Introduction
Definition of Carbide Wear Rods
Carbide wear rods are specialized components used in various industries to enhance the durability and performance of machinery and equipment. These rods are made from a combination of carbide, a hard and wear-resistant material, and other alloys. The primary purpose of carbide wear rods is to provide protection against abrasion, corrosion, and impact, thereby extending the lifespan of the machinery they are installed in. They are commonly used in applications such as mining, construction, and manufacturing, where heavy-duty equipment is subjected to harsh operating conditions. With their high hardness and excellent resistance to wear, carbide wear rods play a crucial role in reducing downtime and maintenance costs, ensuring optimal efficiency and productivity.
Importance of Carbide Wear Rods
Carbide wear rods play a crucial role in various industries, especially in heavy machinery and manufacturing. These durable and high-performance rods are designed to withstand extreme wear and tear, providing exceptional resistance to abrasion and impact. The importance of carbide wear rods lies in their ability to enhance the lifespan and performance of equipment by minimizing the effects of friction and reducing downtime for maintenance and replacement. With their exceptional hardness and toughness, carbide wear rods offer superior protection against wear, extending the longevity of critical components and improving overall productivity. Furthermore, their precise dimensions and accurate fit ensure optimal performance, making them an essential component in industries where reliability and efficiency are paramount. In conclusion, the importance of carbide wear rods cannot be understated, as they play a vital role in enhancing equipment durability, minimizing downtime, and maximizing productivity.
Applications of Carbide Wear Rods
Carbide wear rods are widely used in various applications due to their exceptional durability and resistance to wear. These rods are commonly utilized in industries such as mining, construction, and manufacturing, where abrasive materials and harsh conditions are prevalent. In the mining industry, carbide wear rods are used in drilling and excavation equipment to withstand the abrasive nature of rocks and minerals. In construction, these rods find applications in machinery and tools that are exposed to constant friction and impact. Additionally, carbide wear rods are utilized in the manufacturing sector for cutting, shaping, and machining processes. With their high hardness and toughness, carbide wear rods ensure extended tool life and improved productivity. Overall, the applications of carbide wear rods are diverse and essential in industries that require reliable and long-lasting wear-resistant solutions.
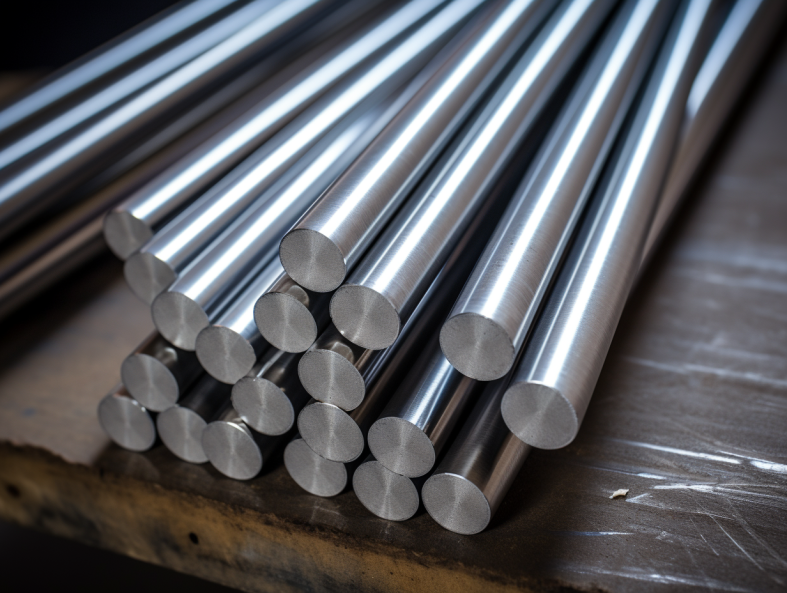
Composition
Materials Used in Carbide Wear Rods
Carbide wear rods are manufactured using a variety of high-quality materials that are specifically chosen for their exceptional durability and wear resistance. These materials include tungsten carbide, which is known for its hardness and ability to withstand extreme conditions. Additionally, cobalt is often used as a binder material to enhance the strength and toughness of the carbide wear rods. Other alloying elements such as chromium and titanium are also incorporated to further improve the performance and longevity of these rods. The careful selection of materials ensures that carbide wear rods can effectively withstand the harsh operating conditions they are subjected to, making them an ideal choice for applications that require superior wear resistance and reliability.
Properties of Carbide Wear Rods
Carbide wear rods are known for their exceptional properties that make them a popular choice in various industries. These rods are made from a combination of carbide and other materials, resulting in a high-strength and durable product. One of the key properties of carbide wear rods is their resistance to wear and abrasion. They can withstand harsh conditions and heavy usage, making them ideal for applications that require long-lasting performance. Additionally, carbide wear rods have excellent heat resistance, allowing them to maintain their integrity even at high temperatures. This property makes them suitable for use in environments where extreme heat is present. Furthermore, these rods exhibit high corrosion resistance, protecting them from chemical reactions and ensuring their longevity. Overall, the properties of carbide wear rods make them an excellent choice for industries such as mining, construction, and manufacturing, where durability and performance are crucial.
Manufacturing Process of Carbide Wear Rods
Carbide wear rods are manufactured through a meticulous process that ensures their durability and performance. The manufacturing process begins with the selection of high-quality carbide materials, which are then carefully shaped and formed into rods of the desired dimensions. These rods are subjected to a series of precision machining operations, including grinding, milling, and drilling, to achieve the required shape and surface finish. Next, the rods undergo a heat treatment process to enhance their hardness and strength. This involves heating the rods to a specific temperature and then rapidly cooling them to induce a controlled transformation of the carbide material. Finally, the carbide wear rods are carefully inspected and tested to ensure that they meet the stringent quality standards. The manufacturing process of carbide wear rods combines advanced technology, skilled craftsmanship, and rigorous quality control measures to produce high-performance components that are widely used in various industries.
Advantages
High Wear Resistance
Carbide wear rods are known for their exceptional durability and high wear resistance. These rods are specifically designed to withstand harsh conditions and abrasive environments, making them ideal for applications that require prolonged use and resistance to wear and tear. With their superior hardness and strength, carbide wear rods provide reliable protection against the damaging effects of friction and impact. Whether it is in mining, construction, or manufacturing industries, these wear rods offer a cost-effective solution for extending the lifespan of equipment and reducing maintenance costs. In addition, their precise dimensions and consistent performance ensure a perfect fit and optimal functionality. When it comes to high wear resistance, carbide wear rods are the go-to choice for professionals seeking long-lasting and reliable performance.
Long Service Life
Carbide wear rods offer exceptional durability and longevity, making them ideal for applications requiring a long service life. These rods are specifically designed to withstand high levels of wear and abrasion, ensuring reliable performance even in the most demanding environments. With their superior hardness and resistance to corrosion, carbide wear rods can outlast traditional materials, reducing the need for frequent replacements and minimizing downtime. Whether used in mining, construction, or manufacturing industries, carbide wear rods provide a cost-effective solution that guarantees extended service life and enhanced productivity.
Cost-effectiveness
Carbide wear rods offer a cost-effective solution for industries that require high wear resistance in their equipment. These rods are made from a combination of tungsten carbide and other materials, resulting in a durable and long-lasting product. The use of carbide wear rods can significantly reduce maintenance costs by minimizing the need for frequent replacements. Additionally, the exceptional hardness of carbide wear rods ensures superior performance and extended service life, making them an ideal choice for heavy-duty applications. With their cost-effectiveness and superior wear resistance, carbide wear rods are a reliable solution for industries looking to optimize their operational efficiency and minimize downtime.
Disadvantages
Brittleness
Brittleness is an important characteristic to consider when it comes to carbide wear rods. Carbide wear rods are known for their high hardness and resistance to wear, but they can also be prone to brittleness. This means that they are more likely to break or fracture under certain conditions, especially if they are subjected to sudden impacts or excessive stress. It is important to take this into account when using carbide wear rods in applications where durability and toughness are crucial. Proper handling and maintenance can help minimize the risk of brittleness and ensure the longevity of the carbide wear rods.
Limited Applications
Carbide wear rods have limited applications in various industries due to their unique properties and characteristics. These rods are widely used in the manufacturing and construction sectors for their exceptional hardness and resistance to wear and abrasion. They are commonly employed in the production of cutting tools, such as drills and saw blades, where durability and longevity are essential. Additionally, carbide wear rods are utilized in the mining industry for their ability to withstand harsh conditions and high-impact environments. Their superior strength and toughness make them ideal for applications that involve heavy machinery and equipment. Despite their limited applications, carbide wear rods continue to be a valuable asset in industries that require reliable and long-lasting materials.
Higher Initial Cost
Carbide wear rods, despite their numerous advantages, come with a higher initial cost. This is primarily due to the expensive materials used in their construction, such as tungsten carbide. However, this higher cost is often justified by the extended lifespan and superior performance that carbide wear rods offer. By investing in carbide wear rods, industries can minimize downtime and maintenance costs in the long run, making them a cost-effective choice for applications that require high wear resistance and durability.
Maintenance and Care
Proper Cleaning and Inspection
Proper cleaning and inspection of carbide wear rods is essential to ensure their optimal performance and longevity. When it comes to cleaning, it is important to use non-abrasive cleaning agents and avoid harsh chemicals that can damage the carbide surface. Regular inspection should be carried out to identify any signs of wear, such as chipping or cracking, which may affect the performance of the rods. Additionally, any buildup of debris or contaminants should be removed to prevent any potential damage. By following proper cleaning and inspection practices, users can maximize the lifespan of their carbide wear rods and maintain their effectiveness in various applications.
Regular Lubrication
Regular lubrication is essential for maintaining the performance and longevity of carbide wear rods. By applying a suitable lubricant regularly, friction and wear between the rods and other moving parts can be minimized. This not only ensures smooth operation but also helps to prevent premature damage or failure. Additionally, proper lubrication helps to dissipate heat generated during operation, reducing the risk of overheating. It is recommended to follow the manufacturer’s guidelines for lubrication intervals and use the recommended lubricant to ensure optimal performance and maximize the lifespan of carbide wear rods.
Replacement of Worn-out Rods
Carbide wear rods are an essential component in various industrial applications, providing durability and resistance to wear and tear. However, over time, these rods can become worn-out and need to be replaced. The replacement of worn-out rods is a crucial maintenance task that ensures the continued efficiency and performance of the machinery. By replacing the worn-out rods with new ones, the equipment can operate at its optimal level, reducing downtime and increasing productivity. Additionally, the replacement process involves careful inspection and measurement to ensure the new rods fit perfectly, guaranteeing a seamless transition and minimizing any potential disruptions. Overall, the replacement of worn-out carbide wear rods is a necessary step in maintaining the longevity and reliability of industrial machinery.
Conclusion
Summary of Carbide Wear Rods
Carbide wear rods are a type of tool used in various industries for their exceptional wear resistance and durability. These rods are made from a combination of carbide and other materials, which gives them the ability to withstand extreme conditions and heavy usage. The main purpose of carbide wear rods is to provide protection and support in applications where abrasion and impact are common, such as mining, construction, and manufacturing. With their superior hardness and toughness, carbide wear rods offer extended service life and reduced maintenance costs. In addition, their precise dimensions and excellent dimensional stability ensure consistent performance and accuracy. Overall, carbide wear rods are an essential component in many industrial applications, providing reliable and long-lasting solutions for wear and tear challenges.
Future Developments
In terms of future developments, there are several exciting advancements in carbide wear rods. One area of focus is improving the durability and longevity of these rods. Researchers are exploring new materials and manufacturing techniques to enhance the wear resistance and performance of carbide wear rods. Additionally, efforts are being made to optimize the design and shape of these rods to maximize their effectiveness in various applications. Another area of development is the incorporation of advanced coatings and surface treatments to further enhance the wear resistance and reduce friction. These coatings can provide additional protection against abrasion and extend the lifespan of carbide wear rods. Furthermore, advancements in nanotechnology are being explored to develop nanostructured carbide wear rods with superior mechanical properties and wear resistance. Overall, the future of carbide wear rods looks promising, with continuous research and development efforts focused on improving their performance and expanding their applications.
Final Thoughts
In conclusion, carbide wear rods are a crucial component in various industries due to their exceptional durability and resistance to wear. These rods are commonly used in applications such as mining, construction, and manufacturing, where heavy machinery and abrasive materials are involved. The use of carbide wear rods not only extends the lifespan of equipment but also improves overall productivity and efficiency. With their high hardness and strength, carbide wear rods provide reliable protection against wear and tear, reducing the need for frequent replacements and maintenance. As technology continues to advance, carbide wear rods are expected to play an even more significant role in enhancing the performance and longevity of industrial equipment.