Introduction
Definition of cemented carbide unground rod
A cemented carbide unground rod is a type of material commonly used in the manufacturing industry. It is made by combining tungsten carbide particles with a binder material, such as cobalt, to form a solid and durable rod. The unground rod refers to the fact that the rod has not undergone any grinding or finishing processes, and is therefore in its raw and unfinished state. Cemented carbide unground rods are known for their high hardness, wear resistance, and strength, making them ideal for various applications, including cutting tools, wear parts, and tooling components.
Applications of cemented carbide unground rod
Cemented carbide unground rod finds wide-ranging applications in various industries due to its exceptional hardness, strength, and wear resistance. One of its primary uses is in the manufacturing of cutting tools such as drills, end mills, and inserts, where it provides excellent performance and extended tool life. Additionally, cemented carbide unground rod is utilized in the production of wear parts for mining and construction equipment, as well as in the fabrication of precision components for the automotive and aerospace industries. Its high thermal and chemical stability make it suitable for applications in high-temperature environments, such as in the oil and gas sector. Overall, the applications of cemented carbide unground rod are diverse and crucial in enhancing productivity and efficiency in various industrial sectors.
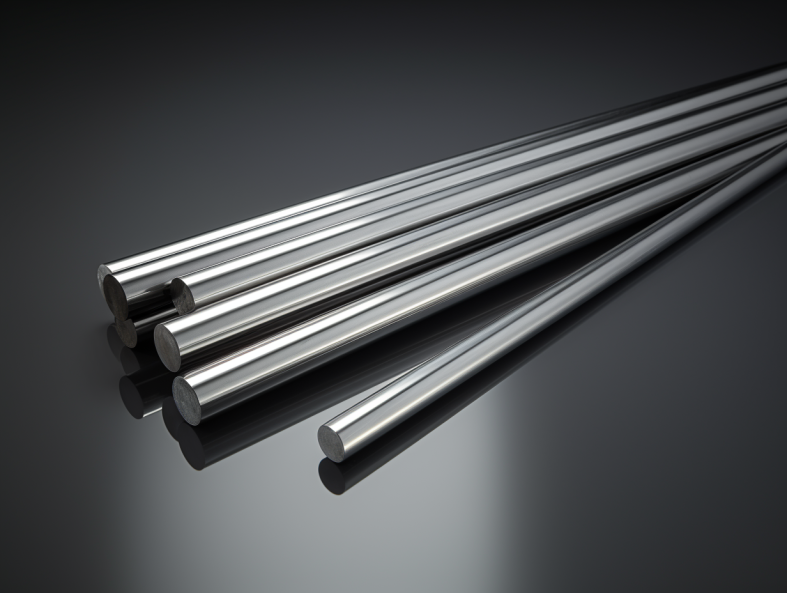
Importance of cemented carbide unground rod in various industries
Cemented carbide unground rods play a crucial role in various industries due to their exceptional properties and characteristics. These rods are widely used in applications that require high strength, wear resistance, and toughness. The importance of cemented carbide unground rods lies in their ability to withstand extreme conditions, making them suitable for use in industries such as manufacturing, construction, mining, and oil and gas. Their high thermal conductivity and resistance to corrosion make them ideal for cutting tools, molds, and wear parts. Additionally, these rods offer excellent dimensional stability and can be easily machined to meet specific requirements, further enhancing their versatility and usability. Overall, the use of cemented carbide unground rods is of utmost importance in various industries, contributing to improved efficiency, durability, and performance.
Composition
Primary components of cemented carbide unground rod
Cemented carbide unground rod is composed of two primary components: tungsten carbide and a binder metal. Tungsten carbide, a compound of tungsten and carbon, provides the hardness and wear resistance to the rod. The binder metal, typically cobalt or nickel, acts as a binding agent, holding the tungsten carbide particles together and providing toughness and strength to the rod. These primary components work together to make cemented carbide unground rod a durable and high-performance material.
Role of each component in the performance of the rod
The performance of the cemented carbide unground rod is influenced by various components. Each component plays a crucial role in determining the overall performance and durability of the rod. The main components of the rod include tungsten carbide, cobalt binder, and other trace elements. Tungsten carbide is the primary component that provides high hardness and wear resistance to the rod. Cobalt binder acts as a binding agent, holding the tungsten carbide grains together and providing strength to the rod. The addition of trace elements further enhances the performance of the rod by improving its toughness, corrosion resistance, and thermal stability. Therefore, the proper combination and composition of each component are essential in achieving optimal performance and longevity of the cemented carbide unground rod.
Factors affecting the composition of cemented carbide unground rod
There are several factors that can affect the composition of cemented carbide unground rod. One of the key factors is the choice of raw materials. The composition of cemented carbide unground rod is determined by the types and proportions of the powders used, including tungsten carbide and cobalt. The quality and purity of these raw materials can greatly impact the final composition and performance of the rod. Another factor to consider is the manufacturing process. The temperature, pressure, and duration of the sintering process can influence the composition and structure of the rod. Additionally, any impurities or contaminants present during production can also affect the composition. It is important to carefully control these factors to ensure the desired composition and properties of the cemented carbide unground rod.
Manufacturing Process
Powder preparation
Powder preparation is a crucial step in the production of cemented carbide unground rod. It involves the careful selection and blending of raw materials, such as tungsten carbide and cobalt powders, to achieve the desired composition and properties. The raw materials are first weighed and then mixed in a controlled environment to ensure uniform distribution. This mixture is then subjected to a series of processes, including milling and sieving, to further refine the powder particles. The resulting powder is then ready for the subsequent steps in the manufacturing process of cemented carbide unground rod.
Mixing and blending
Mixing and blending is a crucial step in the production of cemented carbide unground rods. During this process, various raw materials such as tungsten carbide powder, cobalt powder, and other additives are carefully measured and mixed together in precise proportions. The purpose of this step is to ensure a homogeneous distribution of the ingredients, which is essential for achieving the desired properties and performance of the final product. The mixing and blending process is typically carried out in specialized equipment, such as ball mills or mixers, that provide efficient and uniform blending. Once the materials are thoroughly mixed, the resulting mixture is then ready for the next stage of the manufacturing process.
Compaction and shaping
Compaction and shaping are crucial steps in the production of cemented carbide unground rod. During compaction, a mixture of tungsten carbide powder and a binder material is pressed into a desired shape using high pressure. This process ensures that the powder particles are densely packed and bonded together. Shaping is then carried out to further refine the dimensions and surface finish of the rod. Various techniques such as extrusion, rolling, and drawing can be employed to achieve the desired shape. These steps are essential for ensuring the quality and performance of the cemented carbide unground rod.
Properties
Hardness and wear resistance
Cemented carbide unground rod exhibits exceptional hardness and wear resistance, making it a highly sought-after material in various industries. The hardness of the rod is attributed to the combination of tungsten carbide particles and a metallic binder, typically cobalt or nickel. This unique composition enables the rod to withstand intense pressure and abrasion, ensuring its longevity and durability. Moreover, the wear resistance of cemented carbide unground rod allows it to maintain its performance even in harsh operating conditions, making it an ideal choice for applications that involve high temperatures, heavy loads, and abrasive environments. With its remarkable hardness and wear resistance, cemented carbide unground rod is a reliable and efficient solution for numerous industrial applications.
Strength and toughness
Cemented carbide unground rod exhibits exceptional strength and toughness, making it an ideal material for various industrial applications. The combination of high hardness and resistance to wear allows it to withstand the most demanding conditions, ensuring long-lasting performance. Additionally, its impressive toughness enables it to absorb and dissipate impact energy, preventing fractures and breakages. Whether used in cutting tools, mining equipment, or wear-resistant parts, cemented carbide unground rod delivers unparalleled strength and durability, making it a preferred choice in many industries.
Thermal and chemical stability
Cemented carbide unground rod exhibits exceptional thermal and chemical stability, making it a highly sought-after material in various industries. Its ability to withstand high temperatures and resist corrosion allows it to be used in demanding applications where other materials would fail. The unique composition of cemented carbide, consisting of a hard carbide phase embedded in a tough metallic binder, contributes to its remarkable stability. Whether it is exposed to extreme heat or harsh chemicals, cemented carbide unground rod maintains its structural integrity, ensuring reliable and long-lasting performance.
Applications
Cutting and machining tools
Cemented carbide unground rod is a crucial material used in the manufacturing of cutting and machining tools. With its exceptional hardness and wear resistance, cemented carbide unground rod is able to withstand the extreme conditions and pressures of cutting and machining processes. Its high thermal conductivity also allows for efficient heat dissipation, preventing the tool from overheating and prolonging its lifespan. Moreover, the unique composition of cemented carbide unground rod enables it to maintain its sharpness and cutting edge, ensuring precise and accurate cuts. This makes it an indispensable component in the production of high-quality cutting and machining tools.
Mining and drilling equipment
Cemented carbide unground rod is an integral component in the mining and drilling equipment industry. With its exceptional hardness and wear resistance, cemented carbide unground rod is widely used in the manufacturing of drilling bits, cutting tools, and wear parts for mining and drilling applications. Its superior strength and durability make it an ideal material for withstanding the harsh conditions encountered in mining and drilling operations. The use of cemented carbide unground rod in mining and drilling equipment ensures increased productivity, reduced downtime, and enhanced performance, making it a vital component in the industry.
Wear parts for industrial machinery
Cemented carbide unground rods are essential wear parts for industrial machinery. These rods are made from a combination of tungsten carbide and cobalt, resulting in a material that is extremely hard and wear-resistant. They are commonly used in industries such as mining, construction, and manufacturing, where they are employed in various applications such as drilling, cutting, and milling. The high hardness of cemented carbide unground rods allows them to withstand the harsh operating conditions of industrial machinery, ensuring long-lasting performance and minimal downtime. With their exceptional durability and reliability, these rods play a crucial role in enhancing the efficiency and productivity of industrial processes.
Advantages and Limitations
Advantages of cemented carbide unground rod
Cemented carbide unground rod offers several advantages that make it a popular choice in various applications. Firstly, its exceptional hardness and wear resistance ensure long-lasting performance even in the most demanding conditions. This makes it ideal for use in industries such as mining, construction, and manufacturing. Additionally, cemented carbide unground rod exhibits high strength and toughness, allowing it to withstand heavy loads and impacts without deformation or breakage. Moreover, its excellent thermal and chemical stability make it resistant to corrosion and oxidation, further enhancing its durability. Lastly, the dimensional accuracy and precision of cemented carbide unground rod ensure consistent performance and tight tolerances, making it suitable for applications that require high precision. Overall, the advantages of cemented carbide unground rod make it a reliable and cost-effective choice for various industrial and engineering applications.
Limitations and challenges in its use
Cemented carbide unground rod, despite its numerous advantages, is not without its limitations and challenges in its use. One of the main limitations is the difficulty in achieving precise dimensions and tolerances. Due to the nature of the manufacturing process, slight variations in composition and grain size can affect the final product, making it challenging to consistently produce rods with exact specifications. Another challenge is the high cost associated with producing cemented carbide unground rods. The raw materials used in the production process, such as tungsten carbide powder and cobalt, are expensive, leading to higher production costs. Additionally, the hardness and brittleness of cemented carbide unground rods can make machining and shaping them more challenging compared to other materials. Despite these limitations and challenges, cemented carbide unground rods remain a popular choice in various industries due to their exceptional hardness, wear resistance, and high strength.
Future prospects and research areas
In the field of cemented carbide unground rod, there are several future prospects and research areas that hold great potential. One such area is the development of advanced manufacturing techniques that can enhance the performance and properties of cemented carbide unground rod. This includes exploring new methods for improving the hardness, wear resistance, and toughness of the material. Additionally, research efforts can be directed towards optimizing the composition and microstructure of cemented carbide unground rod to achieve superior mechanical and thermal properties. Furthermore, investigating the use of alternative raw materials and sustainable manufacturing processes can contribute to the future sustainability of cemented carbide unground rod production. Overall, the future prospects in this field are promising, and continued research and innovation can lead to significant advancements in the performance and applications of cemented carbide unground rod.