Carbide blanks are pieces of carbide that can be custom machined or ground into specialty cutting tools, industrial parts, or other components. Carbide’s high hardness, wear resistance, compressive strength, and chemical inertness make it an ideal material for applications requiring durability, longevity, and dimensional accuracy.
Custom carbide blanks provide the advantage of tailoring a part’s geometry, finish, and tolerances to your exact specifications. This article will cover everything you need to know about custom carbide blanks, including types, design considerations, applications, sourcing, costs, FAQs, and more.
Overview of Custom Carbide Blanks
Carbide, also called cemented or tungsten carbide, refers to a composite material made of fine tungsten carbide particles bonded together with cobalt as the binder metal. Conventional manufacturing processes like pressing and sintering shape powdered carbide into blanks. These blanks then undergo additional machining and finishing to create the final custom part.
The table below summarizes the key characteristics of carbide blanks:
Feature | Description |
---|---|
Base Material | Tungsten carbide particles bonded by cobalt |
Hardness | HV 1600-2400; HRA 86-92 |
Toughness | Hard, brittle material |
Strength | High compressive and transverse rupture strength |
Wear Resistance | Extremely good abrasion and adhesion resistance |
Chemical Resistance | Inert to most acids and alkalis |
Corrosion Resistance | Resists oxidation and chemical corrosion |
Thermal Properties | Withstands high temperatures without deforming or softening |
Other Attributes | Dimensional stability, heat dissipation, thermal shock resistance |
The two main advantages of using custom carbide blanks are:
- Superior material properties like hardness and wear resistance for tough applications
- Customization of part features including special shapes, finishes, geometries, etc.
Carbide blanks can be manufactured into various end-use components across industries like machining, mining, construction, oil and gas, aerospace, medical, and more.
Types of Carbide Blanks
There are several types of carbide blanks available in different material grades. The carbide powder composition and binder percentage determine the performance characteristics. The main types of carbide blanks include:
Tungsten carbide (WC) – Most common grade containing tungsten carbide particles in cobalt binder. Offers good hardness and toughness. General purpose for machining, drawing dies, pelletizing, etc.
Tungsten carbide-cobalt (WC-Co) – Similar to WC but with higher cobalt content (10-30% cobalt). Best hardness and wear resistance but lower toughness. Used for metal cutting tools, draw dies, granulator teeth, etc.
Tungsten carbide-nickel (WC-Ni) – Nickel binder instead of cobalt. Good corrosion resistance and hardness. Applications include pelletizer knives, slitters, granulator tips.
Tungsten carbide-nickel-chromium (WC-Ni-Cr) – Addition of chromium increases hardness, abrasion resistance, and corrosion resistance. Use in paper knives, dicing saws, pelletizer tooling.
Submicron carbide – Ultrafine WC particles under 1 micron with uniform distribution. Very hard, dense structure. Used for micro-grooving, scribing, dicing saws.
Ceramic-carbide composites – Carbide combined with ceramic nanoparticles like titanium carbide, tantalum carbide, chromium carbide. Superior hardness, strength, and wear resistance. Used in metal cutting inserts, drawing dies, pelletizers.
Carbide Type | Hardness | Toughness | Wear Resistance | Corrosion Resistance |
---|---|---|---|---|
Tungsten Carbide (WC) | Very Hard | Moderate | Very Good | Moderate |
Tungsten Carbide-Cobalt (WC-Co) | Extremely Hard | Brittle | Excellent | Low |
Tungsten Carbide-Nickel (WC-Ni) | Very Hard | Good | Very Good | Good |
Tungsten Carbide-Nickel-Chromium (WC-Ni-Cr) | Very Hard | Good | Excellent | Very Good |
Submicron Carbide | Extremely Hard | Brittle | Excellent | Moderate |
Carbide-Ceramic Composites | Extremely Hard | Moderate | Excellent | Very Good |
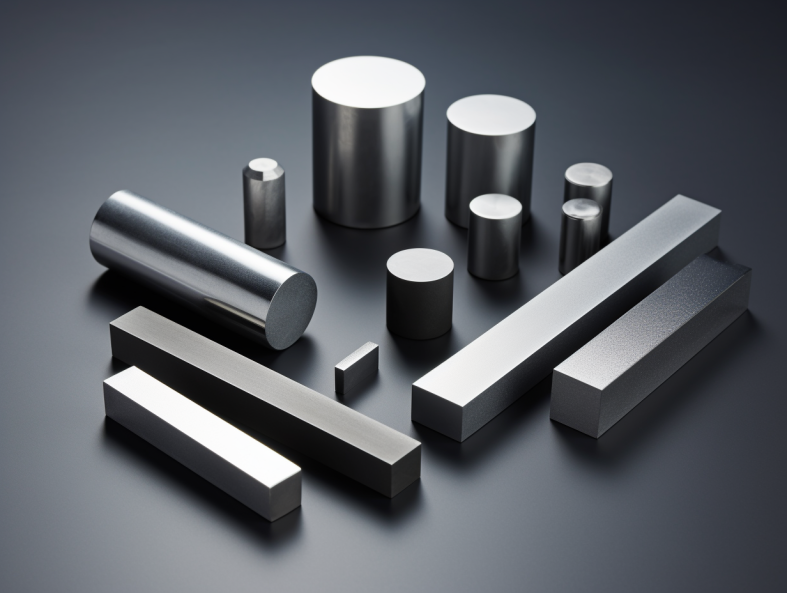
Applications and Uses of Carbide Blanks
The ultrahard and wear-resistant nature of carbide makes it suitable for the following applications when manufactured into end-use parts:
Cutting, Drilling, and Machining
- Cutting tools – inserts, bits, burrs, end mills, reamers
- Drawing dies, form tools, punches
- Wire EDM guides, electrodes
- Drill bits for oil, gas, and geothermal drilling
Wear Parts and Surfaces
- Nozzles, pump parts and impellers
- Crushing, grinding media – hammers, jaws, rollers
- Conveyor and slides – liners, pulverizer tips
- Granulator and pelletizer knife edges and inserts
- Bushings, bearings, pistons
Mining and Construction
- Rock drill bits, tool inserts, teeth
- Pulverizer and mixer blades
- Kiln tires, thermocouple guides
- Balls for grinding mills
- Wire drawing capstans
Electronics and Engineering
- Wafer / silicon scribing and dicing
- Wire drawing dies, extrusion tips
- Micromachining components
- Atomic force microscopy tips
- Microwave guides, electrodes
Medical and Dental
- Dental burs
- Surgical blades and drills
- Orthopedic tools
- Micropipettes, needles
Defense
- Armor penetrators
- Gun barrels
- Guidance system parts
This table summarizes the typical applications for each carbide blank type:
Carbide Type | Typical Applications |
---|---|
Tungsten Carbide (WC) | Cutting tools, drawing dies, pelletizing, machining |
Tungsten Carbide-Cobalt (WC-Co) | Cutting tools, draw dies, granulator teeth |
Tungsten Carbide-Nickel (WC-Ni) | Pelletizer knives, slitters, granulator tips |
Tungsten Carbide-Nickel-Chromium (WC-Ni-Cr) | Paper knives, dicing saws, pelletizer tooling |
Submicron Carbide | Micro-grooving, scribing, dicing saws |
Carbide-Ceramic Composites | Metal cutting inserts, drawing dies, pelletizers |
Design Considerations for Carbide Blanks
Several factors must be considered when designing custom carbide blank parts and tooling:
Geometry: The carbide blank must be shaped to achieve the desired cutting edge or wear surface shape, clearance angles, thickness, hole sizes, etc. Complex 3D geometries are possible.
Tolerances: Carbide can be machined to tight tolerances of ±0.005″ or ±0.127mm or better for precise parts.
Surface Finish: The surface can be polished to a mirror finish or textured as needed. Typical surface finishes range from 2-25 Ra microinches.
Grain Structure: Finer grain carbides offer the best hardness and wear resistance. Micron and submicron grains are preferred.
Percent Binder: Varying the cobalt or nickel binder percentage affects toughness and wear resistance. Common percentages range from 6-30%.
Grades: The carbide grade and composition must align with the material’s hardness, toughness, and chemical resistance needs.
Coatings: Carbide blanks are often coated after machining to further enhance hardness, lubricity, or corrosion resistance. Common coatings include titanium aluminum nitride (TiAlN), titanium nitride (TiN), and diamond-like carbon (DLC).
Dimensions: Carbide blanks can be produced in any required size – typical dimensions range from 0.5″ to 16″ diameter. Thicknesses are application specific.
Testing: Prototyping, evaluation testing, and measurements ensure the carbide blank meets functional requirements before full production.
This table summarizes the key design considerations:
Design Aspect | Options |
---|---|
Geometry | Cutting edge shape, clearance angles, thickness, 3D forms |
Tolerances | ±0.005″ (±0.127mm) or tighter |
Surface Finish | 2-25 Ra microinches |
Grain Structure | Ultrafine grains for maximum hardness |
Binder Content | 6-30% cobalt or nickel |
Grades | WC, WC-Co, WC-Ni variations |
Coatings | TiAlN, TiN, DLC, etc. |
Dimensions | Diameters up to 16″, thickness per application |
Testing | Prototyping, evaluations, measurements |
Specifications for Carbide Blanks
Carbide blank parts must meet precise specifications tailored to the operating conditions and performance requirements. Typical specifications include:
Hardness: Measured on Rockwell or Vickers scales. Desired hardness depends on application, but is typically 86-92 HRA or 1600-2400 HV.
Microstructure: Carbide grain size, binder percentage, homogeneity, and carbide phase composition determine wear resistance, fracture strength, and other properties. Common grades are submicron, micrograin, and macrograin.
Dimensional Tolerance: Blanks require tight dimensional tolerances, often ±0.005″ (±0.127mm) or better. Finished tools may need tolerances up to ±0.0002″ (±0.005mm).
Surface Roughness: For most applications a surface finish of 16 Ra microinches (0.4 Ra microns) or finer is used. Polished, honed, and lapped finishes are also possible.
Straightness: Blanks must have minimal bowing or deviation from a straight profile based on application requirements. 0.001-0.005” per inch or better is typical.
Concentricity: For round carbide blanks, runout must be controlled, often to 0.001” or better for high precision. This ensures concentricity between diameters, bores, and edges.
Defects: Carbide blanks should be free of pores, voids, cracks, pits, inclusions, and other defects which can initiate failures.
This table summarizes common carbide blank specifications:
Parameter | Typical Specification |
---|---|
Hardness | 1600-2400 HV; 86-92 HRA |
Microstructure | Submicron, micrograin, macrograin |
Dimensional Tolerance | ±0.005″ (±0.127mm) or better |
Surface Finish | 16 Ra microinches (0.4 Ra microns) or finer |
Straightness | 0.001-0.005” per inch deviation |
Concentricity | 0.001” runout or better |
Defects | Minimal porosity, pits, cracks |
Machining Carbide Blanks
Creating custom carbide blank components requires specialized machining processes due to the material’s extreme hardness. Here are the typical techniques:
Grinding: Rotary surface grinding, OD/ID grinding, centerless grinding, or CNC grinding machines shape carbide to specifications. Diamond or silicon carbide grinding wheels are used.
Milling: CNC milling with small carbide end mills or indexable carbide insert cutters is an efficient method for complex 3D shapes. Low speeds, feeds, and depths of cut are used.
Turning: CNC turning using polycrystalline diamond (PCD) insert cutters is suitable for diameters and faces. Carbide cannot be cut by high speed steel tools. Low speeds and feeds must be maintained.
EDM: Electric discharge machining (EDM) erodes material via electrical sparks. Wire EDM and sinker EDM allow intricate profiles or cavities. Surface finish may require additional polishing.
Lapping: Abrasive lapping with diamond or boron carbide achieves fine surface finishes and flatness. Used on critical mating surfaces.
Other: Other processes like laser or waterjet cutting and electrical chemical machining (ECM) have very limited use on carbide.
This table compares the machining methods for carbide:
Machining Process | Tools Used | Geometry Capabilities | Finish Achievable | Limitations |
---|---|---|---|---|
Grinding | Diamond or SiC wheels | Simple to complex | Close tolerances | Slow process |
Milling | Carbide end mills, inserts | Complex 3D shapes | Medium finish | Limited tool life |
Turning | PCD insert cutters | OD/ID features | Good finish | Brittle tools, low speeds |
EDM | Copper electrodes | Intricate profiles | Medium finish | Slow process |
Lapping | Diamond abrasives | Flat mating faces | Mirror finish | Dimensional control |
Sourcing Custom Carbide Blanks
Finding a qualified and experienced carbide blank manufacturer is critical to get cost-effective parts that meet your specifications. Use this criteria when selecting suppliers:
- Specialized in custom carbide machining services, at least 10-15 years experience
- Extensive in-house carbide machining capabilities and equipment
- Tight process controls and sophisticated metrology
- Range of available carbide grades and compositions
- Flexible order quantities from prototypes to high production volumes
- Secondary processing like grinding, heat treatment, coatings
- Design, engineering support, and testing services
- ISO certified quality management system
- Competitive pricing with good value
- Responsiveness and excellent project management
Be sure to get quotes from several manufacturers and compare. Request prototypes before committing to a full production order.
Here are the approximate price ranges for custom carbide blank components:
Carbide Product | Typical Price Range |
---|---|
Cutting tools | $8 – $250 per piece |
Carbide wear parts | $5 – $500 per piece |
Precision carbide components | $50 – $2,000 per piece |
Pricing depends heavily on order volumes, complexity, tolerance requirements, lead times, and other specifications.
How to Choose a Carbide Blanks Supplier
Follow these steps for selecting the best custom carbide blank manufacturer:
Define Requirements
- Gather all technical specifications, tolerances, material grade needed, annual quantity estimates
- Determine size limits, geometries, features like bores/holes if known
- Identify any secondary processing required – grinding, heat treating, coatings
Develop Design
- Conceptualize design and function, create models or drawings if available
- Provide operating conditions – temperature, pressure, media, cycles, etc.
- Indicate critical areas – wear surfaces, cutting edges, mating fits
Research Potential Suppliers
- Search for custom carbide machining specialists, evaluate experience and capabilities
- Check certifications – ISO 9001, ISO13485 preferred
- Review example components relevant to your needs
- Determine services offered – design help, prototyping, testing, etc.
Compare Quotes
- Get pricing for prototype parts from several suppliers
- Compare on quality, responsiveness, expertise, services, total costs
- Check production capacity and scalability for higher volumes
Order Prototypes
- Test out 2-3 suppliers by ordering prototypes or small batches first
- Review parts for tolerance, finish, and specification conformance
- Assess overall provider performance on communication, timeliness, packaging, documentation
Select Provider and Scale Up
- Choose the best custom carbide partner based on prototyping experience
- Place larger production orders and monitor quality rigorously
- Develop an ongoing relationship for future projects
Following this process helps identify the ideal custom carbide blanks manufacturer for your specific application needs.
Advantages of Custom Carbide Blanks
Custom carbide blanks offer several notable benefits compared to standard catalog tooling:
Optimized Geometry
- Carbide can be machined into any required shape, angle, or feature
- Ideal for complex profiles like cutting tool inserts, dies, specialty wear parts
- Achieves maximum efficiency of design, avoids unnecessary material
Enhanced Performance
- Geometry enhancements improve cutting, wear life, corrosion resistance
- Ability to control grain structure, grades, and hardness/toughness balance
- Coatings can be applied to further boost properties
Tight Tolerances
- Carbide can be machined to very tight tolerances where needed
- Critical areas like cutting edges, seal faces, mating dimensions can be held to ±0.005″ (±0.13mm) or better
Custom Features
- Unique geometries, hole patterns, slots, relief areas can be incorporated
- Special identifiers like part numbers or logos can be machined on
Material Savings
- No excess material required compared to using standard catalog sizes
- Low production volumes possible since no large blocks must be sintered
Shorter Lead Times
- Avoid long wait times for special sizes versus custom machining existing blanks
- Prototyping in days versus weeks
Cost Savings
- Eliminates secondary grinding or machining steps to modify standard blanks
- Low volume production results in lower costs
For critical applications where standard carbide tooling cannot meet requirements, custom carbide blanks enable optimized performance, geometries, and economical production.
Limitations of Carbide Blanks
Despite the benefits, carbide blanks do have some inherent limitations to consider:
Brittleness
- Carbide has low fracture toughness, limiting use in extreme impact conditions
- Risk of chipping, cracking, or fracturing under shock loads
Machining Difficulty
- Very hard and abrasive material requires special tooling and process controls
- Slow production rates compared to machining metals
- Higher machining costs result
Dimensional Changes
- Carbide growth during sintering can cause distortion or size changes
- Finish machining often required after sintering to final tolerances
Coefficient of Thermal Expansion
- Carbide has a higher CTE than metals, limiting high temperature uses
- Can induce thermal stresses between carbide and mating components
Joining Challenges
- Cannot be welded or mechanically joined by conventional methods
- Brazing or adhesive bonding must be used instead
Limited Size Availability
- Standard blank sizes limited to maximum diameters around 16” (400mm)
- Custom large diameters may lack stability and be prone to cracking
High Cost
- Much more expensive than steel tooling blanks
- Economics limit use to critical wear areas or entirely carbide components
By understanding the limitations, engineers can account for them in the design and machining of custom carbide blanks. Suitable applications maximize the advantages while avoiding excessive stresses.
Frequently Asked Questions About Carbide Blanks
Here are answers to some common questions about custom carbide blanks:
What tolerances can you hold on carbide blanks?
Carbide is machinable to very tight tolerances of ±0.005” (±0.127mm) or ±0.0005” (±0.0127mm) for critical features. Even finer tolerances are possible through additional processing like grinding or lapping. The achievable tolerance depends on the blank size and machining method used.
What surface finishes are possible on carbide?
Surface finishes from 2 microinches Ra (0.05 microns) to around 64 microinches Ra (1.6 microns) can be obtained right off the machining process. Polishing and lapping can further reduce the surface roughness down to < 1 microinch Ra (0.025 microns).
Can you fabricate holes or special geometries in carbide blanks?
Yes, a range of internal features like holes, cross-holes, counterbores, threads, and slots can be incorporated into carbide blanks through CNC machining processes. Complex internal geometries are possible through EDM.
Whatshapes can carbide blanksbe made into?
A wide variety of shapes including round discs, flats, tubes, bars, plates, cylinders and complex 3D contours can be machined from carbide. The only limitations are the initial blank form and the rigidity of thin or small features.
What size carbide blanks can you produce?
Standard tungsten carbide blanks are available up to 16” diameter, but custom blanks can potentially be made larger. However, dimensions over several inches increase the risk of cracking during sintering or machining due to internal stresses.
How should I design parts made from carbide blanks?
Avoid fragile thin sections or segments prone to cracking or fracture. Minimize large voids or holes to maintain strength. Account for carbide’s higher CTE during thermal cycling. Apply generous fillet radii and avoid sharp corners. Consider potential vibration issues that may cause chipping or abrasion.
What are lead times for delivery of custom carbide blanks?
Lead times vary by supplier shop load and part complexity. Typical estimates range from 2-4 weeks for CNC machining standard geometries and grades. More exotic carbide grades, additional processing like EDM or grinding, or high-precision features can extend lead times to 4-8 weeks in some cases. Prototypes can often be delivered in 1-2 weeks.
How should I choose a custom carbide machining supplier?
Look for extensive experience machining carbide specifically – 10+ years preferred. Ensure they have in-house process capabilities and don’t outsource. Check for stringent quality control procedures. Request customer references with similar projects. Evaluate based on responsiveness, pricing, and capabilities to meet your needs.
What testing do you recommend for custom carbide blanks?
Depending on the application, testing may involve microstructure analysis, hardness checks, dimensional verification, microscopy, chemical composition confirmation, grain size measurement, test runs or trials under actual loading conditions, CT scanning to check for internal voids or defects, strength testing, etc. Discuss required testing with your supplier.
Conclusion
Custom carbide blanks enable engineers to optimize the geometry, tolerances, hardness, toughness, and other properties for their specific application. Carbide’s extreme wear resistance allows manufacture of durable components with long working life across a diverse range of industries.
Collaborating with a specialized carbide machining provider makes producing custom blanks fast and affordable, even in low quantities. By supplying your requirements and prototypes for testing, they can quickly hone in on a design that meets your needs. The result is exceptional performance and value from your custom carbide components.