Introduction
Definition of cemented carbide rod
A cemented carbide rod is a type of cutting tool that is commonly used in various industries. It is made by combining tungsten carbide particles with a binder material, such as cobalt, through a process called sintering. This results in a hard and durable material that is resistant to wear and can withstand high temperatures. Cemented carbide rods are known for their excellent cutting performance and are widely used in machining applications, including milling, drilling, and turning. They are especially suitable for cutting hard materials like steel, cast iron, and stainless steel. With their superior hardness and toughness, cemented carbide rods have become an indispensable tool in the manufacturing and metalworking industries.
History of cemented carbide rod
Cemented carbide rod, also known as tungsten carbide rod, has a rich history dating back to the early 20th century. It was first developed by researchers seeking to improve the performance of cutting tools. The breakthrough came when they discovered that combining tungsten carbide, a hard and brittle material, with a metallic binder such as cobalt could create a material with exceptional hardness, strength, and wear resistance. Since then, cemented carbide rod has revolutionized the cutting tool industry, enabling faster and more precise machining of various materials. Today, it is widely used in industries such as aerospace, automotive, and manufacturing, where high-performance cutting tools are essential for efficient and accurate operations.
Applications of cemented carbide rod
Cemented carbide rods are widely used in various cutting tool applications due to their exceptional hardness and wear resistance. These rods are commonly used in the manufacturing industry for cutting, drilling, and milling operations. They are especially popular in the metalworking industry for machining hardened steels, cast irons, and stainless steels. The high hardness of cemented carbide rods allows them to withstand the extreme heat and pressure generated during cutting, ensuring a longer tool life and improved cutting performance. Additionally, these rods are also used in woodworking, plastic molding, and other industries where precision cutting and shaping are required. With their superior strength and durability, cemented carbide rods have become an indispensable tool for professionals and hobbyists alike.
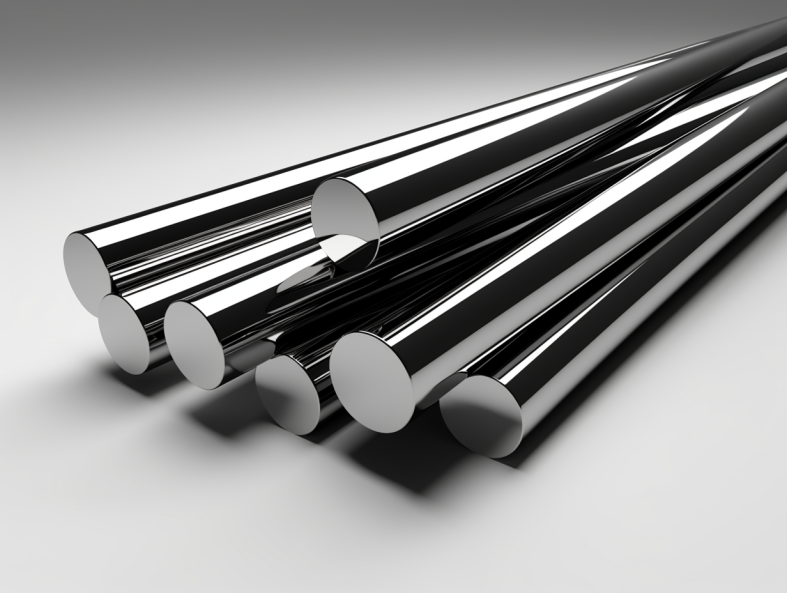
Composition
Tungsten carbide
Tungsten carbide is a type of cemented carbide that is widely used in cutting tools due to its exceptional hardness and toughness. It is composed of tungsten and carbon atoms, which are combined through a process called sintering. The resulting material has a high resistance to wear and can withstand high temperatures, making it ideal for applications that require precision cutting, such as machining and metalworking. Tungsten carbide cutting tools offer superior performance and durability, making them a popular choice in various industries, including automotive, aerospace, and manufacturing.
Cobalt binder
Cobalt binder is an essential component in cemented carbide rods for cutting tools. It acts as a binding agent, holding the tungsten carbide particles together to form a strong and durable material. The addition of cobalt enhances the toughness and wear resistance of the cutting tool, allowing it to withstand high-speed machining and heavy-duty cutting applications. Furthermore, the cobalt binder also helps to improve the overall performance and stability of the cutting tool, ensuring precise and efficient cutting operations. With its crucial role in cemented carbide rods, the cobalt binder is a key factor in achieving superior cutting performance and extending the tool’s lifespan.
Other additives
Cemented carbide rods for cutting tools are widely used in various industries due to their exceptional hardness and wear resistance. However, in order to enhance the performance and properties of these rods, other additives are often incorporated. These additives can include cobalt, titanium, tantalum, and niobium, among others. The addition of these elements helps improve the toughness, strength, and thermal stability of the cemented carbide rods, making them even more suitable for demanding cutting applications. Furthermore, the use of these additives allows for the customization of the rods’ properties to meet specific requirements of different cutting operations. Overall, the incorporation of other additives in cemented carbide rods greatly enhances their performance and expands their range of applications in the cutting tool industry.
Manufacturing Process
Powder preparation
Powder preparation is a crucial step in the production of cemented carbide rods for cutting tools. It involves the meticulous selection and blending of various raw materials, such as tungsten carbide powder, cobalt powder, and other additives. The quality and consistency of the powder mixture directly impact the performance and durability of the final product. To ensure optimal results, manufacturers employ advanced techniques, including ball milling and mixing, to achieve a homogeneous and fine-grained powder. This ensures that the cemented carbide rods possess the desired hardness, strength, and wear resistance necessary for efficient cutting operations.
Mixing and blending
Mixing and blending are crucial steps in the production of cemented carbide rods for cutting tools. During this process, various raw materials such as tungsten carbide powder, cobalt powder, and other additives are carefully measured and mixed together to create a homogeneous mixture. The quality of the mixing and blending directly affects the final properties and performance of the cemented carbide rods. Therefore, strict control and monitoring of the mixing parameters, such as mixing time, speed, and temperature, are essential to ensure the desired composition and uniformity of the mixture. Additionally, advanced mixing techniques, such as high-energy ball milling, are often employed to achieve a finer and more uniform distribution of the particles, resulting in improved strength, hardness, and wear resistance of the cemented carbide rods. Overall, the mixing and blending process plays a vital role in the production of high-quality cemented carbide rods for cutting tools.
Compaction and shaping
Compaction and shaping are crucial steps in the production of cemented carbide rods for cutting tools. During the compaction process, a mixture of tungsten carbide powder and a binder is compressed under high pressure to form a solid mass. This mass is then shaped into the desired rod shape using various shaping techniques, such as extrusion or pressing. The compaction and shaping processes ensure that the cemented carbide rods have the necessary strength, hardness, and dimensional accuracy required for cutting applications. Additionally, these processes also play a significant role in controlling the microstructure and porosity of the rods, which further contribute to their overall performance and durability. Overall, compaction and shaping are critical stages in the manufacturing of cemented carbide rods, ensuring that they meet the stringent requirements of cutting tool applications.
Properties
Hardness
Cemented carbide rods for cutting tools are renowned for their exceptional hardness. With a high level of tungsten carbide content, these rods exhibit a remarkable resistance to wear and abrasion, making them ideal for demanding cutting applications. The hardness of cemented carbide rods allows for precise and efficient cutting, ensuring clean and accurate results. Whether used in machining, milling, or drilling operations, these rods provide the necessary strength and durability to withstand heavy loads and prolonged use. Additionally, their hardness ensures minimal deformation, maintaining the integrity of the cutting edge for extended periods. Overall, the hardness of cemented carbide rods is a key factor in their effectiveness and reliability as cutting tools.
Wear resistance
Wear resistance is a crucial factor to consider when it comes to cutting tools, and cemented carbide rods excel in this aspect. The unique composition of cemented carbide, which consists of tungsten carbide particles embedded in a cobalt matrix, provides exceptional hardness and durability. This results in a cutting tool that can withstand the most demanding machining applications without compromising on performance. The high wear resistance of cemented carbide rods ensures extended tool life, reducing the need for frequent replacements and increasing productivity. Whether it’s for milling, drilling, or turning operations, cemented carbide rods are the go-to choice for professionals in the metalworking industry.
Toughness
Toughness is a crucial characteristic when it comes to cemented carbide rods for cutting tools. It refers to the ability of the material to resist fracture and deformation under applied stress. A high level of toughness ensures that the rod can withstand the demanding conditions of cutting operations without breaking or chipping. This is particularly important in industries such as machining and metalworking where precision and durability are paramount. Cemented carbide rods with excellent toughness not only enhance the overall performance and longevity of cutting tools but also contribute to improved productivity and cost-effectiveness in various manufacturing processes.
Advantages
High cutting performance
Cemented carbide rods are widely recognized for their high cutting performance in the field of cutting tools. With their exceptional hardness and wear resistance, these rods are capable of withstanding the most demanding cutting applications. The unique composition of cemented carbide, consisting of tungsten carbide particles embedded in a cobalt matrix, provides the necessary strength and toughness for efficient and precise cutting. Whether it’s machining, milling, or drilling, cemented carbide rods consistently deliver superior performance, making them the preferred choice for professionals in various industries.
Long tool life
Long tool life is one of the key advantages of using cemented carbide rods for cutting tools. These rods are known for their exceptional durability and resistance to wear, allowing them to maintain their sharpness and cutting performance for extended periods of time. With a longer tool life, operators can reduce downtime for tool changes and increase productivity. This makes cemented carbide rods a preferred choice for industries that require high precision and efficiency in cutting operations. Whether it’s in metalworking, woodworking, or any other application, the longevity of cemented carbide rods ensures cost savings and improved overall performance.
Wide range of applications
Cemented carbide rods for cutting tools have a wide range of applications in various industries. These rods are known for their exceptional hardness, wear resistance, and high strength, making them ideal for cutting, drilling, and shaping materials such as wood, metal, and plastics. They are widely used in the manufacturing and construction sectors, as well as in the automotive, aerospace, and electronics industries. The versatility and durability of cemented carbide rods make them a popular choice among professionals and hobbyists alike, offering precision and efficiency in a wide variety of applications.
Maintenance and Care
Proper storage
Proper storage is crucial for maintaining the quality and performance of cemented carbide rods used for cutting tools. These rods are made from a combination of tungsten carbide and a binder material, which gives them their exceptional hardness and durability. To ensure their longevity, it is important to store them in a dry and controlled environment, away from moisture and extreme temperatures. Additionally, they should be stored in a vertical position to prevent any bending or warping. Proper storage not only extends the lifespan of the rods but also ensures consistent and precise cutting performance when they are used in various machining applications.
Cleaning and lubrication
Cleaning and lubrication are crucial steps in maintaining the performance and longevity of cemented carbide rods for cutting tools. Proper cleaning removes any debris or contaminants that may have accumulated during use, ensuring optimal cutting performance. Lubrication, on the other hand, reduces friction and heat generation during cutting, prolonging the life of the carbide rod. It is recommended to use a non-corrosive cleaning agent and a high-quality lubricant specifically designed for cutting tools. Regular cleaning and lubrication not only enhance the efficiency of the cutting process but also prevent premature wear and damage to the rod, ultimately saving time and money in the long run.
Regular inspection and replacement
Regular inspection and replacement are crucial for maintaining the efficiency and longevity of cemented carbide rods used in cutting tools. Over time, these rods can wear down due to the constant friction and pressure exerted during cutting operations. Therefore, it is essential to regularly inspect the condition of the rods to identify any signs of wear or damage. If any issues are detected, timely replacement is necessary to ensure optimal performance and prevent any potential failure or accidents. By implementing a proactive inspection and replacement schedule, operators can maximize the lifespan of the cemented carbide rods and minimize downtime in the cutting process.