Overview of carbide strips with chamfer
Carbide strips with chamfer refer to thin rectangular sections of tungsten or titanium carbide material that feature an angled edge edge for installation into slots. The extremely hard, wear-resistant properties of carbides combined with geometric flexibility facilitate durable knife and tooling components in demanding industrial applications.
Common configurations include:
- Various carbide grades and binders to tailor hardness, toughness and other properties
- Customizable dimensions cut precisely to size
- Chamfer dimensions designed prevent edge chipping
- Smooth surface finishes enable sliding contact
- Brazed or clamped retention alternatives
Continue reading to learn more details about materials, sizes, chamfer profiles, installation methods and leading suppliers.
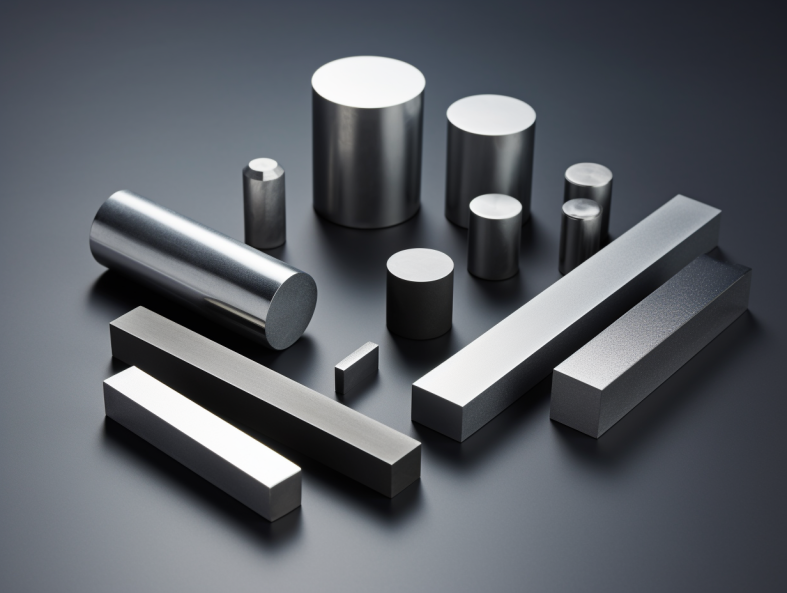
Composition and Grades
Common compositions for carbide strips featuring a chamfered edge:
Carbide Type | Binder/Alloy | Hardness | Color | Key Properties |
---|---|---|---|---|
Straight Tungsten Carbide | Cobalt | Rockwell C67 | Dark Grey | Maximum wear resistance and hardness |
Titanium Carbide | Nickel/alloy steel matrix | Rockwell C54 | Grey/Silver | Good corrosion resistance and hardness |
Zirconium toughened WC | Cobalt + trace Zr/Ta/Nb | Similar to WC | Grey | Improved resistance to cracking vs. straight tungsten carbide |
Table 1: Carbide material options for chamfer-edge insert strips used in various applications
The binder composition and sintering method influence final strip performance – customize to operating conditions.
Dimensions of carbide strips with chamfer
Typical size ranges available:
Parameter | Options |
---|---|
Thicknesses | 0.5mm to 4mm (~0.020″ to 0.150″) |
Widths | 2mm to 20mm (~0.080″ to 0.750″) |
Strip Length | 50mm to 300mm (2″ to 12″) |
Chamfer Angle | 30°, 45°, 60° most common |
Chamfer Depth | Up to 2mm (0.080″) |
Table 2: Variable dimensions and geometries offered for carbide chamfer strips
Carbide strips usually come in standard sizes but custom profiling services create application-specific inserts tailored to unique tooling requirements.
Key Properties of carbide strips with chamfer
Characteristic | Description |
---|---|
Hardness | Up to Rockwell C68 for tungsten carbide grades |
Wear Resistance | 10X that of tool steel facilitates long working life |
Toughness | Brittle material but zirconium enhanced grades improve crack resistance |
Corrosion Resistance | Grades containing nickel and chromium additions more resilient |
Compressive Strength | WC hardness maintains integrity under high contact loads |
Table 3: How carbide CTP geometry leverages intrinsic material properties
The unrivaled hardness enables maintaining sharp cutting geometry even under extreme pressures and temperatures prolonging lifespan.
Manufacturing Process
- Raw carbide powder mixed with nickel/cobalt binder
- Ball milling forms uniform blend
- Binder liquefies during sintering phase transformation
- Carefully controlled cooling cycle freezes optimal mixture of eta/cubic carbides
- Forging consolidates to final density prior to machining
- Wire EDM cuts complex profiles with micron precision
- CNC grinding and diamond wheel finishing
- Chamfer edge added through additional machining pass
- Custom marking/labeling for clear identification
Modern subtractive techniques create inserts of any required shape. Wire EDM enables intricate contours.
Applications of carbide strips with chamfer
Industries and uses taking advantage of enhanced cutter/tooling component wear life:
Segment | Application | Operating Conditions |
---|---|---|
Woodworking | Cutters, planer and jointer knives | High speeds, wood resin abrasion |
Food Processing | Slicing blades | High acid foods like tomatos erode standard stainless |
Medical/Pharma | Cutting tools to section bone/teeth | Hard contact stresses |
Automotive | Cut-off tooling, trimming | Prolonged, repetitive cuts through aluminum alloys |
Electronics | Wafer dicing | Require exceptional precision cutting carbon steel and glass |
Aerospace | Composites trimming | Abrasive reinforced plastics wear down steel cutters |
Table 4: Industries applying carbide chamfer strips to enhance durability of cutting components against wear
Any operation experiencing premature tool failure from wear or abrasion stays productive by upgrading to carbide.
Suppliers and Costs
Supplier | Materials | Pricing | Lead Times |
---|---|---|---|
Kennametal | Wide range of tungsten and titanium grades/compositions | $5 – $40 per insert | ~3-5 days |
Mitsubishi Carbide | Custom formula carbides for optimized wear and toughness | $10 – $60 per insert | ~2-3 weeks |
Sandvik Coromant | Standard and custom CTP geometries | $2.50 – $75+ per insert | Quick ship catalog items, or longer for customized orders |
Table 5: Sample carbide strip suppliers with indicative chamfered insert pricing
Carbide costs 5X to 10X over conventional tool steel but significantly enhances lifespan – payback within first production run typical.
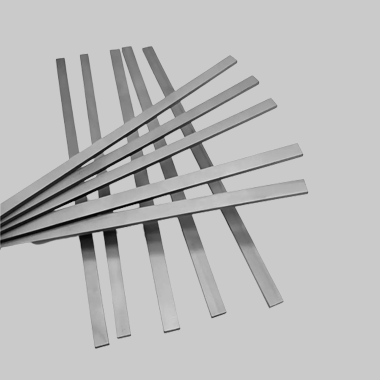
Pros and Cons
Advantages
- 10X or better life expectancy over HSS tooling
- Enables faster machining speeds/feeds boosting productivity
- Consistent sharp cutting edge from retained hardness
- Withstand highly abrasive composite materials without wear
- Resists deformation under high machining forces
- Tailorable grades balance wear resistance and brittleness
Disadvantages
- Higher upfront insert cost vs steel knives and edges
- Catastrophic breakage if shock overloaded and tolerance exceeded
- Requires rigidity of tool bodies to support hard insert material
- Edge integrity dependent on braze/clamp quality and precision
- Wire EDM can produce weakening microfractures if process parameters not optimized
FAQs
Q: What thickness carbide strip is best for woodworking planer and joiner knives?
A: 2mm to 4mm thick inserts with chamfers are typical for woodworking to withstand knocks and provide the backing support needed during re-sharpening. Hardwood species may dictate more robust 3mm – 4mm sections.
Q: Do brazed carbide inserts for cutters need to match tool steel expansion rates?
A: For best results when brazing carbide chamfer sections into tool steel bodies, choose carbide binders like nickel with thermal expansion rates closely matching (within ~15%) that of the tool steel grade to minimize internal stresses from heating/cooling and extend lifespan.
Q: How long can carbide chamfered inserts reasonably perform before needing replacement?
A: Endurance depends on specific use – 300+ hours of operation is reasonable for metal cutting. Less for highly abrasive composites or glass. Hardwood slicing can permit over 1000 operating hours if sharpened regularly. Far longer than conventional wear components.
Q: What precision can we expect on dimensions and tolerances for wire EDM-machined carbide parts like chamfer inserts?
A: Wire EDM using fine diameter molybdenum and brass wire allows cutting accuracy down to ~0.004″ (100 micron) or better for most profiles. Carbide’s low coefficient of thermal expansion minimizes distortion enabling dependable tolerances. Precision ground topcoat removal improves flatness. Discuss specifics with vendors.
Q: What international availability options exist for custom carbide CTP inserts beyond domestic US manufacturing sources?
A: In additional to major United States carbide strip suppliers, custom chamfer insert profiles are also offered internationally from production workshops in China, Germany and other European countries able to create application-specific geometries tailored to unique toolholder designs and hardened tool steel body requirements.