Carbide rectangular strips refer to long, thin segments of tungsten or titanium carbide material used primarily to reinforce the wear resistance of woodworking and metal forming tools.
The hard, durable rectangular carbide inserts help machine and press tooling cope with line contact friction and material abrasion spanning continuous feed distances, extending service lifetime before reconditioning is needed.
This guide covers carbide grades, key properties, dimensions, applications, comparisons with alternatives, and FAQs when considering carbide strip selection for industrial tooling and machining enhancements.
Composition of Carbide Rectangular Strip Materials
Two primary carbide materials are used:
Carbide Type | Description | Key Properties |
---|---|---|
Tungsten carbide (WC) | Extremely rigid compound of W and C atoms | Hardness up to 92 HRA, heat resistance, wear resistance, chemical inertness |
Titanium carbide (TiC) | Interstitial compound of Ti and C | Hardness up to 72 HRA, high corrosion resistance, thermal conductivity |
These advanced ceramics retain hardness and stiffness at high temperatures allowing durable cutting performance.
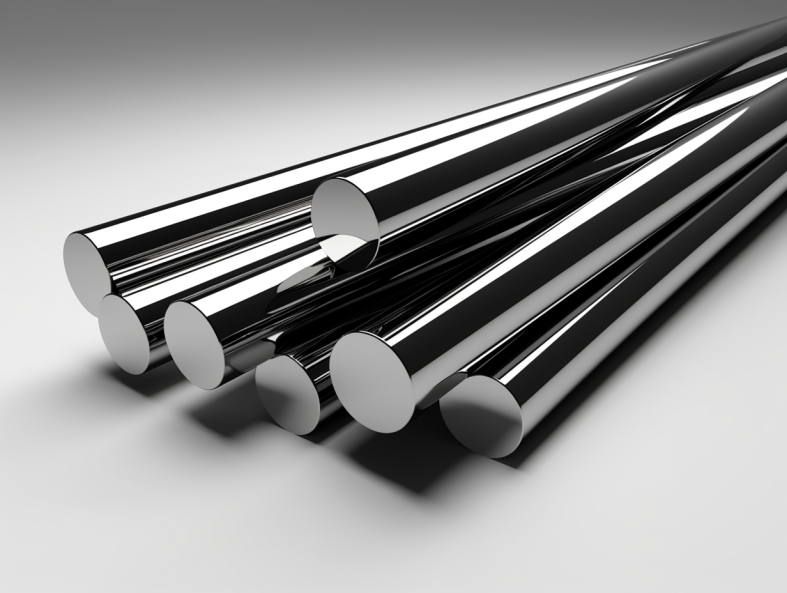
Characteristics of Carbide Rectangular Strips
In addition to carbide composition, key performance properties include:
Property | Typical Values |
---|---|
Hardness | 82-92 HRA (tungsten carbide), < 72 HRA (titanium carbide) |
Compressive strength | 4.5-6 GPa (~650-870 ksi) |
Transverse rupture strength | 350-650 MPa (50-95 ksi) |
Elastic modulus | 540-650 GPa |
Max service temperature | 500-1000°C (~930-1800°F) |
Thermal conductivity | 60-120 W/(m-K) |
Thermal expansion coefficient | 5-6.5 x 10^-6/K |
These characteristics suit carbide inserts for enhancing tooling durability and wear performance at high loads and temperatures during machining or forming.
Carbide Rectangular Strip Dimensions
Common standard available dimensions include:
Parameter | Ranges |
---|---|
Thicknesses | 1/16” (1.6 mm) up to over 1” (25 mm) |
Widths | 1/8” (3 mm) up to 1” (25 mm) |
Lengths | 2” (50 mm) up to 12”+(300 mm+) |
1/4” x 1/2″ x 6” is a frequently used size in tooling applications. Custom widths, lengths and thickness combinations are readily manufactured as well.
Applications of Carbide Rectangular Strips
Industry | Application Examples |
---|---|
Woodworking | Cutting blades, planer knives |
Metal forming | Punch-and-die sets, extrusion dies |
Food processing | Slicing blades, rasping/grating tools |
Mining/drilling | Rock drill inserts and teeth |
Machining | Cutting tool inserts for turning, boring, grooving, feeds |
The wear resistance and temperature capability enhance component life across continuous contact processes.
Carbide Strip Insert Suppliers
Supplier | Description |
---|---|
Kennametal | Global leader in industrial tooling provides standard and custom geometries/compositions |
Sandvik Coromant | Major cutting tooling manufacturer supplies indexable inserts in various carbide substrate options |
Lovejoy Tool | Carbide stock source aimed at woodworking applications |
Global Tooling Solutions | Source of standard and special order wear parts like dies, blades, and cutting inserts |
TiC Coated Tungsten Carbide | Chinese exporters focused primarily on custom geometries |
Comparing Carbide Strips vs Alternatives
Advantages vs steel:
- 5x harder than hardened tool steels
- Retains hardness and stiffness at higher temperatures
- Far more wear resistant for much longer tool life
- Chemically inert to most processing conditions
Advantages vs other ceramics:
- Higher transverse rupture strength than oxide ceramics
- Higher thermal conductivity than aluminum/silicon carbides
- Less brittle than pure carbide substrates
- Avoid issues with diamond abrasives like affinity for ferrous materials
Limitations:
- Difficult to conventionally machine requiring diamond grinding/EDM
- Higher upfront cost than tool steels
- Still lower stiffness than boron nitride at extreme temperatures
- Shock sensitivity requiring careful handling
Carbide inserts provide excellent versatility balancing hardness, toughness and temperature performance for continuous-contact wear applications.
FAQ
How are carbide rectangular strips manufactured?
Powder metallurgy consolidation processes form carbide substrates which get ground to final dimensional tolerance levels down to +/- 0.005” typically. Edge treatments/chamfers and specialty coatings can further enhance inserts.
What causes chipping failures in carbide strips?
Excessive interrupted cuts may create shock loads exceeding transverse rupture strength. Gradual engagement, conservative depths + feeds, and radiusing cutting edges combat such issues.
How are carbide strip tool failures detected?
Changes in cut surface quality, tool forces, vibration/chatter, or sudden wear indicate issues like fractures or material welding. Timely tool inspection avoids damage spreading to machinery or processed parts.
What sizes are most commonly used?
1⁄4” x 1⁄2″ with lengths spanning 2-6 inches cover ~90% of applications from micro drill bits to 12” planer knives for context. Width suits most holder slots while thickness withstands loads.
How long can carbide inserts last relative to tool steel?
Properly run carbide strip tooling often cuts 5-10x as long between sharpening/replacement than hardened tool steel versions operating 60+ HRC for perspective.