide rod blanks: $5 – $40 per inch
- Carbide block blanks: $15 – $150 per cubic inch
- Premium C7-C8 grades are 2X cost of standard C2-C4
- Custom blanks with tight tolerances cost 20-50% more
When selecting a supplier, consider carbide grade, quality control, size range, lead times, and pricing. Established manufacturers like Kennametal and Sandvik offer the highest quality and reliability.
Installation and Operation
Follow these steps when setting up carbide blank machining processes:
Preparation
- Review tool design and blank size required
- Order blanks with sufficient margin
- Clean blanks to remove oils, grease, or handling marks
Setup
- Mount blanks in proper fixtures for each operation
- Ensure stability, rigidity, and vibration isolation
- Select suitable bonded grinding wheels
- Set machine speeds, feeds, coolant flow
First-off Inspection
- Visually inspect first parts for defects
- Verify critical dimensions
- Adjust process parameters if needed
- Repeat until specifications are met
Operation
- Run process with adequate coolant
- Dress wheels regularly to expose fresh grains
- Periodically test part quality
- Follow schedules for maintenance and housekeeping
Starting with quality blanks, proven fixtures, and the right process parameters ensures smooth production of carbide cutting tools. Allow for adequate grinding wheel wear and dressing to maintain precision.
Maintenance of Carbide Machining Equipment
Effective maintenance is crucial for consistent qualityoutput and maximum uptime when grinding carbide blanks.
Key maintenance activities:
- Daily cleaning of equipment and work area
- Monitoring coolant concentration and filtration
- Dressing and truing grinding wheels
- Replacing worn wheels and disks
- Lubricating spindles, slides and bearings
- Checking for loose fixtures and worn components
- Monitoring wheel wear and part finish
- Scheduling periodic maintenance checks
- Keeping records of maintenance work
Essential maintenance tools:
- Precision gages and measuring instruments
- Hand scrapers for cleaning flat surfaces
- Diamond dressing tools
- Coolant refractometer and filtration systems
- Ultrasonic bath for cleaning fixtures
- Spare hardware kits and lubricants
- Wheel pullers and arbors
Establish a comprehensive maintenance program covering daily, weekly, and monthly actions to minimize unplanned downtime. Invest in high quality accessories and tooling to support maintenance work.
Choosing a Carbide Blank Supplier
Selecting the right supplier is crucial for obtaining high-quality carbide blanks tailored to the application. Here are the key factors to consider:
Carbide Grades
- Range of carbide grades (C2 to C8)
- Grades match cutting tool requirements
- Certs for grade composition and Grain size
Dimensional Accuracy
- Tight tolerances on diameters and squareness
- Precision ground to close specs
- Custom special shapes available
Surface Finish
- Fine ground blanks with 8-25 μin finish
- Complements tool finish requirements
- Custom polishing available
Quality Control
- Stringent process control standards
- Reliable and repeatable processes
- Proof of product testing and SPC
Technical Support
- Expertise in tool design and manufacturing
- Help select optimal blank specs
- Metallurgical lab for failure analysis
Inventory and Lead Times
- Range of standard and special sizes in stock
- Rapid fulfillment of orders
- Short lead times for custom blanks
Value
- Competitive pricing
- Balance of cost, quality, and delivery
- Focus on customer productivity
Finding the best fit between capabilities, quality, and pricing leads to a productive long-term partnership with carbide blank suppliers.
Pros and Cons of Carbide Blanks
Advantages
- Extreme hardness for tool wear resistance
- Strength to withstand cutting forces
- Customized to required tool geometry
- Enables optimal tool design and features
- Grinds to mirror surface finish
- Improves tool performance and life
- Consistent quality from reputed suppliers
Limitations
- Brittle material requiring special handling
- Dependent on operator skill for grinding
- Sensitive to vibration and instability
- Specialized equipment needed to machine
- Premium grades are expensive
- Long lead time for custom sizes
Applications Best Suited For
- Cutting tools for hard materials
- Metal dies with tight tolerances
- Precision grinding and machining
- Super-finishing of critical surfaces
- Situations requiring long tool life
Applications to Avoid
- Highly interrupted cuts
- High shock loads during machining
- Low-volume tool requirements
- Very large cutting tools
Carbide blanks enable cutting tool and die performance not attainable with other materials like HSS. The limitations can be minimized through optimal blank design and using best practices in machining.
Carbide Blanks – Frequently Asked Questions
Q: What is the composition of tungsten carbide blanks?
A: Carbide blanks consist of fine grained tungsten carbide particles bonded together using 6-15% cobalt. Small amounts of other carbides like tantalum or titanium carbide may also be added.
Q: How are carbide blanks made?
A: The powder metallurgy process involves compacting, pressing and sintering the carbide and cobalt powders into a dense material. This produces the as-sintered blank ready for grinding.
Q: What tolerances are achievable on carbide blanks?
A: Blanks can be ground to precise tolerances like ±0.0005″ on diameter. But most economical range is ±0.001″ to ±0.003″ for standard blanks.
Q: Does wire EDM work effectively on carbide?
A: Yes, wire EDM is commonly used to cut complex 2D profiles or 3D cavities into carbide blanks. Surface finish of Ra 25-125 μin is typical.
Q: How are carbide blanks sharpened or reconditioned?
A: Carbide cannot be mechanically sharpened. Used blanks are discarded. However, worn carbide cutting edges can be recoated to extend tool life.
Q: Can standard carbide rods be used to make cutting tools?
A: Yes, standard grade carbide rods can be ground into endmills, drills, etc. But tool life is lower than custom premium carbide blanks.
Q: What precautions are needed when grinding carbide?
A: Carbide grinding needs specialized equipment, rigid fixturing, diamond wheels, high coolant flow, and dresses wheels to avoid heat damage.
Q: How should I store unused carbide blanks?
A: Keep blanks in a clean, dry area away from temperature extremes. Use racks, bins, or trays to avoid damage to blanks.
Q: Where can I get help selecting the optimal carbide blank specifications?
A: Discuss your tool requirements with technical experts at leading carbide blank suppliers. They can guide you in selecting the ideal carbide grade, quality, tolerances, and coating for your application.