Overview of Carbide Wear Strips
Carbide wear strips refer to precision ground tool steel pads or plates made from durable cemented carbide alloys used across demanding environments prone to excessive abrasion, erosion, sliding friction or high impact stresses causing accelerated wear rates through surfaces.
They provide armoring sacrificially shielding less durable mechanical components made from steels or cast materials – maximizing longevity across critical assemblies found in ore processing equipment, pelletizers, pulverizers, chutes, pipes, valves, pumps and other high wear industrial applications.
Table 1: Overview of Carbide Wear Strips
Properties | Details |
---|---|
Composition | Tungsten or chromium carbide in cobalt matrix |
Key Features | Ultrahard, temperature and corrosion resistance |
Manufacture Method | Sinter-HIP |
Thickness Range | 1/16″ to over 1”+ |
Typical Size | Up to 60” x 12” plates |
Main Applications | Mining, minerals processing, agriculture, energy |
With exceptional hardness exceeding 80 HRC plus heat resistance over 1000°C, carbide strips deliver significant life cycle cost savings and reduced maintenance versus alternatives across abrasive ore flows or highly erosive fluid transport pipelines thanks to durable compositions tailored resisting mechanical wear, sliding friction, acidic corrosion plus particle impacts.
Compositions of Carbide Wear Products
Carbide wear resistant strips rely on sophisticated metallurgical compositions fusing fine ultrahard grains like tungsten and chromium carbides forged in a cobalt matrix providing temperature resistance plus additional fracture toughness necessary surviving repeated mechanical stresses across mining, minerals handling and heavy industrial environments.
Table 2: Typical Compositions of Carbide Wear Strips
Constituent | Role | Percentage Range |
---|---|---|
Tungsten carbide | Primarily hard phase | 75-97% |
Chromium carbide | Hard phase with enhanced corrosion resistance | 0-15% |
Cobalt binder | Ductile support matrix | 3-25% |
Trace elements like Ta, Ti, Nb | Grain growth inhibitors | 0-5% total |
Specialized proprietary formulations tune relative ratios between carbide grain matrices and cobalt contents based on balancing durability needs against particular operating conditions spanning highly abrasive flows, extreme impact stresses or acidic corrosion risks.
These idealized compositions get manufactured into wear resistant plates, tiles or custom fabricated geometries shielding crucial infrastructure assets across mining, mineral processing, fuel transportation plus demanding slurry pumping industries where traditional steel or chrome alternatives fail prematurely thanks to extreme daily operation stresses degrading weaker metallurgies.
Properties of Carbide Wear Strips
Thanks to an optimized balance between ultra hard carbide phases resisting abrasion/erosion paired with tough cobalt and trace elements inhibiting cracks, carbide wear strip products offer a unique combination of properties otherwise unattainable facilitating 10-100X lifetime expansions relative to traditional materials under identical demanding service conditions.
Table 3: Overview of Carbide Wear Strip Characteristics
Property | Contributing Factors | Values |
---|---|---|
Hardness | Ultrafine chromium/tungsten carbides in cobalt | Over 80 HRC (1200 HV), up to 87 HRC possible |
Transverse rupture strength | Controlled cobalt ratios | 500 – 1750 MPa |
Toughness | Cobalt mean free path, grain size | 7-20 MPa-m^1/2 |
Erosion resistance | Controlled carbide grain formation and cobalt ratios | Up to 500x that of steel depending on particle sizes, velocities and angles |
Corrosion resistance | Cobalt/carbide ratios | Resists most inorganic mineral acids and alkaline solutions |
Max service temperature | Phase changes, oxidation resistance | Up to 1000°C without coatings |
The balanced formulations facilitate unmatched operational lifetimes across applications like:
- Mining conveyors, chutes and hoppers managing highly abrasive taconite, quartzite or other mineral ores
- Agitators and slurry pipe elbows contending concentrated particle streams
- Pug mills interacting hot acidic mixtures during minerals processing
- Lock hoppers and valve bodies regulating abrasive media flows
In each situation, deliberately developed carbide wear strip compositions, proprietary production techniques and custom-fitted component geometries provide tailored solutions maximizing asset integrity and availability – dramatically lowering maintenance costs and unplanned downtimes.
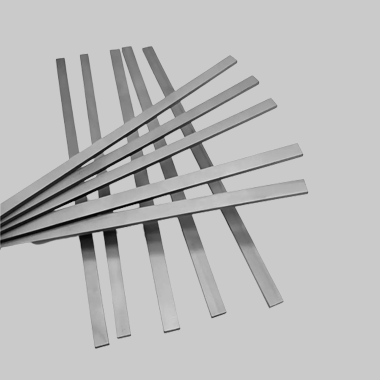
Grades and Classifications of Carbide Wear Components
With diverse applications across industries like mining, dredging, minerals processing, and power generation; numerous carbide grade formulations exist classified by hardness, toughness, cobalt ratios, corrosion resistance, grain size, or max service temperatures to best match intended operating conditions and wear mechanisms encountered.
Table 4: Classifications of Carbide Wear Strips
Grade Class | Description | Typical Uses |
---|---|---|
Ultra-fine grain | Exceptional hardness and polish | Water jet nozzles, aerospace bearings |
Medium grain | Balance of hardness and fracture resistance | Mining conveyors, dredging slurry lines |
Coarse grain | Enhanced impact strength | Brick kiln fans, pulverizer hammers |
6% cobalt | Higher hardness and wear resistance | Classifier blades, cyclones |
15% cobalt | Improves thermal shock robustness | Power generation ash handling, radiant tubes |
25% cobalt | Maximum toughness grade | Agricultural fertilizer manufacturing, turbine water injection |
The ultrafine C-type pressing grades offer ultimate abrasion resistance across smoothing or sealing contacts, while tougher medium P-type composites better manage moderate impacts across mining or minerals processing environments.
Higher cobalt M-types alternatively provide necessary resilience against thermal fluctuations seen in power generation or chemicals handling applications as well.
Careful customer collaboration assessing particular wear mechanisms occurring across operational conditions facilitates appropriate carbide selection from available formulations optimized resisting specific environmental attacks.
Typical Specifications of Carbide Wear Components
Thanks to broad adoption across mining, minerals processing, diesel engines and power generation industries; various international specifications guide consistent quality, manufacture, testing methods and certification standards for cemented carbide wear products facilitating performance benchmarking and quality verification of purchased materials.
Table 5: Carbide Strip Product Typical Specification Values
Parameter | Common Values | Test Methods | Importance |
---|---|---|---|
Density | 11.5 – 15.5 g/cm3 | Archimedes density scale measurement | Influences wear rate calculations |
Hardness | Over 80 HRC (800+ HV) | Microindentation per ASTM C1327 | Resists abrasion severity |
Transverse rupture strength | 450 – 1750 MPa | Multipoint 4-ball bending per ISO 3327 | Managing cyclic loading stresses |
Toughness | 7 – 20 MPa-m^1/2 | Palmqvist crack length per ASTM C1421 | Brittle fracture avoidance |
Young’s modulus | 450-650 MPa | Impulse excitation vibration analysis | Elastic rigidity, deflection resistance |
Electrical conductivity | 18-30% IACS | 4-probe test | Grounding, cathodic protection capacity |
With commercial carbide wear items utilized globally across mining assets, minerals processing infrastructure and power industry components; standardized test methodology conformity and certification documentation builds end user trust in supplied material quality – ensuring reliable field operation.
Applications of Carbide Wear Components
Thanks to an exceptional combination of hardness, fracture toughness and corrosion resistance attainable in geometrically complex shapes using precision powder metallurgy manufacturing techniques, commercial cemented carbide products empower substantial maintenance savings and operational lifetime gains across demanding minerals processing and handling industry sectors.
Table 6: Common Applications for Carbide Wear Strips
Category | Component Examples | Unique Advantages vs Incumbents |
---|---|---|
Mining | Chute liners, classifier blades, conveyor skirts | Handling highly abrasive copper, iron, quartz, phosphate ores |
Minerals processing | Cyclone cones, hydrotransport elbows, dredge line slurry pipes | Managing extreme erosive-corrosive mineral slurries |
Fertilizer production | Granulator barrels, mixer blades | Withstands abrasion and chemical attack |
Biomass handling | Feedscrews and barrels, pulverizer blade tips | Enhanced cutter life across highly siliceous sugarcane, almond shells and wood waste feeds |
Coal power generation | Gravimetric coal feeders, ash and FGD pipe liners | Resists coal impingements and acidic discharge flows |
In each scenario, exploiting the extraordinary hardness and balanced toughness of tailored carbide alloys strike the ideal economic balance between lifetime advantages against incumbent fabrications using traditional chrome, tool steel or stainless alternatives.
This facilitates slashing key production input costs for end products – making fertilizers, biomass fuels, critical mineral concentrates and electricity more affordable thanks to reduced downtimes maximizing plant availability and lowering maintenance expenses keeping vital equipment in service reliably.
Major Carbide Wear Parts Manufacturers
Given growth outlooks across essential minerals like iron ore, potash and lithium feeding infrastructure buildouts supporting economic development plus renewable energy ambitions globally over the next 20 years; leading cemented carbide producers actively expand manufacturing capacities delivering larger wear-resistant components securing vital supply chains against potential market imbalances or commodity pricing volatility.
Table 7: Leading Carbide Wear Parts Manufacturers
Company | Core Capabilities | Plant Locations |
---|---|---|
Kennametal | Mining grades expertise | North America, Europe, Australia |
Sandvik | Custom geometries and coatings | North America, South America, Europe |
Ceratizit | Complex pressed shapes and surface finishing | Europe, India, China |
Mitsubishi Materials | Thick heavy-duty plates and tiles | Japan, Europe, North America |
Tungaloy | Precision tolerances across thinner strips | Japan, Southeast Asia |
These major establishments and smaller regional specialists like Precision Carbide offer extensive selections of off-the-shelf blanks plus value-added fabrication services tailored meeting unique requirements – coating overlays adding corrosion protection or custom pressing special profiles in proprietary compositions.
Combining tailored carbide material science breakthroughs with practical metalworking innovations brings tremendous value securing supply chains againstCommodity market uncertainties or unexpected geopolitical dynamics through sustainable localized output.
Cost Analysis
Thanks to engineered compositions and tight dimensional-property conformance, cemented carbide wear products necessitate prices often 5-15X above standard tool steel or stainless alternatives used for conventional wear applications. However substantially longer operational lifetimes in production environments yield attractive per-piece and lifecycle cost savings.
Table 8: Carbide Strip Cost Considerations
Parameter | Typical Pricing | Market Trends |
---|---|---|
Carbide plate blanks | $60-220 per kg | 10-20% regional premiums common |
Complete wear components | $4-25 per square inch | Economy of scale discounts beyond 10 pieces |
Relative lifetime advantage | 8-100X over tool steel | Up to 1000X for highly abrasive ore flows |
For example:
- Specialized aircraft engine nozzle throat inserts in ultrafine grain grades sell for over $150/kg with complex geometries and exotic coatings.
- Meanwhile larger batches of straightforward brick kiln fan blade tips or classifier housings in common medium grain P20/30 sell between $20-60/kg.
However, inserts or tiles lasting for example 1000+ operating hours versus 50 hours with tool steel alternatives support substantial productivity, maintenance savings and safety gains per replaced part – rapidly offsetting higher initial carbide material and fabrication prices.
Future Adoption Trends
With sizable demand growth anticipated across minerals like iron ore, potash and copper feeding global infrastructure and renewable energy buildouts, abrasion/corrosion resistant grades of cemented carbide will realize expanded adoption securing supply chain assets against market imbalances or unexpected commotion over the next 10-15 years.
In particular, analysts predict tungsten and chromium carbide volumes expanding over 6% CAGR through 2030 as vital equipment modernization initiatives embrace materials science breakthroughs maximizing maintenance intervals and availability for existing plants before requiring capacity expansions – prioritizing enhanced capital efficiency.
However, rare earth supply uncertainties around critical constituent cobalt may encourage substitutions towards more readily available binder chemistries securing stable future cost outlooks and healthy inventories buffering short term logistics variability.
Overall, with exceptional hardness unattainable using alternate metallurgy solutions, tailored carbide compositions innovated balancing strength and toughness at affordable pricing structures promise tremendous savings potential revolutionizing wear components equipment longevity across more vital infrastructure.
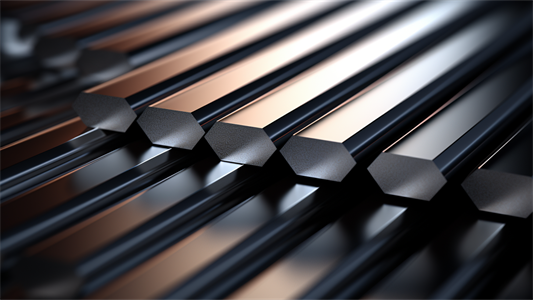
FAQ
Q: What joining options work well to install carbide wear strips?
A: Carbides cannot fuse weld without specialized techniques. Mechanical fasteners or high silver brazing offer ideal mounting approaches facilitating maintenance down the road. Careful design also enables precise interference fits for replacements.
Q: What restricted elements require consideration in recycling?
A: While most carbide wear products contain no hazardous elements,cobalt binder formulations and possible wax residues mandate safety precautions during reuse handling or remelting – requiring proper protocols and personnel protections.
Q: What safety gloves effectively manage carbide handling risks?
A: Linemen-style electrical gloves with leather outer layers protect hands adequately when transporting plates or performing workshop fabrication involving grinding/cutting risks requiring protection against abrasions and burring edges.
Q: What thickness ranges facilitate optimal carbide strip durability?
A: Between 3-25mm suits most wear situations. Above 25mm, impact stresses may cause internal cracking. Below 3mm increases risks of twisting or warping losing flatness tolerances. Custom stepped contours with thicker leading edges balance rigidity against cost.
Q: Which sectors show greatest growth potential for carbide adoption?
A: Mining, metal fabrication like extrusion dies, biomass processing, and additive manufacturing represent strong prospects as producers economize lighter sections withstand extreme pressures by substituting dense durable carbide grades whenever fatigue life expectations fall below 3-6 months with incumbent alloys.