Introduction
Definition of Carbide Rod
A carbide rod is a type of cutting tool made from carbide, a compound of carbon and a metal such as tungsten or titanium. It is used in various industries for cutting, shaping, and machining hard materials such as metal, wood, and plastic. Carbide rods are known for their exceptional hardness and durability, making them ideal for applications that require high precision and long tool life. They are commonly used in manufacturing, construction, and automotive industries, among others. The composition and quality of the carbide rod play a crucial role in determining its performance and effectiveness in cutting applications.
Importance of Carbide Rod in Cutting Tools
Carbide rods play a crucial role in cutting tools, offering numerous advantages that make them indispensable in various industries. One of the key importance of carbide rods is their exceptional hardness, which allows them to withstand high temperatures and resist wear and tear. This makes them ideal for cutting tools that need to endure heavy-duty applications and maintain sharpness over an extended period. Additionally, carbide rods provide excellent cutting performance, ensuring precision and efficiency in various cutting operations. Their ability to retain their cutting edge for longer periods reduces the need for frequent tool replacements, resulting in increased productivity and cost savings. Moreover, carbide rods have excellent heat and corrosion resistance, making them suitable for cutting tools used in challenging environments. Overall, the importance of carbide rods in cutting tools cannot be overstated, as they significantly enhance performance, durability, and cost-effectiveness.
History of Carbide Rod
Carbide rods have a long and fascinating history in the field of cutting tools. The development of carbide rods can be traced back to the late 19th century when engineers were searching for a material that could withstand the high temperatures and pressures involved in cutting and machining processes. It was in the early 20th century that carbide rods made their breakthrough, thanks to the pioneering work of scientists and inventors. Since then, carbide rods have revolutionized the cutting tool industry, providing superior strength, durability, and precision. Today, carbide rods are widely used in various applications, including milling, drilling, turning, and grinding, making them an essential component in modern manufacturing processes.
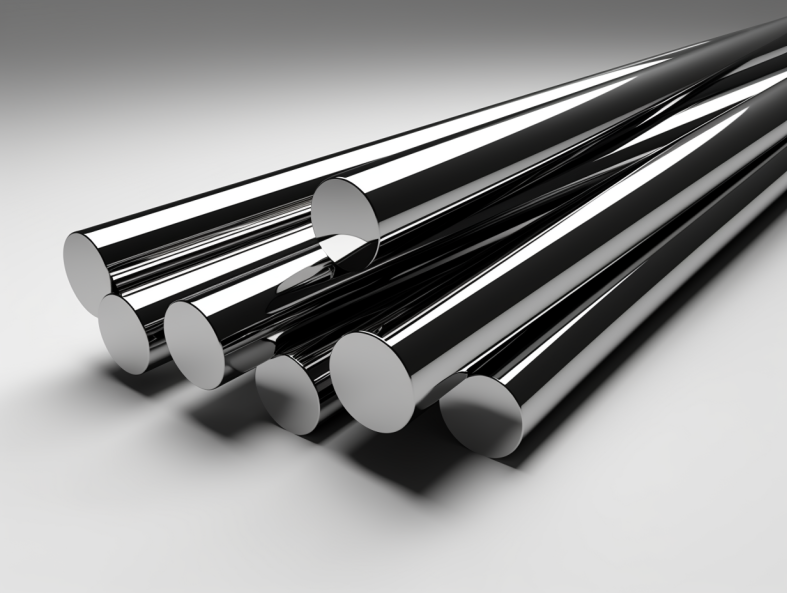
Composition of Carbide Rod
Materials Used in Carbide Rod
Carbide rods for cutting tools are made from a variety of high-performance materials. The most commonly used material is tungsten carbide, which is known for its exceptional hardness and wear resistance. Other materials used in carbide rod production include cobalt, titanium, and tantalum, which enhance the strength and toughness of the rods. These materials are carefully selected and combined to create carbide rods that can withstand the high temperatures and pressures involved in cutting operations. The use of these advanced materials ensures that carbide rods provide long-lasting performance and precision in various cutting applications.
Properties of Carbide Rod
Carbide rods are widely used in the manufacturing industry for cutting tools due to their exceptional properties. These rods are known for their high hardness, which allows them to withstand the extreme forces and temperatures encountered during cutting processes. Additionally, carbide rods have excellent wear resistance, ensuring a longer tool life and reducing the need for frequent replacements. The exceptional strength and toughness of carbide rods make them suitable for machining a wide range of materials, including steel, cast iron, and non-ferrous metals. Furthermore, carbide rods exhibit good thermal conductivity, helping to dissipate heat generated during cutting and preventing tool damage. Overall, the properties of carbide rods make them an indispensable component in the production of high-quality cutting tools.
Manufacturing Process of Carbide Rod
The manufacturing process of carbide rod involves several steps to ensure its high quality and durability. The first step is the selection of high-quality raw materials, such as tungsten carbide powder and cobalt powder. These materials are carefully measured and mixed in precise proportions to create a homogenous mixture. The mixture is then compacted under high pressure using a hydraulic press to form a green compact. The green compact is then subjected to a process called sintering, where it is heated at a high temperature in a controlled atmosphere. This process allows the particles to bond together, resulting in a solid and dense carbide rod. After sintering, the rod is machined and ground to achieve the desired dimensions and surface finish. Finally, the rod undergoes rigorous quality control tests to ensure its strength, hardness, and resistance to wear. The manufacturing process of carbide rod is complex and requires skilled technicians and advanced machinery, but it is essential for producing cutting tools that are reliable and efficient.
Types of Carbide Rod
Solid Carbide Rod
Solid Carbide Rod is a crucial component in the manufacturing of cutting tools. It is made from high-quality carbide material, which provides exceptional hardness and wear resistance. The rod is designed to withstand high temperatures and intense cutting forces, making it ideal for various machining applications. With its excellent strength and durability, the solid carbide rod ensures precise and efficient cutting performance, resulting in superior quality end products. Whether used in milling, drilling, or turning operations, the solid carbide rod is an essential tool for achieving optimal cutting performance and enhancing productivity in the metalworking industry.
Tungsten Carbide Rod
A Tungsten Carbide Rod is a type of cutting tool that is widely used in various industries. It is made from a high-quality tungsten carbide material, which is known for its exceptional hardness and durability. The rod is designed to be used in cutting applications that require precision and efficiency. Due to its superior strength and wear resistance, it can withstand high temperatures and maintain its cutting edge for a longer period of time. Tungsten Carbide Rods are commonly used in machining operations such as drilling, milling, and turning, where they provide excellent performance and reliability. With their ability to withstand heavy loads and extreme conditions, these rods are an essential component in the manufacturing and metalworking industries.
Cobalt Carbide Rod
A cobalt carbide rod is a type of cutting tool used in various industries. It is made from a combination of cobalt and carbide, which gives it exceptional hardness and durability. The rod is designed to withstand high temperatures and can be used for cutting, drilling, and shaping materials such as metal, wood, and plastic. The cobalt carbide rod is known for its excellent cutting performance and long lifespan, making it a popular choice among professionals in the manufacturing and construction sectors. With its superior strength and precision, the cobalt carbide rod is an essential tool for achieving high-quality results in cutting applications.
Applications of Carbide Rod
Metal Cutting
Metal Cutting is a crucial process in various industries, and carbide rods for cutting tools play a vital role in achieving precise and efficient cutting operations. These rods are made from high-quality carbide materials, which provide exceptional hardness and wear resistance. With their superior strength and durability, carbide rods can withstand the demanding conditions of metal cutting applications. They are designed to deliver high cutting speeds, excellent precision, and extended tool life. Whether it’s milling, turning, or drilling, carbide rods for cutting tools are the go-to choice for professionals who require top-notch performance and reliability. By using carbide rods, manufacturers can achieve superior results, improve productivity, and reduce downtime, making them an indispensable component in the metal cutting industry.
Woodworking
Woodworking is a versatile craft that requires the right tools for precision and efficiency. When it comes to cutting tools, one essential component is the carbide rod. A carbide rod is a durable and high-performance material that is commonly used in woodworking for its exceptional hardness and wear resistance. It is especially effective in cutting through various types of wood, providing clean and precise cuts. Whether you are a professional woodworker or a hobbyist, incorporating carbide rods into your cutting tools arsenal can greatly enhance your woodworking experience and produce exceptional results.
Plastic Cutting
Plastic cutting is a crucial process in various industries, and carbide rods have proven to be invaluable tools for this task. With their exceptional hardness and durability, carbide rods provide the necessary strength to cut through plastic materials effortlessly. The sharp cutting edges of these rods ensure clean and precise cuts, resulting in high-quality finished products. Additionally, carbide rods offer excellent heat resistance, allowing for prolonged use without the risk of deformation or damage. Whether it’s for manufacturing plastic components or crafting intricate designs, carbide rods are the go-to choice for achieving efficient and reliable plastic cutting operations.
Advantages of Carbide Rod
High Hardness and Wear Resistance
Carbide rods are widely used in the manufacturing industry for cutting tools due to their high hardness and wear resistance. These rods are made from a combination of tungsten carbide and cobalt, which gives them exceptional strength and durability. The high hardness of carbide rods allows them to withstand the intense pressure and heat generated during cutting operations, ensuring a longer tool life. Additionally, their excellent wear resistance ensures that the cutting edges stay sharp for extended periods, resulting in improved cutting performance and productivity. Whether it’s for milling, drilling, or turning, carbide rods are the go-to choice for professionals in the cutting tool industry.
Excellent Heat Resistance
Carbide rods for cutting tools offer excellent heat resistance, making them a preferred choice in various industries. The high melting point of carbide materials allows these rods to withstand extreme temperatures without compromising their performance. This exceptional heat resistance ensures that the cutting tools maintain their hardness and sharpness even during prolonged use. Whether in metalworking, woodworking, or other cutting applications, carbide rods provide the necessary durability to handle high-temperature environments. With their ability to resist heat, these rods contribute to increased productivity and efficiency in cutting operations, making them an indispensable tool for professionals in the field.
Long Tool Life
Carbide rods for cutting tools offer exceptional durability, resulting in a long tool life. These rods are made from a high-strength material that can withstand the rigors of heavy-duty cutting applications. With their superior hardness and resistance to wear, carbide rods maintain their sharpness and cutting performance for an extended period. This prolonged tool life not only improves productivity but also reduces the frequency of tool replacements, saving time and costs. Whether used in milling, drilling, or turning operations, carbide rods ensure consistent and reliable performance, making them an ideal choice for professionals in various industries.
Conclusion
Summary of Carbide Rod
Carbide rods are essential components in the manufacturing industry, particularly in the production of cutting tools. These rods are made from a combination of tungsten carbide and cobalt, which gives them exceptional hardness and wear resistance. The summary of carbide rod highlights their importance in providing superior cutting performance and longevity. They are widely used in various applications, including metalworking, woodworking, and machining. With their high strength and durability, carbide rods have become a preferred choice for professionals and hobbyists alike. Whether it’s for precision cutting or heavy-duty tasks, carbide rods ensure efficiency and accuracy in every use.
Future Developments
Future developments in the field of carbide rod for cutting tools are expected to bring significant advancements and improvements. Researchers and manufacturers are continuously working towards enhancing the durability, strength, and performance of carbide rods. One of the key areas of focus is the development of new carbide materials that offer even higher hardness and wear resistance. Additionally, efforts are being made to optimize the manufacturing processes to achieve better consistency and quality control. Furthermore, advancements in coating technologies are being explored to improve the surface properties of carbide rods, thereby increasing their efficiency and longevity. With these future developments, carbide rods are poised to play a crucial role in the cutting tool industry, enabling precision and efficiency in various machining applications.
Final Thoughts
In conclusion, carbide rods are an essential component in cutting tools. Their superior hardness and durability make them ideal for various applications in industries such as automotive, aerospace, and manufacturing. The use of carbide rods ensures precise and efficient cutting, resulting in high-quality products. Additionally, their resistance to wear and heat makes them suitable for prolonged use, reducing the need for frequent replacements. Overall, carbide rods are a reliable choice for professionals in the cutting tool industry, providing the necessary strength and performance for a wide range of cutting tasks.