Introduction
Definition of Carbide Tool Blanks
Carbide tool blanks, also known as cemented carbide blanks, are preformed pieces of tungsten carbide that are used as the base material for manufacturing various cutting tools. These blanks are made by mixing tungsten carbide powder with a binder material, such as cobalt, and then compacting and sintering the mixture at high temperatures. The resulting carbide tool blanks possess exceptional hardness, wear resistance, and strength, making them ideal for applications that require precision cutting, drilling, or shaping. Due to their superior properties, carbide tool blanks are widely used in industries such as metalworking, woodworking, and mining, where high-performance cutting tools are essential for efficient and accurate operations.
Importance of Carbide Tool Blanks
Carbide tool blanks play a crucial role in various industries, especially in the manufacturing sector. The importance of carbide tool blanks cannot be overstated as they are the foundation for creating high-quality cutting tools. These blanks are made from a combination of tungsten carbide and cobalt, which gives them exceptional hardness and durability. The use of carbide tool blanks ensures precision and efficiency in cutting operations, resulting in improved productivity and cost-effectiveness. Moreover, carbide tool blanks have excellent heat resistance, allowing them to withstand high temperatures during machining processes. Overall, the use of carbide tool blanks is essential for achieving superior cutting performance and maintaining the highest standards of quality in the manufacturing industry.
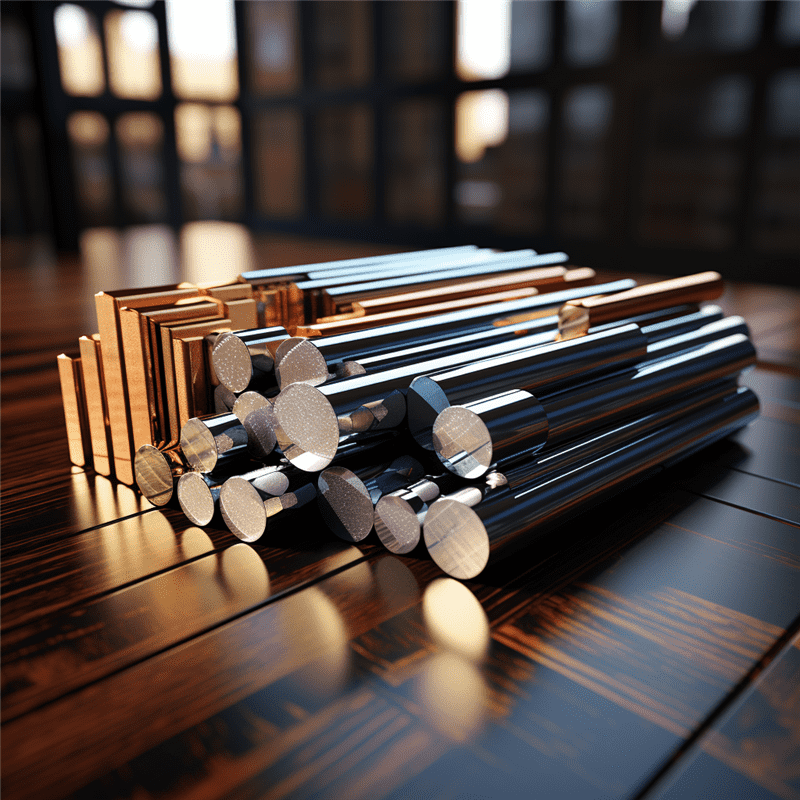
History of Carbide Tool Blanks
Carbide tool blanks have a rich and fascinating history. The development of carbide tool blanks can be traced back to the early 20th century when scientists and engineers were searching for a material that could withstand high temperatures and provide superior cutting performance. It was during this time that tungsten carbide, a compound of tungsten and carbon, was discovered. This groundbreaking discovery paved the way for the production of carbide tool blanks, which revolutionized the machining industry. Today, carbide tool blanks are widely used in various applications, including metalworking, woodworking, and mining, due to their exceptional hardness, wear resistance, and heat resistance. The history of carbide tool blanks is a testament to human ingenuity and the constant pursuit of innovation in the field of materials science and engineering.
Composition of Carbide Tool Blanks
Tungsten Carbide
Tungsten carbide is a versatile and highly durable material used in various industries, including manufacturing and construction. It is a compound made of tungsten and carbon, known for its exceptional hardness and resistance to wear and tear. Carbide tool blanks, made from tungsten carbide, are widely used in cutting and drilling applications. These blanks provide superior performance and longevity compared to traditional steel tools. With their exceptional strength and hardness, carbide tool blanks are capable of withstanding high temperatures and heavy loads, making them ideal for demanding tasks. Whether it’s machining, metalworking, or woodworking, tungsten carbide tool blanks are the go-to choice for professionals seeking precision and efficiency in their work.
Cobalt
Cobalt is a crucial element in the manufacturing of carbide tool blanks. It is used as a binder material to hold the tungsten carbide particles together, providing strength and durability to the tool. The addition of cobalt improves the performance and wear resistance of the carbide tool, making it suitable for cutting and shaping hard materials such as steel, cast iron, and stainless steel. The cobalt content in the carbide tool blanks can vary depending on the specific application and desired properties. Overall, cobalt plays a vital role in the production of high-quality carbide tool blanks.
Other Additives
Carbide tool blanks are an essential component in the manufacturing industry. They are used to create cutting tools that are known for their durability and precision. These tool blanks are made from a combination of tungsten carbide and other additives. The addition of these additives enhances the strength and hardness of the carbide, making it suitable for various machining applications. In addition, the use of carbide tool blanks improves the overall efficiency and productivity of the machining process. With their excellent wear resistance and high heat tolerance, carbide tool blanks have become the preferred choice for professionals in the industry. Other additives, such as cobalt, nickel, and titanium, are often added to further enhance the performance of the carbide tool blanks. These additives help to improve the toughness, corrosion resistance, and thermal stability of the tool blanks, ensuring their longevity and reliability. Overall, carbide tool blanks with other additives play a crucial role in enabling precise and efficient machining operations in various industries.
Manufacturing Process
Powder Metallurgy
Powder metallurgy is a manufacturing process that involves the production of metal powders and their consolidation into solid components. It is widely used in the production of carbide tool blanks, which are essential in various industries such as automotive, aerospace, and machining. The powder metallurgy technique allows for the precise control of the composition and microstructure of the carbide tool blanks, resulting in superior hardness, wear resistance, and toughness. With the advancements in powder metallurgy technology, carbide tool blanks have become increasingly popular due to their high performance and long service life. They are utilized for cutting, drilling, and shaping hard materials like metal, wood, and composites. The versatility and reliability of carbide tool blanks make them indispensable in modern manufacturing processes.
Mixing and Blending
Mixing and blending are crucial processes in the production of carbide tool blanks. These processes involve combining various raw materials, such as tungsten carbide powder, cobalt powder, and other additives, in precise proportions to create a homogeneous mixture. The mixture is then subjected to intense mechanical forces, such as milling and grinding, to ensure proper particle size distribution and uniformity. This ensures that the resulting carbide tool blanks have the desired properties, such as high hardness, wear resistance, and toughness. The mixing and blending stage is a critical step in the manufacturing process, as it directly impacts the quality and performance of the final carbide tool blanks.
Compaction and Sintering
Compaction and sintering are crucial steps in the production of carbide tool blanks. Compaction involves pressing the powdered carbide material into a desired shape using high pressure. This process helps to ensure that the carbide particles are closely packed together, resulting in a dense and uniform structure. Sintering, on the other hand, involves heating the compacted carbide material at a specific temperature to bond the particles together. During sintering, the carbide particles undergo a process called diffusion, where they migrate and form strong bonds with each other. The combination of compaction and sintering results in carbide tool blanks that possess excellent hardness, wear resistance, and toughness, making them ideal for various cutting and machining applications.
Types of Carbide Tool Blanks
Solid Carbide Tool Blanks
Solid Carbide Tool Blanks are essential components in the manufacturing industry. These high-quality blanks are made from solid carbide material, which provides excellent hardness and durability. They are widely used in various applications, such as drilling, milling, and cutting. With their superior strength and wear resistance, solid carbide tool blanks ensure precision and efficiency in machining operations. Whether it’s for industrial production or DIY projects, these tool blanks are a reliable choice for professionals and enthusiasts alike.
Brazed Carbide Tool Blanks
Brazed carbide tool blanks are essential components in the manufacturing industry. These tool blanks are made from high-quality carbide materials that are known for their exceptional hardness and durability. The brazing process involves joining the carbide tips to the tool body, creating a strong and reliable bond. This allows the carbide tool blanks to withstand the high temperatures and pressures experienced during machining operations. With their superior cutting performance and long tool life, brazed carbide tool blanks are widely used in applications such as metalworking, woodworking, and automotive industries.
Indexable Carbide Tool Blanks
Indexable carbide tool blanks are an essential component in the manufacturing industry. These tool blanks are made from carbide, a durable and high-performance material that is known for its strength and wear resistance. The indexable feature of these tool blanks allows for easy replacement and repositioning of the cutting edges, increasing efficiency and reducing downtime. With their versatility and precision, indexable carbide tool blanks are widely used in various applications such as milling, turning, and drilling. Whether it’s for automotive, aerospace, or general machining, indexable carbide tool blanks play a crucial role in achieving precise and high-quality results.
Applications of Carbide Tool Blanks
Metal Cutting
Metal cutting is a crucial process in various industries, and carbide tool blanks play a significant role in this field. These tool blanks, made from a combination of tungsten carbide and cobalt, offer exceptional hardness and wear resistance. They are specifically designed to withstand the high temperatures and pressures involved in metal cutting operations. Carbide tool blanks are known for their superior cutting performance, allowing for precise and efficient machining of different metals. With their excellent durability and longevity, these tool blanks ensure consistent and reliable results. Whether it’s milling, turning, or drilling, carbide tool blanks are the go-to choice for professionals in the metal cutting industry.
Woodworking
Woodworking is a versatile craft that allows individuals to create beautiful and functional pieces from wood. One essential aspect of woodworking is the use of carbide tool blanks. These specially designed tools are made from carbide, a durable and long-lasting material that is perfect for cutting and shaping wood. Carbide tool blanks offer superior performance and precision, making them a favorite among woodworkers of all skill levels. Whether you’re a professional furniture maker or a hobbyist looking to create unique wooden crafts, carbide tool blanks are a must-have in your woodworking arsenal. With their exceptional durability and cutting-edge design, these tools ensure clean and precise cuts, resulting in high-quality finished products. So, if you’re passionate about woodworking and want to take your projects to the next level, don’t forget to include carbide tool blanks in your toolkit!
Mining and Construction
Mining and construction industries heavily rely on carbide tool blanks for their various applications. These high-performance materials are used in the manufacturing of cutting tools, such as drills, end mills, and inserts, that are essential for mining and construction activities. Carbide tool blanks offer exceptional hardness, wear resistance, and thermal stability, making them ideal for withstanding the harsh conditions and demanding requirements of these industries. With their superior performance and durability, carbide tool blanks contribute to increased productivity, efficiency, and cost-effectiveness in mining and construction operations.
Advantages and Disadvantages
Advantages of Carbide Tool Blanks
Carbide tool blanks offer several advantages that make them a popular choice in various industries. Firstly, carbide tool blanks have exceptional hardness and wear resistance, allowing them to withstand high-speed machining operations and prolonged use. This results in longer tool life and reduced downtime for tool changes. Additionally, carbide tool blanks have excellent heat resistance, enabling them to maintain their cutting performance even at elevated temperatures. This makes them suitable for demanding applications that involve high-temperature cutting. Moreover, carbide tool blanks provide superior dimensional stability, ensuring consistent and precise machining results. With their high strength and rigidity, carbide tool blanks can handle heavy cutting loads and deliver excellent surface finishes. Overall, the advantages of carbide tool blanks make them an essential component in the manufacturing and machining processes, contributing to improved productivity and cost-efficiency.
Disadvantages of Carbide Tool Blanks
Carbide tool blanks, despite their many advantages, also have some disadvantages. One of the main drawbacks of using carbide tool blanks is their high cost. Compared to other types of tool materials, carbide tool blanks can be significantly more expensive. Additionally, carbide tool blanks are brittle and can be prone to chipping or breaking under certain conditions. This can result in the need for frequent replacements, adding to the overall cost of using carbide tool blanks. However, despite these disadvantages, carbide tool blanks are still widely used in various industries due to their exceptional hardness, wear resistance, and ability to withstand high temperatures.
Comparison with Other Tool Materials
Carbide tool blanks offer several advantages when compared to other tool materials. Firstly, carbide tool blanks have superior hardness and wear resistance, making them ideal for cutting and machining applications. Additionally, carbide tool blanks have excellent heat resistance, allowing them to withstand high temperatures without losing their hardness or shape. This makes them suitable for use in high-speed machining operations. Moreover, carbide tool blanks have good chemical stability, ensuring their durability and longevity. Overall, the use of carbide tool blanks provides a reliable and efficient solution for various tooling needs.