Introduction
Definition of Cemented Carbide Rod Blank
A cemented carbide rod blank is a type of material used in various industries, particularly in the manufacturing and machining sectors. It is made by combining tungsten carbide particles with a binder material, such as cobalt, through a process called sintering. The resulting material is extremely hard, durable, and resistant to wear and corrosion, making it ideal for applications that require high strength and longevity. Cemented carbide rod blanks are commonly used to produce cutting tools, such as drills, end mills, and inserts, as well as wear parts for mining, construction, and oil and gas industries. They offer excellent performance and precision, allowing for efficient and accurate machining operations. Overall, cemented carbide rod blanks play a crucial role in enhancing productivity and efficiency in various manufacturing processes.
Applications of Cemented Carbide Rod Blank
Cemented carbide rod blanks have a wide range of applications in various industries. One of the key applications is in the manufacturing of cutting tools. The high hardness and wear resistance of cemented carbide make it an ideal material for producing drill bits, end mills, and inserts for machining operations. Additionally, cemented carbide rod blanks are used in the production of wear parts for mining and construction equipment, such as crusher hammers and drilling tools. The exceptional strength and toughness of cemented carbide contribute to the durability and performance of these components. Moreover, cemented carbide rod blanks find applications in the automotive industry for producing punches, dies, and wear-resistant components for engine parts. Overall, the versatility and superior properties of cemented carbide rod blanks make them indispensable in various industrial applications.
Importance of Cemented Carbide Rod Blank in Various Industries
Cemented carbide rod blanks play a crucial role in various industries due to their exceptional properties. These rod blanks are made from a combination of tungsten carbide and a binder metal, resulting in a material that is extremely hard, durable, and resistant to wear and corrosion. The importance of cemented carbide rod blanks lies in their ability to withstand high temperatures, maintain their shape and strength under heavy loads, and provide excellent cutting performance. In the manufacturing industry, these rod blanks are widely used for the production of cutting tools, such as drills, end mills, and inserts, which are essential for machining operations. Moreover, cemented carbide rod blanks find applications in the mining, construction, and oil and gas industries, where they are used for drilling, rock breaking, and wear-resistant components. The versatility and reliability of cemented carbide rod blanks make them indispensable in various sectors, contributing to increased efficiency, productivity, and cost-effectiveness.
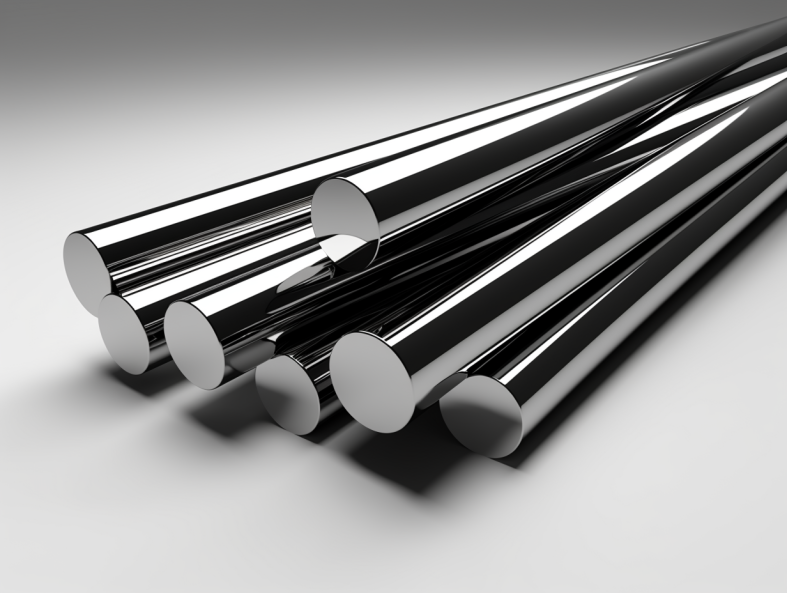
Composition and Manufacturing Process
Materials Used in Cemented Carbide Rod Blank
Cemented carbide rod blanks are composed of a combination of tungsten carbide and a binder material, typically cobalt or nickel. Tungsten carbide, known for its exceptional hardness and wear resistance, makes up the majority of the composition, while the binder material provides strength and toughness. These materials are carefully selected and blended to create a homogeneous mixture, which is then shaped into rod blanks through a process called powder metallurgy. The resulting cemented carbide rod blanks exhibit excellent mechanical properties, making them ideal for various applications in industries such as mining, machining, and metalworking.
Powder Metallurgy Process
The powder metallurgy process is a widely used method for manufacturing cemented carbide rod blanks. It involves several steps, starting with the selection and preparation of high-quality raw materials. These materials, typically tungsten carbide powder and cobalt powder, are carefully mixed and blended to achieve a homogeneous composition. The mixture is then compacted under high pressure to form a green compact. This compact is then subjected to a sintering process, where it is heated in a controlled environment to a temperature below the melting point of the material. During sintering, the powders bond together, resulting in a dense and solid carbide structure. The sintered rod blank is then further processed, including machining, grinding, and polishing, to achieve the desired dimensions and surface finish. The powder metallurgy process ensures the production of high-quality cemented carbide rod blanks with excellent mechanical properties and performance.
Sintering Process
The sintering process is a crucial step in the production of cemented carbide rod blanks. It involves subjecting the raw materials, such as tungsten carbide and cobalt, to high temperatures and pressure in a controlled environment. During sintering, the powders are compacted and fused together, resulting in a dense and solid structure. This process helps to enhance the mechanical properties of the rod blanks, such as hardness, strength, and wear resistance. Additionally, sintering allows for the customization of the carbide composition and microstructure, enabling the production of rod blanks with specific properties tailored to different applications. Overall, the sintering process plays a vital role in ensuring the quality and performance of cemented carbide rod blanks.
Properties and Characteristics
Hardness and Wear Resistance
Cemented carbide rod blanks are known for their exceptional hardness and wear resistance. These rods are manufactured using a combination of tungsten carbide and a binder metal, typically cobalt. The high hardness of the tungsten carbide gives the rod its excellent resistance to wear, making it ideal for applications in industries such as mining, construction, and machining. Additionally, the binder metal provides the necessary toughness and strength to withstand heavy loads and extreme conditions. With their superior hardness and wear resistance, cemented carbide rod blanks are widely used in the production of cutting tools, drilling tools, and wear parts that require long-lasting performance and reliability.
High Strength and Toughness
Cemented carbide rod blanks are renowned for their exceptional high strength and toughness. These rods are specifically designed to withstand heavy loads and harsh operating conditions, making them ideal for a wide range of industrial applications. With their superior mechanical properties, cemented carbide rod blanks provide excellent resistance to wear, corrosion, and deformation. Whether used in the manufacturing of cutting tools, mining equipment, or wear parts, these rod blanks offer unmatched durability and reliability. Furthermore, their high strength ensures enhanced performance and extended tool life, resulting in increased productivity and cost savings. Overall, cemented carbide rod blanks are a vital component in various industries, delivering exceptional strength and toughness for demanding applications.
Thermal Stability and Chemical Inertness
Cemented carbide rod blanks exhibit exceptional thermal stability and chemical inertness. These properties make them highly suitable for applications in high-temperature environments and corrosive conditions. The unique combination of tungsten carbide and a binder material provides excellent resistance to heat, oxidation, and chemical reactions. This ensures the longevity and reliability of cemented carbide rod blanks, even under demanding operating conditions. Additionally, their chemical inertness minimizes the risk of material degradation or contamination, making them ideal for use in industries such as aerospace, automotive, and manufacturing. Overall, the thermal stability and chemical inertness of cemented carbide rod blanks make them a reliable and durable choice for various industrial applications.
Types of Cemented Carbide Rod Blanks
Solid Carbide Rod Blanks
Solid carbide rod blanks are a crucial component in the manufacturing of cemented carbide products. These rod blanks are made from a combination of tungsten carbide and a binding metal, such as cobalt. The high hardness and excellent wear resistance of solid carbide rod blanks make them ideal for applications in industries such as automotive, aerospace, and machining. With their superior strength and durability, solid carbide rod blanks provide the necessary foundation for producing high-quality cemented carbide tools and parts. Whether it’s for cutting, drilling, or shaping, solid carbide rod blanks play a vital role in delivering precision and reliability in various industrial processes.
Tungsten Carbide Rod Blanks
Tungsten carbide rod blanks, also known as cemented carbide rod blanks, are essential components in various industrial applications. These rod blanks are made from a combination of tungsten carbide particles and a binder material, typically cobalt. The high hardness and exceptional wear resistance of tungsten carbide make it an ideal choice for manufacturing rod blanks that can withstand extreme conditions and heavy-duty operations. Tungsten carbide rod blanks are commonly used in the production of cutting tools, such as drills, end mills, and reamers, as well as in the manufacturing of wear parts for industries such as mining, construction, and oil and gas. With their superior strength and durability, tungsten carbide rod blanks play a crucial role in enhancing productivity and efficiency in various industrial sectors.
Titanium Carbide Rod Blanks
Titanium carbide rod blanks are a type of cemented carbide rod blank that are widely used in various industries. These rod blanks are made from a combination of titanium and carbon, resulting in a material that is extremely hard and wear-resistant. Titanium carbide rod blanks have excellent thermal stability and can withstand high temperatures without losing their hardness. They are commonly used in the manufacturing of cutting tools, such as drills, end mills, and inserts, as well as in the production of wear parts for machinery and equipment. With their superior strength and durability, titanium carbide rod blanks are an essential component in many industrial applications.
Applications
Metal Cutting Tools
Cemented carbide rod blanks are widely used in the manufacturing of metal cutting tools. These rod blanks are made from a combination of tungsten carbide and a binder metal, usually cobalt. The high hardness and wear resistance of cemented carbide make it an ideal material for cutting tools that are subjected to high temperatures and abrasive conditions. The rod blanks are machined and shaped into various tool designs, such as drills, end mills, and inserts, that are used in industries like automotive, aerospace, and machining. With their exceptional strength and durability, cemented carbide rod blanks play a crucial role in enhancing the efficiency and precision of metal cutting processes.
Mining and Construction Tools
Cemented carbide rod blanks play a crucial role in the mining and construction industry. These high-performance tools are widely used for drilling, cutting, and shaping various materials, including rocks, concrete, and metals. With their exceptional hardness and wear resistance, cemented carbide rod blanks ensure efficient and precise operations in demanding environments. Their durability and strength make them ideal for heavy-duty applications, allowing miners and construction workers to tackle challenging tasks with ease. Furthermore, the versatility of cemented carbide rod blanks allows for the creation of customized tools to meet specific project requirements. In conclusion, cemented carbide rod blanks are indispensable tools that contribute to the success and efficiency of mining and construction operations.
Wear Parts for Oil and Gas Industry
Cemented carbide rod blanks are essential components in the manufacturing of wear parts for the oil and gas industry. These rod blanks, made from a combination of tungsten carbide and cobalt, offer exceptional hardness and wear resistance, making them ideal for applications in harsh and demanding environments. The high-performance properties of cemented carbide rod blanks ensure the longevity and reliability of wear parts, allowing them to withstand extreme conditions and provide effective protection against abrasion, erosion, and corrosion. Whether used in drilling tools, valve components, or pump parts, cemented carbide rod blanks play a crucial role in enhancing the performance and efficiency of oil and gas operations.
Advantages and Limitations
Advantages of Cemented Carbide Rod Blanks
Cemented carbide rod blanks offer several advantages in various industries. One of the key advantages is their exceptional hardness and wear resistance, making them ideal for applications that require cutting, drilling, or milling. Additionally, cemented carbide rod blanks have excellent thermal and chemical stability, allowing them to withstand high temperatures and harsh environments. Another benefit is their superior strength, which enables them to endure heavy loads and maintain their shape over time. Furthermore, cemented carbide rod blanks have excellent dimensional accuracy, ensuring precise and consistent performance. Overall, the advantages of cemented carbide rod blanks make them a preferred choice for many industrial applications.
Limitations of Cemented Carbide Rod Blanks
Cemented carbide rod blanks, while highly versatile and widely used in various industries, do have their limitations. One of the main limitations is their brittleness. Due to their high hardness and rigidity, cemented carbide rod blanks are prone to cracking and breaking under excessive stress or impact. This can result in the failure of the tool or component being made from the rod blank. Another limitation is their limited resistance to thermal shock. Cemented carbide rod blanks can experience thermal cracking or deformation when exposed to rapid temperature changes, leading to reduced performance and reliability. Additionally, the production of cemented carbide rod blanks involves complex manufacturing processes and requires specialized equipment, making them relatively expensive compared to other materials. Despite these limitations, cemented carbide rod blanks continue to be valued for their exceptional wear resistance, high strength, and excellent cutting performance.
Future Developments and Research
In the field of cemented carbide rod blanks, future developments and research aim to enhance the overall performance and extend the range of applications. One area of focus is the improvement of the manufacturing process to achieve higher precision and consistency in the rod blank production. Additionally, there is a growing interest in exploring new alloy compositions and microstructures to optimize the mechanical properties and increase the tool’s resistance to wear and deformation. Furthermore, researchers are investigating innovative coating technologies to enhance the surface hardness and reduce friction, thereby improving the tool’s cutting efficiency. With ongoing advancements in materials science and manufacturing techniques, the future of cemented carbide rod blanks holds great potential for advancements in various industries, including aerospace, automotive, and machining.