Introduction
Definition of cemented carbide rod
A cemented carbide rod with coolant hole is a type of cutting tool used in various machining operations. It is made from a combination of tungsten carbide particles and a metal binder, typically cobalt. The coolant hole is a feature that allows for the passage of coolant or cutting fluid, which helps to reduce heat and friction during the cutting process. This improves tool life and cutting performance, resulting in higher productivity and better surface finish. Cemented carbide rods with coolant holes are commonly used in industries such as aerospace, automotive, and manufacturing.
Importance of coolant hole in cemented carbide rod
The coolant hole in a cemented carbide rod plays a crucial role in various machining operations. It is designed to facilitate the effective cooling and lubrication of the cutting tool during the cutting process. By directing coolant directly to the cutting edge, the coolant hole helps to dissipate heat generated by the friction between the tool and the workpiece. This not only prolongs the tool’s lifespan but also ensures consistent and accurate cutting performance. Additionally, the coolant hole helps to flush away chips and debris, preventing them from clogging the cutting edge and affecting the machining quality. Overall, the presence of a coolant hole in a cemented carbide rod significantly enhances the tool’s efficiency, productivity, and longevity.
Overview of the article
The article titled ‘Cemented Carbide Rod with Coolant Hole’ provides an in-depth overview of this innovative and essential tool used in various industries. This paragraph will highlight the key features, benefits, and applications of the cemented carbide rod with a coolant hole. It will discuss how this rod is manufactured using high-quality materials and advanced techniques, ensuring superior durability and performance. Additionally, it will emphasize the importance of the coolant hole in enhancing heat dissipation and prolonging the tool’s lifespan. The paragraph will also mention the diverse applications of this rod, including machining, metalworking, and woodworking, where it offers increased efficiency, precision, and cost-effectiveness. Overall, this article aims to provide a comprehensive understanding of the cemented carbide rod with a coolant hole and its significance in modern industrial processes.
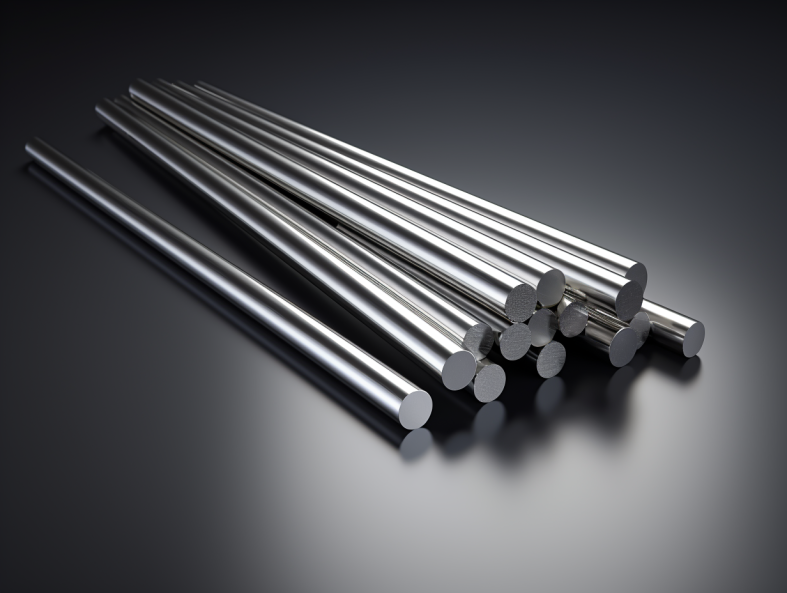
Properties of Cemented Carbide Rod
Hardness and wear resistance
Cemented carbide rods with coolant holes are known for their exceptional hardness and wear resistance. These rods are specifically designed to withstand high temperatures and abrasive environments, making them ideal for various industrial applications. The addition of coolant holes further enhances their performance by allowing for efficient heat dissipation and lubrication. The hardness of cemented carbide rods ensures long-lasting durability, while their wear resistance ensures minimal material loss over time. Whether used in machining, drilling, or cutting operations, cemented carbide rods with coolant holes provide reliable and consistent performance, making them a valuable tool for any industry.
Strength and toughness
Cemented carbide rods with coolant holes offer a unique combination of strength and toughness. These rods are specially designed to withstand high temperatures and heavy loads, making them ideal for use in various industrial applications. The coolant holes provide an added advantage by effectively dissipating heat, ensuring optimal performance and prolonging the lifespan of the rods. With their exceptional strength and toughness, cemented carbide rods with coolant holes are a reliable choice for demanding machining operations, providing enhanced productivity and cost-efficiency.
Thermal conductivity
Thermal conductivity is an important property of cemented carbide rods with coolant holes. It refers to the ability of the material to conduct heat. In the case of cemented carbide rods, a high thermal conductivity is desirable as it allows for efficient heat transfer away from the cutting zone. This helps in reducing the temperature of the tool, preventing thermal damage and prolonging the tool life. The presence of coolant holes further enhances the thermal conductivity by facilitating the flow of coolant, which helps in dissipating heat more effectively. By optimizing the thermal conductivity of cemented carbide rods with coolant holes, manufacturers can ensure better performance and durability of cutting tools in various machining applications.
Manufacturing Process
Powder preparation
Powder preparation is a crucial step in the production of cemented carbide rods with coolant holes. The quality and characteristics of the powder used directly impact the performance and durability of the final product. In this process, various raw materials are carefully selected and mixed in precise proportions to create a homogenous mixture. The mixture is then subjected to a series of grinding and milling processes to achieve the desired particle size and distribution. Additionally, additives and binders may be incorporated to enhance the powder’s flowability and compactability. The resulting powder is then ready for the subsequent steps in the manufacturing process.
Mixing and pressing
In the process of manufacturing cemented carbide rods with coolant holes, the stage of mixing and pressing plays a crucial role. During this stage, various raw materials such as tungsten carbide powder, cobalt powder, and other additives are carefully mixed together to achieve the desired composition. The mixture is then compacted under high pressure to form a solid rod shape. The pressing process ensures that the materials are evenly distributed and tightly bonded, resulting in a strong and durable carbide rod. Additionally, the presence of coolant holes is strategically incorporated during the pressing stage to allow for efficient cooling during machining operations, enhancing the performance and longevity of the rod.
Sintering
Sintering is a crucial process in the production of cemented carbide rods with coolant holes. During sintering, the powdered tungsten carbide and binder materials are heated at high temperatures to form a solid, dense structure. This process allows for the consolidation of the individual particles, resulting in improved strength and hardness. Additionally, the presence of coolant holes in the carbide rods enhances their performance by facilitating the efficient cooling of the cutting tool during operation. Sintering not only ensures the structural integrity of the cemented carbide rods but also plays a vital role in determining their overall quality and performance.
Coolant Hole Design
Purpose of coolant hole
The purpose of the coolant hole in a cemented carbide rod is to enhance the performance and longevity of the rod during machining processes. By allowing coolant to flow through the hole, heat generated during cutting operations is effectively dissipated, preventing the rod from overheating and maintaining its structural integrity. This helps to reduce tool wear, improve cutting speeds, and ensure consistent and accurate machining results. Additionally, the coolant hole aids in chip evacuation, allowing for smoother and more efficient chip removal, which further contributes to the overall efficiency and effectiveness of the machining process.
Factors to consider in coolant hole design
When designing the coolant hole in a cemented carbide rod, there are several factors that need to be considered. Firstly, the size and shape of the hole play a crucial role in determining the effectiveness of the coolant flow. A larger hole allows for better coolant circulation, while a specific shape can help direct the flow towards specific areas. Secondly, the positioning of the hole is important in ensuring that the coolant reaches the desired areas of the rod. It should be strategically placed to cool the cutting edge and reduce heat buildup. Additionally, the number of coolant holes should be determined based on the application requirements and the desired cooling effect. Too few holes may result in inadequate cooling, while too many holes can weaken the structural integrity of the rod. Lastly, the material used for the coolant hole should be compatible with the coolant being used to prevent any chemical reactions or corrosion. Taking all these factors into consideration will result in a well-designed coolant hole that enhances the performance and lifespan of the cemented carbide rod.
Types of coolant hole designs
There are several types of coolant hole designs used in cemented carbide rods. One common design is the straight coolant hole, where the hole runs straight through the rod. This design allows for efficient coolant flow and helps in cooling the rod during machining operations. Another design is the spiral coolant hole, where the hole is spiraled around the rod. This design provides a longer coolant path, ensuring better heat dissipation and improved chip evacuation. Additionally, there are also custom coolant hole designs that can be tailored to specific machining requirements. These designs may include combinations of straight and spiral holes or unique patterns to optimize coolant flow and cooling performance. Overall, the choice of coolant hole design depends on the specific application and machining conditions, with each design offering its own advantages and benefits.
Advantages of Coolant Hole in Cemented Carbide Rod
Improved heat dissipation
Improved heat dissipation is a crucial factor in the performance of cemented carbide rods with coolant holes. The addition of coolant holes enhances the cooling effect, allowing for efficient heat dissipation during machining operations. This improved heat dissipation helps to prevent overheating and prolongs the lifespan of the carbide rod. By effectively managing heat, the cemented carbide rod with coolant holes ensures optimal performance and accuracy, making it an excellent choice for various machining applications.
Reduced cutting temperature
Reduced cutting temperature is a crucial factor in the performance of a cemented carbide rod with a coolant hole. By incorporating a coolant hole in the rod, heat generated during the cutting process can be effectively dissipated, resulting in lower cutting temperatures. This not only helps to prolong the tool life but also improves the overall cutting performance. The coolant hole allows for better chip evacuation and reduces the risk of workpiece material sticking to the cutting edge. With reduced cutting temperature, operators can achieve higher machining speeds and feed rates, leading to increased productivity and efficiency.
Extended tool life
The use of cemented carbide rods with coolant holes has significantly extended the tool life in various industries. The coolant holes allow for efficient cooling during the machining process, reducing heat buildup and minimizing tool wear. This extended tool life not only improves productivity but also reduces the frequency of tool replacements, resulting in cost savings for businesses. Additionally, the use of coolant holes helps maintain dimensional accuracy and surface finish, ensuring high-quality machining results. Overall, the incorporation of cemented carbide rods with coolant holes has proven to be a valuable solution for enhancing tool performance and longevity in industrial applications.
Applications of Cemented Carbide Rod with Coolant Hole
Metal cutting and machining
Metal cutting and machining play a crucial role in various industries, and the use of cemented carbide rods with coolant holes has revolutionized the process. These rods are specially designed to withstand high temperatures and provide efficient cooling during cutting operations. The coolant holes ensure that the heat generated during the cutting process is quickly dissipated, preventing damage to the workpiece and extending the tool life. With their exceptional hardness and wear resistance, cemented carbide rods with coolant holes offer superior performance and precision in metal cutting applications. They are widely used in the manufacturing of automotive parts, aerospace components, and various other high-precision products. The integration of coolant holes in these rods has significantly improved the efficiency and productivity of metal cutting and machining processes, making them an indispensable tool in the industry.
Drilling and milling
In the process of drilling and milling, the use of cemented carbide rods with coolant holes offers several advantages. The coolant holes allow for effective cooling and lubrication, reducing heat and friction during the machining process. This helps to prolong the tool life and improve the overall machining efficiency. Additionally, the coolant holes also help to remove chips and debris from the cutting area, ensuring a clean and smooth operation. With the use of cemented carbide rods with coolant holes, drilling and milling operations can be carried out with precision and accuracy, resulting in high-quality finished products.
Turning and threading
Turning and threading are two common machining processes used in the manufacturing of cemented carbide rods with coolant holes. Turning involves removing material from the rod’s outer diameter to create a cylindrical shape, while threading is the process of cutting helical grooves on the rod’s surface to create threads. These processes require precision and expertise to ensure the dimensions and surface finish of the rod meet the required specifications. Additionally, coolant holes are incorporated into the design to optimize the cooling and lubrication during the machining process, improving the tool life and overall performance of the cemented carbide rod.